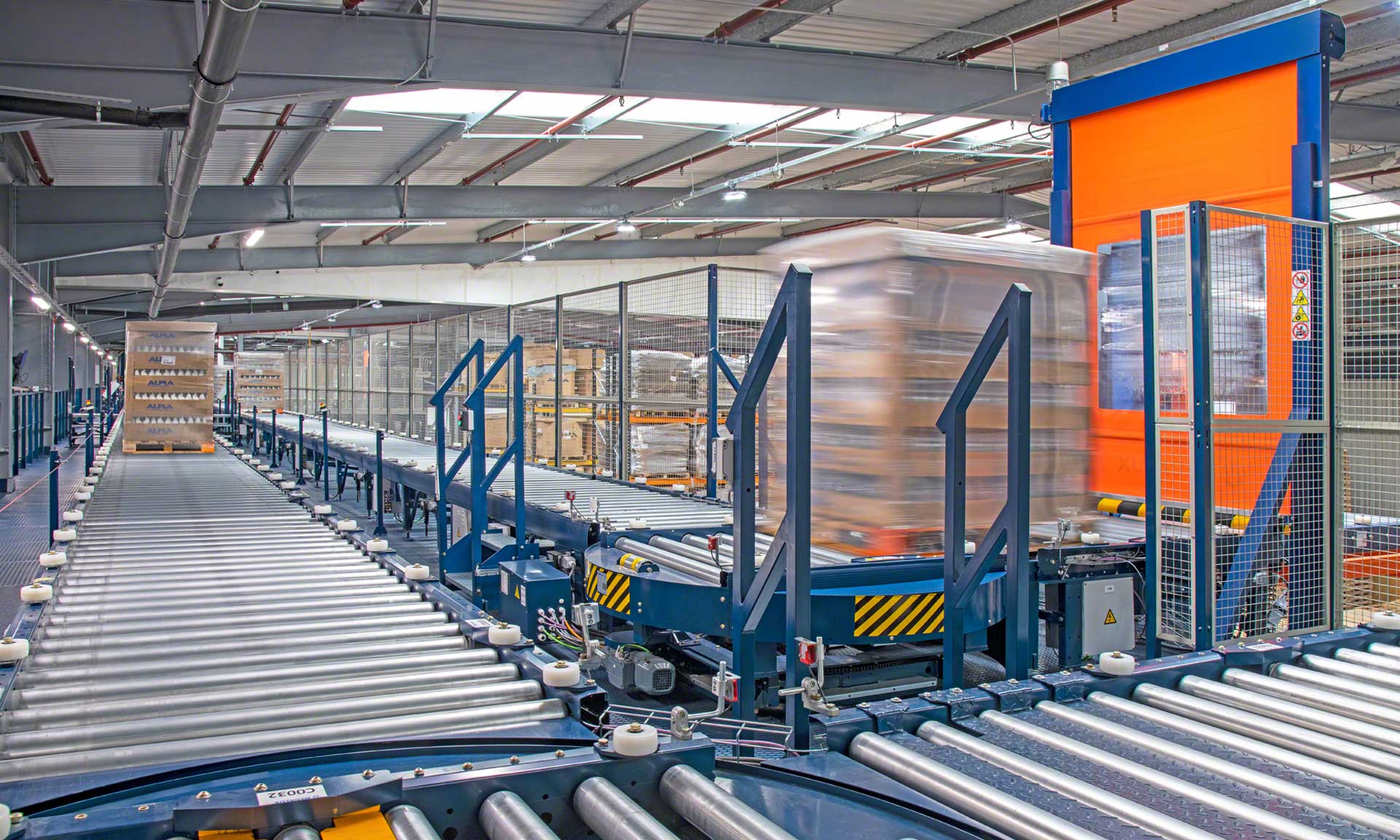
ALPLA installs an automatic conveyor system in its plant in Golborne (UK)
Plastic packaging systems specialist ALPLA moves 2,500 pallets a day thanks to an automatic conveyor system.
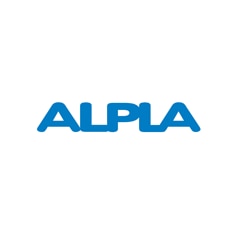
ALPLA has installed a conveyor system to connect its warehouse with its production lines in Golborne, UK. This global leader in the development and production of plastic packaging systems moves 2,500 pallets a day thanks to an automated conveyor solution.
ALPLA: innovative packaging solutions
Founded in Austria, ALPLA is one of the world’s leading companies in the packaging solutions sector. The company is recognised around the globe for producing high-quality plastic packaging solutions. Its plastic packaging is used in a wide range of industries, such as the food, pharmaceutical and cosmetics sectors. One of ALPLA’s main priorities is to carry out sustainable, environmentally friendly operations with the help of its own recycling plants.
- Founded in: 1955
- International presence: 45 countries
- Production centres: 177
- No. of employees: 22,100
- Turnover: €4 billion in 2021
CHALLENGES
|
SOLUTIONS
|
BENEFITS
|
---|
How can a warehouse be connected to a production plant when the two buildings are 70 m apart, separated by a road? ALPLA, a top manufacturer of packaging products, managed to overcome this challenge with a technology solution from Mecalux. “With the logistics solution installed, consisting of automatic pallet conveyors and lifts, we’ve cut our handling costs and carbon dioxide emissions drastically, making our business greener and more sustainable,” says Liam Grimwood, UK Plant Engineering Manager at ALPLA.
Present in 45 countries, ALPLA brought in a turnover of €4 billion in 2021, up 8.4% compared to the previous year. In the UK, the company is implementing an unprecedented growth plan. A few years ago, it built a modern production centre in the town of Golborne.
