
Hipanema: the WMS that’s all the rage
Seasonality was the main challenge when implementing Easy WMS in Hipanema's facility in Paris, France
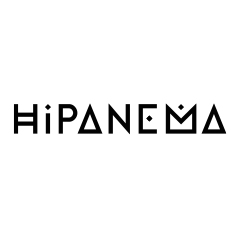
French fashion jewellery and ready-to-wear clothing brand Hipanema continues to modernise its business. To keep growing and optimising its logistics operations, the company has decided to partner with Mecalux, which will equip it with Easy WMS, its latest-generation warehouse management system (WMS). The seasonality of Hipanema’s business was the main challenge when it came to implementing the WMS in the firm’s warehouse in the Paris region.
Ethnic fashion in vogue
The name Hipanema was inspired by Ipanema, one of Brazil’s most iconic neighbourhoods, which conjures up pleasant sensations of sunny beaches and cocktails by the sea.
In business since 2012, Hipanema is a French fashion jewellery brand with an international presence. Entrepreneurs Jenny Collinet and Delphine Crech’riou created colourful bracelets that launched them to fame. Since then, they have sold millions of units all over the world.
The Hipanema founders are constantly updating and renewing their brand. Nowadays, through its summer and winter collections, the retailer’s fashion accessories, bracelets, necklaces, swimwear and ready-to-wear, boho-chic-inspired clothing are purchased by more and more women.
In 2018, at a time when sales were growing rapidly, Hipanema turned to Mecalux in order to improve its supply chain.
Seasonal logistics
The company’s warehouse in the Paris region houses all the items in its collection — around 300 SKUs per season — which are subsequently sent to over 300 sales outlets in France and abroad. Twice a year, in connection with the launch of a new collection, the firm reorganises the merchandise in its centre, replacing the old with the new.
Initially, the goods were controlled manually, with a list on paper, whereby employees stored the products in their locations in the shelves in alphabetical order. However, those working methods became obsolete in this fast-growing facility. “When a new SKU would arrive, we’d have to move all the warehouse stock to make room for those new products,” explains Jenny Collinet, Managing Partner at Hipanema.
Daily activity in the warehouse became increasingly hectic, reaching 300 orders with the launch of a new collection. “We work with demanding shops, so we have to avoid making mistakes to make sure our orders aren’t rejected. That’s why we’re extremely strict when it comes to the quality of our service,” says Collinet.
In view of its constantly changing business — with faster operations and a wide variety of SKUs in stock — Hipanema realised it needed to reduce the risk of error and rigorously manage its entire supply chain. “The time had come to digitise our logistics systems with the help of a warehouse management system,” says Collinet.
Digitisation of the supply chain
After analysing various warehouse management systems (WMS), the company chose Easy WMS from Mecalux, for several reasons: “because of its ability to adapt to the particular quirks of our business, its intuitive use and its easy integration with our Sage 100c ERP system,” indicates Jenny Collinet.
“Our team got together with the Mecalux team on a number of occasions because we wanted to be sure that its WMS would meet our criteria and expectations,” says Collinet.
Easy WMS integrated with Sage 100c
The warehouse management system Easy WMS has been integrated with Hipanema’s Sage 100c ERP system. This was essential so that both systems could transfer data and information to improve management of the facility. To ensure an optimal connection between both IT programs, the Hipanema, Mecalux and Sage teams worked closely together.
Although the WMS from Mecalux can be connected to any ERP system, it was necessary to define which information each software program required. To do this, numerous tests and interface validations were run during the project phase. After making some adjustments, the two systems were coordinated, and the WMS was fully operational.
“Today, thanks to this communication, customer orders can be prepared as soon as possible. The sales department, for its part, has access to the status of the stock in real time, giving us better visibility of delivery times,” says Collinet.
On-trend logistics
Orders are no longer prepared using paper, and picking errors are a thing of the past. Since Easy WMS has come into play, everything in the Hipanema warehouse is perfectly coordinated.
The WMS from Mecalux manages and enhances operations in the Hipanema centre, from the time products are received through to order dispatch. Easy WMS communicates with the operators in real time, sending them instructions via an RF scanner so that they know where to go and which items to handle. And it does all of this while minimising operator travel, thanks to a route optimised by the system itself.
