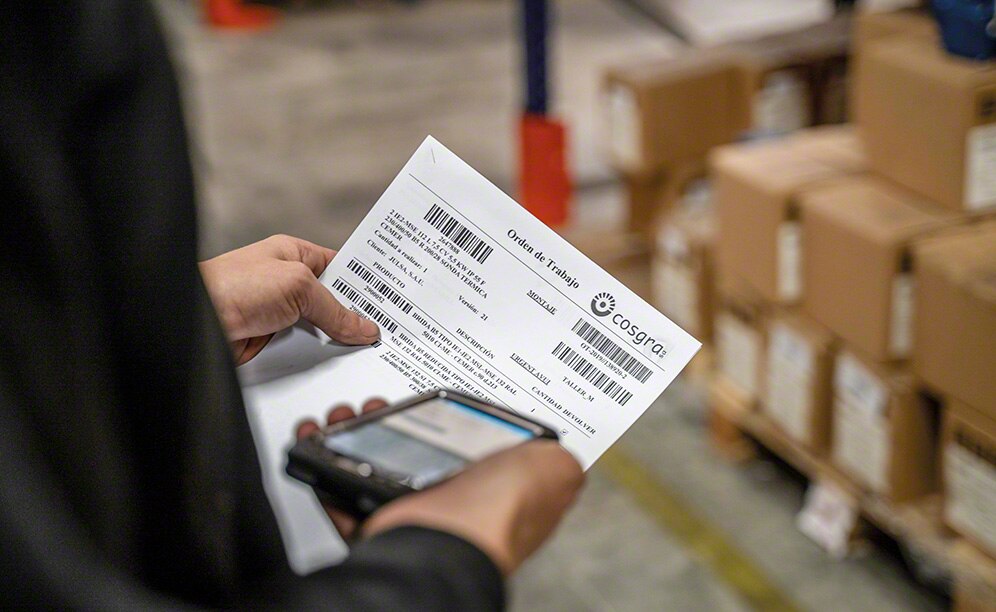
Easy WMS at the Cosgra warehouse in Girona for engines and spare parts
Mecalux's Easy WMS warehouse management system manages the Cosgra warehouse for picking
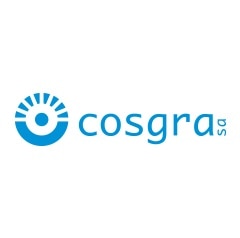
In its logistics centre in Girona (Spain), Cosgra stores in excess of 10,000 different SKUs of electric motors, gearboxes, drum motors and mechanical seals. Mecalux’s Easy WMS warehouse management software is a system that controls all stock and avoids any potential error in storage and order preparation tasks. The WMS not only oversees, coordinates and manages the movements, processes and operations of the warehouse, but also ensures a high level customer service.
Rotating equipment solutions
Headquartered in Girona (Spain), Cosgra distributes electric motors, gearboxes, drum motors and mechanical seals for automotive and electronics companies, plus machinery manufacturers.
Since it was founded in 1980, it has been a pioneer and an innovative trendsetter in the sector, as well as being oriented towards the international market. Today, it is one of the largest companies in the industry within southern Europe: it markets its products in over 20 countries in Europe, Africa and Latin America.
Shared engine-spare parts warehouse
Cosgra’s priority is to supply its customers promptly. So, the warehouse’s site is crucial to ensuring quick delivery times. “It is located in Crespià (Girona), in a strategic point next to the motorway between Barcelona and the French border. It is very close to the Barcelona, Girona and Perpignan airports,” explains Jordi Company, Cosgra’s production manager.
Not only is the warehouse’s position crucial to speeding up order distribution, but also to sound management of all operations and goods. The company has a catalogue with over 10,000 SKUs, all of different sizes and volumes. Divided into two areas (one for engines and bulky products, and another for spare parts and smaller products), this warehouse feature makes it easier for in-house operators to work.
Jordi Company - Production Manager at Cosgra
“We are very satisfied with the warehouse management system from Mecalux. Obviously, we had to get up to speed. Plus, it took time to learn to use the WMS, count our inventory and register it all in the system. But, in the end we didn’t care because the benefits were obvious and our operators are a flexible bunch of people.”
All flows managed
Cosgra had a particular interest in revamping its warehouse operations to become more flexible and cope better with continuous market changes. To achieve this, it needed a warehouse management system (WMS).
“Before, we used an ERP that ran all the company’s activities, including part of the logistics. Only the ERP managed the in-warehouse stock: we knew what we received, what we had stored and what we shipped out. However, we couldn’t keep track of product characteristics or their exact location,” says Jordi Company.
Cosgra has deployed the Mecalux Easy WMS warehouse management system to simplify and optimise operations and, all in all, make the most of its distribution centre. “We decided to work with Mecalux because of its brand image in the sector and its expertise in deploying warehouse management systems,” adds the production manager.
The Easy WMS benefits Cosgra most because of its flexibility and scalability, adapting to any change faced by the business. This might involve introducing new technologies in any of its processes, increasing sales, etc.
Before the Easy WMS was up and running, the different merchandise each had a descriptive product leaflet (with parts, characteristics, weight, functions, etc.), which was hardly practical. Instead, items are now tagged with a barcode that operators can scan using RF devices. “Including barcodes was the real breakthrough for our logistics. Each article has an ID number, which means we can locate it and fully trace its whereabouts. With that code, we can find any spare part within all the products supplied in the last five years,” points out Jordi Company.
