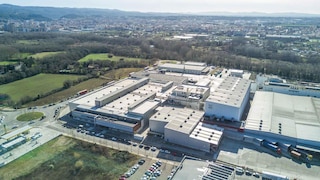
What is a lead time in logistics? And how to optimise it…
A lead time refers to the time it takes from when a purchase order is created for a supplier… until the goods are delivered from that supplier to the customer (this can be an individual or a shop). Coping with this concept is pivotal to organising all the different processes throughout your supply chain.
What does each lead time measure along the supply chain?
Depending on the part of the supply chain you look at and your point of view, the words ‘lead time’ can take on slightly different meanings. This concept can be divided into sections to understand how it affects each area.
- Sales or commercial management: knowing the precise lead time will allow you to commit to one delivery date or another with your customers.
- Purchasing or procurement: managing the lead time of raw material suppliers is the key to prevent production line shortages.
- Manufacturing lead time: this lead time simplifies manufacturing time calculations, which in turn influences logistics and sales management.
- Logistics and distribution: a logistics lead time takes on a holistic dimension since you need to know other area’s supply times to know how long it will take to produce them; when they will arrive at the warehouse; and how long it will take to process and deliver them to the customer.
How is the lead time calculated?
Normally, the time of delivery is calculated using:
Lead time = Delivery date - order date
The answer shows the days from when the order was placed until it reached the customer. It is measured in calendar days to keep it simple. This calculation must be made based on each piece of the supply chain we had already mentioned and for each particular product.
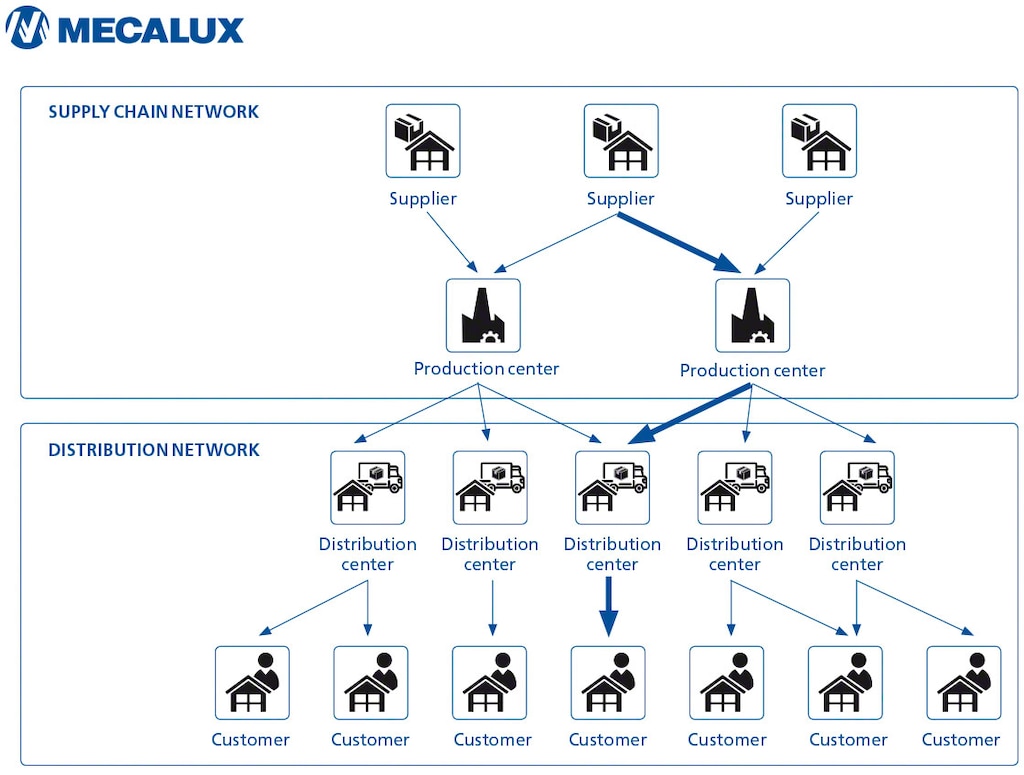
Take a look at this diagram. If you are a customer at the end of a long supply chain, your lead time will be the accumulated lead time of the other players: the raw material suppliers, the production plant and the distribution centre that will send the item to you.
