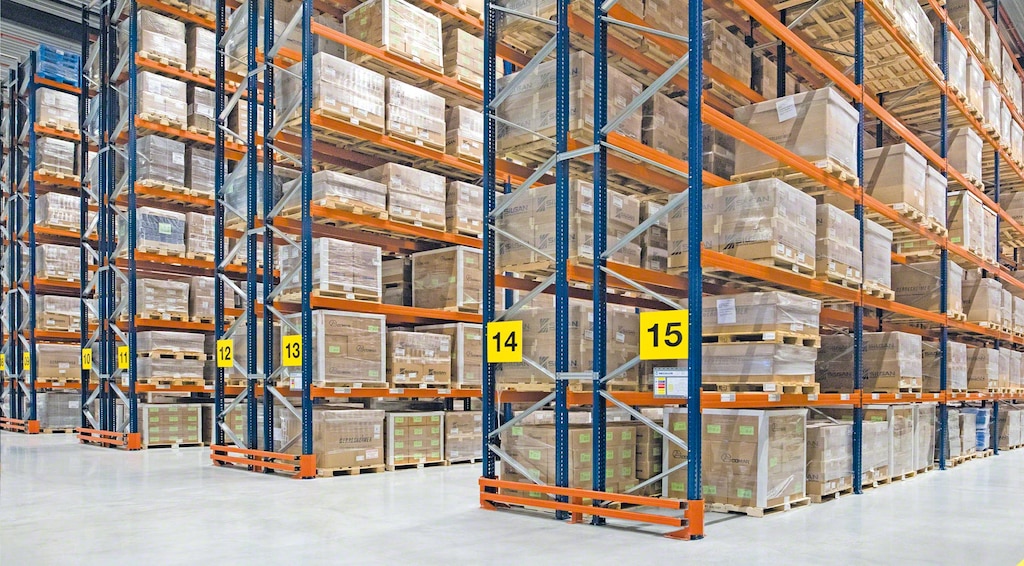
Pallet Racking
Versatile, robust storage solution that offers direct access to each pallet. Adaptable to all types of facilities.
The product
Pallet Racking: efficiency and flexibility
Selective pallet racking is the most universal storage system thanks to its versatility. Its distribution in the warehouse creates a series of interior aisles, enabling direct, individual access to all pallets. This setup is ideal when working with a wide array of SKUs.
Mecalux’s racks are manufactured in accordance with the highest quality pallet racking standards and are equipped with several safety features. An extensive range of uprights, beams, shelving and supports allow for the design of installations tailored to the most demanding needs.
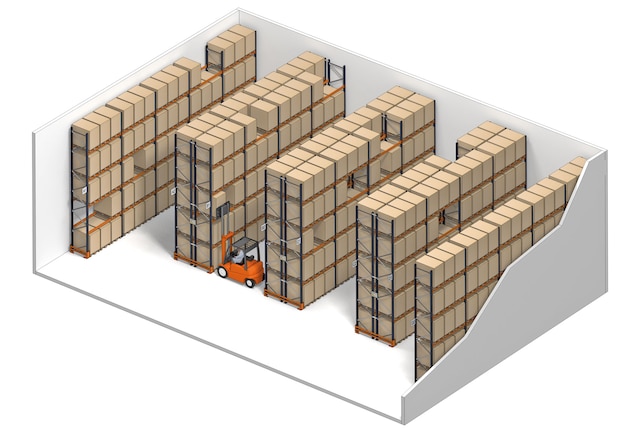
Advantages of selective pallet racking
- Direct access to each pallet: all pallets are accessible from the working aisle.
- Safety locking system (Mecalux-exclusive): this mechanism prevents the accidental displacement of the beam, enhancing the overall safety of the racking.
- Easy implementation: the structures are assembled quickly and have a low maintenance cost.
- Versatile: these racks adapt to the height of the facility and to multiple load types (from pallets and containers of different weights and sizes to boxes, drums and reels).
- Configurable and scalable: the height of the storage levels is adjustable and can be modified to reconfigure the storage system. Moreover, the racking can be expanded easily by adding bays and height levels.
- Suitable for picking: operators can perform picking tasks at floor level (or on the lowest parts of the racking). They can also pick items from higher locations using order pickers.
- Cataphoresis: Mecalux applies a cataphoresis coating to the uprights, increasing their resistance to corrosion.
