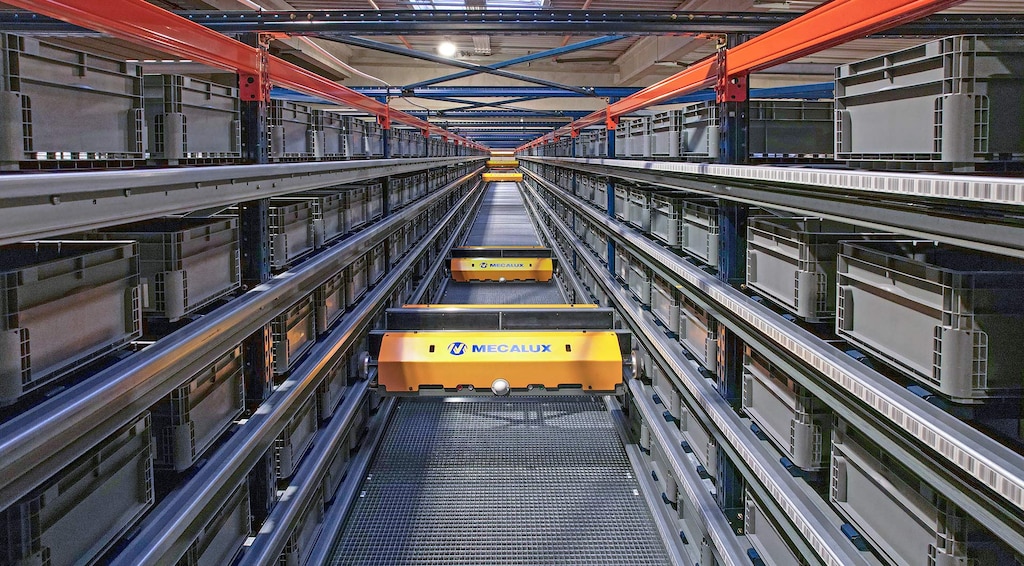
Shuttle System
Automated shuttle storage solution for boxes and small products
Product
Automated shuttle system for high throughput distribution centres
The Shuttle System is an automated storage solution for boxes that speeds up order picking, ensuring a constant flow of products from the warehouse slots to the pick stations.
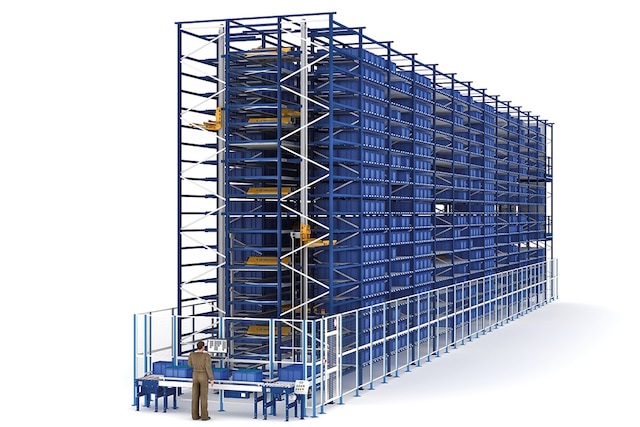
Advantages
More agility in order prep and increased storage capacity
This solution increases storage density and picking speed, boosting productivity.
- Continuous flows and operations (24/7).
- Fully automated storage system for boxes, bins, totes and small parts.
- Maximum speed in goods entry and exit operations.
- High number of movements per hour.
- Perpetual inventory (in real time) thanks to the Easy WMS warehouse management system.
- Modular and scalable system: can be expanded according to logistics needs.
- Optimization of available surface area to provide greater storage capacity.
- Adaptable to different unit loads (plastic totes, cardboard boxes, metal trays) of multiple sizes.
- Easy maintenance without the need to completely stop warehouse operations.
Applications
Intensive, more efficient picking for all types of companies
The Shuttle System is suitable for companies in any industry. It’s especially advantageous for those that house many small products in a limited space and need to enhance order picking productivity in their logistics facilities. Moreover, this system facilitates the consolidation and sequencing of prepared orders and the supply of materials to production lines.