For this reason, although it may seem that the lead time calculation is straightforward, it is essential to understand how it all hashes out to correctly plan operations. Plus, other additional variables must be borne in mind, such as a supplier who only accepts orders on a specific day of the week. For example, only on Tuesdays and Thursdays, meaning an order placed on Monday will be delayed one day; but Friday's order will be delayed four days.
Delivery times are measured more accurately based on the company’s order history and deliveries. This is a more reliable starting point than promises from suppliers, since in reality changes do happen.
The importance of having short logistics lead times
The main logistics goals are to deliver the right products to the right place, at the right time, in the right quantities and under the right conditions. Within the logistics equation, lead time shows the time dimension, which is closely related to the service level, but has a huge influence over stock control and demand planning.
The advantages of short delivery times are evident in…
- More precise demand planning: short term demand forecasting makes it possible to be more accurate. One of demand management’s main rules of thumb is that the further into the future you organise, the more uncertainty there will be. Shorter delivery times can reduce this concern, as it allows more reliable, more accurate forecasts to be made.
- The opportunity to carry less stock: a short lead time means you operate with a smaller inventory volume to meet customer demand. The primary reason why warehouse stock management takes place is to bridge the time difference between when a customer places an order and how long it takes the supplier to get the order to the customer. Supply times have a linear effect on inventory policy: the higher the lead time, the more stored stock and vice versa.
- Overall better customer care: having a short lead time allows you to speed up delivery times and meet customer deadlines. In today’s business dominated by 4.0 logistics and omnichannel logistics, eliminating between-steps and simplifying processes have proven to be a crucial added value for any company.
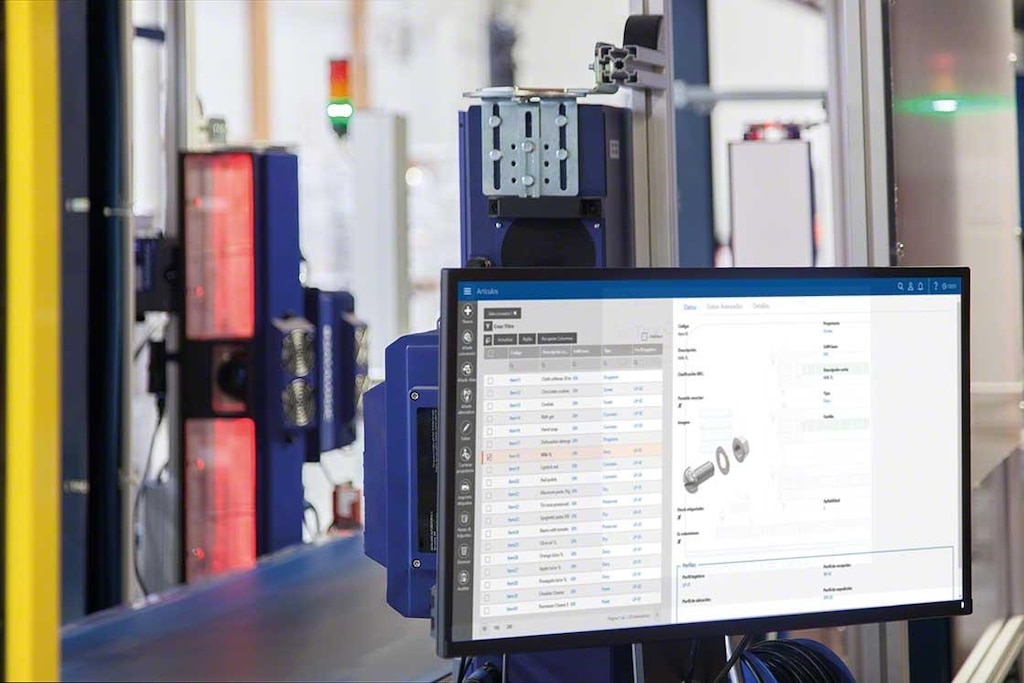
How to optimise a supply chain’s lead time
1. Accurately measure all supply times through ranges
The perfect departure point for reducing delivery times is to isolate and identify critical lead times (e.g. manufacturing, transport, warehouse processing, etc.). Afterwards, each supply time must be broken down into smaller parts to understand and optimise them.
This is the same foundation on which warehouse KPI metrics is built. Specialised software is often used to facilitate this task, seamlessly integrating data across the entire supply chain.
2. Analyse intralogistics processes and sub-processes in detail
It is important to analyse intralogistics related operations to detect bottlenecks and malfunctions that delay the flow of materials. If you move to analysing the warehouse, global operational management is the result of multiple sub-processes that work in a chain. And, the smallest detail can send ripples through these flows.