- Racking inspection: as a manufacturer of industrial pallet racking, Mecalux offers an annual mandatory racking inspection service. Inspections are conducted by a highly qualified specialised technical team.
- Mecalux warranty: Mecalux’s racking complies with the highest quality standards and the regulations in force in each country.
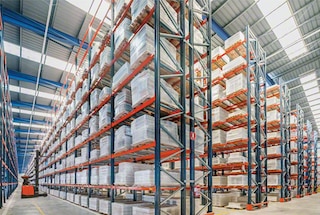
Pallet racks are the best way to manage our orders and fully optimise our storage capacity
Applications of pallet racking
Perfect solution for a broad range variety of SKUs
Due to its simple construction, versatility, easy assembly and low implementation cost, conventional pallet racking is the most commonly used storage system in warehouses. It is especially appropriate in the following cases:
Testimonials
Case studies
See more case studiesPallet racking configurations
Storage solution available in multiple combinations
Mecalux offers several variants of its conventional pallet racking system, adapted to the specific needs of each warehouse.
Selective pallet racking components
Mecalux pallet racking stands out for the manufacturing quality of all its components. Mecalux applies a cataphoresis coating to its uprights, increasing their resistance to corrosion. Additionally, it complies with the EN 15512, EN 15620, EN 15629 and EN 15635 standards.
The basic structure of conventional pallet racking — whether single- or double-deep — comprises a set of vertical and horizontal metal parts. Their adjustable connections allow for easy, fast assembly.
Adjustable pallet racking features multiple safety accessories to prevent accidents and strengthen the structural integrity of the racks. Moreover, Mecalux offers an annual pallet racking inspection service.
Pallet racking accessories
Wide range of accessories to enhance pallet racking versatility
Catalogues
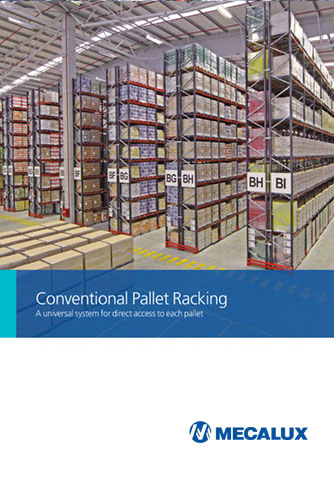
Selective Pallet Racking (catalogue)
The most universal system for direct access to every pallet
Download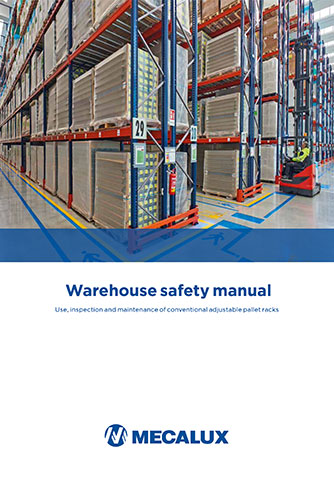
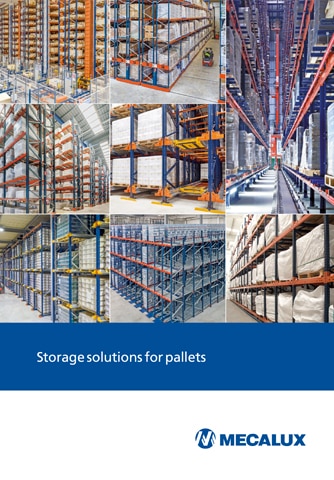
FAQs
Selective pallet racking is the most widespread storage system in warehouses that stock palletised goods. This is due to its versatility, simple construction, easy assembly and relatively low cost. Moreover, it is the only system that offers direct access to every pallet stored, ensuring efficient inventory management. This makes pallet racks the perfect solution for companies that handle many SKUs and few pallets of each.
The main advantage of selective pallet racking lies in direct access to each pallet stored. This ensures maximum agility in loading and unloading operations and efficient inventory management. Similarly, its versatility and the large number of storage locations it provides make it the ideal solution for multiple storage needs.
However, the choice of these racks may limit storage capacity in certain circumstances, particularly when dealing with few SKUs and many pallets per each. In this case, high-density storage systems are generally recommended. Examples include drive-in racking, pallet flow racking, push-back pallet racking and the Pallet Shuttle system.
