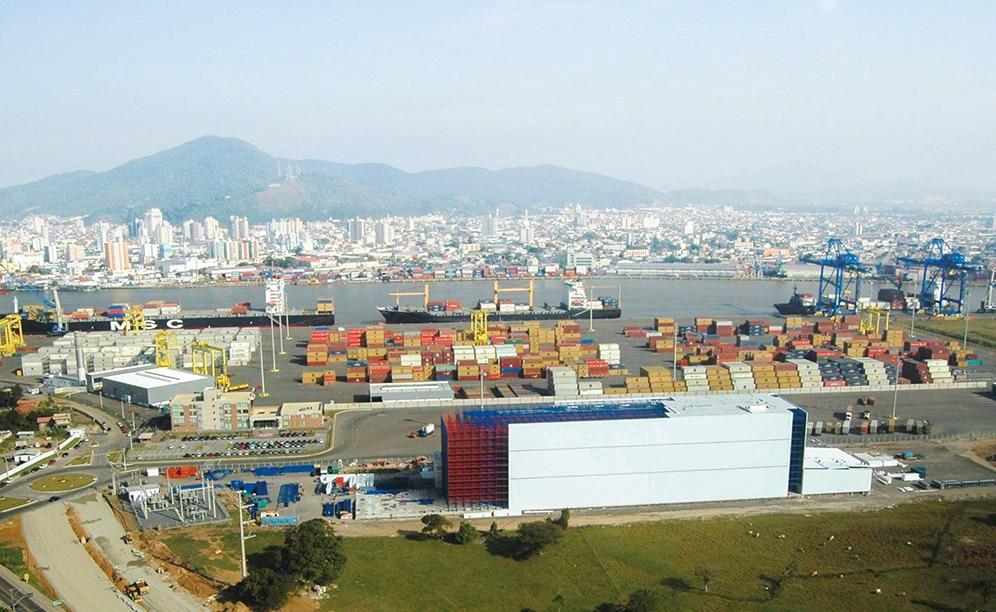
An ambitious project in the port of Navegantes, Brazil, consolidates Portonave’s growth in the Latin American market
Iceport receives a clad-rack automated cold storage

Mecalux has built a clad-rack cold storage for Iceport, a logistics company in the Portonave group, the port of Navegantes’ administrator, in Brazil. The automated warehouse has a capacity of more than 16,000 pallets and all the operations are managed via the Mecalux Easy WMS software. The installation is integrated into the port terminal in order to meet the demands of its customers and enhance the pace of growth and distribution in Latin America.
Who is Portonave?
Portonave is a Brazilian logistics port operator founded in 2001. After receiving the corresponding authorisations in October 2005, they began the construction of the port of Navegantes, in the state of Santa Catarina (Brazil), taking advantage of the growing interest in the private sector, its unique geographical position and the favourable economic conditions of the region.
The location of the navigation channel is strategic and key to the growth of the company and is ideal for the transport of products manufactured in the south of Brazil and destined for the rest of Latin America. In addition, the port is very well connected, close to administrative centres, to the most important highways in the country and the international airport.
The construction of the Iceport warehouse
The company needed to strengthen its position in the Latin American market and enhance the growth achieved in recent years, for that reason they decided to build a large capacity cold storage. They asked for the collaboration of Mecalux to find the most ideal solution, which will proffer all facilities to producers, importers and exporters that operate in the port.
The new Portonave centre for the housing, handling and distribution of frozen goods has been installed next to a cold storage warehouse with pallet racking. Both share 13 loading and unloading docks.
Features of the clad-rack warehouse
Clad-rack warehouses are buildings formed by the racks themselves, which support their own weight, that of the vertical cladding, the roofing, as well as the goods. When designed, provision is also made for other factors that act upon the structure, like wind force, the degree of seismic risk that corresponds to the zone, and also the local regulations in force.
These racks are widely used in cold storage due to surface and height optimisation. They occupy just the space that is strictly necessary, which means savings in the cost of energy to maintain the installation constantly at sub-zero.
The cold storage
The new Portonave clad-rack warehouse is 161 m long, 28.2 m wide, with a height of 31.7 m and operates at a constant temperature of -28 ºC. It is composed of six aisles where stacker cranes circulate, with single-depth racking on both sides.
