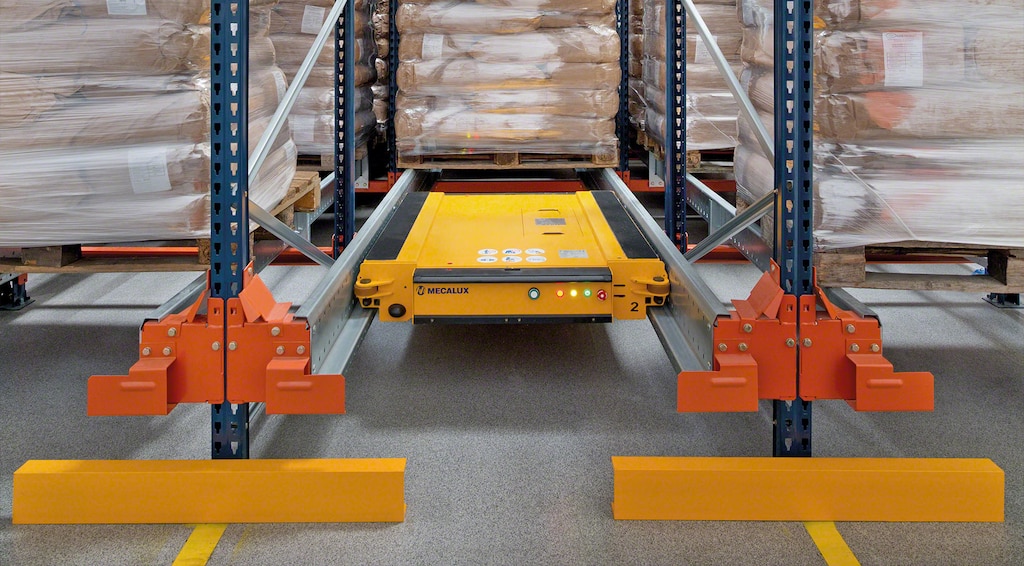
Pallet Shuttle Racking System
Semi-automated, high-density and high-throughput system that uses a motor-driven shuttle to place and remove pallets within racking structure.
The product
The evolution of high-density pallet storage systems: greater capacity, speed and throughput
The Pallet Shuttle is a semi-automated high-density storage system in which a shuttle with an electric motor runs along rails within the storage channels to load and unload pallets. The process is controlled by an operator, who places the shuttle in the racking using a forklift and controls it via a tablet.
Compared to other high-density solutions, e.g., drive-in racking, the shuttle rack system increases storage capacity, goods-in/goods-out flows and the number of products to be stored. The system is also available in a fully automated version, which features either stacker cranes or transfer cars.
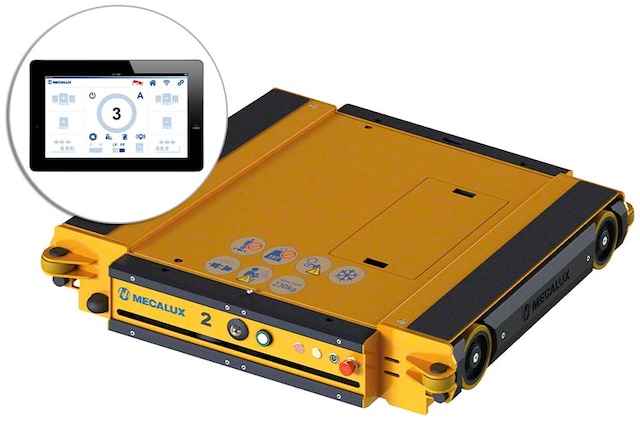
Advantages of the Pallet Shuttle system
- Time savings and productivity gains: the shuttle executes orders speedily, and the forklift operates in the aisle without entering the racking. This shortens loading/unloading times and raises the number of cycles/hour.
- Space savings: storage channels can exceed 60 m in depth, while clearances between levels are minimal, increasing storage capacity.
- Cost savings: the optimal use of space reduces the system’s footprint, thus keeping down land costs. And in cold storage warehouses, this means less surface area to be cooled, resulting in lower energy consumption.
