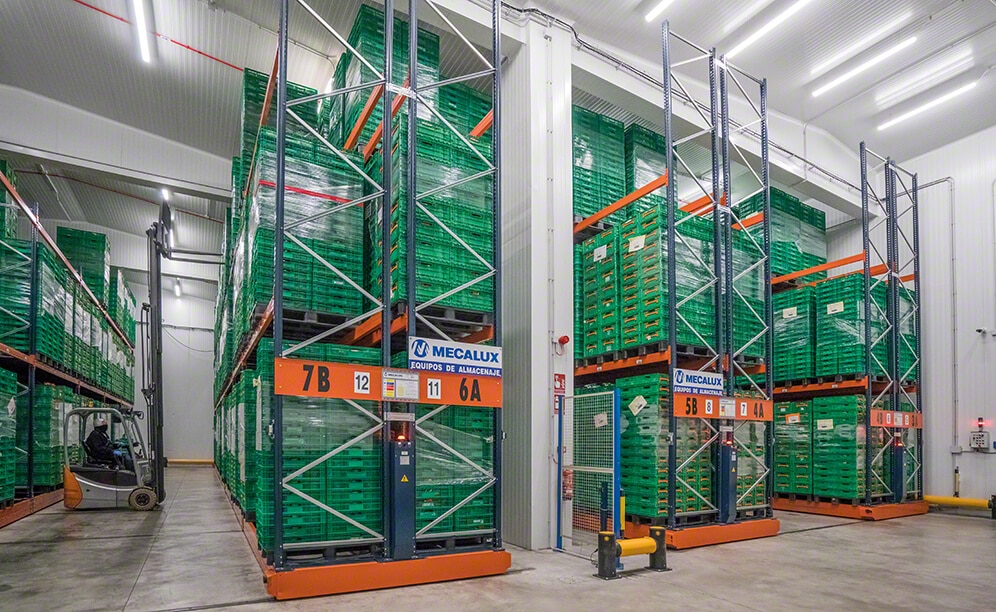
Sectored cold-storage warehouse of Grupo Alimentario Citrus
Grupo Alimentario Citrus combines various storage solutions for refrigerated products
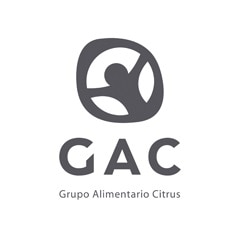
Mecalux has equipped the 4th range food warehouse of Grupo Alimentario Citrus’s (GAC) production centre in Ribarroja (Valencia) with Movirack mobile pallet racking, push-back racks with rollers and live preload channels. Input and output pallet conveyors were also installed in the finished products warehouse. The combination of these solutions helps optimise the available space, to achieve a >1,500 pallet storage capacity and to organise goods according to their features and rotation.
About Grupo Alimentario Citrus (GAC)
GAC is a company which specialises in fresh product making. Among its main customers, Mercadona stands out, the leading supermarket chain in Spain.
The company carries a wide variety of fresh and healthy, on-the-go packaged foods, which it updates continually launching new products like green smoothies, different ready-to-eat salad varieties, spiralised courgette or quinoa salads, among others.
Needs of GAC
Grupo Alimentario Citrus focuses its business strategy on developing cutting-edge products, as well as diversifying popular ready-to-eat salad bowls.
It had to reorganise operations of the 4th range food processing plant’s warehouse in Ribaroja de Túria (just 20 km from Valencia) to handle business growth. The company, which maintains a close relationship with Mecalux for many years running, once again requested its collaboration to expand the warehouse and mould it to the storage requirements.
GAC knew more storage capacity was a must, with products sorted as per their characteristics and rotation. Likewise, by dealing with perishable products, it would have to pay special attention to preserving the cold chain in all processes, aiming to ensure the foods’ maximum quality and optimal freshness.
Pau Pérez - GAC’s project engineer
“The automated warehouse for the 4th range plant in Ribarroja has solidified our decision to go with efficiency and quality service that the system gives our installations. We enjoy greater versatility and speed in our dispatches, while at the same time we have improved workplace safety for our workers.”
Warehouse distribution
The installation –which runs at a steady 4 ºC–is split into four different zones, each one allocated to a specific operation and product type. These zones are separated via vertical doors that block cold air from escaping.
Mecalux has supplied a quadruple storage solution:
- Movirack mobile pallet racking
- Live preload channels
- Push-back pallet racking
- Pallet racking
Finished product warehouse
This warehouse holds processed goods waiting to be shipped out. It contains eight double Movirack mobile pallet racks, each 8 m high with three storage levels, placed on laterally sliding mobile bases.
