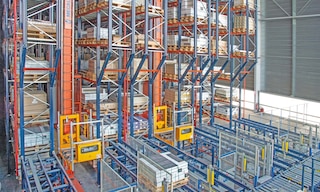
Materials storage: strategies for logistics efficiency
Materials storage is a fundamental process that enables companies to stock the goods they need to supply their production lines. Correct organisation of raw materials results in not only more effective logistics operations but also faster production processes.
Why is materials storage important?
The supply chain of any product manufacturer encompasses a multitude of processes: from raw material storage to production line supply. Like a domino effect, maximising efficiency in each operation will positively impact the other activities performed in the logistics facility.
Warehousing is a core process for any manufacturer. Streamlined materials storage is essential for production planning and, in turn, meeting planned deadlines. These are some of its advantages:
- Availability of resources required for manufacturing.
- Storage space optimisation.
- Reduction in logistics costs.
- Rapid, effective responsiveness to demand.
So, how do you get the most throughput out of materials storage? By organising goods according to their characteristics and demand level, among other factors. For instance, higher-consumption raw materials can be stored near the production lines to enable their delivery as required and without delay.
To optimise the storage of material and, ultimately, improve stock management, you need two solutions. The first is a storage system that facilitates operator tasks and maintains goods in perfect condition. The second is a warehouse management system (WMS) that arranges products strategically in your facility and controls their status in real time.
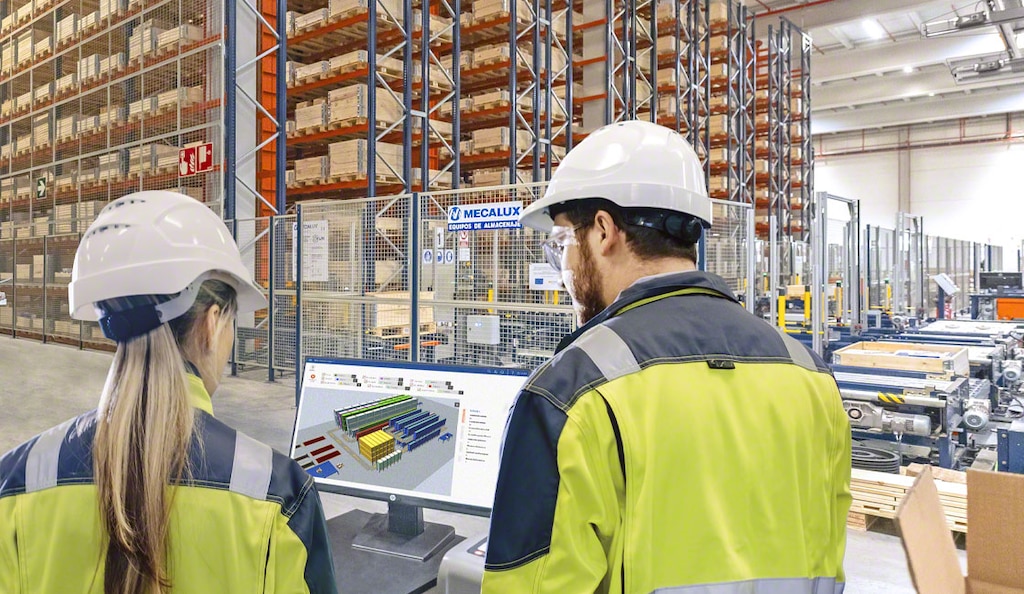
What is the correct storage of materials?
Correct materials storage involves choosing the storage system that best addresses your logistics needs. Although racking are the most common solution, other methods can be used. One example is cross-docking, whereby products are distributed quickly without having to be stored. Another is block stacking, where unit loads are stacked on the warehouse floor.
Combining different storage solutions in a single facility allows you to organise goods and operations. That is, you can assign each product to the most appropriate system.
Materials storage systems can be classified into 2 main categories:
- Manual systems. Operators handle goods manually with the help of forklifts.
- Automated systems. Handling equipment physically manages unit loads and places them in the ideal locations.
Multiple factors will influence your choice of the best system for your warehouse. The right solution is the one that adapts to your company and takes into account the particular characteristics of its logistics processes. When selecting your system, consider these 3 crucial factors:
- Product to be stored: stock type, unit load (characteristics, measurements and weight), SKU quantity and turnover rates.
- Area allocated to storage: available space and flooring characteristics.
- Handling equipment used: from forklifts to automated systems.
Racking employed in the storing of materials can be grouped into these two categories:
- Pallet racking with direct access. Goods are accessible from the working aisle, facilitating put away and picking. This category includes selective pallet racking, mobile racking systems and cantilever racking. For businesses that prioritise speed in delivering materials to the production lines, these kinds of solutions allow operators to remove items more quickly.
- High-density storage systems. These solutions make the best use of the storage area, offering greater storage capacity. This category encompasses drive-in pallet racking, push-back racking systems, pallet flow racking and the Pallet Shuttle. Companies that install high-density solutions typically manage a large quantity of goods that need to be sent to the production lines at the right time.
Businesses primarily focused on enhancing productivity and streamlining materials storage will gain significantly from logistics automation. Automated systems — e.g., stacker cranes, conveyors and transfer cars — manage products more effectively.
Solutions like the automated Pallet Shuttle, for example, considerably expedite the movement of goods. This system consists of stacker cranes or transfer cars and a motor-driven shuttle that stores and retrieves pallets from their positions. Subsequently, conveyors move the materials to the production lines autonomously.
