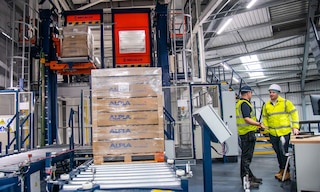
Warehouse organisational chart: purpose and elements
One of the most critical aspects of warehouse management has to do with the capabilities and organisation of the personnel responsible for receiving, storing and shipping goods every day. How is all of this arranged?
What is a warehouse organisational chart?
A warehouse organisational chart is a graphical representation of the structure of this department. It typically includes the roles, responsibilities and names of the people who compose and lead it, illustrating their hierarchical relationships in a diagram. This tool provides a clear and organised way to visualise how functions and activities are distributed within the warehouse.
According to the Institute of Science and Innovation in Mechanical and Industrial Engineering (INEGI), warehouses and their management are becoming increasingly vital for the supply chain and business outcomes. As a result, the positions in this field have more responsibility and autonomy. Almost all companies have some kind of warehouse, regardless of their size, level of technology or complexity.
How has the warehouse organisational structure changed in recent years?
The rise in online sales has forced warehouses to evolve — often through automation — to handle quicker, more flexible deliveries without increasing costs.
Customer expectations in terms of service quality are ever-heightened, and order processing involves greater personalisation. In today’s changing environment, the warehouse, its organisational chart and its optimisation are crucial for the success of business operations.
How does the warehouse organisational chart impact management?
Traditionally, warehouse management has depended on departments that also encompass other tasks and employees, such as Procurement, Manufacturing and Logistics. Nevertheless, it might play a more prominent role in organisations whose main activities are related to storage, e.g., logistics providers. Alternatively, it might fall to a lower level in the hierarchy of other types of companies.
These are some ways in which the organisational chart affects warehouse management:
- Definition of responsibilities
- Coordination of activities
- Process optimisation
- Improved internal communication
What to consider when creating a warehouse org chart
There’s no single organisational chart model applicable to all companies. An appropriate structure enables your business to achieve its goals using its material and human resources, whether existing or to be incorporated. The basis of a good warehouse department organisational chart is to determine the functions to be performed, design the job positions, group them and establish relationships between them.
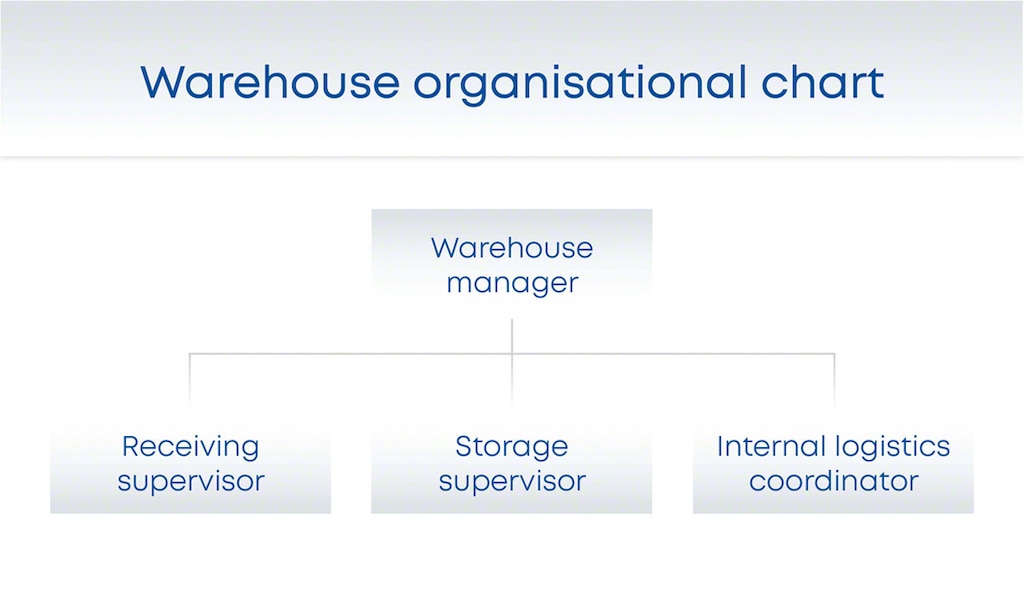
Managers and roles to include in an organisational chart
One option for putting together your warehouse organisational chart is to start with your logistics processes and assign a manager to each. This way, the warehouse manager would have the most decision-making authority. At the next level would be the people in charge of subprocesses, such as receiving, storage and internal transport.