- Multiple SKUs: grouping SKUs by channels as opposed to complete lanes allows for greater product diversity in the storage system.
- Compatible with LIFO and FIFO: the system can operate in line with the LIFO (last in, first out) or FIFO (first in, first out) inventory management strategies.
- Easy to use: all system functions are activated from the control tablet, which is equipped with an intuitive user interface.
- Safety: as the forklifts do not operate inside the racking, the metal structure remains free from damage, and the risk of accidents is minimized.
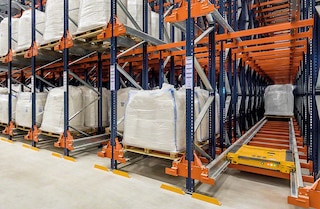
Compared to other high-density storage solutions, the Shuttle racking system is faster, more agile and safer
Pallet Shuttle system applications
For companies that need high-density storage and maximum throughput
The Pallet Shuttle is the perfect storage solution for boosting productivity in warehouses looking to considerably increase storage capacity while facilitating and streamlining loading and unloading operations.
How does the Pallet Shuttle racking system work?
Semi-automated solution consisting of a shuttle, a forklift and an operator
Using a forklift, the operator positions the pallet shuttle car at the entrance to the channel. Next, they deposit the pallet on the rails, just above the shuttle. The shuttle then raises the pallet slightly and transports it, placing it in the first free location. Operators issue commands to the shuttle from a tablet.
Testimonials
Case studies
See more case studiesStorage configurations with Pallet Shuttle racking
Different distribution possibilities to find the solution that best meets your company’s logistics needs
Choosing which configuration to implement will depend on factors such as the size of your facility, the number of SKUs, the storage capacity needed, the load management system and the required flow of goods.
Pallet Shuttle components
The Pallet Shuttle racking system consists of one or more shuttles, the racking unit in which the shuttle operates, a control tablet and a series of safety elements that protect the integrity of the operators, the goods and the structural assembly.
The Pallet Shuttle car is the core element of this storage solution. It moves mechanically and autonomously thanks to various electronic components (PLC, batteries, antennas, sensors, etc.). It also has a number of safety features to prevent incidents.
Shuttle racking is a high-density structure specially designed to ensure the safe, smooth movement of the shuttle inside it. It has a set of rails along which the shuttle moves and on which the pallets rest.
In addition to the various safety features incorporated in the car, the Mecalux Pallet Shuttle racking system also has a set of accessories that help to reinforce the safety of operators and goods and to comply with regulations in force.
Functions of the Pallet Shuttle control system
High operational versatility thanks to a wide range of functions
FAQs
The Pallet Shuttle — also known as radio shuttle racking or satellite shuttle racking — is a semi-automated high-density storage system that makes the most of the available surface area to achieve a higher storage capacity. It consists of an electrically powered shuttle that, controlled remotely by an operator, moves on rails inside the storage channels to insert and extract pallets autonomously.
The Pallet Shuttle is an evolution of other more traditional high-density storage systems. Compared to drive-in racking, for example, the Pallet Shuttle system makes it possible to house a wider variety of goods. This is because instead of allocating the entire lane to one SKU, each storage channel can accommodate a different SKU. Moreover, forklifts do not enter the Pallet Shuttle racking. This streamlines loading and unloading tasks and makes operations safer by considerably reducing the risk of collisions and accidents. Meanwhile, with regard to push-back pallet racking or pallet flow racks, the Pallet Shuttle allows for deeper channels and better leveraging of the facility’s height, respectively.
Absolutely. Different storage systems can coexist within the same warehouse (selective pallet racking, drive-in racking, Pallet Shuttle, etc.). A common combination, for instance, is to have one area with pallet racking to store a wide range of SKUs with few pallets and another section equipped with Pallet Shuttle racks to house more homogeneous goods with many pallets per SKU.
Yes, by adding the necessary beams and rails to allow the shuttle to move inside the racks.
The Pallet Shuttle is a semi-automated system featuring a shuttle that moves inside the racking automatically. However, it requires an operator to place or remove the shuttle from the rack, to deposit or retrieve the pallets from the entrance of the channel, and to select from the tablet the operation to be carried out.
