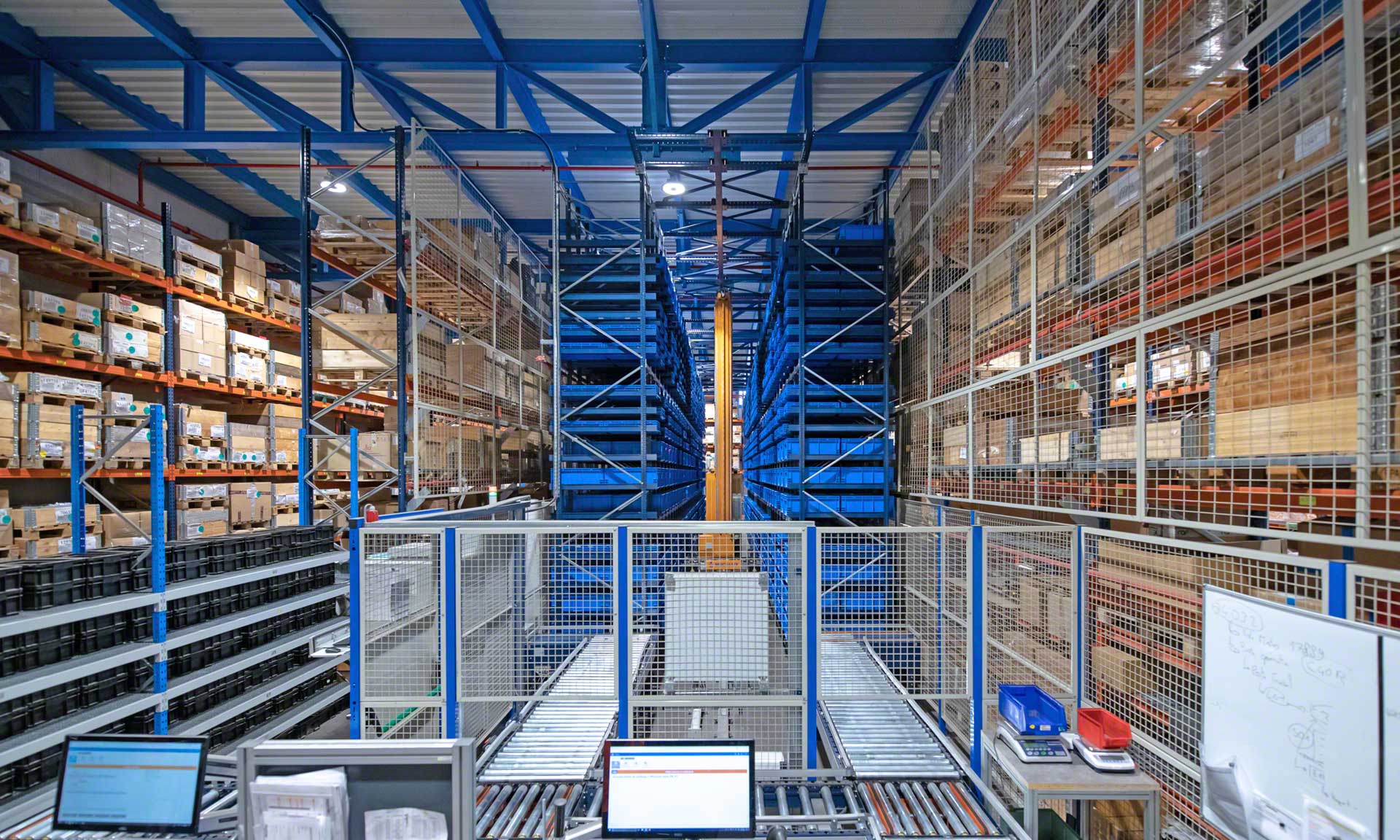
PELLENC: Logistics 4.0 for a just-in-time strategy
In the miniload system, PELLENC stores 2,280 boxes in just 85 m² of surface area
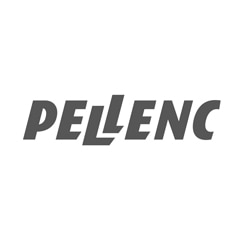
Managing over 20,000 SKUs of different sizes and turnover calls for logistics operations that are organised as well as efficient. With this in mind, PELLENC, a French designer and manufacturer of tools for viticulture, fruit growing and maintenance of urban green areas, has transformed its logistics centre in Pertuis (France) with the installation of a new automated storage and retrieval system (AS/RS) for boxes and the Easy WMS warehouse management software from Mecalux. With this comprehensive solution, the company has increased its operational throughput by 12%, preparing up to 1,000 order lines a day to supply the production lines at just the right time.
