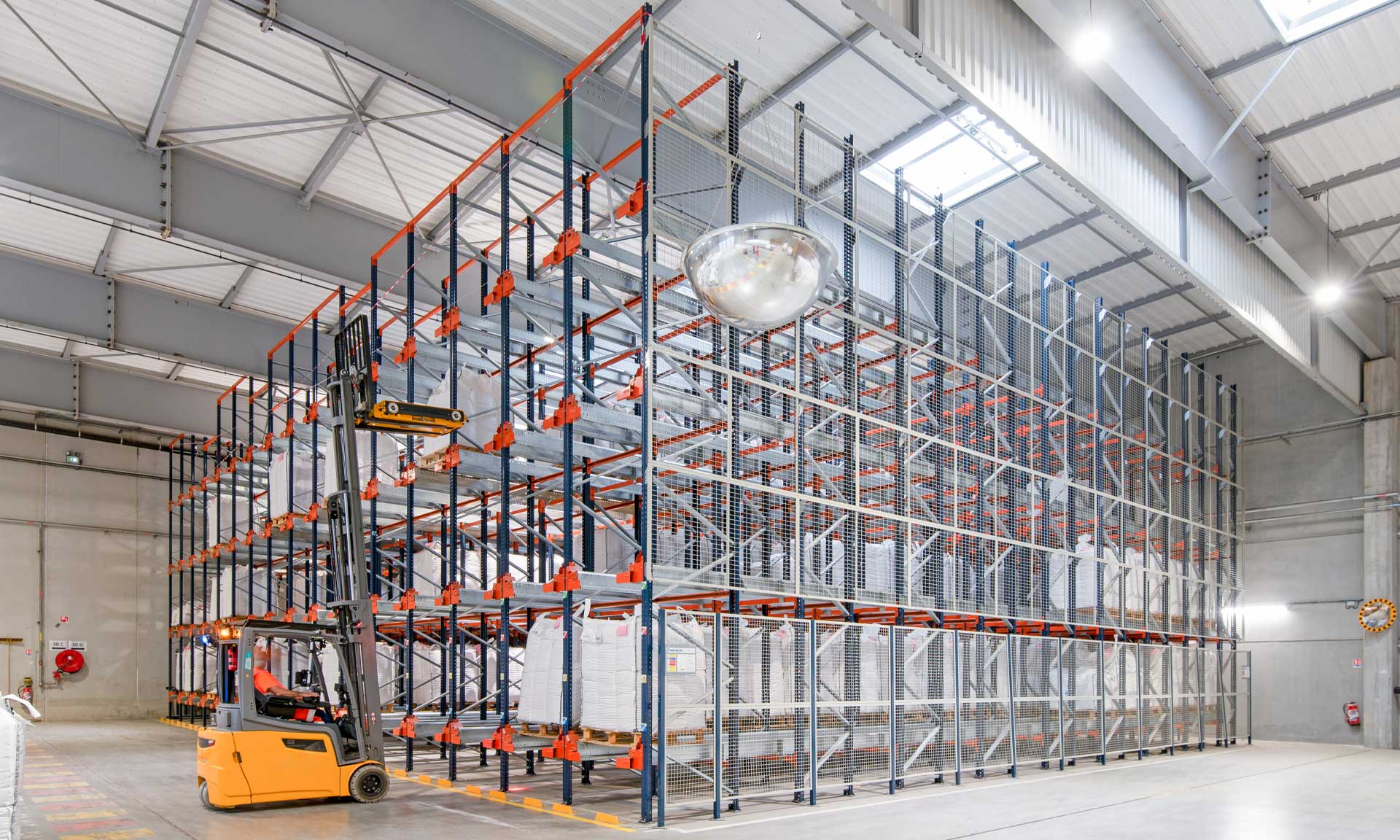
High-density storage for Bayer, a leading global agricultural company
International group Bayer has a warehouse where it manages 11,000 tonnes of seeds a year for its Crop Science unit.
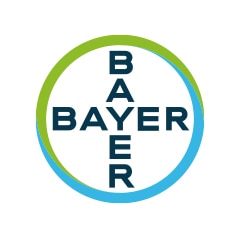
Bayer, an international life sciences group whose core business is centred on healthcare and agriculture, has a warehouse in Trèbes, France. There, Bayer manages 11,000 tonnes of seeds a year for its Crop Science division with the semi-automated Pallet Shuttle system from Mecalux.
Founded in Germany in 1863, Bayer is a company specialising in life sciences. The multinational has three main business units: Pharmaceuticals, Consumer Health and Crop Science. Pharmaceuticals develops and markets prescription medications for cardiovascular diseases, women’s health, ophthalmology, neurology, haematology, oncology and radiology. Consumer Health focuses on vitamins and minerals, skincare and dermatology treatments, digestion, herbal medicine, pain management and women’s reproductive health. Lastly, Crop Science, a leader in the field of agriculture, offers a complete range of solutions for farmers based on its four pillars: seeds, plant protection products, biocontrol and digital agriculture.
- Founded in: 1863
- International presence: 100+ countries
- Group sales (2020): €41 billion
- No. of employees (2020): 100,000
CHALLENGES
|
SOLUTIONS
|
BENEFITS
|
---|
In the French town of Trèbes, home to Bayer’s Crop Science division, the company has a complex dedicated to the production of corn and rapeseed. With a network of 400 contract farmers and a professional team of nearly 200 people, Crop Science works every day to provide quality seeds to farmers to meet the yield, quality and sustainability challenges of agricultural production.