- Goods receipt. Operators use RF terminals to individually identify items as they arrive at the warehouse. Reading the barcode, they verify that the label corresponds to the product; that is, they make sure they have received the right products.
- Storage. The operators move the goods to the locations assigned by Easy WMS. This WMS organises the products by SKU (bracelets, dresses, swimwear, and so on). Likewise, it is programmed specifically to replenish the picking slots before they become empty. “Thus, the operators can concentrate solely on the instructions the WMS gives them. The advantage is that there are no interruptions: the employees preparing orders are never held up due to lack of stock,” says Collinet.
- Order picking. Two types of orders are prepared: small (made up of few items to replenish individual shops) and large (with many SKUs, mainly from retail outlets in shopping centres). For small orders, operators locate the items requested and bring them directly to the packaging area. In this process, Easy WMS checks that the employee has picked the correct product and quantity. On the other hand, with large orders, operators go around the warehouse with a cart, which they fill with all the items indicated to them by Easy WMS. They then bring the cart to the consolidation area, where it is verified that they have picked the correct product quantities. Collinet says, “Thanks to this way of working, we’ve eliminated mistakes in order prep and can provide the service our customers expect from us.”
- Consolidation and dispatch. Once the orders are finished, they are packaged and labelled. To improve effectiveness in shipping, Hipanema has installed the Multi Carrier Shipping Software module. This app is automatically synced with Station-chargeur, the software used by Hipanema’s carriers. Thus, the WMS sends to DHL all the information on the orders to be distributed (number of pallets, sizes, weight, destination, etc.) and prints the labels and necessary documentation.
- Returns. Previously, products returned by customers were temporarily stored on the floor. The operators would then verify their status to decide what to do with them (store them, repair them, etc.). Now, Easy WMS assigns the returns a location on the shelves until they can be inspected. “This way, everything is better organised, we no longer have products on the floor and returns management is much more efficient,” highlights Jenny Collinet.
A facility at the cutting edge of fashion
Hipanema is a French fashion company with highly seasonal logistics operations and a warehouse that is reorganised every season. Additionally, its international distribution network calls for the need to carry out strict control of the goods and of the entire supply chain.
“Easy WMS is a system capable of enhancing all operations, from goods receipt to dispatch,” says Collinet. The WMS has streamlined the job of the logistics manager, who can now devote time to managing the team, assigning tasks, and so forth. Moreover, the logistics manager has a comprehensive, reliable view of all actions in real time.
Optimal organisation of operations such as picking and dispatch has boosted the productivity of the facility and of the operators. New employees who arrive at the warehouse learn how to use Easy WMS in just two hours. The system then guides them at every turn. For Collinet, “The most difficult thing was learning to trust the software. Now, we allow ourselves to be guided by Easy WMS’s instructions because it works really well.”
This software is flexible, scalable and can easily adjust to changes in the business. Hipanema was able to verify this in 2020, when it moved to a new facility. Mecalux’s technical team designed a simulation of the new warehouse (with the various working areas and locations) so that, when the goods arrived, they would already have a preassigned storage location. “When moving the pallets to the new warehouse, the operators simply had to identify the products, and the WMS told them where to put each item. Thanks to Easy WMS, the move from one facility to another was practically seamless,” says Collinet.
Today, Hipanema has a modern, computerised warehouse. Easy WMS has completely optimised the company’s logistics flows, helping it to reach its targets and leveraging its supply chain to ensure the success of future collections.
The Easy WMS warehouse management system has raised the productivity of our facility and, thus, of our business. Plus, this software optimises all operations, from goods receipt to dispatch.
Advantages for Hipanema
- Seasonal logistics: Hipanema reorganises its warehouse twice a year, when it launches a new collection. Easy WMS ensures that this process takes place quickly and without error.
- Increased control: the company has benefited from total reliability in all processes, including goods receipts from suppliers, returns management and the shipment of numerous orders prepared every day.
- Accurate dispatches: the Multi Carrier Shipping Software module has enhanced order shipments by automatically generating all necessary documentation for carriers.
Ask an expert