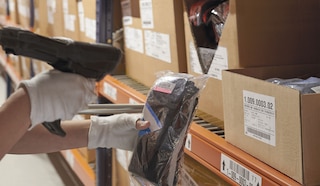
GS1-128 barcodes in logistics
The GS1-128 barcode (formerly known as EAN-128) constitutes the standard barcode in logistics for storage and the exchange of product information at the international level. In fact, this method has become one of the most effective for organizing goods inflows and outflows in warehouses, one of the biggest headaches for logistics managers.
In this post, we analyze the GS1-128, the data that make it up, and its real-life applications in storage installations today. Let’s get down to business.
What’s a GS1-128 barcode?
The GS1-128 label is an international code used in manufacturing, product storage, and order preparation. Employed extensively in the logistics field, this code contains numeric and alphanumeric characters that represent a product’s characteristics, for example, its batch number, manufacturing date, and expiration date.
Known as EAN-128 until 2005, when it was renamed as GS1-128, this standard has a set of application identifiers (AIs) — the relationship between the digits and their meaning in the real world — that guarantee the traceability of the product throughout its journey along the supply chain.
Thus, GS1-128 barcodes need to include humanly readable encoded information to facilitate both the automatic operations of the machines (pallet checkpoints and barcode scanners) and the work of the people charged with preparing and receiving the goods.
In reality, the aim of this encoding is to optimize the automatic entry of data into the computer systems. All the same, to double-check the information in case of doubt, the label also contains data that can be read without an electronic device.
GS1-128 barcodes can include the following data:
- Package number and product quantities
- Product weight and capacity
- Product manufacturing and/or expiration date
- Final destination of the product
- Customer order number
- Batch number
- Customer account code
What data does a GS1-128 label contain?
A GS1-128 label reflects the various elements that define the logistics operation: humanly readable data, such as the best-by date or recipient; the SSCC (Serial Shipping Container Code), which makes it possible to send the order; and the barcode, which streamlines the recording of product information in the system.
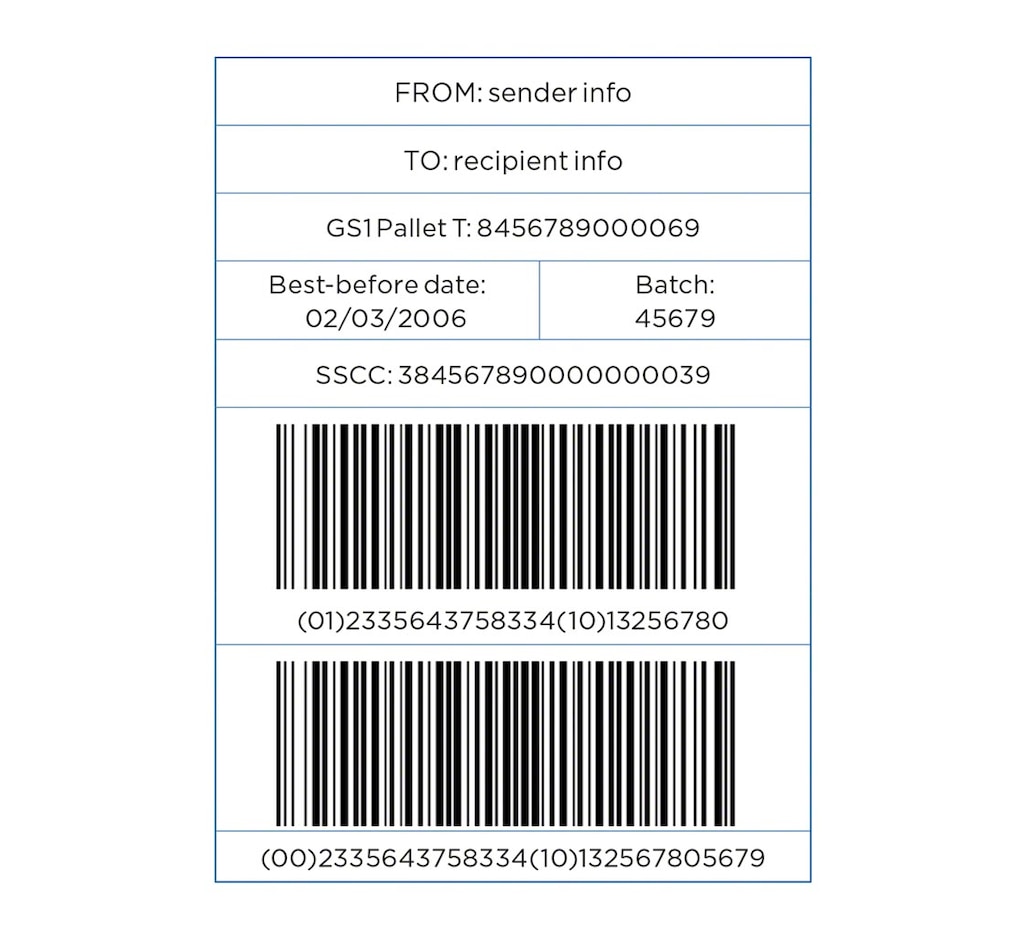
Humanly readable information
General information on each sector, specifying data such as product batch number, shipping date, and name of issuing company, among other data.
SSCC code
The SSCC (Serial Shipping Container Code) makes it possible to identify a load in a shipment or dispatch. This code is especially useful for ensuring efficient deliveries.
The SSCC has a total of 18 digits arranged as follows:
- The extension digit, a value between 0 and 9 (the first digit) assigned by the business.
- The GS1 company prefix (7 to 10 digits).
- The serial reference number, based on the length of the GS1 company prefix (between 6 and 9 digits).
- The check digit, derived from a mathematical calculation representing the code in its entirety.
Barcode
This is an encoded number that identifies a product and includes the following components:
- Application identifiers (AIs)
- FNC1 separators
AIs are numeric codes of two or more digits reflecting a data category, such as batch number (10) or packaging date (13), among many others. The main attribute of these codes is their concatenability, that is, the ability to link together multiple combinations of AIs to form a single barcode.
Meanwhile, FNC1 separators are variable elements inserted between the various AIs to differentiate them from each other.
This table shows the most common AIs:
AI | Content | Structure |
---|---|---|
00 | Serial Shipping Container Code (SSCC) | n2 + n18 |
01 | Global Trade Item Number (GTIN) | n2 + n14 |
10 | Batch number | n2 + an...20 |
11 | Production date | n2 + n6 |
13 | Packaging date | n2 + n6 |
15 | Best before date | n2 + n6 |
17 | Expiration date | n2 + n6 |
37 | Count of trade items or trade item pieces contained in a logistic unit | n2 + n...8 |
320X | Net weight, pounds | n4 + n6 |
Legend:
- nX: a mandatory, fixed-length numeric datum of X characters.
- n...X: a numeric datum of variable length with a maximum of X numeric characters.
- an...X: an alphanumeric datum of variable length with a maximum of X characters.
Example: (02)67884344353521(37)23123902(10)34533
Placement of GS1-128 barcodes
Placement of GS1-128 barcodes on pallets
On pallets less than 16" tall, labels should be affixed as high as possible without making it difficult to read the barcode and always ensuring that they are placed at least 2" from the vertical edge.
For pallets over 16" tall, labels are to be attached 16-32" from the base, leaving at least 2" of space from the vertical edge.
In both cases, labels should be affixed to both sides of the pallet to facilitate barcode reading.
Placement on boxes or pallets
In the case of goods in boxes, the standard is for at least one side of the parcel to contain a label. Nevertheless, it’s advisable to print a different GS1-128 for every side of the box. The end of the code should be placed at least 1.25" from the base and 0.75" from the vertical edge.
From pallet checkpoints to picking: the use of GS1-128 labels in logistics
In logistics, the role of barcodes is to consolidate information about a product onto a single label. This guarantees the automation of such complex processes as quality control and order fulfillment.