The stacker cranes work at an average travel speed of 200 m/min and a 50 m/min lift speed, with a capability that allows the handling of more than 280 pallets/hour. These machines move the goods between locations on the racks and the entry and exit conveyors located at one end.
The stacker crane’s operation is very straightforward: a conveyor circuit with rollers and chains constantly directs pallets to enter and exit the warehouse.
In order to protect operators and the stored products, the installation is isolated using metal cladding, fast-acting roll-up doors and safety devices on the elements in motion (conveyors and stacker cranes).
The receipt and dispatch of goods
At the front of the warehouse the input and output of goods is performed thanks to the 13 loading and unloading docks. First, a checkpoint was installed within the input conveyor, which validates that the pallets meet the requirements laid down with regard to weight, state and size. Those that fail to meet standards are redirected to a conveyor for rejected pallets that is placed in parallel, to be reconditioned.
On the other hand, dispatches are separated to avoid interference between both operations. A preload zone is set up on the floor in front of the docks, allocated to the preparation of goods being readied for distribution.
The cold storage warehouse with pallet racking
In the conventional cold storage located next to the clad-rack warehouse, irregular sized load units are deposited. This 1,626 m2 warehouse has capacity for more than 1,500 pallets.
It is equipped with adjustable pallet racks, which are characterised by their versatility to accommodate pallets of any shape or size. Direct access is ideal for Portonave’s needs, because it provides great agility for managing goods and facilitates the introduction and extraction of pallets.
Easy WMS by Mecalux
The Easy WMS warehouse management software developed by Mecalux governs the warehouse. This system is responsible for organising and coordinating the different operations that take place inside the installation.
Some of its features include:
- Management of the input of goods from their reception at the docks.
- Allocation of pallet locations based on consumption and turnover, whose goal is to achieve maximum productivity.
- Organisation and management of stock.
- Control of warehouse outputs to the various destinations.
- Query of the status of the handling equipment.
Advantages for Portonave
- Great storage capacity: the clad-rack warehouse has a capacity of more than 16,000 pallets of frozen products.
- Maximum performance: the installation is fully automated with a very simple conveyor circuit and six stacker cranes that operate in the different aisles.
- Optimal management: the Easy WMS warehouse management software by Mecalux streamlines all movements, processes and operations performed in the warehouse.
Conventional cold storage, Brazil | |
---|---|
Storage capacity:: | >1,500 pallets |
Storage system:: | Conventional racks |
Gallery
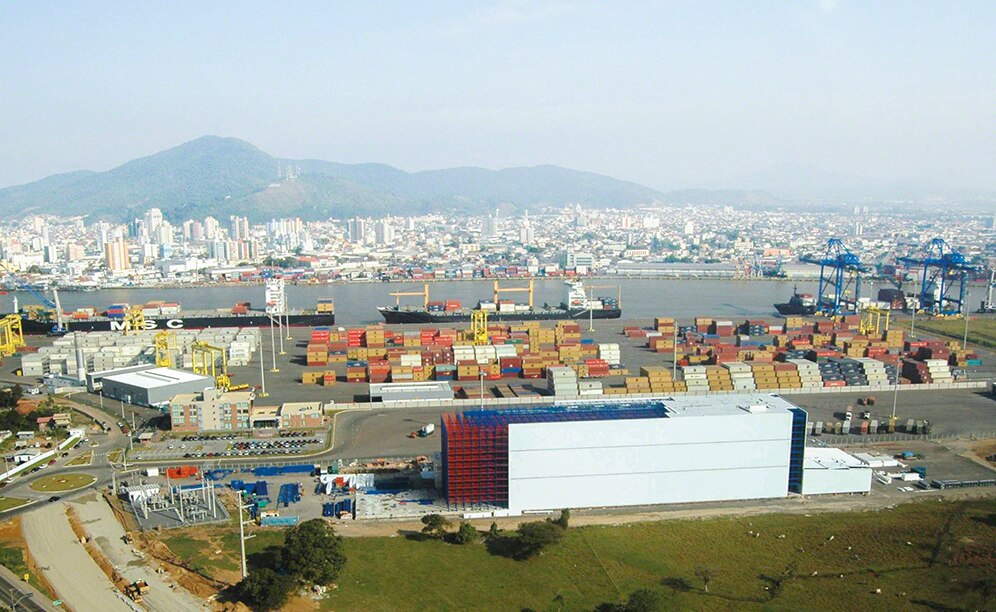
Ask an expert