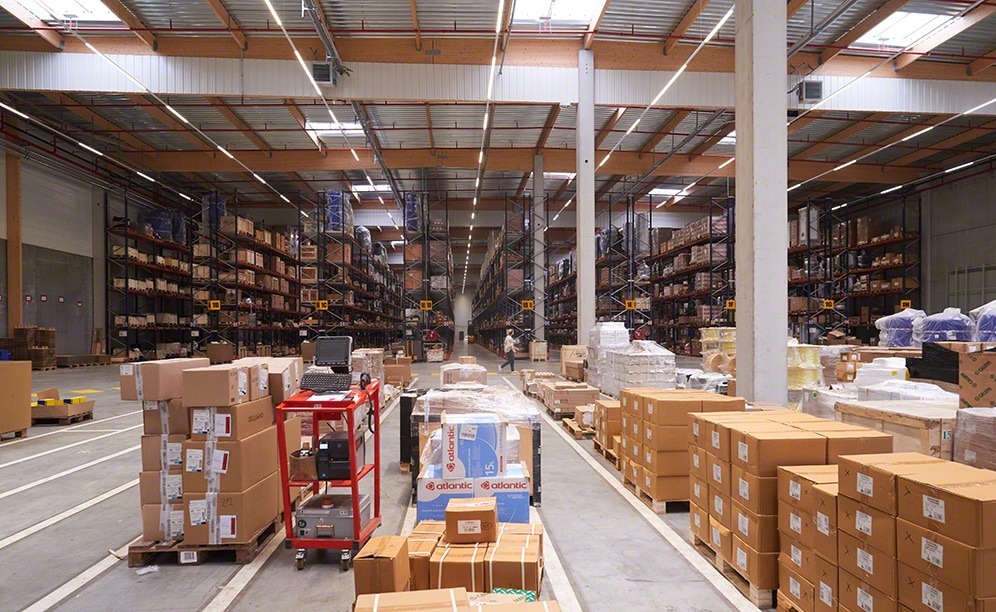
Solutions for the industrial parts warehouse of Sofinther
Sofinther’s warehouse is filled with accessories and components for heating and cooling systems
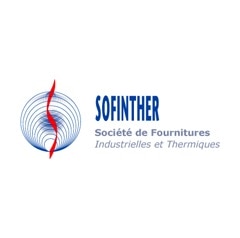
Sofinther, a thermal technology engineering firm, has constructed its distribution centre in Saint Hilaire de Loulay (France) by setting up pallet racks, shelving for picking, cantilever racks and a box conveyor system in the consolidation zone. All these solutions by Mecalux have multiplied the initial storage capacity by five and, likewise, mean the company can fulfil more than 300 orders daily.
The heating experts
Founded in 1982 and with its headquarters in Nantes (the Loire-Atlantique region of France), Sofinther is a subsidiary of the Rexel Group specialised in thermal technology engineering. It distributes heating units (boilers, regulator units, radiators, etc.) to companies that build dwellings, hospitals, industrial buildings, etc.
Sofinther has more than 250 employees and more than 30 branches from which it services its customers’ needs throughout all of France. In 2016, it built a 20,000 m2 logistics platform in Montaigu-Vendée that, recently, has been reorganised through a collaborative effort with Mecalux.
The company needed to face its current growth and what the future would bring. In the words of Lionel Lenroué, logistics manager at Sofinther, “we had to line up five times more storage capacity than we started out with. So, we deployed an adaptable, business-friendly solution that would, in parallel, increase the performance levels of all in-house operations.”
Lionel Lenroué - Logistics manager at Sofinther
“We approached Mecalux because of its reputation, quality products and prices.The warehouse has brought about excellent results and we are highly satisfied with the installed systems, the assembly process and the hands-on advice Mecalux’s technical team has provided throughout the process.”
Two different areas, one warehouse
Sofinther’s warehouse is divided into two zones for safety reasons due to the type of operation and to fulfil local regulations with regards to fire safety and prevention.
The two storage areas are very similar in size and characteristics. In one of these areas, Mecalux has set up 9.5 m high pallet racks allocated to large-sized palletised products, such as boilers, expansion vessels, hot water tanks, etc. Meanwhile, the other is equipped with shelving for picking (for small-sized items like accessories, measuring units, etc.) and cantilever racks for much longer unit loads (pipes).
In this centre, Sofinther manages around 13,000 SKUs of various sizes, characteristics and rotations. Into the bargain, it receives an average of 100 pallets a day flowing, mainly, from France and Eastern Europe, and distributes 200 pallets and 200 boxes throughout the entire country.
