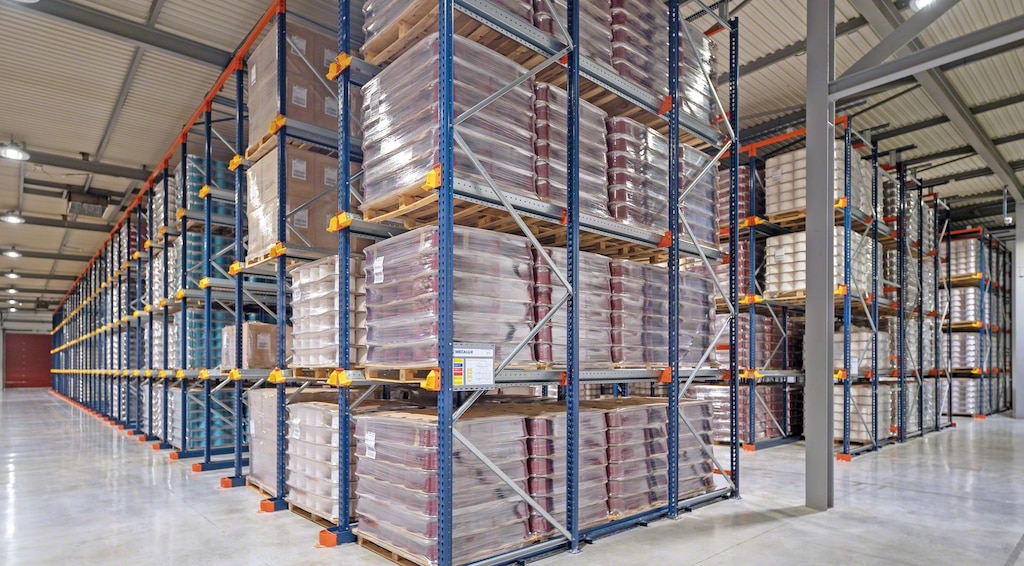
Drive-in/Drive-through Racking System
High-density racking based on the storage-by-accumulation principle. Designed to store homogeneous goods and make maximum use of available space.
The product
Drive-in/drive-through racking system: perfect for warehouses with homogeneous goods and a large number of pallets per SKU
Drive-in racking is the simplest and most affordable high-density storage method. It is comprised of multiple racks with a series of lanes accessed by forklifts to deposit or retrieve pallets. Compared to conventional pallet racking, this solution notably increases storage capacity.
These racks can have two configurations: drive-in (pallets are loaded and unloaded from the same working aisle) or drive-through (pallets are loaded through the front aisle and unloaded through the rear aisle).
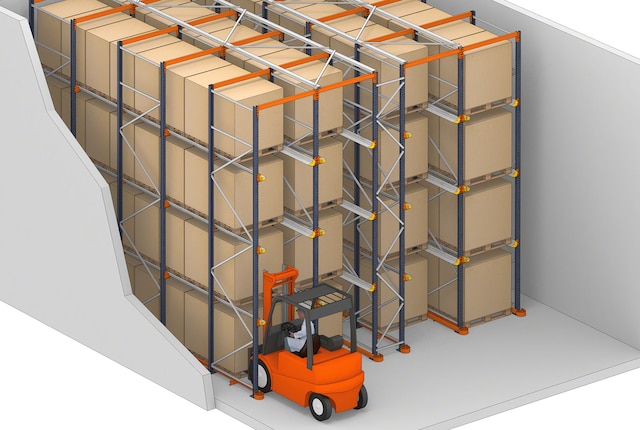
Advantages of a drive-in/drive-through racking system
- Maximum utilisation of space: it makes excellent use of both the available surface area and height, thus increasing storage capacity compared to conventional pallet racking.
- Simple and cost-effective: it is the simplest high-density storage system and requires the lowest investment.
- Configurable: the depth and height of this racking can be adapted to the needs of each customer and to the characteristics of the goods handled.
- One or two aisles: this solution can be used with just one aisle (loading and unloading from the front) or with two (loading in the front, unloading from the back).
