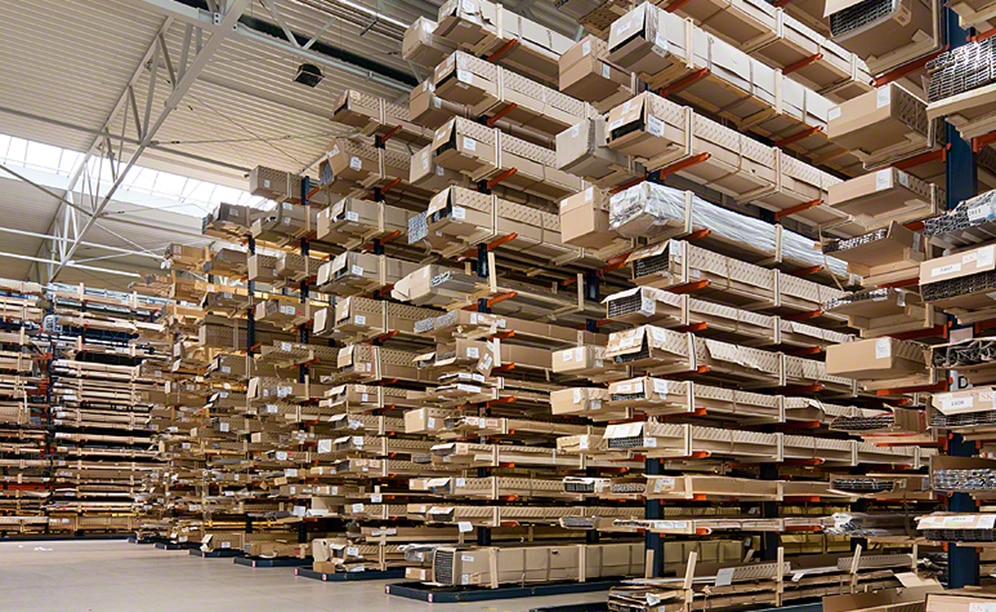
Aluminium profile warehouse of Aluprof with cantilever racks and pallet racks
The aluminium profile manufacturer Aluprof obtains maximum storage capacity
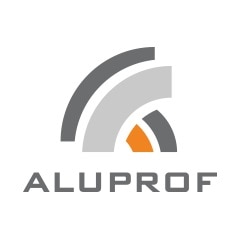
Aluprof has set up both cantilever racking and pallet racks in its finished products warehouse located in Bielsko-Biała (Poland). Featuring a multi-solution system designed to house aluminium profiles and pallets of varied volumes, it provides direct access to the goods, streamlining tasks related to storage and order picking.
About Aluprof
With more than 50 years under its belt, Aluprof is the largest manufacturer of aluminium profiles in Poland and one of the companies leading the European market in this sector. It makes and supplies aluminium building materials like windows, doors, blinds and shutters, fire protection systems, etc. By constantly developing new products, the company satisfies its customers’ needs, no matter how selective they may be.
In recent years, it has broadened its market participation and currently has delegations in various European countries (Germany, the UK, Ukraine, Czechia, Hungry, Romania, Belgium, the Netherlands and Denmark), as well as in the US.
Needs and the solution
The company requested Mecalux’s expert advice to fit out its warehouse located in the Bielsko-Biała (Poland) manufacturing centre. Since different sized and rotation SKUs need to be stored, a quick pick system for fast workflows was key.
In light of the criteria presented by the customer, Mecalux proposed and provisioned cantilever racking and pallet rack bays. Extra-long aluminium profiles are placed in the first ones and palletised goods in the second.
Marek Ściga - Warehouse manager at Aluprof
“Seeing that our products are stored in racks supplied by Mecalux, we have been able to: deploy our own WMS, really apply the FIFO principle to manage goods, access and handle each SKU in short-order and make our warehouse safer for staff during storing operations.”
Cantilever racking
Cantilever racks comprise 8.5 or 9 m high columns, with nine, ten or fourteen levels (depending on the proportions of the goods), and cantilevered arms where unit loads are set.
Four-way sideloading forklifts are used to handle goods, given that they are able to move inside narrow aisles to transport up to 12 m long materials in a very balanced way.