In this vein, the main function of the GS1-128 standard in logistics is to register product unit loads and enter the key data in the system: from the expiration date to any other essential logistics information, such as dispatch routes.
This solution ensures the traceability and monitoring of the product throughout all the links of the supply chain as well as optimal goods flows in the installation.
So, we’ve seen that GS1-128 labels are vital for the management of product entries in and exits from the warehouse. But where exactly are they used for the most part?
- Pallet checkpoints: during the monitoring of warehouse inflows and outflows, automated storage systems usually have conveyor lines equipped with pallet checkpoints. There, product data is entered into the system by means of a barcode reader, while the measurements and proper condition of both the pallet and the goods are verified.
- Picking: multiple systems such as pick-to-light incorporate barcodes in their operations. This speeds up order prep and minimizes errors normally occurring during this process.
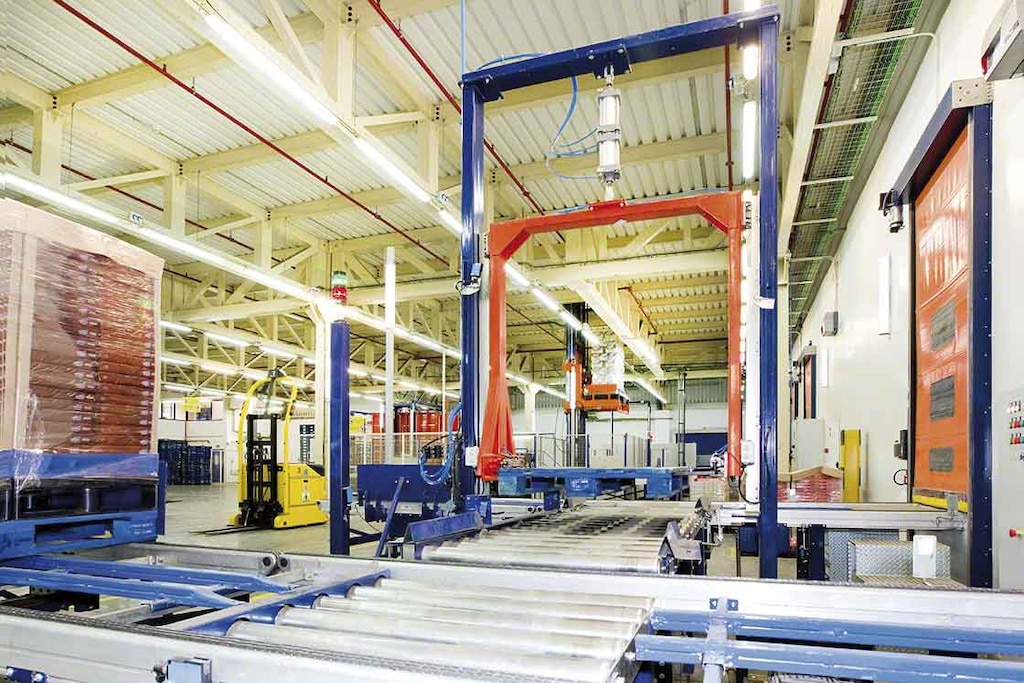
The future: IoT and WMSs
Warehouse management systems (WMSs) feature the ability to scan and record GS1-128 code information in order to streamline operations taking place in an installation. Indeed, WMSs are capable of reading, designing, and printing labels with the corresponding barcodes from the data entered into the system.
Yet companies are gradually integrating other technologies to combine with — or even replace — barcodes. This is the case, for example, of RFID technology. Just the same, GS1-128 labels have multiple advantages that make them indispensable for certain operations nowadays. In goods receipts, for instance, only a barcode scanner can guarantee the correct reading of the label.
Ultimately, although these labels will continue to constitute an effective solution in logistics, particularly in put/pick-to-light processes, other more innovative technologies such as 5G and the IIoT (Industrial Internet of Things) are hot on their heels. These new technologies represent a very promising future in which all logistics elements will be interconnected, resulting in increased efficiency and productivity in logistics installations.