Selective pallet racking dimensions are adapted to the requirements of each warehouse. Rack height can range from a few metres to over 40 metres (in automated warehouses). There is no limit in length: racking units can be installed one after another. Nevertheless, safety passageways must be enabled, and interior tunnels can be created as a shortcut between aisles. The depth of the frame is determined by the dimensions of the pallet. For a Euro-pallet measuring 1,200 mm deep, the frame will normally be 1,100 mm.
The length of selective pallet racking beams is subject to the type of pallet stored. For instance, for Euro-pallets, standard beam lengths are 1,825, 2,700 and 3,600 mm. In the case of North American (GMA) pallets, beam dimensions are 2,225 and 3,300 mm.
The endplate that joins the beam and upright features a built-in safety locking mechanism designed to make the structure even safer. Since it forms part of the endplate itself, the mechanism is always activated. Once in place, it cannot be removed without completely dismantling the beam. This prevents accidental or deliberate manipulation, ensuring the strength and stability of the racking. The safety locking mechanism is an exclusive innovation of Mecalux.
Cataphoresis is an immersion coating process that provides high corrosion resistance. Notably, it also covers the entire surface of the pieces, reaching even the most inaccessible parts and ensuring a uniform coating thickness. This enhances the components’ resistance to corrosion while safeguarding edges and corners. Mecalux applies cataphoresis coating to the uprights that make up pallet rack frames.
While primarily used for pallet storage, pallet racks can be adapted through various accessories to accommodate other types of loads, such as containers (metal, plastic and wood), reels, drums and other cylindrical items. It can also house different medium-sized and large unpalletised products.
In their standard configuration, pallet racking does not use shelves, as pallets are stored directly on the beams. However, it is possible to place metal or chipboard shelves on the beams. This will adapt the racks to house other types of unit loads and perform additional operations, such as order picking directly from the racking.
Yes, pallet racks are compatible with order picking, allowing for both storage functions and picking tasks. One option is to perform order picking directly from the pallets located at floor level. This is a common practice in many warehouses. Likewise, it is possible to allocate the first 2 or 3 levels of the racking to order picking directly from pallets. This strategy can be implemented provided that the location heights are appropriate and operators can access the products easily (assisted, for example, by an order picker). Another alternative is to place picking shelves on the lower levels. This makes it possible to store other types of unit loads while housing reserve pallets on the upper racking levels.
Any type of forklift can be used (counterbalanced, reach trucks, VNA trucks, etc.), as long as the aisle has the appropriate width and the machines can reach the upper load levels. In the case of double-deep pallet racking, the forklift employed must have telescopic forks to reach the pallet furthest away.
When using VNA trucks — typically used in narrow aisles with high-bay pallet racking — a guidance system is installed to direct the forklift’s path within the working aisle. This system can be mechanically guided, using profiles fitted to both sides of the aisle and anchored to the floor. Alternatively, it can be wire-guided, whereby a wire is embedded into the floor, producing a magnetic field to direct the forklift’s movement.
In warehouses using VNA trucks, pallet racking with a height of up to 15 m can be easily automated, without altering the structure of the storage system. This is achieved by installing automatic trilateral stacker cranes. This solution, equipped with a trilateral extraction system, fully automates storage and retrieval operations. In the event that you require complete automation of pallet storage, Mecalux can assist you in the design and implementation of an automated warehouse.
Absolutely. Mecalux offers a complimentary technical visit where our storage solutions experts — together with the client — identify the requirements and flows of goods to define a warehouse layout tailored to the client’s logistic needs.
Mecalux provides its clients with after-sales services including regular inspections, advice on the safe use of racking, delivery of the pallet rack installation manual and safety manual, technical guidance on warehouse solutions and safety, investigation of incidents/accidents in the facility and telephone support. Clients can also sign an inspection contract to implement a schedule of periodic inspections.
Yes. Mecalux offers a Racking Inspection service, an annual requirement stipulated by the UNE-EN 15635 standard (Steel static storage systems. Application and maintenance of storage equipment). After conducting the inspection, Mecalux will prepare a report outlining the findings of the assessment, with proposals for implementing safety measures in the facility, where applicable. Mecalux’s technical inspection department carries out annual inspections, issues certification reports and generates inspection labels.
Ask an expert