For example: just imagine a case where goods movements follow the FIFO criterion (first in, first out) and a roller conveyor is used to do so. At some way point, the conveyor is unable to keep up with the flow and boxes accumulate on the floor next to the overcrowded conveyor. They keep on piling up on top of each other.
When the congestion on the other side of the circuit is cleared and the conveyor reloads, it is likely that operators will first pick the top boxes, changing the criteria to LIFO (last in, first out) and prioritising in the wrong order. And here is where a type of inefficiency sinkhole forms, dragging out operating times. Consequently, meticulous analysis of warehouse flows is essential to pinpoint and remedy the root of problem(s).
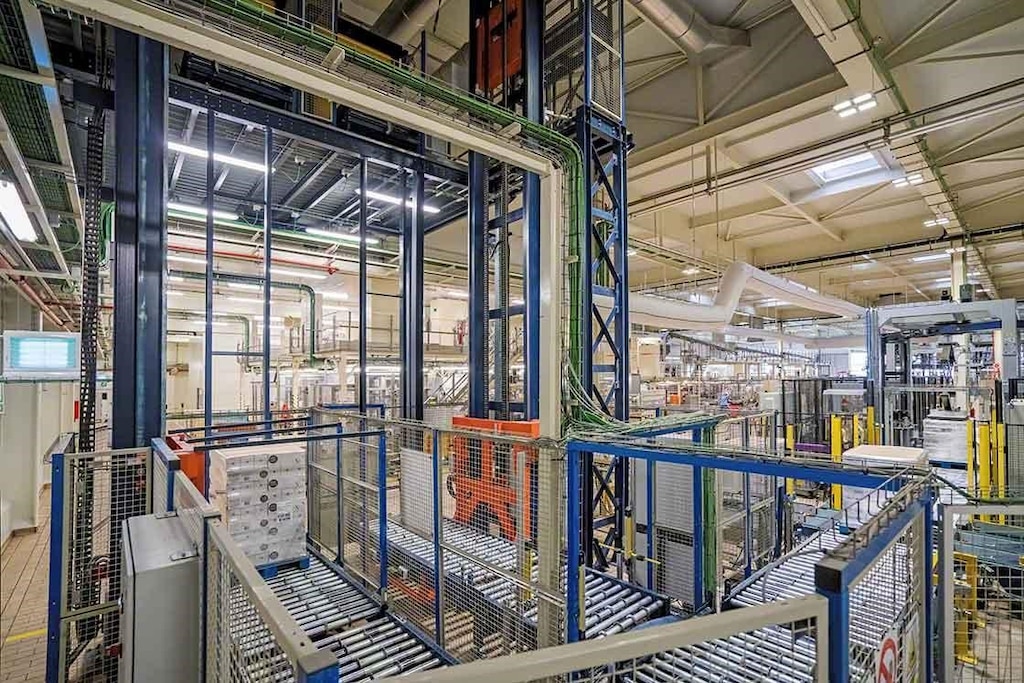
3. Manage contingencies with the help of specialised software
A variety of reasons can lead to fluctuations in supply times. Many of them are random and unexpected. In this regard, specialised logistics software helps cut back this uncertainty and improve the lead time:
- Improving your ability to react to unexpected events. This takes on greater meaning in a warehouse environment. How do I deal with a blind reception (unexpected stock arrivals)? What logistics parameters should be followed to organise order picking? These issues, and many more, can be fixed quickly thanks to a warehouse management system such as Easy WMS.
- Integrating and unifying all the information in your supply chain: software with cutting-edge algorithms facilitates decision-making and detects of hot spots throughout the supply chain. This is the case for the Supply Chain Analytics Software, a special module for analysing Easy WMS data.
4. Reach collaborative agreements with suppliers
When selecting suppliers, the tendency is lean towards long-term relationships as a priority. This is because you can standardise processes and fine-tune supply time schedules. They can be shortened to operate with cross-docking or follow the just-in-time method.
Software such as the Multi Carrier Shipping module of the Mecalux Easy WMS simplifies a warehouse’s integration with the main transport agencies, an essential point for e-commerce logistics, among other sectors.
The warehouse, as an invaluable nexus between supply and demand, plays a fundamental role in the entire supply chain's backbone. So, good warehouse management is pivotal in reducing lead times. If you are looking for a warehouse management system that improves your efficiency, do not hesitate to get in touch. We will demo our systems and provide you with all the information you need.