- Guiding elements: Mecalux drive-in racks incorporate accessories that facilitate forklift movements and correct pallet positioning.
- Energy savings: the smaller footprint reduces the surface area to be cooled in cold storage and freezer warehouses.
- Easy inventory management: each lane stores a single SKU, streamlining stock control.
- Different pallet types: this racking can accommodate pallets of varying weights and dimensions.
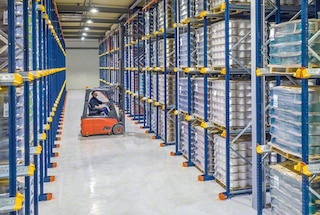
The drive-in racks have made great use of our available space and significantly boosted our storage capacity
Drive-in racking applications
Ideal for warehouses with few SKUs and many pallets
Drive-in racking is ideal for companies that manage homogeneous SKUs with a large number of pallets per SKU and want to maximise their available surface area and storage capacity.
How does drive-in high-density racking work?
Loading and unloading operations with the drive-in and drive-through varieties
In a high-density racking system, load management depends on the configuration of the racks. With drive-in pallet racking, storage and retrieval are carried out from a single working aisle. With drive-through pallet racking, two different aisles are used.
Testimonials
Case studies
See more case studiesDrive-in racking components
Mecalux’s drive-in warehouse racking stands out for the manufacturing quality of all its components. Cataphoresis coating is applied to the elements most prone to wear and corrosion.
The structure of drive-in racking is made up of a set of frames that provide the system’s vertical support. These frames incorporate interior lanes equipped with support rails, i.e., horizontal profiles on which the pallets are placed.
Mecalux drive-in racking has a series of components — some optional — that reinforce the safety of the system and help to prevent accidents when forklifts operate inside it.
Catalogues
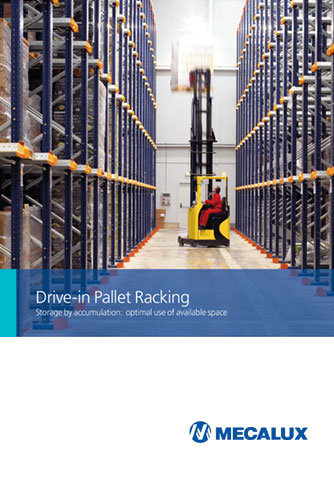
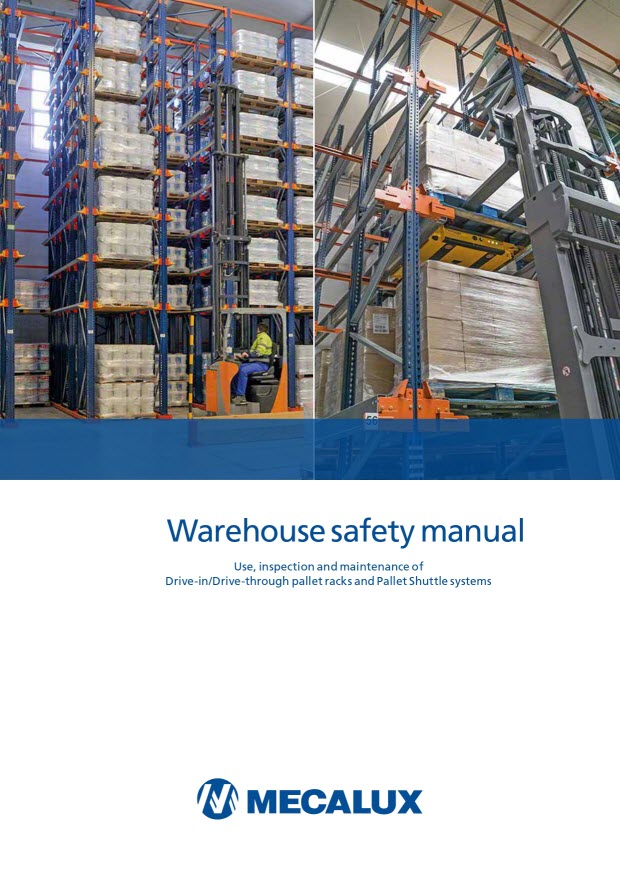
Warehouse safety manual
Operation, use, inspection and maintenance of drive-in/drive-through racking systems
Download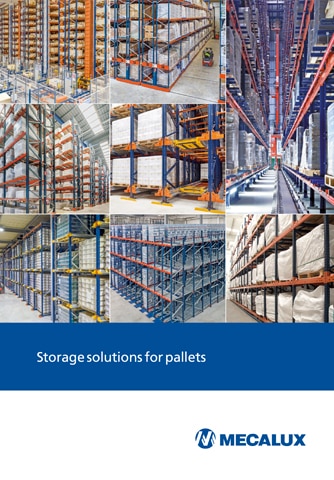
FAQs
Drive-in racking, also known as drive-in and drive-through racking, is a high-density pallet racking system made up of multiple racks that form internal lanes with support rails to hold pallets. Forklifts enter the structure, moving inside these lanes to load and unload goods. Thanks to the height and depth of the lanes, this solution makes excellent use of the available space and increases storage capacity compared to conventional pallet racking.