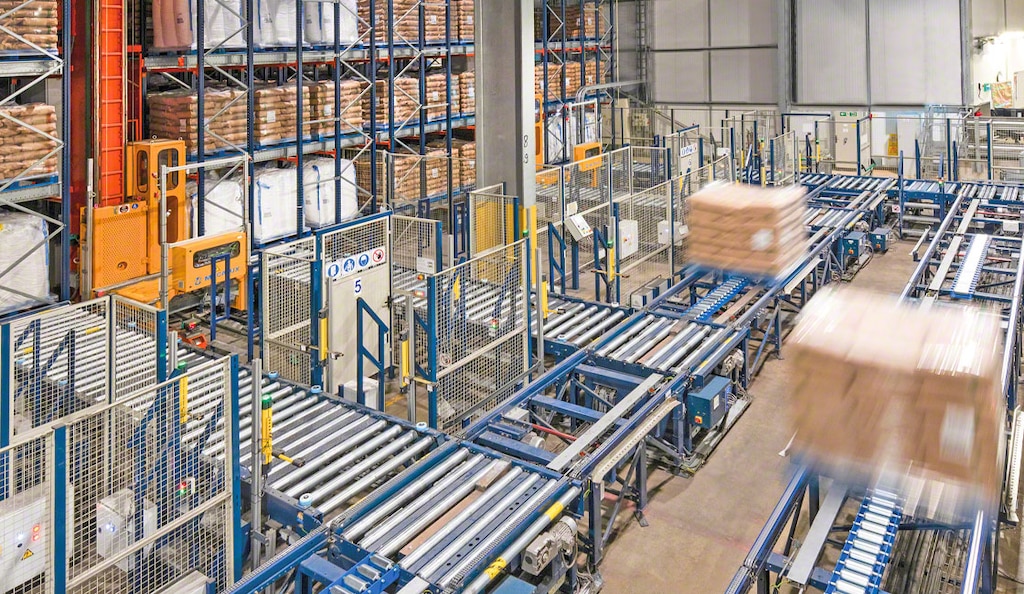
How do you classify the types of materials stored?
Categorising your materials logically will facilitate warehouse operations. Once your goods are correctly identified and organised, operators can locate the items they need more easily to send them to production as soon as possible.
Facilities that house a wide array of products — from raw materials to finished goods — can benefit from implementing warehouse management software such as Easy WMS. With this solution, you can control stock rigorously by assigning an optimal storage slot to each item, thus knowing its location in real time.
Classifying the different types of materials in your facility is a must for guaranteeing their correct storage and error-free delivery to the manufacturing area. WMS software assigns each item the most convenient position by analysing details such as its demand level and characteristics (size, perishable, corrosive, fragile, etc.).
One widespread practice in warehousing is to classify and organise materials in line with their consumption criteria. For instance, A items (those with the highest demand) are stored near the receiving area or production lines, followed by the B items. Finally, C items (low consumption) are placed in more distant and less accessible areas.
WMS software is becoming a critical tool in all types of logistics facilities. The program considers all possible scenarios when classifying materials to distribute goods efficiently. At the same time, it guides operators in their storage tasks and in locating items to pick for production.
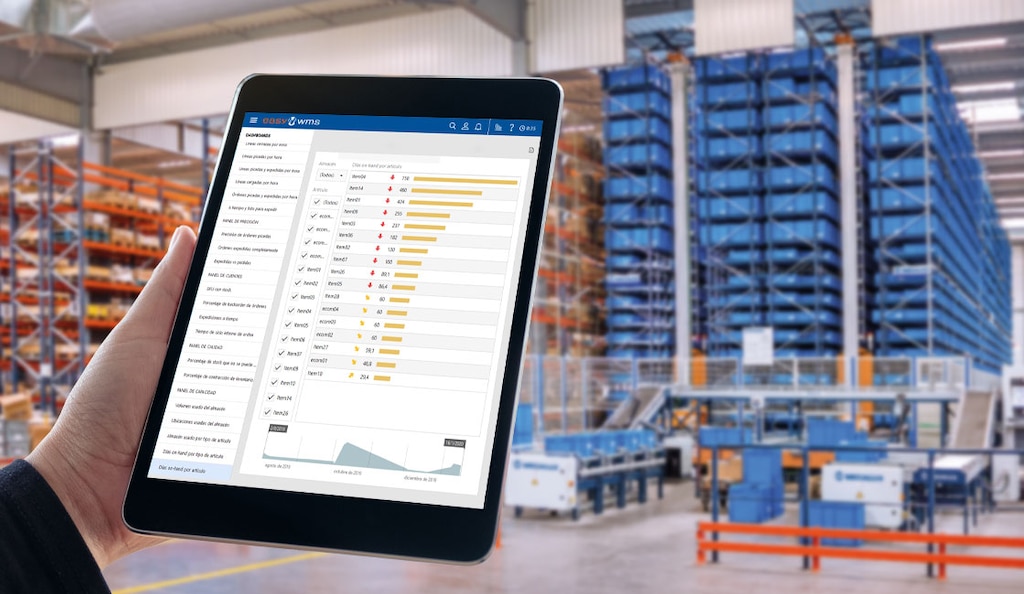
Correct materials storage for effective logistics processes
Streamlining the storage of material used to supply production lines is standard practice in numerous companies across all sectors. Raw materials are stored before being moved to the production lines when required. These types of items should be logically organised and classified to avoid stock loss, mistakes and delivery delays.
Materials storage isn’t just another task in logistics facilities; it’s an activity that drives business performance. Competent management of materials translates into best practices for the supply chain. With the ideal storage system and software that organises warehouse operations, your logistics processes will be more successful. At Mecalux, we’re backed by more than 55 years of experience in developing logistics solutions that support companies in their growth. Get in touch and we’ll show you how to modernise your supply chain and optimise materials storage.