Agriculture and progress
Up and running since 1973, PELLENC develops sustainable technology solutions aimed at facilitating the work of operators, reducing their fatigue and optimising production quality. The company has eight production plants and 19 subsidiaries worldwide where it produces, distributes and sells its machines to over 500,000 customers.
The firm is convinced that technology is indispensable for driving its business and progress in the primary sector. Therefore, automation is found in most of its processes (including logistics). The purpose? To provide improved service and efficiently meet its customers’ needs.
From manual logistics to robotics
PELLENC’s commitment to automation is on display in its modern logistics centre in Pertuis, where it manages more than 20,000 SKUs (from spare parts sent to the production lines to finished products distributed to customers around the world). Although the company now boasts a high-tech logistics centre, PELLENC Logistics Manager Syril Spinosi acknowledges that this was not always the case: “We used to manage all our products using conventional logistics solutions for picking and storage.“
Before making the technological leap, the company had stored all its products on double-deep pallet racking. As the business expanded and the production rate became more intense, this storage system ceased to be effective.
This was because all goods management was carried out manually, and the operators, aided by forklifts, had to insert and remove the pallets from their locations. “We realised that if we wanted to optimise the throughput of our logistics centre, we had to overhaul our operations,” says Spinosi.
The first step to modernising the firm’s logistics operations involved reorganising the distribution of the goods, taking into account their size and characteristics. To do this, PELLENC sought a “specific solution for small items that would make the most of the storage space, speed up picking tasks and reduce errors,” says Spinosi.
The company has transformed its logistics centre with the installation of single-deep pallet racks and an AS/RS for boxes managed by Mecalux’s Easy WMS, a technological solution that enables companies to monitor their stock, providing total traceability. It does this by assigning a location to each box the minute it arrives at the warehouse, giving the company full control over entries and exits.
AS/RS for boxes: characteristics
One of the features of this miniload system that most impressed PELLENC is its ability to leverage the surface area and accommodate a larger amount of raw materials: in just 85 m², the company stores 2,280 boxes.
The AS/RS for boxes comprises a single aisle with single-deep racking on both sides. As the company works with boxes of two different heights (240 and 120 mm), the slots in the racks had to adapt to that peculiarity. The lower levels are used for the larger boxes and the upper levels for the smaller ones.
In the aisle, a stacker crane deposits and extracts the goods from their locations quickly, safely and with full autonomy. Additionally, this robot ensures the continuous movement of boxes without any chance of error.
“The AS/RS for boxes has allowed us to maximise space, increase capacity, and effectively integrate ourselves in Logistics 4.0,” says Spinosi.
Order picking
The main operation of this logistics centre is order preparation to supply the production lines with raw materials just in time. Inefficient operations would jeopardise the rest of PELLENC’s supply chain. Therefore, with a view to preparing over 1,000 lines a day, the company is extremely strict in guaranteeing the correct organisation and distribution of the goods.
Orders are prepared in both the AS/RS for boxes and the pallet racks in two different ways. At the pallet racks, picking is done according to the person-to-goods method. In other words, the operators travel up and down the aisles using carts in which they place products as they remove them from the pallets. These carts, carrying larger items, are deposited in a temporary storage area and sent to production at the appropriate time.
Meanwhile, in the miniload system, orders are prepared in line with the goods-to-person concept. To do this, two pick stations have been set up at the front of the warehouse. Operators remain there as the goods are brought to them automatically by means of orders sent by Easy WMS and executed by stacker cranes and conveyors. Thus, the operators merely need to remove the products from the boxes and leave them on pallets. Once the orders are completed, they are moved to the production lines. “With this picking system, our operators are more productive. Plus, they can prepare orders more ergonomically,” says Spinosi.
