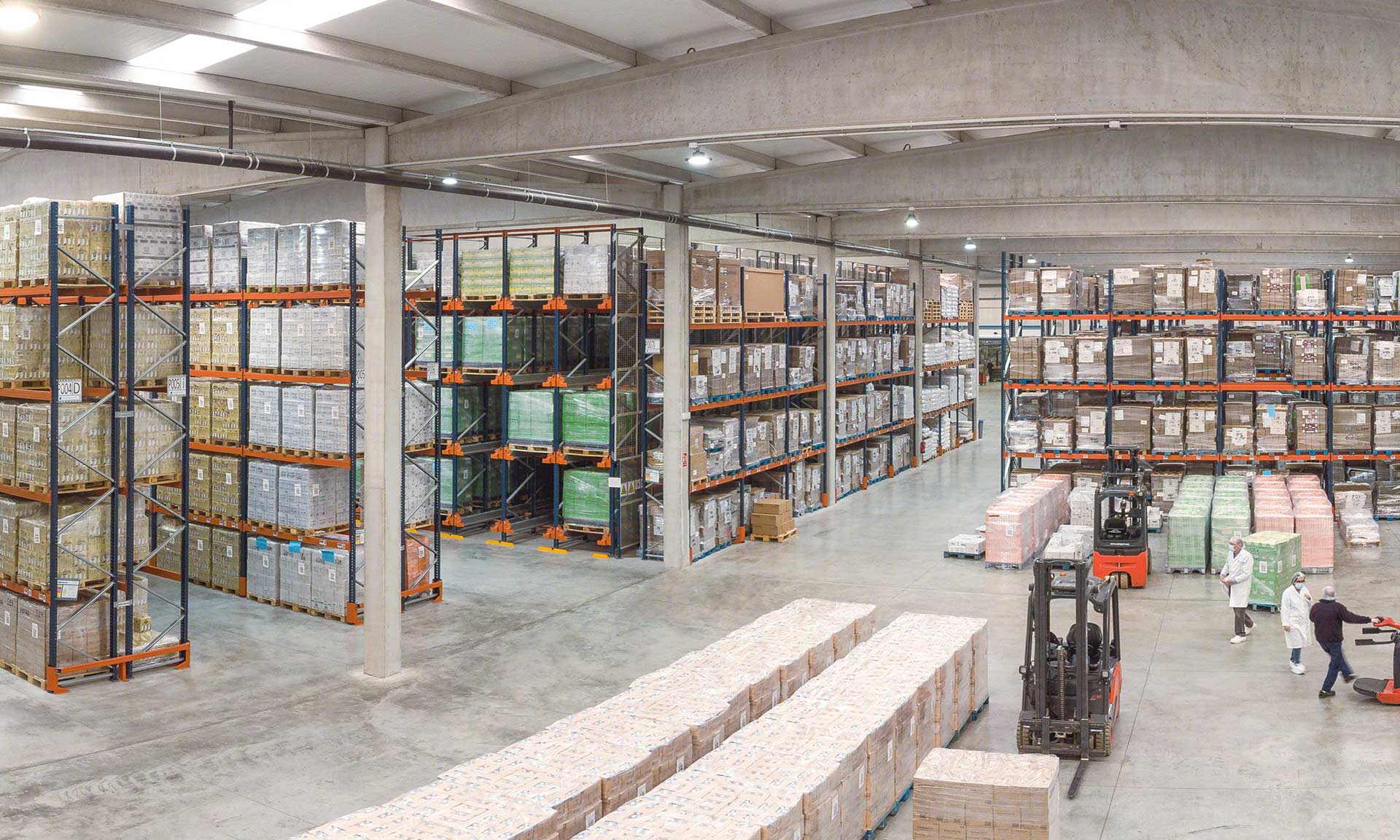
Costa Concentrados Levantinos: technology refreshes the supply chain
The WMS & Pallet Shuttle Integration module simplifies the work of employees who operate the motorised shuttle
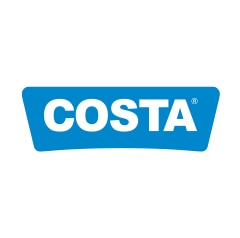
Horchata and vegetable drink manufacturer Costa Concentrados Levantinos S.L. has recently optimised its supply chain with a comprehensive logistics solution from Mecalux: pallet racking, racks with the Pallet Shuttle system and the Easy WMS warehouse management system. As traceability is an indispensable process for this food company, it is crucial for it to be equipped with a warehouse management system such as Easy WMS, which monitors each product in real time. Likewise, specific software has been installed to simplify the tasks of operators working with the Pallet Shuttle system.
