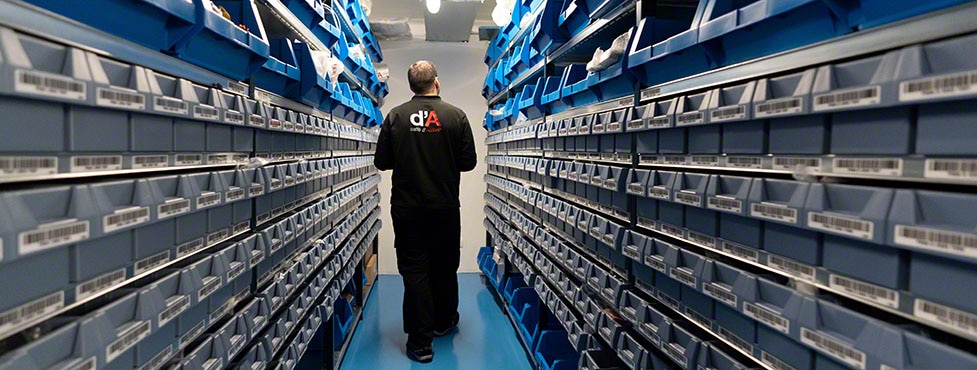
Caffè d’Autore: all logistics begin with a good cup of coffee
Easy WMS from Mecalux has streamlined the management of the entire Caffè d’Autore supply chain
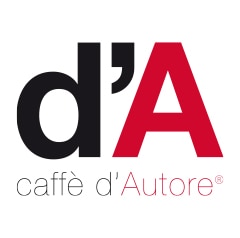
Caffè d’Autore, a service company and distributor of espresso machines for bars, cafés and restaurants, has improved its logistics through a complete solution from Mecalux: racks for picking and the implementation of Mecalux’s Easy WMS in its warehouse in Barcelona (Spain). This system precisely controls the 2,800 available SKUs and scrupulously manages all operations. As a result, the company has streamlined its order preparation and reduced the time spent on inventory calculation by 50%.
The perfect cup of coffee
Caffè d’Autore defines itself as a technologically advanced and coffee-loving company. Its main activity consists of providing services to its partners and distributing La Spaziale, an Italian coffee machine that is a leader in the hospitality sector.
“Although our main business within the services we offer is the sale of coffee machines and grinders, we also have significant technical activity for which we need spare parts. This activity represents a growing percentage of the overall turnover, and we consider it a strategic activity for our company. As a result, we want to strengthen it,” explains Roger Vilaplana, Technical Department Director at Caffè d’Autore.
Although Caffè d’Autore’s offices and warehouse are located in Barcelona, the company is very close to its customers in the rest of Spain thanks to the 150 technicians strategically located throughout the country. With this working method, it provides after-sales service to companies that use La Spaziale, either by supplying them with spare parts or carrying out maintenance work.
Technology and innovation are two basic characteristics of the company. “Our technicians have been using tablets for many years, so we have eliminated the use of paper — a critical link in the digitalisation of our processes,” says Roger Vilaplana. Now Caffè d’Autore is embarking on an ambitious project in the coming months: the opening of an online shop from which customers will be able to buy spare parts. “In order to take that step, all our logistics need to be well structured,” says the Technical Department Director.
Functioning of the warehouse
Caffè d’Autore’s 240 m² warehouse is equipped with Mecalux racks for picking. They are 2 m high and contain more than 2,800 SKUs of small dimensions and different rotations, mainly consisting of components and accessories for coffee machines.
“We manage our stock on the basis of maximum and minimum levels and make scheduled replacements, prioritising products that are indispensable for providing service”, states the Director of the Technical Department. “Because they are such small items, handling them is a complex task with a high risk of error,” he acknowledges.
Every week, Caffè d’Autore receives several pallets that are sent by its suppliers (not only La Spaziale, but also other coffee solution manufacturers). All these pallets include about 350 items that have to be counted, sorted and stored in the appropriate location. According to Roger Vilaplana, “since we were dealing with such a large number of items, we used to spend a whole day checking the goods received.”
