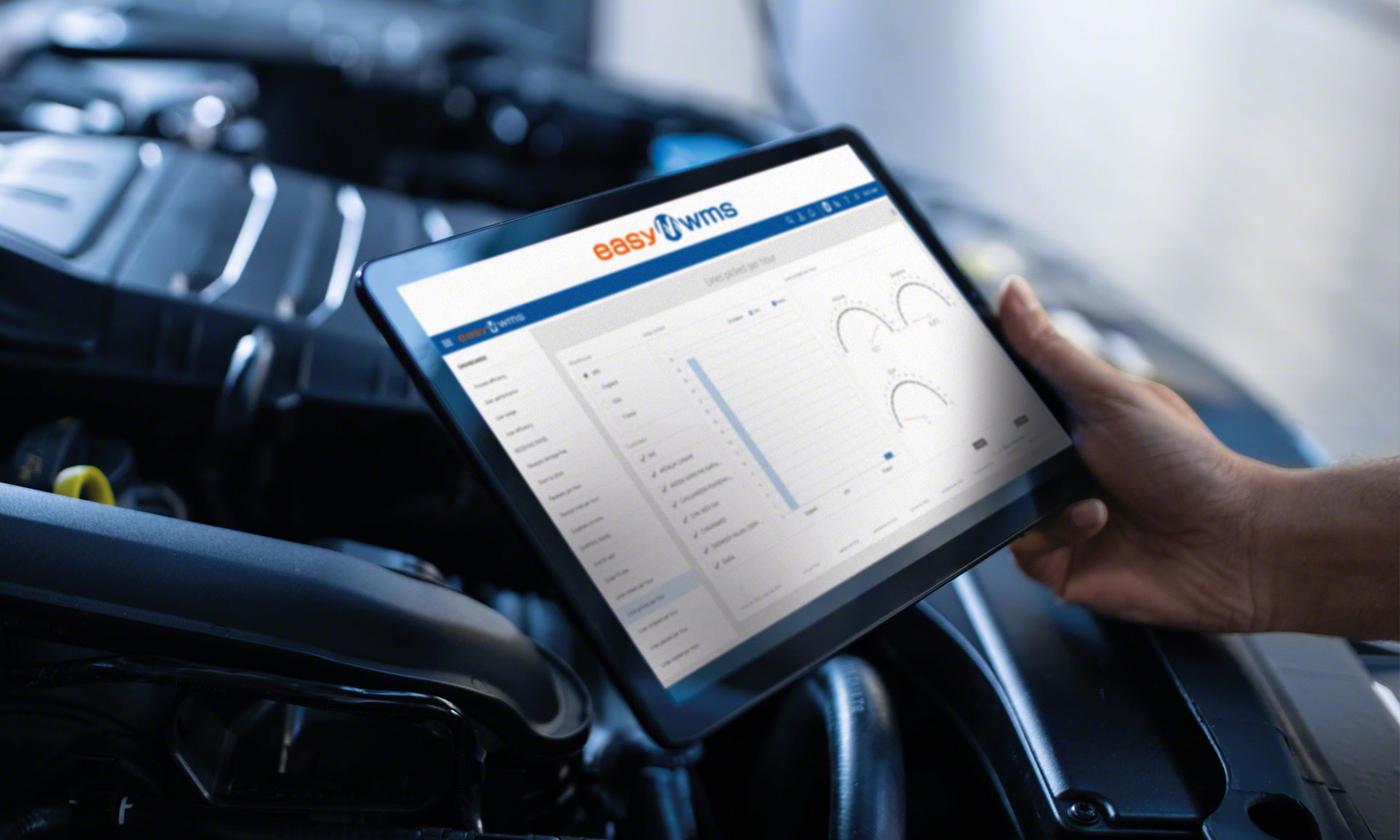
Distrimotos and Integrando automate their shared warehouses with Easy WMS
Distrimotos and Integrando, two automotive and spare parts businesses, drive continuous improvement with Easy WMS.
Spare parts companies Distrimotos and Integrando have digitalised their two warehouses in Colombia with Mecalux’s Easy WMS software. The system controls SKU status in real time and organises operations to boost efficiency.
Distrimotos and Integrando: the core of the auto industry
Founded over 40 years ago, Distrimotos and Integrando are two Colombian companies that are part of the Cassarella group. Distrimotos distributes spare parts for auto garages, petrol stations and the automotive industry. Integrando is a business with expertise in the metalworking sector, designing and manufacturing auto parts replacements. The two companies were founded in Pereira, Colombia and have a total surface area of 4,500 m².
CHALLENGES
|
SOLUTIONS
|
BENEFITS
|
---|
Transformation and adaptability are fundamental for the expansion of any organisation. In Colombia, Distrimotos and Integrando, two leading companies in the automotive and spare parts industry, set out to implement continuous improvement processes in their supply chains. Their top priorities were to boost productivity and provide customers throughout the country with more competitive service.
The companies, which belong to the Cassarella group, share two warehouses in the city of Pereira. There, they store over 11,200 SKUs — 8,200 belonging to Distrimotos and 3,000 to Integrando — of different sizes, turnover rates, attributes and demand levels.
