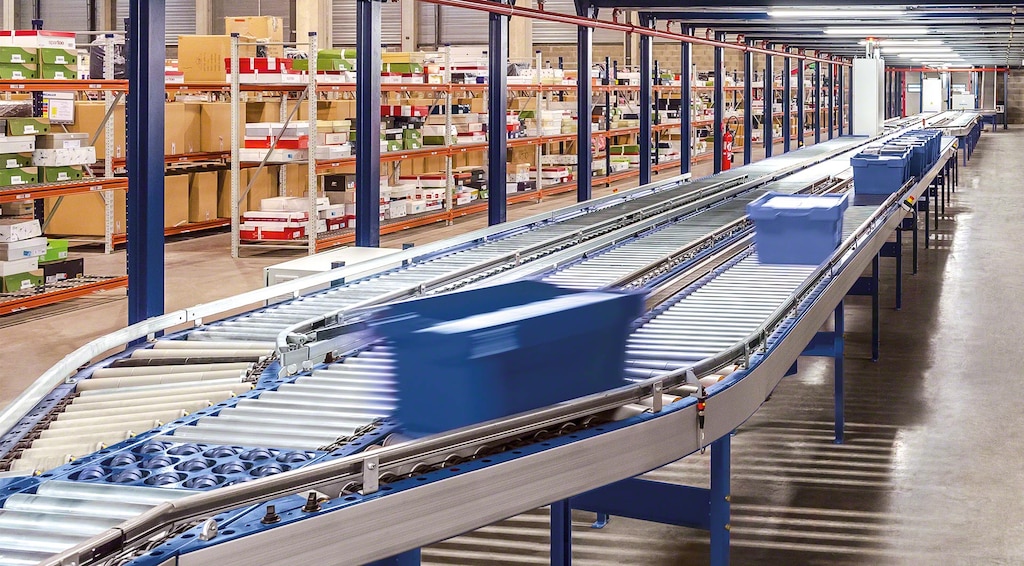
Carton and Box Conveyor Systems
The product
Automating the movement of boxes and lightweight loads in the warehouse
A carton conveyor is a continuous, automated transport solution for boxes and light loads. It can consist of roller, belt or toothed belt modules. The wide range of box conveyor variants and multiple combination options allow for the design of simple or complex solutions tailored to each company’s needs.
Carton conveying systems minimise manual goods handling as well as operator and equipment traffic, boosting productivity while reducing errors and operating costs.
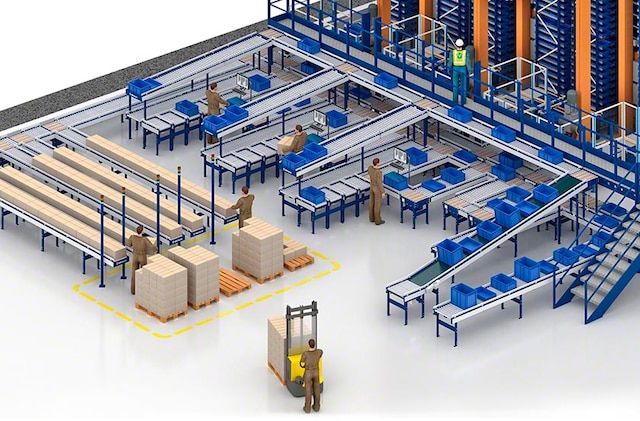
Advantages of box conveyor systems
- Long distances: extensive, complex circuits can be designed to connect the different areas of a facility.
- Constant flow: carton conveyors move goods continuously.
- Multiple unit loads: these systems are compatible with cartons, boxes, trays, totes, bins, cases and crates of various materials and sizes, in addition to other lightweight loads.
- Flexibility and scalability: box conveyors allow for the creation of any type of circuit, while existing systems can be expanded or modified.
- Ergonomic operation: staff perform tasks such as order fulfilment more comfortably with carton handling systems.
- Robust construction: case conveyors are a durable solution for high-performance operations.
- Minimal maintenance: their upkeep is simple and cost-effective.