Caffè d’Autore wanted to perfect its storage and order preparation processes, so it had to reorganise the goods distribution. “I think that the work we were doing was wholly in order, but I also knew it could be improved, especially in terms of efficiency. That is why all areas of the company became involved in this project,” says the Technical Department Director.
Previously, products were grouped into families, and each slot was assigned to a single SKU. The disadvantage was that if a slot was left empty, it was not reoccupied until more products with that SKU arrived, thus wasting warehouse space.
The company also had difficulty monitoring its inventory. “We have a small staff, and this familiarity meant that any employee could enter the warehouse at any time to pick up spare parts,” points out Roger Vilaplana. Lack of protocol monitoring led to stock-outs.
The company, therefore, considered digitalising its logistics and started looking for a market-leading supplier of warehouse management systems (WMSs). It needed a WMS that would optimise the available operations and resources, increase throughput and ensure an efficient and error-free working system.
After analysing in detail the needs of Caffè d’Autore, Mecalux experts proposed the implementation of Easy WMS in collaboration with Code Biting, a company belonging to the Mecalux partner programme. Code Biting was in charge of configuring and parametrising the software to adapt it 100% to the customer’s specific operations, as well as carrying out specific training for warehouse personnel.
Easy WMS is integrated with the Sage 200c ERP so that the warehouse operations are coordinated with the company’s requirements. Pere Deulofeu, ICT Director at Caffè d’Autore, explains that the integration process was “very fast and convenient.” A Microsoft SQL intermediate database has been created between the ERP and the WMS for the two systems to exchange messages on how to perform warehouse operations.
The result of this process is a much more productive warehouse. The team has noticed a substantial improvement in inventory taking. With this software, they have reduced the time spent on inventory by 50%, in addition to being able to do so without interfering with daily operations.
Roger Vilaplana - Technical Department Director at Caffè d’Autore
“With Easy WMS from Mecalux, we have optimised the operations and spaces in our warehouse. We have also eliminated errors and improved service. In short, we are faster and more efficient in serving customers.”
New organisation, new logistics
Caffè d’Autore has implemented Mecalux’s Easy WMS, which controls the receipt of goods, the distribution of items within the warehouse, the work of the operators and the preparation and dispatch of orders.
Receipt of goods
“We have noticed great improvement in this area,” says Roger Vilaplana. Receipt of the goods is much faster, going from allocating a whole day to check the goods received to doing so in just a few hours and without interrupting the other warehouse processes. The operators, using radiofrequency terminals, at all times follow instructions from Easy WMS, which tells them what to do with each product. With this system, moreover, the margin of error is minimal.
The company has also improved the management of back orders (those that cannot be completed until the required item arrives). “The WMS prioritises this type of order and instructs the operators to complete it with the products that have just arrived so that they can be distributed as soon as possible,” states Roger Vilaplana.
With the installation of Easy WMS, Caffè d’Autore has introduced the barcode system in the warehouse. “We have had the opportunity to modify our way of working, and now, suppliers send us products already labelled with barcodes. The effort has been worthwhile, and, as a result, we have considerably speeded up our receptions", says the Technical Department Director.
Storage of goods
Once each item is identified, the WMS assigns it a location depending on its characteristics and demand level. Thus, for example, high-demand items are deposited in the most accessible areas to facilitate their entry and exit.
Currently, the installation employs a chaotic product placement strategy. Despite this paradoxical name, the warehouse follows a very strict order. Easy WMS allocates a location to each product, taking into account its rotation and the spaces available in the warehouse.
The WMS knows the stock status at all times and can locate it in real time. “We have gained reliability and minimised inventory mismatches, aspects on which all processes depend,” says Vilaplana.
Very orderly chaotic placement
The warehouse’s chaotic placement strategy has brought the following advantages to Caffè d’Autore:
- Optimal use of space. The company makes better use of all free space.