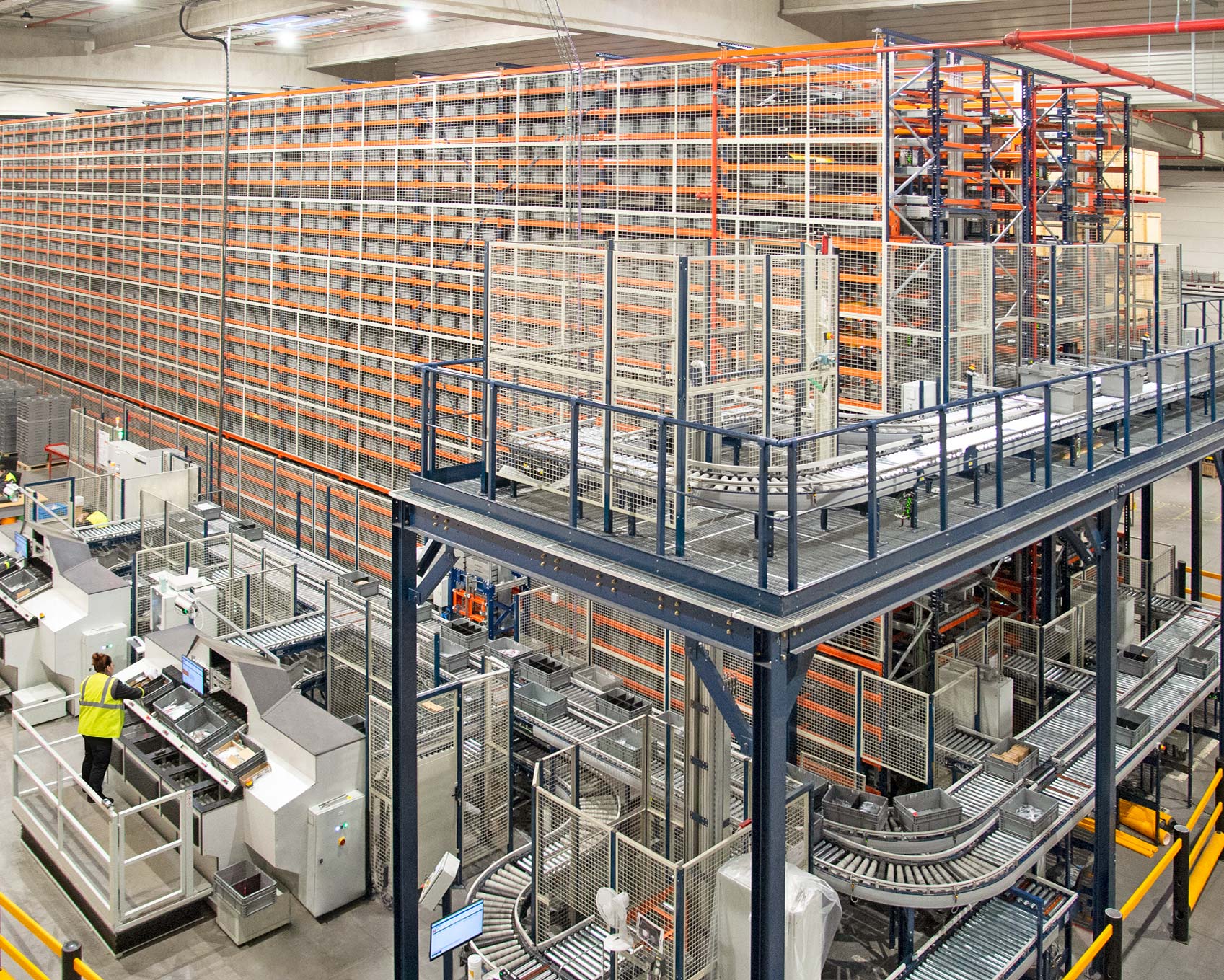
Operation
Continuous, safe movement of goods
The Shuttle System is specifically designed to facilitate the preparation of a large number of orders a day.
Case Studies
See more case studiesPick stations
Three possible picking systems for the same AS/RS
The Shuttle System is combined with pick stations where orders are prepared according to the goods to person method. The boxes are automatically sent to one of these three types of workstations:
- Traditional pick station. This solution is ideal for sporadic order picking. It is based on a U-shaped conveyor system at the front of the AS/RS (with roller conveyors) or on one side (with belt conveyors). Operators pick the boxes they receive from the AS/RS and distribute them to the locations behind them. In this way, depending on the dimensions of the boxes, operators can prepare 60 to 120 order lines per hour for the same SKU.
- Multi-order pick station. This also incorporates a U-shaped conveyor system. In this case, orders are prepared on one side of the operators (as opposed to behind them). There, they receive the boxes automatically (each box corresponds to an order made up of multiple SKUs). Operators remove the items from the boxes received from the AS/RS and sort them into each order. With this workstation, operators only have to turn 90° to prepare between 90 and 165 order lines per hour.
- High performance pick station. This picking solution — the most ergonomic of all — is designed to facilitate and speed up the preparation of orders containing many SKUs and lightweight products. In this pick station, up to 6 orders can be filled simultaneously, reaching a throughput of up to 1,000 picks/hour.
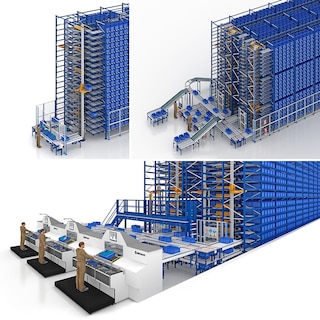
Components
Technical data
Max. AS/RS height | 20 m |
---|---|
Max. AS/RS length | 100 m |
Max. box weight | 50 kg |
Rack types | Single-, double- and triple-deep |
Shuttle speed | Up to 4 m/s |
Shuttle acceleration | Up to 4 m/s2 |
AS/RS temperature | From 0 to 40 °C |
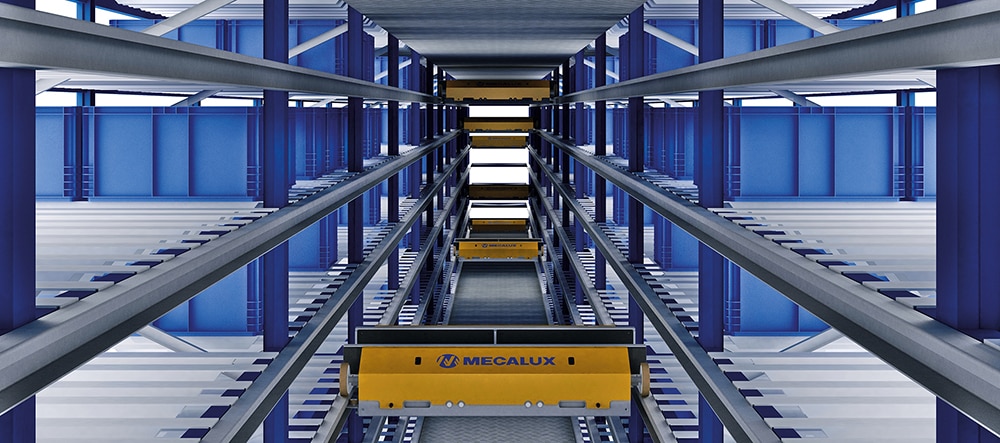
Catalogues
Ask an expert