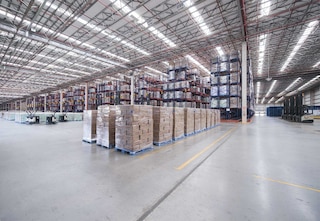
Logistics staging area in a warehouse
In logistics, a warehouse staging area is a rack-free zone usually located in front of the loading docks where goods are placed temporarily on the floor, waiting to be transported to another location.
One common question is: what percentage of warehouse space do you need for the staging area? The answer, however, isn’t a one-size-fits-all solution. On the contrary, this amount needs to be determined according to the type of goods or capacity of each particular installation, among other factors. Below, we’ll show you exactly how to calculate this proportion.
Functions of a warehouse staging area
Depending on the needs of each company, the warehouse staging area can serve as a zone for goods receipt, dispatch, or any other function, such as cross-docking.
Receiving zone
As in the goods receipt zone, the necessary product quality controls are performed in the staging area. Operators check the condition of the pallets and the merchandise and make sure the products match the information on the order documentation.
Automated warehouses offer more efficient alternatives in this regard, especially in installations with a high number of cycles. Thus, setting up a pallet checkpoint to verify the condition of the pallets and the goods and enter the data on each package into the warehouse management system (WMS) automatically is a good way to make the jump from more traditional systems.
Dispatch zone
Companies usually use staging areas as dispatch zones with the aim of sorting goods by order or transportation route and then loading them onto the truck with the help of handling equipment.
The incorporation of technology, such as live roller conveyors for sorting goods to be dispatched, adds extra efficiency to manual work. Additionally, automated loading docks can be installed to load the trucks in a way that’s autonomous, agile, and error-free.
From picking to cross docking: other uses
Beyond the goods receipt and dispatch processes, the staging area can be leveraged for other logistics activities. This is the case of Vente Privée, a European leader in online sales of brand-name products, which uses the staging area in its installation in Rhône-Alpes, France, as a picking zone for preparing orders to be subsequently consolidated.
Likewise, these rack-free spaces are especially useful in warehouses that carry out cross-docking. This process constitutes the management of full pallets that don’t need to be stored on the racks, as they’ll soon be dispatched. An example of this is the new logistics centre of 3PL Luis Simões in Guadalajara, Spain.
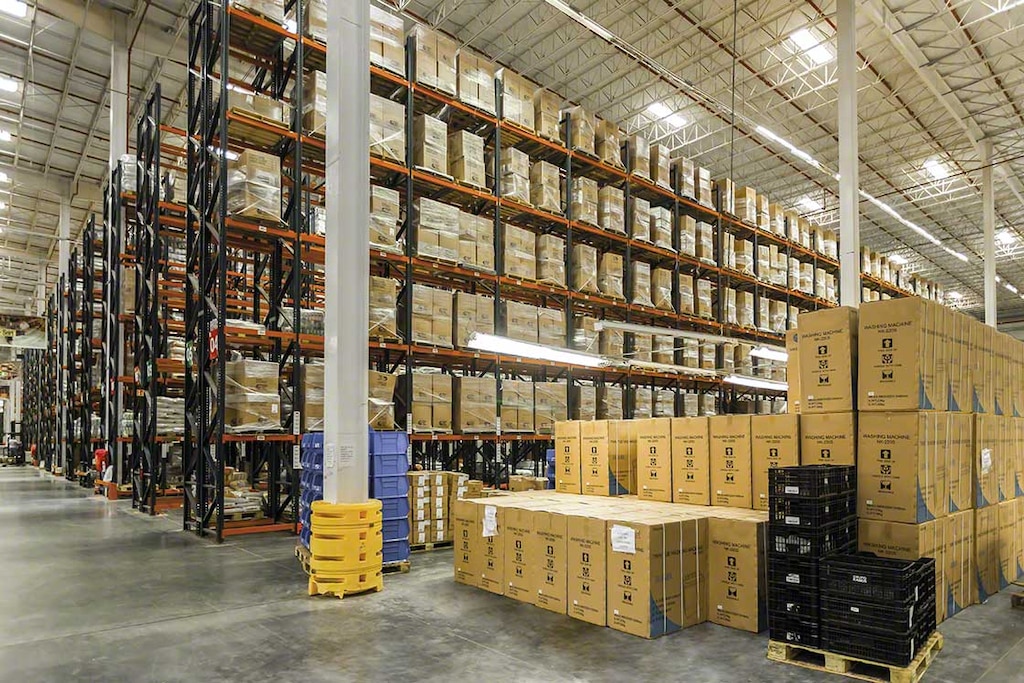
How big should the warehouse staging area be?