- Agility in storage tasks. The WMS automatically assigns a slot to each product. Operators do not need to learn the layout of the plant or decide where to deposit each product.
- Design of the routes through the warehouse. The WMS optimises the movements of the operators so that they travel the minimum distance possible in storage and order preparation tasks.
- Greater precision. Oversight by Easy WMS prevents mistakes in order picking and rack replenishment.
Order preparation and dispatch
From the warehouse, Caffè d’Autore sends spare parts to customers and its team of technicians. These have vans designed as warehouses, as they require weekly replenishment and management of maximum and minimum item numbers.
Before starting to prepare the orders, Easy WMS arranges the printing of the labels and the delivery note for each of them. The operators prepare the orders, made up of 15 lines each on average. To do this, they walk through the warehouse following the directions from Easy WMS, which tells them which slot to go to, which items to pick, and in what quantity. The operators pack the items, label them and, once the order is completed, box them up together with the delivery note.
They then organise the orders according to whether they are to be sent to the customers or to the vans. A good organisation of this process minimises failures and makes the distribution of goods more dynamic.
Coffee-scented technology
Caffè d’Autore is a modest company with a huge project on its hands: to ensure that thousands of people start the day with a delicious cup of coffee. In order to make this possible, the company has always relied on technology, through which it can carry out advanced supervision of all processes, jobs and resources.
Its supply chain is complex, given that it has 2,800 SKUs of multiple dimensions and rotations. However, Easy WMS by Mecalux has simplified its management, which has led to an improvement in productivity and service quality.
Easy WMS not only organises all the goods in the warehouse, but also the storage and order preparation activity. The availability of the goods is a priority for Caffè d’Autore. Its more than 150 technicians distributed throughout Spain must always have the necessary spare parts to serve customers in a timely manner.
Advantages for Caffè d’Autore
- Stock always available: Easy WMS controls Caffè d’Autore’s inventory and knows the exact location of each of the 2,800 SKUs stored. All this has the aim of planning the work and ensuring the distribution of spare parts at the right time.
- A complete solution: the racks for picking and Easy WMS have completely transformed Caffè d’Autore’s logistics. Direct access to products on the racks and WMS monitoring help in the completion of all orders.
- Dynamic goods receipt: the company has simplified goods receipt, one of the busiest areas in its warehouse. Previously, it was necessary to invest a whole day to check the items; with Easy WMS, this process is now done in a few hours.
Warehouse of Caffè d’Autore | |
---|---|
Warehouse surface area: | 240 m² |
No. of SKUs stored: | 2,800 |
No. of items received/week: | 350 |
Gallery
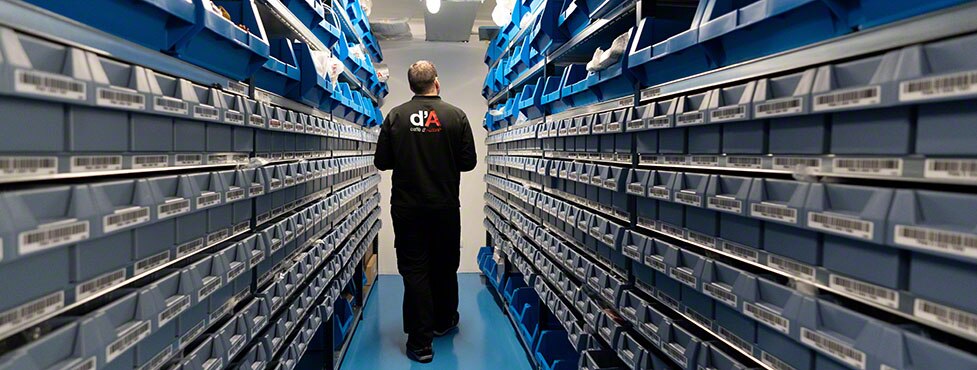
Storage of Caffè d’Autore espresso machines in Barcelona
Ask an expert