It operates straightforwardly: the operator gives the automatic open order to the base selected via a remote control device and, then, enters the desired aisle, where they slot or pick goods with the help of a reach truck.
The system is equipped with several safety devices whose role is to protect the operators and the stored goods. Among these are:
- External sensors: stop everything in motion if a person enters the aisle.
- Internal sensors: detect the presence of objects inside the aisle that would prevent the system from operating properly.
- Proximity sensors: ensure a safe, smooth stop.
Mecalux has also installed input and output conveyors for the goods in this warehouse. The conveyors –with rollers for inputs and chains for outputs– mean pallets can accumulate on the belt and this facilitates quick product retrieval.
Consumer goods warehouse
High consumption products (i.e. consumer goods) are set in two specific distribution centre zones.
Both are comprised of push-back racks with rollers, a solution that secures high space-purposing density and reduces handling times of the goods.
Access to the goods is done from a single working aisle. The first pallet is placed in the level’s first slot (closest the aisle). By inserting the second pallet, it pushes the first, and so on, until the channel is full. The racks are inclined, meaning the front is slightly lower to encourage the unit loads to advance through gravity to the first position when a pallet is removed.
Picking is also done in one of these two zones. To do so, 7.5 m high pallet racks were set up, whose direct access to the merchandise provides direct order picking off lower levels.
Preloads area
The warehouse has a huge preloads staging area with twelve live channels that are each eleven pallets deep.
Roller channels are slightly inclined so that pallets slide via gravity from the highest to the lowest point (which faces the docks). The channel’s split-roller outlet allows unloading via pallet truck.
Pallets are grouped according to if they correspond to a particular order or route, aiming to speed up subsequent distribution vehicle loading which minimises wait times.
Advantages for Grupo Alimentario Citrus (GAC)
- Efficient organisation: each product is slotted in the most suited storage system taking their characteristics and rotation into account.
- Storage capacity: the combination of different storage systems provides a 1,531 pallet capacity.
- High productivity: all installations are organised to dispatch the goods at a fast pace.
Finished product warehouse of Grupo Alimentario Citrus | |
---|---|
Storage capacity: | 1,531 pallets |
Pallet size: | 800 x 1,200 x 2,350 mm |
Max. pallet weight: | 500 kg |
Gallery
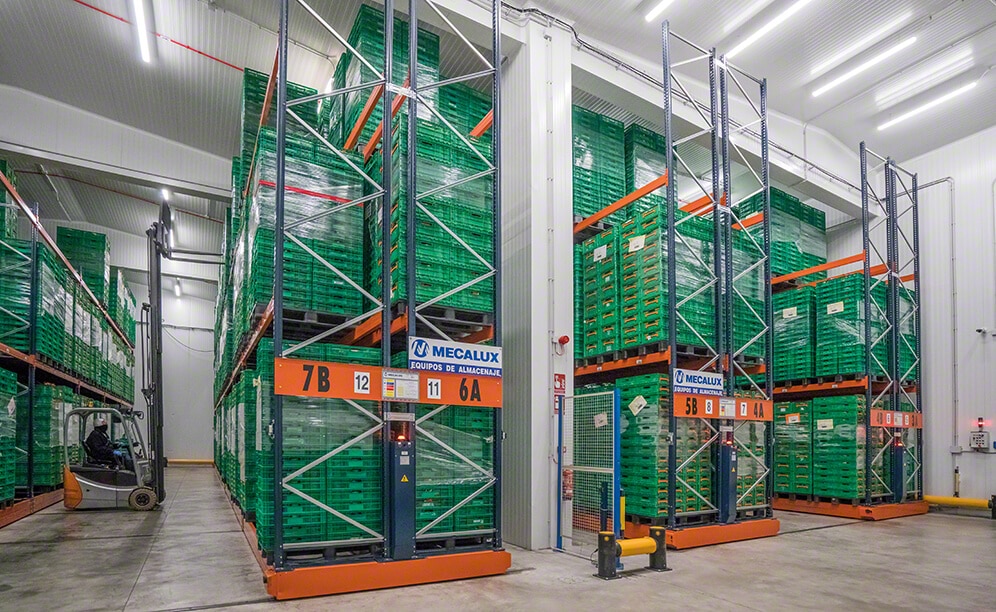
Grupo Alimentario Citrus warehouse with various storage solutions
Ask an expert