LOGISTICS RESEARCH
Increasing employees’ throughput in a logistics facility is no easy task, as many variables can influence performance. But new research findings reveal there is one sure way to make workers more productive. The key lies in warehouse management systems, according to Professor of Economics Ludwik Wicki from the Warsaw University of Life Sciences.
Warehouse management systems (WMSs) are designed to improve all processes taking place inside a logistics facility. This advanced software allows businesses to control and manage warehouse operations from the time goods enter a warehouse until they move out.
“Introducing IT solutions in logistics leads to an increase in the reliability of communication, faster stock turnover and a higher level of service. It also enables higher work efficiency and overall productivity,” writes Professor Wicki in the journal Economics and Organization of Logistics.
His research findings reveal how implementing a WMS solution in a warehouse leads to a steady increase in employee productivity.
The researchers measured labour productivity in three different warehouses dedicated to the handling of fast-moving products for 12 months: three months before implementing the software and nine months after its deployment. The results show significant differences in workers’ throughput.
Warehouse transformation towards productivity
When the logistics software was introduced to help employees organise all the processes in the warehouse, work productivity rose. “Workers’ productivity after implementing the warehouse management system increased by 40% compared to the previous level,” says Wicki.
Labour productivity in the analysed period increased in each month of the analysis. One of the three warehouses showed stabilisation of workforce productivity at a level 50% higher than before the implementation. The research findings confirm that the presence of a WMS solution in the warehouse makes it possible to reach a significant increase in work productivity.
But the results are not immediate. According to the findings, it took at least six months after the software was implemented to see a 40% rise in workers’ productivity. The study shows that employees need a six-month period of productive learning. After this time, the level of productivity is then stabilised. To ease the learning curve, Professor Wicki says companies implementing WMS solutions in warehouses may benefit from providing workers with training support in the early stages in order to adapt faster to the new software.
As in any software implementation process, getting acclimated to a new WMS requires a transition period. “Enterprises must be prepared for a period of organisational learning of the new management system. Only after several months the assumed performance is achieved, the presumed benefits can be accomplished and the users of the system become independent,” says Wicki.
Reoganising logistics for performance
In each of the warehouses studied, the increase in work performance was a result of implementing the WMS, but also of making changes in the space layout and organisation.
“The increase in labour productivity results from several changes introduced together along with the implementation of the warehouse management software,” says Wicki. “Workers’ productivity also increased due to additional changes in spatial distribution, warehouse equipment and reorganisation of internal processes.”
Prior to implementing the new software, the facility was reorganised and the space layout optimised for performance. One of the most important changes applied was dividing the warehouse into two zones — storage and order preparation — instead of dividing it into areas by product group, which was how it was organised in the past.
In each of the warehouses studied, the increase in work performance was a result of implementing the WMS
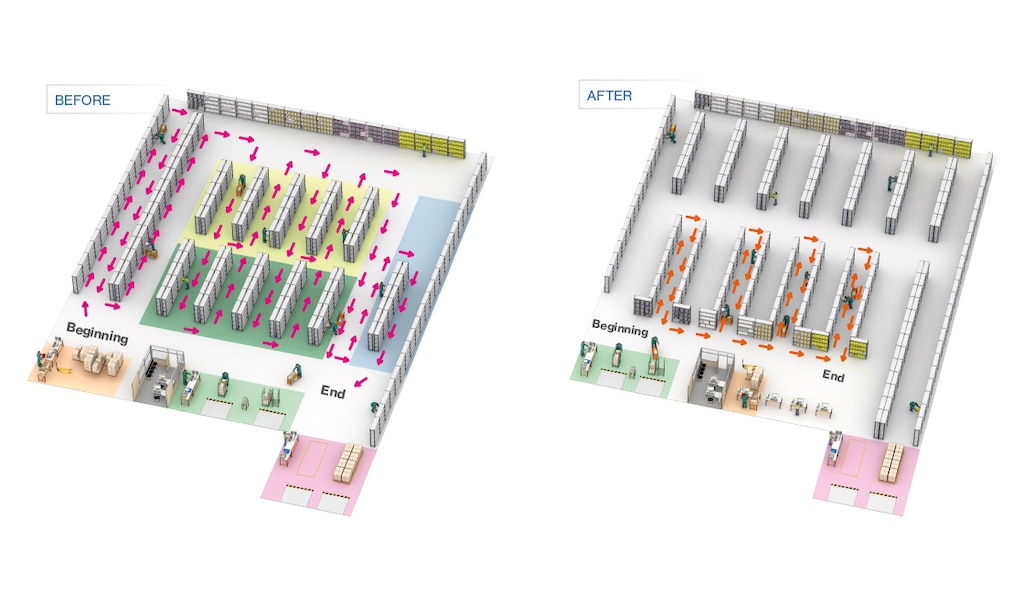
Other changes involved reorganising the pick path for efficiency and optimising the location of goods in the warehouse based on the number of picks and frequency of occurrence of goods in orders.
After the WMS go live, the processes to prepare and dispatch orders were also amended. The orders were processed digitally through the WMS. Based on the analysis of product availability and location, the software automatically generates transfer orders and a complete list taking into account the shelf life of products for sale and location of goods units. The order of products on the picking list results from optimising the path to be followed by a picker.
Before installing the WMS, the picker had to locate products independently, which required perfect knowledge of their distribution within the warehouse. As a result of deploying the WMS solution, the pick path was significantly shortened.
“Before the implementation, the distance covered by the employee during the preparation of a single order was about 410 meters. After the changes, the length of the pick path was shortened by an average of 59%, to 170 meters per order,” says Wicki. To fulfil 100 orders, employees had to travel 41 km before the reorganisation of the warehouse, a distance that was reduced to 17 km after the changes. Thanks to the WMS solution, the time needed for picking was substantially shortened and productivity increased.
Leveraging the opportunity
Introducing IT solutions to support complex logistic processes has become a necessity. Warehouse management systems are a growing trend: the market is expected to reach $6.1 billion by 2026, according to Markets and Markets.
Businesses that want to increase their work productivity may benefit from adding technology to their warehouses and distribution centres. However, they should always keep in mind that to increase workers’ performance substantially, implementation of a warehouse management system must go hand in hand with the reorganisation of logistics processes.