“The centre has a warehouse where we mainly store semi-finished products used during our production season. We also manage finished products prior to their dispatch to other facilities in France and the rest of Europe,” says Thomas Prunel, Warehouse Manager at Bayer’s facility in Trèbes.
When it first started out, Bayer stacked its products in blocks directly on the floor. When its business began to grow, the company decided to modernise its logistics operations by installing racks and a semi-automated storage system. “Our main need was to optimise our storage capacity and improve safety in goods handling,” says Prunel.
Bayer chose to implement the semi-automated Pallet Shuttle, a high-density storage system that employs a motorised shuttle to move pallets inside the storage channels. As the shuttle is automatic, Bayer has considerably reduced its goods entry and exit times.
“With the semi-automated Pallet Shuttle system from Mecalux, we’ve gained in warehousing capacity, in efficiency when storing and dispatching pallets and in operator safety,” says Prunel.
Prunel also explains Bayer’s reasons for relying on Mecalux: “In a market where you find similar storage solutions, we chose Mecalux because, right from the start, there was trust between our team and theirs. Mecalux’s on-the-ground analysis and support work were also factors, with many ideas and proposals exchanged to tailor the solution to our needs.”
High-density storage
Bayer’s logistics centre has capacity for 5,500 pallets “that store 1-tonne big bags carrying seeds ready to be marketed. The goods are managed by SKU and production batch,” says Prunel.
Mecalux installed a total of 10 high-density racking units distributed among four different areas of the Bayer centre. High-density storage is a system that eliminates aisles in which handling equipment operates in order to condense locations, storing pallet after pallet in the smallest amount of space. With capacity for a maximum of 15 pallets deep, the goods housed are managed according to the LIFO (last in, first out) method. The procedure is as follows: using a forklift, the operator places the motorised shuttle in front of the storage channel where the pallet is to be stored. Positioned at the entrance to the channel, the electric shuttle moves the pallet horizontally to the deepest available location. Once the goods are stored, the motor-driven shuttle returns to the channel entrance to repeat the same movement with the next pallet.
The motorised shuttles follow instructions sent by the operators via a tablet with a Wi-Fi connection. The software features a wide range of options for performing the different goods loading/unloading and maintenance operations. The program interface is extremely intuitive, so users learn very quickly how to operate it. Additionally, the electric shuttle is equipped with multiple sensors and mechanisms to ensure precise, fast and safe goods movements.
By eliminating the need for forklifts to operate with the racking, Bayer has increased its storage capacity — thanks to the depth of the racks — and minimised the risk of potential accidents. The Pallet Shuttle system compresses a large quantity of goods, so Bayer has enough products to supply its customers in the case of a sudden spike in demand or any unforeseen supply chain event.
11,000 tonnes of seed annually
“This logistics project has taken our warehouse to new levels.” It is clear to Prunel that the Pallet Shuttle is the solution that best fits Bayer’s logistics needs: it represents an evolution of high-density systems, such as the block stacking formerly used by the company.
Prunel says that the company’s forecasts point to continued growth: “Our volume of activity continues to rise. For this reason, we’re considering installing the semi-automated Pallet Shuttle system in another area where we still store products in blocks.”
The automation provided by the Pallet Shuttle system boosts speed and throughput, enabling Bayer to have a supply chain that supports the production of 11,000 tonnes of seeds a year.
We chose the semi-automated Pallet Shuttle system because it was the ideal solution for increasing our daily throughput. Thanks to this solution, we’ve gained in warehousing capacity, in efficiency when storing and dispatching pallets and in operator safety.
Gallery
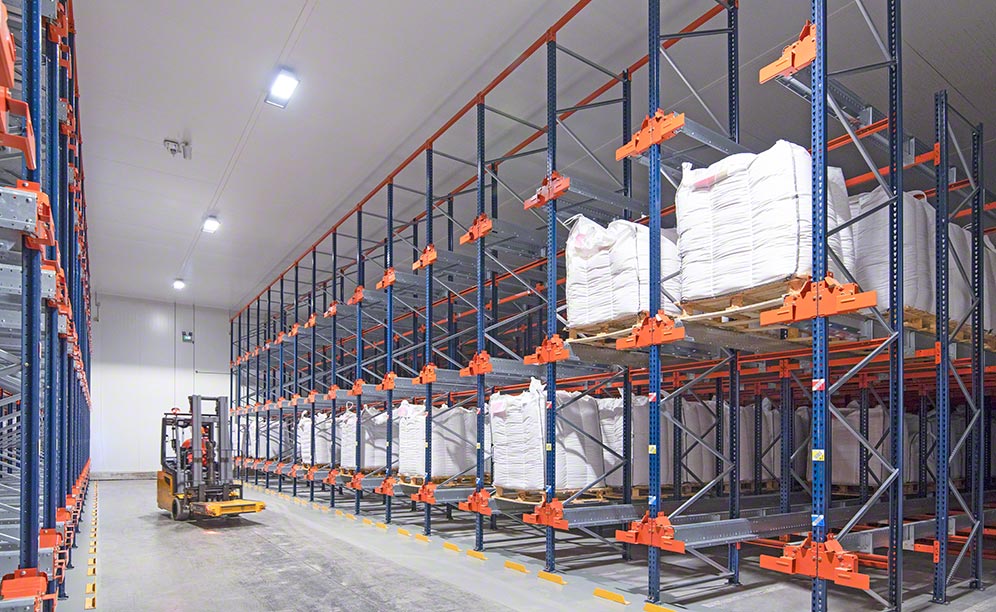
Bayer's warehouse in Trèbes with Pallet Shuttle system racking
Ask an expert