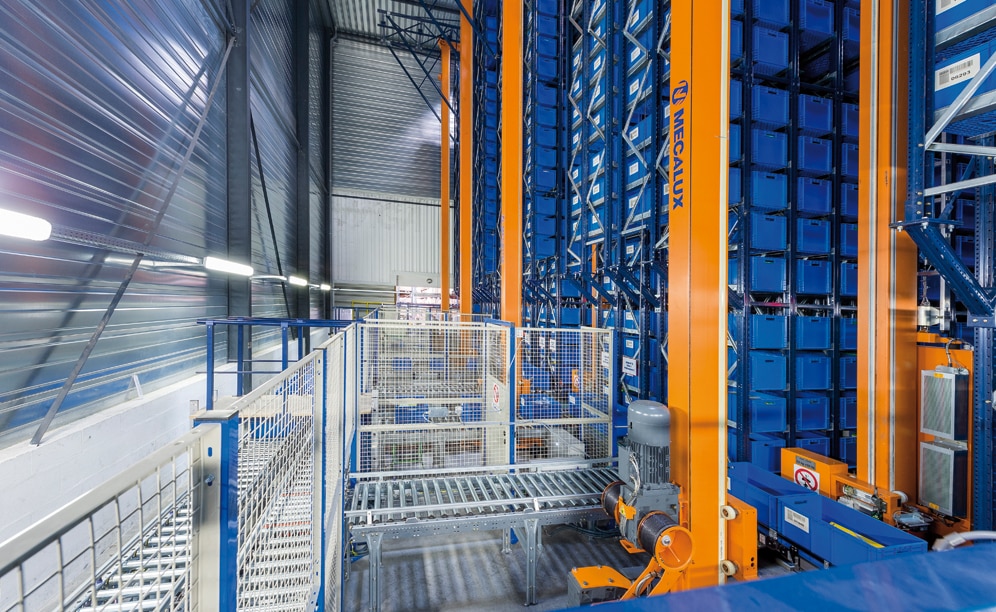
Mecalux has installed an automated miniload warehouse with a capacity of 15,872 boxes for MGA
MGA improves agility picking and service to its wholesalers
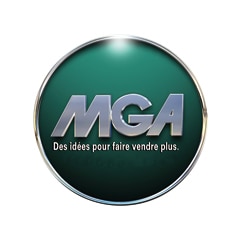
MGA is an important spare parts distributor with regional warehouses in different cities within France. The priority of the company is to offer express delivery to its customers, generally automobile replacement part wholesalers. For the new logistics centre located in Saint-Quentin Fallavier, a town close to the city of Lyon, MGA chose Mecalux as provider of all management and storage systems, including an automated miniload warehouse with a capacity of 15,872 boxes.
In this logistics centre, Mecalux has installed an automated miniload warehouse with a specific picking area and a warehouse for pallets placed on conventional type racks. It has also included the implementation of a Mecalux Easy WMS (warehouse management software), tasked with handling all operations, from the entry of goods till dispatch, previously passing through the storage and picking phases.
Conventional pallet racks
The conventional pallet rack warehouse is intended for bulkier products and items with greater turnover (A type) placed upon pallets. Racks have two lower levels to conduct direct picking from the pallets, while reserves are placed on upper levels.
This storage system is characterised by its simplicity and capacity to adapt itself to the needs of the company. In addition, conventional pallet racks make it possible to directly access each pallet, storing the maximum number of unit loads in a safe and organised way.
The miniload warehouse
A miniload warehouse with four aisles, and two double-deep racks (one per side), was installed, allowing storage of a total of 15,872 plastic euro-boxes, 600 x 400 x 320 mm in size. The height of the racks is 12.3 m and the total admissible weight per box is 50 kg.
All medium and small sized products are located in the miniload warehouse, generally B and C type items. These products are handled by four stacker cranes, three picking stations and a replenishment station.
The construction of the miniload warehouse was done in two phases, in accordance with the needs of MGA. The first included three storage aisles with three stacker cranes and three picking stations, while in the second they installed four aisles, set up a new stacker crane and completed the replenishment station.
If we analyse the parts that the facility is composed of you will see the following:
- A) An automated warehouse
- B) Automated warehouse conveyors
- C) Three pick stations
- D) A replenishment station
Double-mast stacker cranes were installed; the extraction system placed in the cradle is a double box and double-deep, being capable of handling two boxes at a time. The extractor is formed by a fork and two independently moving belts that allow them to interchangeably pick boxes from one or another side, first moving to the contrary side where you are going to make the second extraction.