Over a century of tradition
Founded in Valencia, Spain, at the end of the 19th century, Horchatas Costa was a company dedicated exclusively to producing horchata, a milky drink made from tiger nuts traditionally consumed on the Iberian Peninsula’s Mediterranean coast and enjoyed in the rest of Spain as well. In 2002, the horchata maker was acquired by Joan Escoda S.A, a business in the food sector that was expanding its product portfolio and breaking into new markets.
Costa then became Costa Concentrados Levantinos S.L. and began its national and international expansion, adding to its horchata production a new, extensive range of vegetable drinks and other food products. The firm stands out for always prioritising the maintenance of the quality of its goods and for applying, as far as possible, the ecological and sustainability values for which it is known.
The firm’s products can be found in specialised shops in the sector and on supermarket shelves under the usual brand, Costa, and under the new organic Amandín brand. The business also sells its goods to third parties as white-label products.
A vast assortment of SKUs
Nowadays, Costa Concentrados Levantinos manufactures a wide variety of vegetable drinks. These are consumed as an alternative to cow’s milk by people with food intolerances and allergies, as part of a healthy diet or for the simple pleasure of enjoying them.
The firm also markets nuts, oats, flour, broths, soups, rice- and oat-based vegetable sauces, and hazelnut creams containing cocoa that serve as a base or complement for the preparation of all kinds of cooking and baking recipes.
As a result of the transformation of its production and logistics processes, the company has steadily expanded its catalogue to adapt to new market needs. Thus, in recent years, Costa Concentrados Levantinos has increased its sales, with its production volume reaching 28 million litres a year.
Revamped logistics systems
In its early days, the company had a warehouse in which it stored the raw materials used day to day, as well as finished products as they left production. However, Jordi Llort, Production Department Manager for Costa and Amandín, points out, “We didn’t have a big enough storage capacity to accommodate all the goods.”
Consequently, the company outsourced its logistics processes and distributed the products among several facilities near the production plant. The 3PL operators had to adjust to the production pace of Costa and Amandín and supply the raw materials at the right time, which wasn’t very practical. Moreover, the fact that this type of product is highly seasonal complicated logistics operations even further during specific months of the year.
Increased demand for organic and healthy products motivated the firm to improve its supply chain. “We were absolutely certain that we didn’t want to depend on external warehouses. Thus, we had to optimise the available storage space by using racks that would boost our capacity and, at the same time, help us to better organise the goods,” explains Jordi Llort.
In 2016, faced with the impossibility of expanding the production lines or its headquarters in the Valencian town of Alcàsser, the company decided to move to a new location: Riudoms, in Spain’s Tarragona region.
The facilities of Costa, Amandín and other Joan Escoda companies sit atop a plot of land measuring 45,000 m2. A modern, 10,000 m2 warehouse is home to the offices; the Management, Quality Control, R&D, Sales and Marketing departments; the production plant; the receiving and dispatch areas, and so on.
Improving goods flows in the warehouses
To equip the facility with the storage system that best met its needs and adapted to its flows, the firm contacted Mecalux because, according to Jordi Llort, “It’s a serious business that’s been on the market for many years and has extensive experience providing storage solutions to all kinds of companies.”
After analysing the required movements, the number of SKUs 150 finished products, approximately and the type of products to be stored, Mecalux proposed two storage solutions:
- Pallet racks. This system offers direct access to each of the 1,830 pallets on 6.5-metre-tall racks. Its versatility makes it ideal for housing palletised products with a wide variety of SKUs. For that reason, indicates Jordi Llort, “These racks store our raw materials and all sorts of auxiliary materials, such as the boxes and cartons we use for packaging.”
- Racks served by the Pallet Shuttle system. Mecalux has installed a 7.3-metre-tall by 28-metre-long racking unit. It is composed of 48 channels, each of which can hold 33 pallets deep, bringing its total capacity to 1,584 pallets. This high-density solution is particularly recommended for facilities managing a large number of pallets per SKU and with intense loading and unloading activity. It has a motorised shuttle that moves inside the storage channels, inserting and removing the goods from their locations in a completely autonomous way. Therefore, these racks have been designated to house finished products.
With these two solutions, the company has optimised its warehouse space to be able to accommodate all the goods. Jordi Llort says, “Having two different storage solutions allows us to ensure that our numerous goods are properly organised, in terms of both height and depth, and identified at all times. Our warehouse is now much more orderly.”