- Receiving supervisor. This individual oversees procedures for inbound goods, from their arrival to their storage. The process includes assigning or scanning an identifier code or RFID tag, which is often incorporated by the manufacturer. This method — together with the use of a warehouse management system (WMS) — ensures full visibility of all products in the facility.
- Storage supervisor. This professional is responsible for assigning goods to the ideal locations, either manually or with management tools. Storage supervisors can assign predetermined slots or use random organisation.
- Logistics coordinator. This individual verifies compliance with goods transport rules, both internally and for outbound shipments. The logistics coordinator supervises correct material handling methods for each operation, monitors order fulfilment and manages production supply.
- Warehouse manager. This professional controls and coordinates all other warehouse operations. These include handling supplier interactions, overseeing staff reporting to them, managing the relationship with Procurement, identifying material needs, preparing reports and following up on everything pending delivery. Warehouse managers must stay informed about all supply chain links in their business and correct any inefficient processes.
These tasks, relevant to any logistics facility, can be distributed among a supervisor and three intermediate positions. However, you can also assign them to a single person, two workers or other configurations. Another option is to divide the work of the facility into zones, whether by operating temperature, final destination of the goods or other criteria.
The ultimate objective of the warehouse organisational chart is for information, products and raw materials to flow as smoothly as possible in this space within your company. Its structure will depend on the specific needs and characteristics of your business.
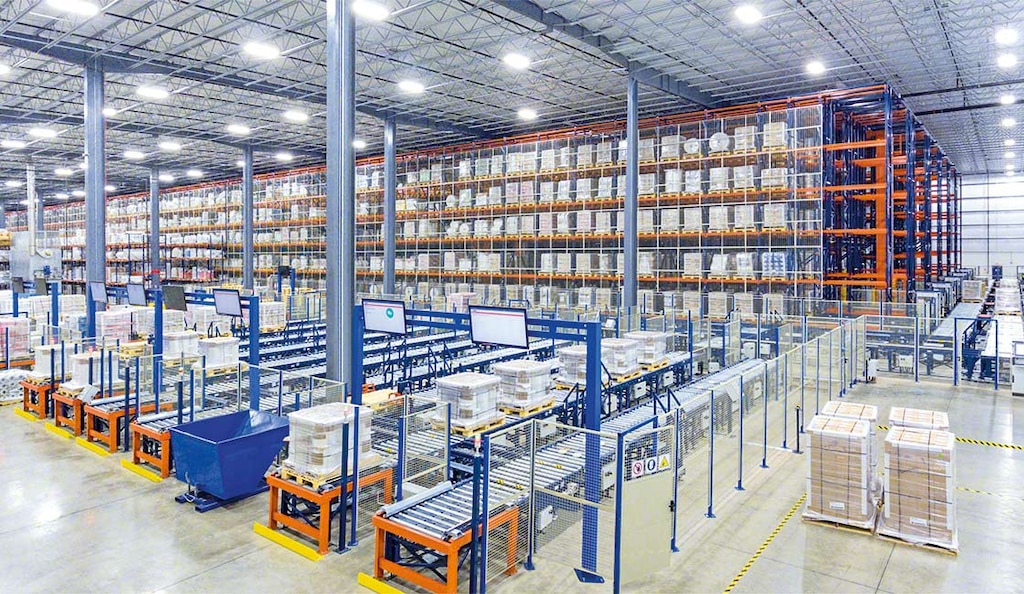
Another critical task is keeping the facility clean and orderly. In addition to enforcing occupational health and safety standards, the work environment will be more pleasant.
Adapt your warehouse to its organisational chart
Creating a warehouse staff organisation chart and distributing roles among employees and supervisors are essential for successful logistics operations. As mentioned above, there’s no cookie-cutter organisational model applicable to all businesses. Despite that, it’s advisable to use this tool to develop your own organisational chart. You’ll optimise processes, coordinate activities and improve internal communication in your facility.
Beyond creating your organisational chart, having a modern, automated warehouse adapted to workloads is also a must for supplying production lines, shipping orders and meeting customer expectations successfully.
Automating and digitalising your supply chain fosters successful business logistics. At Mecalux, we develop warehouse automation and management solutions that drive efficiency in all types of logistics centres. In fact, we’ve been manufacturing our own metal racking since 1966. Get in touch to find out how to take your warehouse team’s performance to the next level.