The space that each installation requires for its staging area should be carefully analysed when designing the facility layout, in line with the following aspects:
Logistics strategy implemented
Depending on the storage methods applied in each warehouse, the amount of surface area needed for the staging area can increase or decrease.
For example, if the company performs cross-docking, the space without racks should be larger compared to installations that, as a rule, store all the goods they receive.
Product characteristics
Each business establishes particular workflows and deals with a very specific type of merchandise. In fact, to define the size of the staging area in each warehouse, it’s essential to consider the particular characteristics of each product: length, weight, material, etc.
Moreover, the layout of the facility should take into account the handling equipment to be used in it. This will optimise workflows and reduce errors and accidents that could damage the goods, the facility, or even the operators.
Warehouse type
Operations normally associated with an installation include goods receipt and storage and order preparation, consolidation, and dispatch. It’s advisable to analyse the particulars of each individual facility, as they don’t all encompass every logistics stage; this, too, will affect the size of the space dedicated to each function.
The characteristics of the product are as relevant as the classification of warehouses according to the flow of materials: in these cases, a raw materials warehouse (manufacturing) will not require the same free space as a distribution centre, for example.
Capacity and movement flow
Lastly, the space set up for goods receipt and dispatch is directly proportional to the flow of movements in the warehouse. Generally, the greater the number of pallets received and/or dispatched every day, the larger the staging area.
In the end, these four criteria only serve to confirm that the space dedicated to storage should be a customised solution adapted to the particular needs of each company and, of course, each warehouse.
Warehouse staging areas: real-world examples
At Mecalux, our team of professionals will personalise the design of your warehouse as per the real needs of your company. Below are several projects we’ve worked on in which the warehouse staging area played a key part in the layout of the facility.
Grupo Ramos (cross-docking)
Grupo Ramos, one of the largest retail, food, and fashion companies in the Dominican Republic, needed an installation that would meet the many challenges facing the sector with the arrival of Logistics 4.0.
We designed the group a complex 9.5-acre warehouse with a capacity for more than 40,000 pallets. In order to manage inflows and outflows (consolidation, dispatch, and cross-docking), the installation boasts a rack-free space measuring over 7,500 ft² (2% of the facility) to effectively administer the 56 loading docks.
Agata (separate staging areas)
Agata was looking for a personalised solution due to the high number of cycles taking place every day at its logistics centre. The company, one of Poland’s main furniture distributors, chose us to design it an installation that would maximise storage capacity while improving stock management.
Given the high volume of inbound and outbound goods, Agata and our firm decided to set up two differentiated staging areas, on each side of the warehouse, to receive and dispatch goods on opposite sides of the facility, respectively. This solution is often employed in distribution centres to prevent interference between the two operations.
Unilever (32,292 ft² staging area)
Unilever, a multinational manufacturer of consumer goods, wanted to build a large warehouse in Montevideo, Uruguay, for one of its most important distribution centres in the Latin American market.
To service the 27 loading docks, we built a 32,292 ft² warehouse staging area (17% of the installation) designed to receive and dispatch goods. This way, pallets are sorted by route on the floor before being loaded onto the truck, doing away with wait times and optimising company resources.