Depending on the type of load management strategy required, this high-density storage system can be configured in two ways: drive-in or drive-through racking. In the first and most common variety, loading and unloading operations are carried out from the same working aisle. Thus, stock is managed following the LIFO (last in, first out) principle. With drive-through storage, on the other hand, pallets are deposited and retrieved in two different aisles: goods go in on one end and are removed from the other. In this case, the loading/unloading sequence is done in line with the FIFO method (first in, first out). This configuration is typically employed when the system is used as a buffer or interim warehouse to effectively regulate flows between two work areas (for example, between production and dispatch or between different manufacturing stages).
The drive-in/drive-through racking system is a compact storage solution that meets a wide range of requirements. Its storage capacity is greater than that of conventional racking. Additionally, it is the simplest and most affordable system compared to other high-density storage solutions. However, since the forklifts have to enter the racking, more manoeuvring time is required for storage and removal operations. Furthermore, as each storage lane is reserved for a single SKU, drive-in pallet racking is not recommended for warehouses that manage a broad array of products. For these scenarios, Mecalux has other compact solutions that facilitate the management of more diverse goods. These include Pallet Flow Racking, Push-Back Pallet Racking and the Pallet Shuttle system.
There are no structural limitations to a drive-in racking system design. However, the maximum height of these racking units will be conditioned by the maximum lifting capacity of the handling equipment employed and by the manoeuvring assistance systems they incorporate (camera, height pre-selector, etc.).
The height of each drive-in racking storage level will depend on the height of the pallets and the type of construction system used to build the racks (with GP rails or with C rails). In the first case, the height of the storage level is equal to the height of the pallet plus 150 mm. For systems using C rails, the height of the storage level is equal to the height of the pallet plus 200 mm.
The depth of each lane is the sum of the depth of all the pallets (including the load dimensions if the goods protrude) plus a clearance per unit load of at least 25 mm. Meanwhile, the number of pallets stored in each lane is usually a multiple of the production batches or of the pallets that fit in a lorry. For instance, the lanes of a drive-in unit used to store finished orders could be designed to hold 11 pallets deep and 3 high. This would add up to the 33-pallet capacity of a trailer.
To achieve maximum efficiency, all pallets deposited in the same storage lane should have the same SKU. This avoids unnecessary handling.
As opposed to conventional pallet racking, with compact drive-in racking, pallets are handled from the wider side, with their bottom deckboards perpendicular to the support profiles. That is, the forklift truck deposits the pallet by resting its bottom deckboards at a 90° angle to the support rails.
Counterbalanced forklifts and reach trucks are used with drive-in racking. While counterbalanced forklifts do not usually surpass 7.5 m in height, reach trucks can exceed 11 m in height.
Given that forklifts drive inside the storage lanes, adequate clearances must be calculated to allow them to work safely, (e.g. a minimum clearance of 75 mm between each side of the forklift and the vertical elements). Likewise, the first level of support rails must be positioned at a height that does not interfere with forklift components (such as the chassis).
Ask an expert