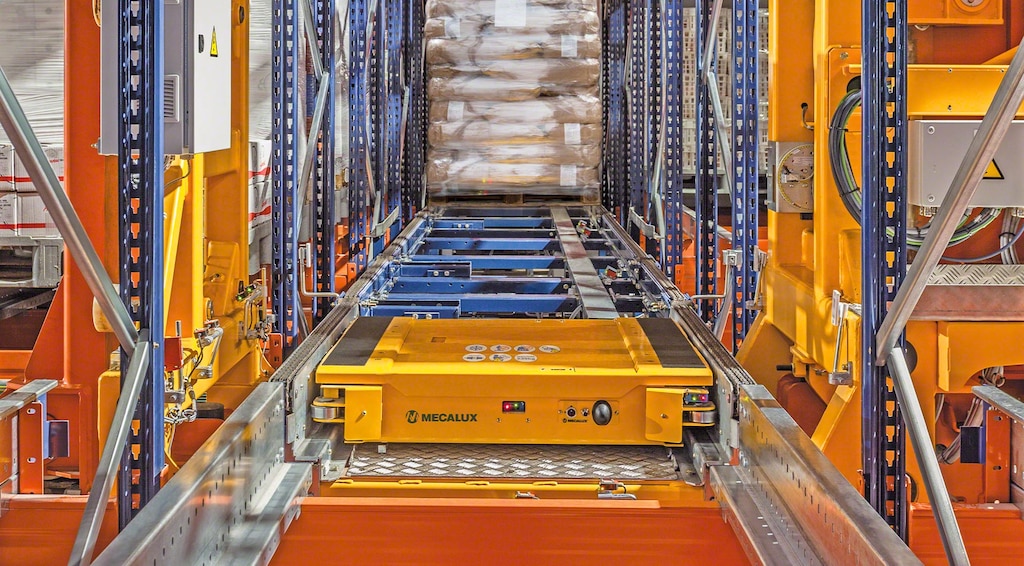
Automated Pallet Shuttle
Compact, completely automatic pallet storage solution that boosts warehouse capacity and productivity.
The product
Fully automated high-density storage to increase warehouse throughput
The Automated Pallet Shuttle is a compact storage system that employs an electric shuttle to load and unload pallets from racking automatically. Automatic handling equipment (stacker cranes or transfer cars) assists the shuttle, moving it from the storage system’s entry/exit points to the various storage channels.
This solution offers the perfect blend of high-density storage and operational automation. It boosts storage capacity considerably while speeding up inflows and outflows. This maximises available surface area as well as warehouse productivity.
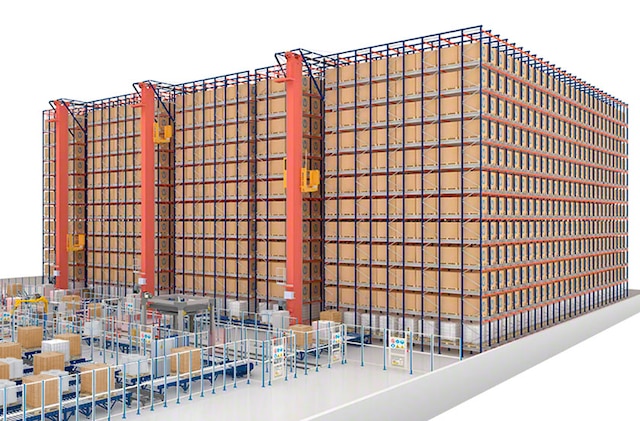
Advantages of the Automated Pallet Shuttle
- Increased productivity: a substantial rise in the number of cycles per hour compared to other compact storage systems, particularly in the configuration with transfer cars.
- Greater storage capacity: with racking that can exceed 40 m in height and storage channels measuring up to 45 m deep, the Automated Pallet Shuttle makes the most of the available space.
- Totally automatic operations: the complete automation of operations optimises movements, ensures flawless inventory control and eliminates errors.
- Fast travel speed: the shuttle’s rapid movement (72 m/min loaded and 108 m/min unloaded) reduces storage and retrieval times.
- Continuous operation: the shuttle car’s supercapacitors charge automatically when the vehicle is on board the stacker crane or transfer car. Therefore, it is always ready to operate.
- High versatility: each storage channel can house a different SKU. Moreover, the system can operate with pallets of different sizes and widths.
- Energy savings in cold stores: compact storage reduces the volume of air to be cooled in cold-storage and freezer warehouses.
- Safety: the shuttle handles and positions pallets with absolute accuracy. Additionally, the system significantly cuts down on the circulation of forklifts and other handling vehicles, enhancing safety in the facility.
- Comprehensive solution: Mecalux designs, manufactures, installs and commissions all system components. These include the racking, shuttle, automatic handling equipment (stacker cranes or transfer cars), conveyors, and warehouse control and management systems (WCS and WMS).
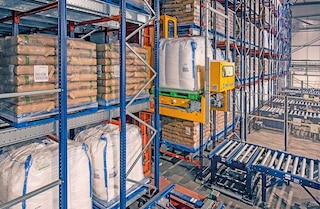
We’ve increased the flow of goods in and out of our business, optimised the vehicle loading process and reduced errors
Automated Pallet Shuttle applications
Perfect solution for automating the management of warehouses with high product turnover
Implementing the compact Automated Pallet Shuttle storage system is especially advisable for businesses that need to leverage available space and significantly increase productivity in moving many pallets per hour.