The logistics complex comprises two buildings — one for the production line, the other for the storage area — separated by a public thoroughfare. “Before, we depended to a large extent on the use of heavy vehicles to manually transport goods from the production centre to the warehouse,” says Grimwood.
As production volumes increased, so too did the manoeuvring and movement of lorries between ALPLA's production and storage buildings. There came a point when transporting the stock manually became untenable. “We needed a system that would connect both buildings and automatically move the goods from the production plant to the warehouse. We wanted to do away with manual handling and the use of heavy vehicles.”
The answer to ALPLA’s needs was the construction of an 8-metre-tall raised tunnel that crosses the public road to connect the production centre and the storage facility. “We chose Mecalux because of its previous experience in carrying out projects such as ours. The experience and know-how of the technical team and the project manager — who was by our side and advised us the entire time — were also key factors for our choice.”
Connection via automated systems
“Every day, we move around 2,500 pallets, thanks to an automated conveying system that works 24 hours, seven days a week,” says Grimwood.
The system installed by Mecalux is made up of a double conveyor line that transports goods from production to the warehouse. “Its main function is to convey pallets with carton trays containing empty bottles, boxes, and metal containers with polyethylene terephthalate (PET) preforms.” The solution chosen could transport up to 5,000 pallets a day; in other words, ALPLA would double the number of movements between the production plant and the warehouse.
The conveyors, which transport the goods automatically, comprise a set of rollers that carry the load and propel it along a line. The system is equipped with electric motors that move the unit loads in a safe, controlled way. Roller conveyors save time and improve efficiency in repetitive load movements with pre-plotted circuits.
In addition to the conveyors, Mecalux has installed seven automatic lifts that move pallets vertically. The lifts overcome differences in height between the conveyor lines and the floor of the raised tunnel. Thus, the pallets’ entire journey from the production plant to the warehouse is automated.
A checkpoint has been set up at the beginning of the conveyor line, right where the pallets come off the production lines. This automated pallet gauge and quality control system is vital for ensuring that both the goods and the pallets entering the conveyor line are suitable for circulation and will not cause any type of accident. The checkpoint verifies that the sizes, weights and condition of the pallets meet the facility’s specifications.
Main components of roller conveyors
- Rollers. These metal cylinders include an axis and two bearings. Placed one behind the other, they support the weight of the pallet and move it to the end of its path.
- Metal structure and legs. These support the rollers and are made of different types of steel, depending on the weight they have to bear. They determine the direction of the conveyor line.
- Electrical components. The movement of the loads along the line is driven by electrical components, motors and power boxes. Power requirements will depend on the necessary speed and load weight to be moved.
- Safety elements. Mechanical devices and sensors, i.e., stops and photocells, ensure the safety of the system. These elements always know where the load is and communicate this information automatically to the control software.
Efficient manufacturing logistics
“The ALPLA complex in Golborne is in a strong position and is poised to continue growing,” says Grimwood. To continue strengthening its presence in the UK market, the company promotes the Lean methodology in its logistics processes. That is, it fosters activities that add value to the business to increase product flows and minimise costs.
The Mecalux solution has provided ALPLA with efficient logistics operations that are connected to production through automated conveying systems. Nowadays, industry demands flexible and diversified production systems in which, to provide efficient customer service, all the gears of manufacturing logistics need to fit together perfectly. With the solution installed, ALPLA’s supply chain is more efficient, optimised and prepared to take on both present and future challenges.
Thanks to the automated transport solution from Mecalux, we’ve slashed costs and CO2 emissions. We can now move around 2,500 pallets a day, 24/7.
Gallery
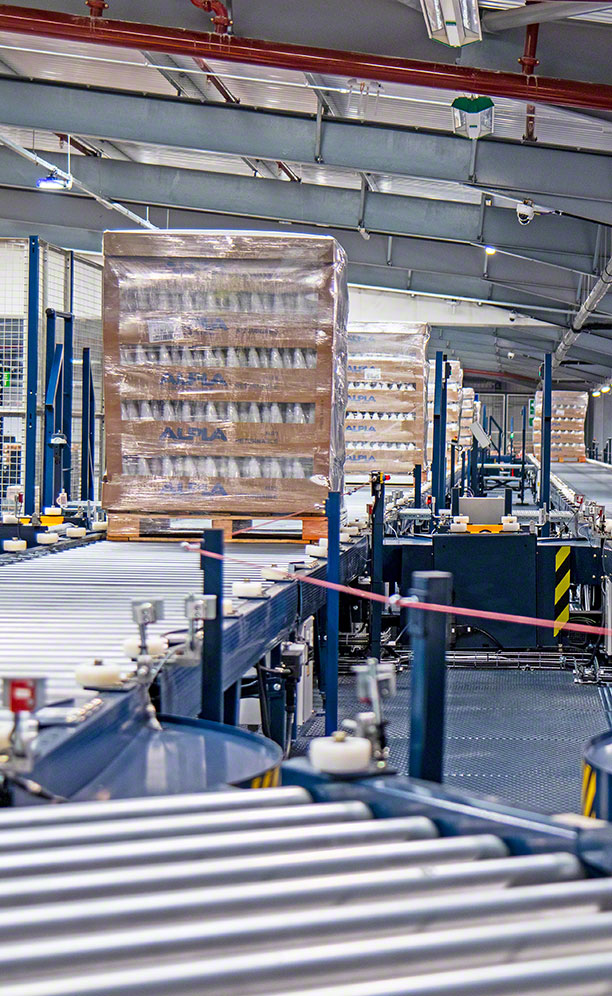
Automatic conveyors for pallets in ALPLA's logistics centre
Ask an expert