Proper organization of warehouse tasks and picking is essential to attain this volume and work pace. In this sense, the racks play a main role. As Lionel Lenroué highlights, “Some of our products weigh just ounces, others weigh 1,000 kg; some are centimetres long, while others run more than 2 metres. So, these very versatile systems are ideal for our diverse stock.”
Racking components can be modified and adapted to the different sizes of the unit loads. Thus, some racks have six storage levels, while others only have four in order to deal will larger-sized pallets.
Hyper-pick warehousing
Daily, the company processes close to 300 orders, each comprised of various lines. Thus, a well-organised team of workers is essential to progress in order fulfilment tasks and ensure that customers have products as soon as possible.
Each operator is assigned a certain zone. Their work consists of walking the aisles picking the products that comprise each order directly from the pallets and shelves. Operators follow the order grouping method, i.e., they put together several orders at a time on the same picking route.
The racks allocated to picking stand an impressive 9.5 m high. One of their interesting features is that pick shelves are located only 3 m below, while palletised reserve products are set in the 6.5 m above. As such, needed goods are always available and picking runs uninterrupted.
This positive change is a real asset for Sofinther, as Lionel Lenroué explains, “by expanding the storage capacity and pushing our order fulfilment productivity in the right direction, we can supply our branches quicker than ever.”
Conveyors to the rescue
Mecalux has installed a box conveyor circuit in the consolidation zone. Its height facilitates the flow of operators and handling equipment below.
In the consolidation zone, orders are validated for correctness and that no mistakes were made so that workers can go ahead with packaging, labelling and issuing of required documentation for their distribution.
Advantages for Sofinther
- 5x bigger storage capacity: Sofinther has expanded its distribution centre’s storage capacity. Currently, it has space for 11,772 pallets and 9,000 boxes.
- Quality, efficient service: Sofinther’s merchandise is sorted as per its size and demand level, which speeds up storage tasks and item picking.
- Direct access to products: the racking facilitates product access so that operators can process more than 300 orders a day.
Sofinther’s warehouse | |
---|---|
Storage capacity: | 12,000 pallets |
Pallet size: | 800 x 1,200 mm |
Max. pallet weight: | 1,000 kg |
Racking height: | 9.5 m |
Racking length: | 76.5 m |
Gallery
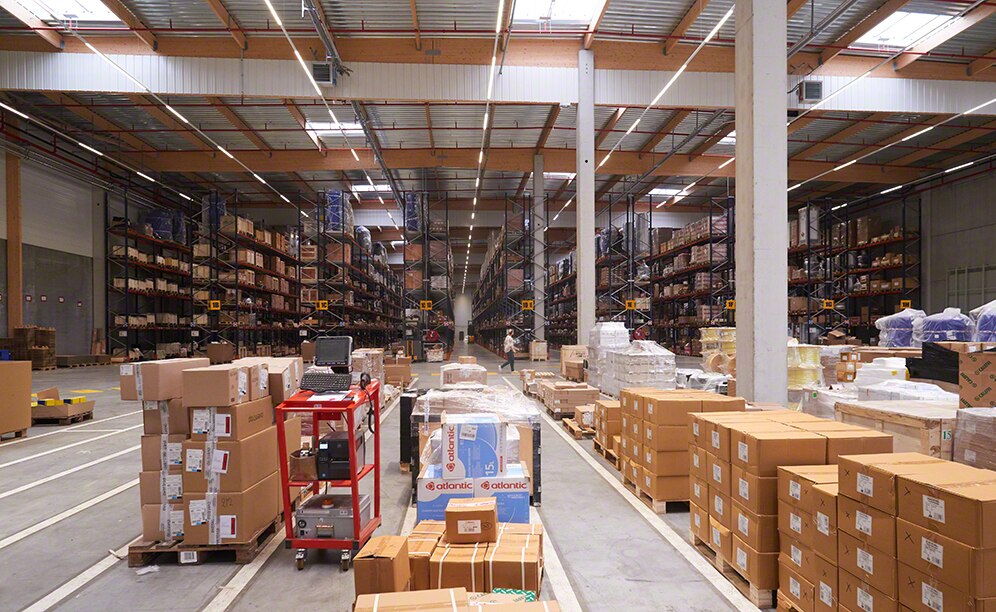
The industrial parts warehouse of Sofinther in France
Ask an expert