Floor guides were installed in each warehouse aisle so that the forklifts run through the aisles in a completely safe manner and avoid blows against the racks and the merchandise.
Pallet racking
Two distinct pallet rack solutions were installed. On one side, 7.5 or 8.5 m racks, fitted out with 4 or 6 storage shelves and warehousing capacity in excess of 2,400 pallets.
On the other, custom racks further fulfil the company’s needs. These are designed specifically to adjust to product features, running longer than the pallet dimensions. Standing 4 m high, they include 5 or 6 levels where they house products that are 4 m or longer and have a total maximum weight of 3,500 kg.
This storage system puts the spotlight on rack versatility and on producing direct-to-goods access. Quality and efficiency have been positively and meaningfully affected during storing and order prep work. In addition, it guarantees excellent stock control, since each location is assigned to the same SKU.
Order preparation
Picking takes place on the lower tiers of the racks, which is done in two ways: the collection of full boxes right off the pallets or longer profiles off racks with a unique product pick design. On the other hand, the upper levels house pallets of reserve product.
Workers sweep through the warehouse with ground-level pickers locating the SKUs for each order, as instructed by the warehouse management software (WMS) via radiofrequency devices.
Once the order is complete, the operators take it to the consolidation area. There, orders are checked for errors.
Last but not least, the boxes are closed, packaged, labelled and issued delivery notes and documentation. Next, ground-floor pallet grouping from the same order or route speeds up the subsequent loading of transport vehicles.
Advantages for Aluprof
- Faster operations: pallet racking offers direct access to the deposited SKUs, which facilitates stock management and pick tasks.
- System versatility: cantilever racking can accommodate very long profiles and the pallet racks, different size and volume loads.
- Space optimised: the height and breadth of the installed warehouse system make full use of facility space, by setting up the maximum number of racks possible to attain a better storage capacity.
Warehouse of Aluprof: Cantilever racking | |
---|---|
Racking height: | 8.5 or 9 m |
No. of levels: | 9, 10 or 14 |
Gallery
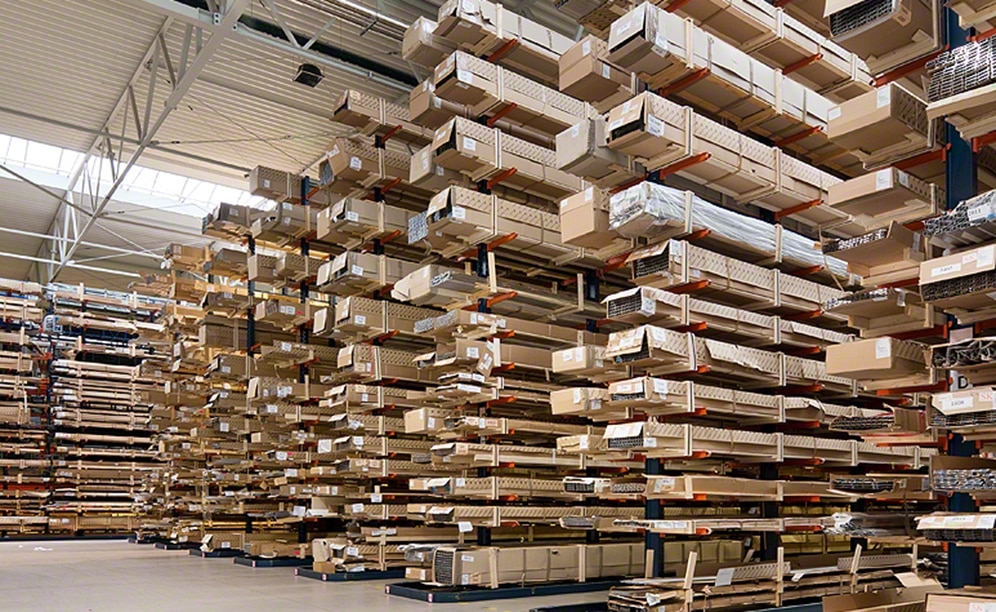
The aluminium profile warehouse of Aluprof with cantilever racks
Ask an expert