Both businesses have seen significant increases in sales in recent years. To successfully meet demand, they realised they needed to optimise management of their logistics operations. To do so, Distrimotos and Integrando decided to equip the two facilities with Mecalux’s Easy WMS warehouse management system. This software — which automates processes such as inventory control — has led to a considerable improvement in customer service.
“The search took more than a year. We were looking for a digital solution for our logistics operations with good references in the industry and that would bring us benefits like optimised product flows and strategic organisation of locations,” says a Distrimotos and Integrando representative.
Stock control across two warehouses
“One of our main requirements when installing Easy WMS was more reliable inventory. The information we manage on our stock has to be accurate and match the merchandise available in either of our logistics facilities,” he says.
With such a large number of SKUs owned by two different companies and spread across two separate facilities, the risk of errors is very high. Easy WMS monitors the status of spare parts from their arrival at one of the two warehouses through to their distribution.
Every day, both facilities receive a multitude of SKUs sent by suppliers from multiple locations in Colombia and other countries, including Brazil, China, the US, India, Japan, Mexico, Panama, Thailand and Taiwan, among others.
In the receiving area, operators simply have to read the barcode of each item with their RFID scanners for Easy WMS to identify the product. The software then classifies and organises the goods based on whether they belong to Distrimotos or Integrando and assigns them a location according to their characteristics and demand level.
“With Easy WMS, we’ve expedited our putaway and replenishment processes. We now have such detailed control of our inventory that we can ensure product traceability. In addition, we always know we have the merchandise necessary to assemble and ship customer orders without delay,” says the representative of Distrimotos and Integrando.
More efficient order picking
“Our two warehouses generate a high volume of daily operations, with constant inflows and outflows. We have to control processes to guarantee order and avoid errors,” says the Distrimotos and Integrando representative.
Easy WMS organises the different activities that take place in both facilities. It distributes work by sending personalised instructions to each operator. Picking, in particular, has increased dramatically thanks to Easy WMS. “The WMS software is responsible for overseeing all operations, from order processing through to shipping,” says the companies’ representative.
Operators follow instructions from Easy WMS to locate the required spare parts more quickly. “Each order includes a variable number of lines, ranging from between 15 and 20 to more than 600. So the software is capable of adapting to the needs of any customer,” says the representative.
Efficient organisation of picking has been decisive for the two businesses to fill and ship up to 200 daily orders to customers in Colombia and other Latin American countries (primarily Costa Rica, Ecuador, Guatemala, Panama and Venezuela).
Distrimotos and Integrando also sell kits, which are assembled and delivered to dealerships and garages. Operators locate the items required to put together the kits and move them to a specific assembly area. Easy WMS assigns a kit to a single operator for that person to retrieve all the necessary products.
Measuring productivity
“Continuous improvement based on data analysis is critical for driving our businesses. We want to constantly analyse the performance of both warehouses to detect areas for enhancement in our logistics processes,” says the representative of the two companies.
The goal of Distrimotos and Integrando is for their logistics operations to be more flexible, scalable and capable of adapting to customers’ most demanding needs. To achieve this, both businesses have installed Supply Chain Analytics Software and Labor Management System. These two extensions of Easy WMS incorporate functionalities that monitor all logistics activities.
Supply Chain Analytics Software
This program collects data on all operations performed in both facilities. Thus, Distrimotos and Integrando can assess the throughput of their processes and obtain an overview of the various activities taking place. “We really like how the program handles data and presents info through the graphs. It gives us valuable insights into our warehouse operations,” says the representative.
Supply Chain Analytics Software incorporates advanced dashboards that cover the majority of functionalities to be considered in a facility. At a glance, logistics managers can check multiple supply chain key performance indicators (KPIs). Examples include goods receipt status, warehouse occupancy rates and orders pending fulfilment.
Labor Management System
This digital solution monitors workflows in the two facilities, providing information to help both companies’ logistics managers identify ways to ramp up productivity.
“Our employees are the foundation of our business. With this software, we’re aiming to reinforce our commitment to customers and become more efficient. To scale up productivity, it’s vital for us to monitor, measure and plan activities in our warehouses,” says the Distrimotos and Integrando representative.
Two optimised facilities
Managing two warehouses for two different companies, with a total of 11,200 SKUs, is a challenge that calls for strict control of stock and operations to prevent interference.
“Easy WMS meets our logistics needs. With this software, processes are much more organised, so we can focus on what we do best: providing quality service to our customers,” says the automotive and spare parts businesses’ representative.
With the help of digital technologies, Distrimotos and Integrando have centralised their inventory management on a single platform. Moreover, they have automated administrative tasks, raised productivity and gained more thorough control of their processes. These two companies demonstrate how digitalisation is an asset in helping businesses overcome complex logistics challenges.
Easy WMS is an advanced software program that has accelerated our logistics processes. Its key advantages include complete visibility of operations and products, reduced errors, improved service levels, traceability and automatic task organisation.
Ask an expert