Through the Mecalux software, the company also gets real-time information on the status of its inventory, where it comes from, where it is located and where it is going.
This translates into greater efficiency in the operators’ work, since they find the products customers request quicker. The Mecalux WMS has a hand in all Cosgra warehouse operations:Receipt of goods
At the dockside, operators are tasked with identifying and sorting all incoming products individually: engines on the one hand and spare parts on the other.
Good communication between the WMS, ERP and operators is essential to prevent errors. The ERP sends an entry order to Easy WMS specifying which items are about to arrive at the warehouse. Once received, the WMS tells the operators to inspect the products. Thus, it is possible to check that the goods specified by the ERP have arrived and, simultaneously, enter the products into the system and assign them a location.
Easy WMS also handles the returns. Occasionally, for whatever reason, customers may wish to return some of the products they purchased. In this situation, the same process applies, although Easy WMS decides what to do with each specific product: send it to the storage area, to the kit assembly area, to be repaired, etc.
Storage tasks
Once the engines have been separated from the spare parts, Easy WMS assigns a location to each product based on its characteristics and size. For example, bulky, heavier products are placed in the lower levels of the racks.
The operators use their radiofrequency handsets to identify the products and Easy WMS shows where to deposit them. The bulky goods zone uses pallet trucks to move products, while the spare parts zone uses hand carts.
Order preparation
More than 250 orders are put together every day, making order prep one of Cosgra’s core operations. Following Easy WMS’s instructions, operators roam the warehouse area assigned to them, locating the products that comprise each order. Operators stay either in the bulky product zone or in the spare parts area to avoid interference and potential mistakes. Once all the items have been collected, they are transferred to the assembly area. Here, the engines are mounted and personalised to meet each customer’s specific needs.
A more advanced supply chain
Mecalux’s Easy WMS represents a big step forward for Cosgra. Through this WMS, the company has streamlined the management of over 10,000 SKUs, from their arrival at the warehouse to their dispatch, guaranteeing total traceability.
The software was installed without stoppages in Cosgra’s customer service. “I admit it was pretty tough,” said Company, “because we have lots of SKUs and had to take an inventory of our warehouse. Even though it involved a lot of hard work, everything rolled along and our customers’ were unaffected by this process. And, we started distributing orders very quickly.” The WMS has become a tool, an ally for operators, because it guides them at every turn and makes their tasks easier. “This tool motivates our team and has helped them get the job done with ease. So, I’m please to say that Easy WMS has been well received,” celebrates the production manager. The warehouse is a strategic facility for this business, housing all the products required by its customers and organising engine assembly and their subsequent distribution.
The management system optimises and streamlines all processes as far as possible, resulting in greater efficiency and customer satisfaction.
Advantages for Cosgra
- Control over 10,000 SKUs: Easy WMS identifies products from the moment they arrive at the warehouse and assigns them a location. As a result, it always knows the real-time status of the stock.
- Accuracy and agility: Easy WMS’s supervision over all operations is central to ensuring that operators can carry out storage and order picking with no mistakes.
- Increased productivity: the warehouse is highly productive, being able to prepare +250 orders per day.
Logistics centre of Cosgra | |
---|---|
No. of stored SKUs: | +10,000 |
No. of orders prepared daily: | 250 |
Gallery
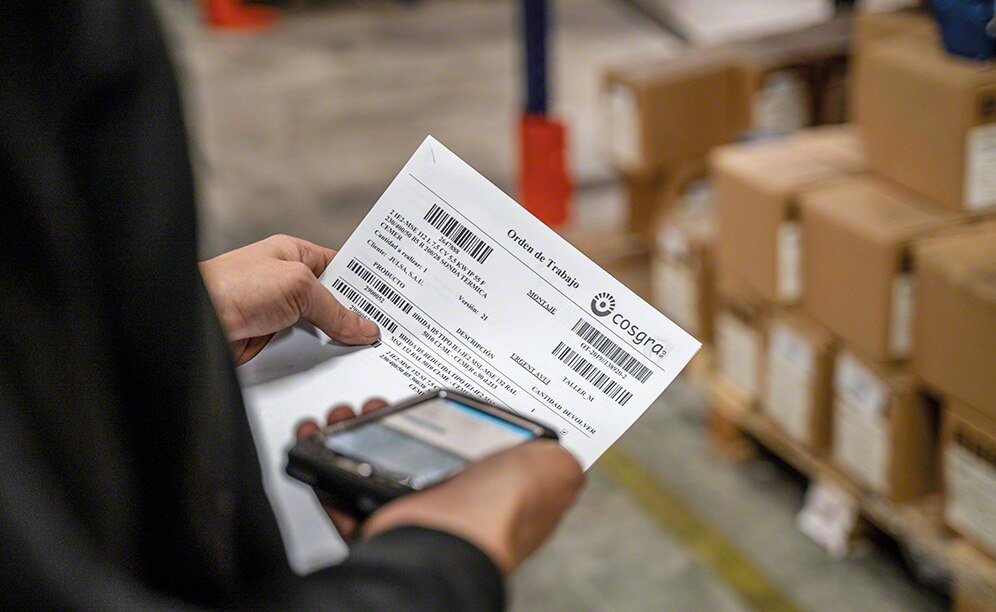
Radio frequency terminals receive Easy WMS commands
Ask an expert