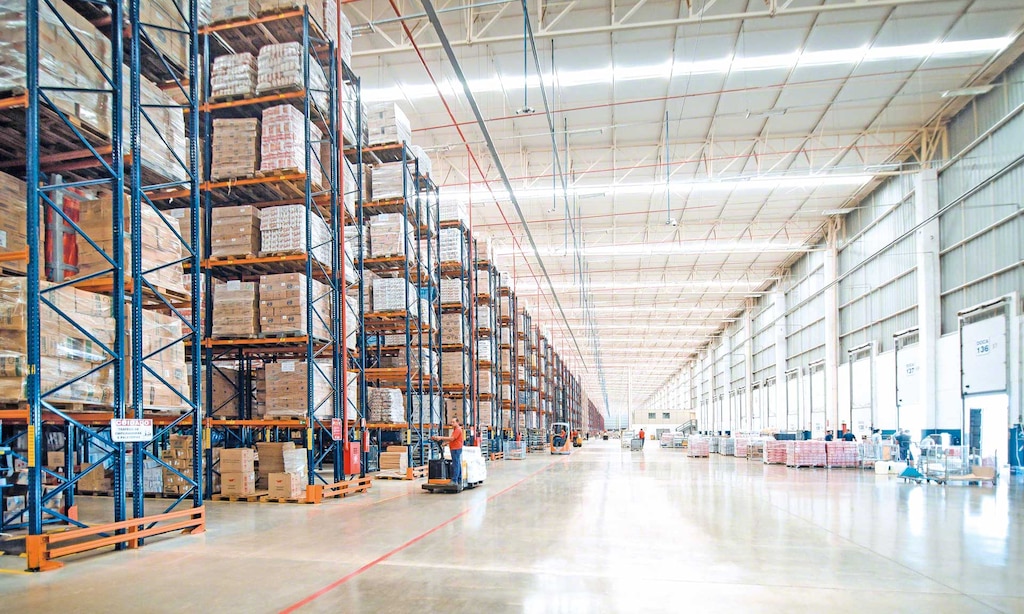
LOGISTICS RESEARCH
By Negin Jamili, Pieter L. Van den Berg and René De Koster
Numerous actors are part of a supply chain, and cooperation among them has the potential to improve their performance. In logistics facilities, organisations can collaborate by sharing resources such as storage space, order pickers or dock doors. This practice reduces both labour and warehousing costs.
There are several ways of achieving collaboration in logistics centres. Retailers, for example, can coordinate to contract a logistics service provider (LSP) to manage a shared warehouse. Kimberly-Clark and Unilever employed this strategy with Kuehne+Nagel. The LSP set up a joint consolidation centre that stores and distributes the finished products of these manufacturers. Because 60–70% of the customers of these two companies overlap, they were able to combine their transport and warehousing activities. As a result, they achieved savings in both the storage and distribution stages.
Another option is to utilise an urban consolidation centre (UCC). Many municipalities have established UCCs in response to the increase in the volumes of urban freight transport and to mitigate the negative consequences, such as noise pollution.
Lastly, organisations can employ multi-user warehouses owned by LSPs. These centres manage the goods of several businesses simultaneously and offer greater flexibility in terms of storage space. However, they also tend to entail a higher cost per unit of storage or product movement compared to private facilities.
Our study focuses on a collaborative warehouse of these characteristics, similar to the one operated by CEVA Logistics. We investigated the impact of sharing resources among the clients of such a warehouse rather than dedicating a specific amount to each party.
Workforce and space
Costs are largely driven by labour and space. Generally, order picking is the most labour-intensive and costly activity for warehouses. Typically, orders destined for a specific lorry are buffered in a temporary storage space at the dock door until all the required orders for that vehicle have been picked. But this space is often restricted compared to the facility’s daily order picking volume.
We analysed the impact of sharing resources such as order pickers and dock doors. We considered the total tardiness of shipping lorry loading as the key performance measure of each company in both collaborative and non-collaborative scenarios. Our main objectives were to investigate whether cooperation improved the overall performance of involved warehouses and under what circumstances this practice is most beneficial. We assumed that lorries were not allowed to depart before their due time.
First, we compared collaborative and non-collaborative warehouses via a computational experiment. We generated 260 random instances and then studied the benefits of carrying out certain tasks cooperatively. To that end, we used a dataset provided by a retailer with multiple operations in Western Europe to obtain realistic values for our parameters. The data pertained to picking and shipping activities performed in four of the company’s facilities over one month.
We centred on three characteristics critical for warehouses as they could potentially result in bottlenecks: picker utilisation, dock utilisation and workload per lorry. We defined five levels for each aspect and then generated 20 random instances for each level. In a collaboration between businesses, they could achieve different outcomes. For instance, while one might see a decrease in tardiness, another could record higher delays. Therefore, we added constraints to the study to ensure that none of the involved parties experienced an increase in tardiness as a result of their cooperation.
The advantage of sharing pickers
We studied the value of collaboration and how it affects the lorries’ tardiness. In the “shared pickers” scenario, we assumed that pickers were the sole joint resource employed by the companies. In the case of “shared docks,” we supposed that the organisations only shared the docks. In all instances (as shown in the figure), cooperation led to a decrease of at least 32% in the total tardiness of shipping lorries, with an average improvement of 61%. Likewise, we observed that sharing only the pickers had a larger impact than using only the dock doors jointly. In 80% of the instances, sharing only the pickers resulted in the same improvement as full collaboration.
The results show that the maximum benefit of cooperation is obtained at medium-level picker utilisation (about 60–70%). Nevertheless, in levels employing smaller numbers of pickers, it could be more advantageous to share dock doors since this speeds up the shipping process. When the dock doors are used jointly without collaboration in picking, fewer spaces are required to complete the operation. All cases in the study recorded at least 20% savings in the number of dock doors, with an average decrease of 32%.
Ultimately, the findings indicate that 30% of the improvement made by full collaboration can be achieved by sharing solely the docks. However, using only the pickers jointly is more beneficial than exclusively sharing the docks. Furthermore, cooperation is much more beneficial when companies have complementary demand patterns and resource requirements.
Original publication:
Jamili, Negin, Van den Berg, Pieter L., De Koster, René. 2022. “Quantifying the impact of sharing resources in a collaborative warehouse”. European Journal of Operational Research, 302 (Elsevier).