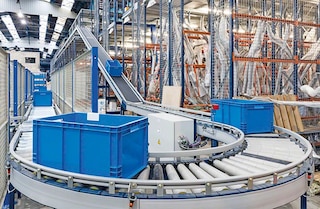
By using carton conveyors, we’ve ramped up our productivity. Our processes are much faster and more reliable
Carton conveyor applications
Highly effective solution adaptable to a wide variety of needs
Box roller conveyors are the perfect solution for automating the movement of cartons and light loads in warehouses with repetitive, constant flows. Thanks to their high versatility, they seamlessly adapt to various operations and accommodate multiple system configurations with varying degrees of complexity.
Testimonials
Case studies
See more case studiesTypes of carton conveyors
Mecalux’s wide range of box conveyor solutions supports multiple distance, path, incline, speed and unit load requirements. The systems’ robust design ensures high reliability in all work environments.
A carton handling system can include both roller and belt conveyors. These machines streamline the movement and handling of boxes, trays, cases and other lightweight loads in warehouses. Standard conveying speeds range from 25 to 60 m/min.
Auxiliary conveyor equipment adapts the circuit layout to meet each facility’s specific needs. These devices help bypass structural obstacles, change the unit loads’ travel direction or create diverging paths.
Carton conveyor accessories
Complementary solutions that improve conveyor system safety and capabilities
FAQs
A box or carton conveyor is a continuous handling system that automates the internal flow of boxes, totes, crates, bins, trays and other light loads. Commonly used in warehouses and production centres across various industries, conveying systems streamline multiple operations, from goods receipt to order fulfilment and dispatch.
Case conveyor systems can transport a wide range of goods stored in boxes, trays and other unit loads of various materials and sizes. They can also handle loose items, packages and even tyres.
Mecalux offers several varieties of carton handling systems, including roller, belt, and mixed roller/toothed belt box transfer conveyors. With box roller conveyors, unit loads are driven by a set of metal cylinders rotating on a shaft and powered by a motor or gravity. In contrast, belt conveyors move boxes and other small unit loads along a continuous surface made of rubber or plastic, which rotates between two motorised drums at the ends of the structure. Finally, mixed conveyors — cross transfer units combining rollers and belts arranged at 90° angles — change the direction or orientation of transported unit loads.
The height of a standard carton conveyor is adjustable, ranging from 570 to 750 mm in horizontal sections and reaching up to 3,000 mm high in inclined segments. The maximum usable width varies by conveyor model but is typically between 400 and 800 mm.
Box and case conveyor systems can handle small unit loads weighing up to 100 kg.
The speed of a box conveyor depends on the characteristics of the unit load transported and ranges from 25 to 60 m/min.
Thanks to Mecalux’s wide range of conveyors, any type of layout can be designed, from simple straight-line systems with one point of origin and one destination to complex circuits with multiple entry and exit points. This versatility ensures the system adapts to specific operational needs. Curved conveyors, for example, help navigate architectural obstacles, while cross transfer conveyors change the direction and orientation of unit loads.
Yes, conveyor lines can link various levels via box conveyor belts as well as continuous or discontinuous box elevator conveyors.
Carton conveyor systems are flexible, scalable solutions that can be adapted to warehouse requirements at any given time. This means the circuit can be expanded or the route changed as needed.
Yes. Any conveyor solution requires a warehouse control system (WCS) to govern its operation. The WCS instructs the conveyors to move, stop or turn unit loads based on pre-parametrised logical sequences that consider the route, number of conveyors and other circuit elements. The WCS should not be confused with a warehouse management system (WMS), which functions at a higher level. More complex circuits require both a WCS and a powerful WMS — such as Mecalux’s Easy WMS — to direct unit loads from origin to destination according to each facility’s specific criteria (order, sequencing, etc.).
Yes, there are two solutions for this. One option is to install conveyor crossovers that enable personnel to walk over the system. The other is to integrate sections with conveyor gates that can be lifted to one side, creating ground-level passageways. This second solution is recommended if handling equipment needs to pass through the conveyor lines.
Ask an expert