The conveyor system has been sized to move great quantities of boxes that may coincide with times of higher demand, while the travel speed, and mainly the stacker crane’s lifting speed, were adjusted to the characteristics of this warehouse.
In addition, a cantilevered structure has been made above the loading and unloading stations, managing to increase capacity by 320 more boxes.
In the rear, equipped with a large maintenance area, there are reference devices for the position of the stacker crane. The whole space is enclosed with mesh panels and safety doors that will individually disconnect the machines in case they are opened.
Picking stations
The enclosure where the main warehouse is located is independent of other buildings and, in particular, from the picking station, which was installed on the side of the warehouse.
The picking stations, in the shape of a "U", are located terraced perpendicularly to the main conveyors. These conveyors are comprised of a double circuit that allows both the re-circulation of boxes, as well as the connection to the warehouse and the replenishment station. Moving boxes to either of the two main conveyors is direct, thus avoiding unnecessary movements.
Each station, with capacity for three boxes on hold plus the one which is being processed, is run by an operator, who in turn is able to prepare waves of six orders at the same time. To that end, there is a computer connected to the Mecalux Easy WMS (warehouse management software) and different support devices for picking. For example, put to light devices placed on top of the containers of each order, indicating to the operator which order each item corresponds to.
On the pallets/containers of each order, the item location in the pallet racks has been previously introduced, that is to say, this same zone serves as an order consolidation area. In this way, fast and agile order preparation has been achieved.
Easy WMS
The Mecalux Easy WMS (warehouse management software) is the nerve centre that manages all the necessary functions for the general operations of any type of warehouse, regardless of its complexity.
Easy WMS controls: all the inbound processes, the warehouse locations, stocks, location rules, storage and extraction, the pallets that have to go to picking stations, the picking itself, returns to the warehouse, etc. It is also able to analyse the state of distinct parts or areas via query and reporting tools, as well as the devices that operate in it.
Easy WMS is in bidirectional and permanent connection with the customer's SAP ERP, exchanging information and the orders necessary for the proper functioning and control of the various operations.
Advantages for MGA
- Improved storage capacity: the MGA miniload warehouse offers a storage capacity of 15,872 boxes.
- Increased productivity: thanks to the high level of warehouse automation, the speed of order preparation has increased.
- Perfect stock control: thanks to the Mecalux Easy WMS, the company MGA can manage all movements, processes and operations that take place within their warehouse.
Conventional pallet racks warehouse | |
---|---|
Pallet capacity:: | 1,480 pallets |
Maximum weight per pallet:: | 1,000 kg |
Gallery
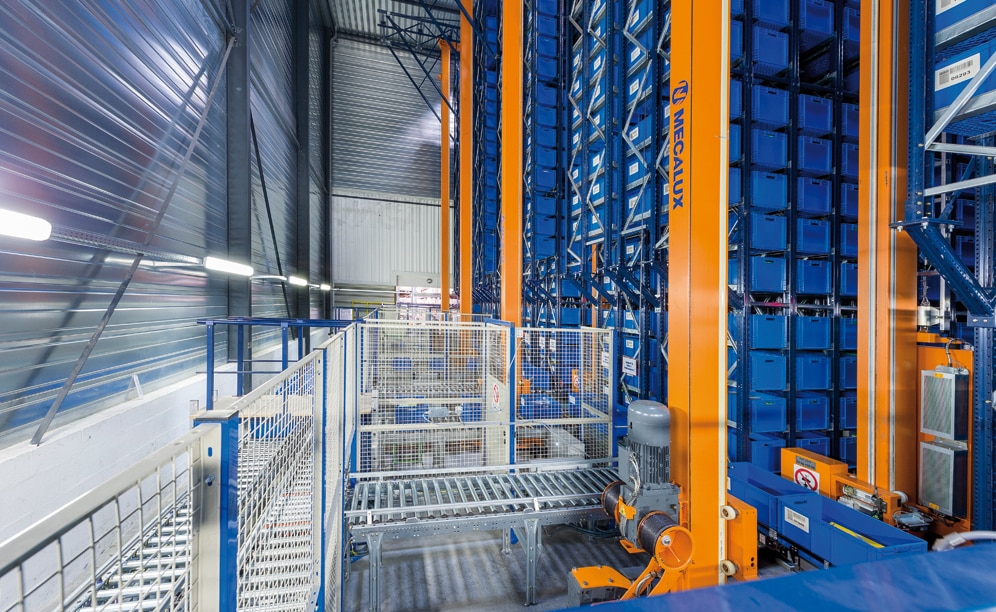
Ask an expert