Easy WMS orchestrates this operation to enable the workers to process a larger number of orders in less time. The WMS tells them which and how many items they require to put together each order. By following these instructions, the risk of error is practically zero. “With the implementation of Easy WMS, our centre's throughput has risen by 12%. At the same time, we’ve streamlined all administrative tasks relating to information management,” says Spinosi.
Modern, high-tech logistics
PELLENC has revamped its logistics centre with two main goals: to optimise the storage of 20,000 SKUs and boost the throughput of its operations, especially picking.
PELLENC now has a warehouse adapted to Logistics 4.0 with improved flexibility and responsiveness. Likewise, the implementation of Easy WMS has enabled it to reach its target efficiency, minimising errors in the preparation of over 1,000 order lines a day.
“Our company is going through a phase of unprecedented growth, which has compelled us to make sure our logistics operations are able to meet all our needs and objectives,” says Spinosi.
We’re thrilled with the improvements resulting from the new storage and management solutions from Mecalux. We decided to automate our operations to ramp up throughput, enhance stock management and speed up order prep.
Advantages for PELLENC
- Management of 20,000 SKUs: larger products are stored on pallets, and the smaller ones are housed in the miniload system.
- Over 1,000 order lines per day: the pallet racks offer direct access to expedite picking, while the miniload system follows the goods-to-person method.
- Leveraged space: the AS/RS for boxes optimises the available space to accommodate the largest number of products. The company stores 2,280 boxes in just 85 m².
- Just-in-time operations: the PELLENC logistics centre is designed to supply the production lines without interruption.
AS/RS for boxes | |
---|---|
Storage capacity: | 2,280 boxes |
Box sizes: | 400 x 600 x 120/240 mm |
Max. box weight: | 50 kg |
Racking height: | 6 m |
Racking length: | 17 m |
Gallery
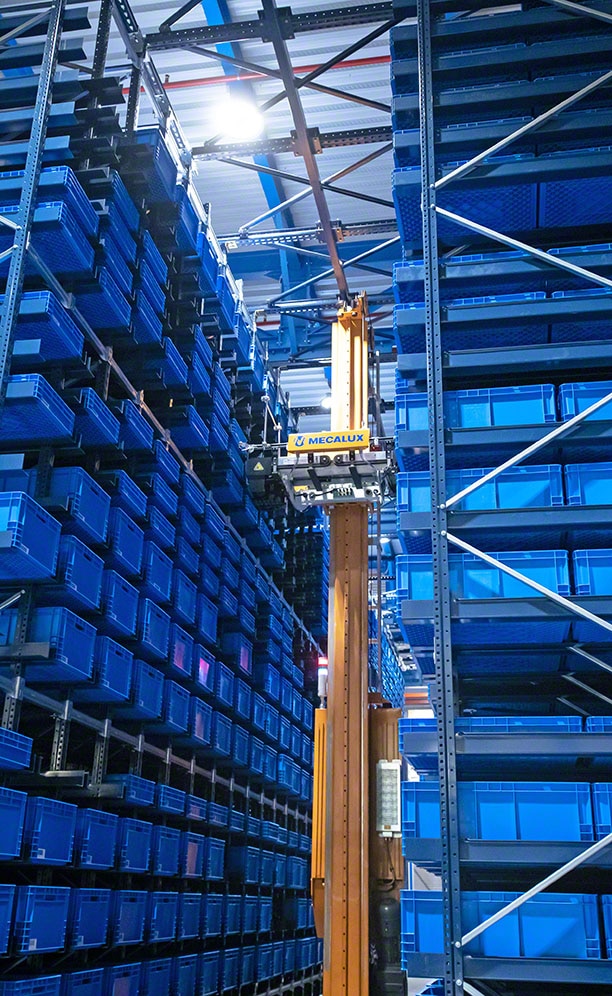
New PELLENC AS/RS in Pertuis for tools
Ask an expert