Automated Pallet Shuttle configurations
Complete automation of the storage and retrieval of palletised loads
In an Automated Pallet Shuttle storage system, the forklift used in the semi-automated version is replaced with fully autonomous handling equipment (stacker cranes or transfer cars). This considerably shortens the time spent on each operation.
Testimonials
Case studies
See more case studiesHow does the Automated Pallet Shuttle work?
Two operating modalities: with stacker cranes and with transfer cars
Each Automated Pallet Shuttle configuration entails a different operation. In the version with stacker cranes, one stacker crane operates in each aisle, while a single shuttle services all storage levels. Meanwhile, in the variant with transfer cars, one transfer car and one shuttle are placed on each level of every aisle of the storage system.
Automated Pallet Shuttle components
The Automated Pallet Shuttle comprises four basic elements: blocks of high-density racking, the electric shuttle that enters the storage channels to store and retrieve pallets, the handling equipment (stacker crane or transfer car) that moves the shuttle along the aisle, and the inbound and outbound pallet conveyors.
The motorised shuttle is the system’s central component. It supports the unit load and enters the channels to perform storage and retrieval operations. This compact, high-performance vehicle operates swiftly and safely.
In this variant, an automatic stacker crane travels along the aisle in a simultaneous translation/elevation movement to transport the shuttle. It moves the shuttle between the aisle entry/exit points and the various storage channels.
This setup also features an automated system: transfer cars and elevators move the shuttle between the aisle entry/exit points and the storage channels.
Automated Pallet Shuttle racking consists of high-density storage structures that increase warehouse capacity significantly. A rail system enables the shuttle to move inside the racking channels.
FAQs
The Automated Pallet Shuttle is a high-density storage system that employs electric shuttles and autonomous handling equipment (stacker cranes or transfer cars) to fully automate pallet storage and retrieval from racking structures. This boosts warehouse productivity and maximises available space.
The main difference between the two systems lies in the way they move unit loads to the entrance of the storage channels. In the semi-automated variant, a forklift transports both the shuttle and the pallet to be stored to the channel. It then places them at the channel entrance. With the automated solution, this operation is performed by stacker cranes or transfer cars, fully automating both manoeuvres.
The Automated Pallet Shuttle is a very effective solution for warehouses with high product turnover, where it is essential to leverage all available storage space. Similarly, it is a perfect system for companies with bulk storage of medium- and high-consumption SKUs or with a large number of pallets per SKU. Lastly, the Automated Pallet Shuttle is also advisable for cold stores. Compact storage saves energy considerably by reducing the volume of air to be cooled. Moreover, pallet shuttle automation makes it unnecessary to expose operators to low temperatures.
Opting for one type of handling equipment over another will depend on the required number of entry and exit movements. In the configuration with stacker cranes — which is more cost-effective — a single shuttle car serves the various storage levels located on both sides of the working aisle. This limits the system’s operational capacity, so the stacker crane option is recommended when the number of storage/retrieval cycles per hour is not a priority. The setup with transfer cars allows for one shuttle to operate on each storage level, multiplying the number of cycles per hour by the number of storage levels.
In a Pallet Shuttle system with transfer cars, a minimum of two elevators per aisle should be installed: one inbound and one outbound. Additionally, in cases requiring a higher number of cycles per hour, it is possible to install two inbound and two outbound elevators in a single aisle.
The shuttle used in Mecalux’s Automated Pallet Shuttle system comes in three sizes that adapt to the most typical pallet dimensions. The front measurement is the same for all three models, as the pallet is handled from its wider side (1,200 mm). The depth is the measurement that varies, in line with the most common pallet depths (800, 1,000 and 1,200 mm).
Yes, although not directly. To house a pallet of irregular dimensions, it must be mounted on a standard pallet compatible with the shuttle and the racking. This standard pallet acts as a slave pallet. To accommodate special loads like intermediate bulk containers (IBCs) and big bags, the unit load is placed on a pallet, which is then deposited on the racking rails.
Yes. To operate, the Automated Pallet Shuttle requires two programs. The warehouse management system (WMS) monitors stock and assigns locations to the various unit loads. Meanwhile, the warehouse control system (WCS) sends movement commands to the automatic handling equipment. Mecalux can supply both software solutions.
The shuttle supports unit loads weighing up to 1,500 kg.
The shuttle travels at a speed of 108 m/min unloaded and 72 m/min loaded.
The system is designed to operate within a wide range of temperatures, from -30 °C to +45 °F.
The shuttles operate continuously, as the supercapacitors charge automatically while the shuttle is on board the stacker crane or transfer car. The recharge time is variable depending on the depth of the channels and the weight of the unit loads. Generally, the supercapacitors reach full charge in less than 25 seconds on standby.
Yes, absolutely: there is no risk of degradation or ignition. Plus, they are maintenance-free, perfectly suited for intensive use and have a long lifespan.
Ask an expert