Nevertheless, Mecalux does offer a completely automatic alternative: the automated Pallet Shuttle. With this solution, forklifts are replaced by a stacker crane or a set of transfer cars, which transport the shuttle and the pallet from the entry point of each storage channel in a completely autonomous way. In addition, in this solution, all operations are orchestrated directly by a warehouse control system (WCS).
Yes, that is precisely one of its main advantages. First and foremost, operators do not have to drive the forklifts inside the racks, as is the case with drive-in racking. In addition, the shuttle itself, which is delivered with the corresponding CE marking, is equipped with multiple devices that ensure its correct positioning within the rails and immediate stop in the event of encountering an unexpected object. The system is also equipped with safety enclosures to limit operator access to the areas in which the motorised shuttle operates and rack safety netting to protect passageways and work areas against the risk of falling loads.
First, the operator uses a forklift to place the shuttle at the entrance to the designated storage channel. Next, the operator places the pallet on the channel rails, just above the shuttle. Using a control tablet, the operator issues the command. The shuttle then raises the pallet slightly to move it to the deepest available location, where it is deposited. This procedure is repeated until the channel is full. Before placing the pallet in the last location, the operator removes the shuttle. To retrieve pallets, the procedure is reversed. However, when working in FIFO mode, unloading is done from the opposite side of the racking.
Yes, the Pallet Shuttle system can operate according to the FIFO (first in, first out) load management strategy, where the first pallet stored is the first to be removed. For this purpose, two working aisles must be set up: a front or loading aisle, where the pallets are deposited, and a rear or unloading aisle, where the goods are retrieved. This prevents interference between the two operations.
The system is scalable, and Pallet Shuttle cars can be added as needed. The recommended number of shuttles is determined by the number of cycles/hour required and by the number of operators actively involved in each work shift. Up to 18 shuttles can be controlled from a single tablet.
Yes, although to do this, the half pallet or odd-sized pallet needs to be placed on a standard pallet, which acts as a slave pallet.
This is highly unlikely, as the Pallet Shuttle car has a battery status indicator that warns the operator when the charge level is low. If the battery were to become completely discharged with the shuttle at the entrance to the channel, a spare battery can be used to bring the trolley back into operation. If, however, the vehicle were to stall at a deeper location, a second shuttle would be inserted to tow it by means of a rescue hook.
Mecalux’s Easy WMS warehouse management software features the WMS & Pallet Shuttle Integration module, a functionality that simplifies and speeds up the operator’s work by consolidating the control of the WMS and of the Pallet Shuttle in a single screen.
Each shuttle can support up to 1,500 kg.
The Pallet Shuttle car can reach a maximum speed of 90 m/min unloaded and 45 m/min loaded.
The shuttle platform lifts the pallet in approximately 2 seconds.
Yes. On the one hand, there are two types of shuttles based on the operating temperature: those that work at ambient temperature (from +5 °C to +45 °C) and those that operate at refrigerated and freezing temperatures (from -30 °C to +5 °C). Shuttles designed to operate in cold environments come equipped with electronic components that are protected and heated to prevent damage.
On the other hand, each type of shuttle comes in three sizes, adapted to the most common pallet measurements. In each configuration, the front measurement of the shuttle is the same, given that in Pallet Shuttle systems, pallets are handled on the wider side (1,200 mm). What varies is their depth, with each configuration corresponding to a different pallet depth measurement (800, 1,000 or 1,200 mm).
The Pallet Shuttle’s lithium batteries provide an autonomy of up to 10 hours at full performance, depending on the temperature and load conditions.
The charging time for the Pallet Shuttle’s lithium batteries is between 4 and 5 hours.
Spare batteries are recommended to ensure uninterrupted operation of the system.
There are no technical limitations on the height or depth of the racking. The dimensions will depend on the particular needs of each warehouse. The depth of the channels will be determined by the homogeneity of the goods and the number of pallets per SKU. The height of the system, meanwhile, will hinge on the maximum lifting capacity of the forklifts used and the height of the facility.
Ask an expert