Besides the storage systems, the company has implemented the Easy WMS warehouse management system from Mecalux to strictly monitor its goods. “As we manage foodstuffs, it’s imperative that we maintain full control of traceability,” asserts the Production Department Manager for Costa and Amandín. With this WMS, the company takes inventory in real time, so it always knows what stock it has and where it is located.
It has also implemented the WMS & Pallet Shuttle Integration module, an extension of Easy WMS that adds the necessary functionalities to this program for it to supervise the Pallet Shuttle system’s operations. The workers send instructions to the motorised shuttles by means of a tablet on which the software is installed. “It’s really intuitive,” remarks Jordi Llort.
Traceability and food safety
Traceability consists of monitoring the production, processing and distribution of a good, from the procurement of raw materials for its manufacture through to its distribution and shipment to the end consumer. “It’s vital for our business, since we have to meet the strictest food safety standards,” emphasises Jordi Llort.
Food safety includes all control policies and measures laid down by the public administration to ensure that the food is safe for human health. Thus, Costa Concentrados Levantinos complies with the following standards:
- International Food Standard (IFS). Promoted by the German, French, and Italian Researchers Associations, it impacts and is recognised by most of the European Union.
- British Retail Consortium Global Standards (BRCGS). Created by the British Retail Consortium, it has become a benchmark for suppliers of brand-name and white-label products in supermarkets.
- Food Safety Modernization Act (FSMA). Implemented by the by US Food & Drug Administration (FDA), this standard concentrates on the prevention of food safety issues along the food chain for businesses in the sector that export their products to the US.
Monitoring each process that the products undergo ensures that errors are reduced and hygiene standards are met. Moreover, the product design, production and distribution stages fully comply with their corresponding specific legislation.
In logistics nowadays, it is increasingly imperative to rely on tools that record information quickly and accurately. Easy WMS is a computer system that can be used to rigorously monitor the products that enter, remain in and leave the warehouse. This WMS knows all the product details: size, batch, weight, characteristics, production and expiry dates, inspection controls passed, etc.
Optimised, controlled supply chain
Every day, the warehouse receives around 125 pallets sent by suppliers and containing the raw and auxiliary materials used to
make the company’s various products. First and foremost, these items must pass the relevant quality controls. Jordi Llort confirms, “This is mandatory; we don’t store anything that we haven’t inspected for quality.”
Next, Easy WMS assigns a location to each item, taking into account its SKU type and turnover. These products are primarily placed on the pallet racks, although if necessary, they could be sent directly to the production lines.
When the facility receives the finished products from the production lines (approximately 150 pallets a day), their quality is inspected, and, with the help of radiofrequency scanners, operators read the barcode of each item. This way, Easy WMS registers them in the warehouse and assigns them a location.
These goods are deposited on the racks of the Pallet Shuttle system. “The advantage of this solution is that we can store a large number of products in a small space,” notes Jordi Llort. The operators place each pallet at the channel entry point, and the motorised shuttle automatically moves it to the first free location.
The goods are inserted on one side of the racking and removed on the other. Thus, they are stored according to the FIFO (first in, first out) method, ensuring that the company distributes products with an earlier expiry date before others.
Every day, 300 pallets are distributed and sent to establishments that sell the various finished products. Following instructions from Easy WMS, operators remove the pallets from their locations and bring them to the lorries waiting at the loading docks.
Integration of the WMS and Pallet Shuttle
Costa Concentrados Levantinos has also installed a specific Easy WMS module for controlling the Pallet Shuttle. This program enables operators to manage the movements of the motorised shuttles by means of a Wi-Fi-connected tablet with a very intuitive interface. Likewise, they can execute numerous other functions, such as:
- Select the number of pallets to be inserted and removed from the storage channel on a continuous basis.
- Choose the side of the shelves on which they will work.
- Activate the additional locking system to better secure the shuttle to the forks of the forklift.
- Group the pallets in a compact way at the beginning or end of the channel.
- Count the number of pallets stored in each channel.
- Establish user permissions for the shuttles for authorised personnel.
With the WMS & Pallet Shuttle Integration module, the company has streamlined and sped up the tasks of the operators charged with operating the motorised shuttles. “This storage system has not only maximised space — all our pallets are stored together, one behind the other — but also enhanced the work of the operators,” enthuses Jordi Llort.
Always at the vanguard
Since it was founded, the business has relied on innovation and progress to achieve the goals of quality, ecology and sustainability that it pursues in all its production processes. With its new warehouse, Costa Concentrados Levantinos S.L. has leveraged all its resources in order to provide better service, ensure the continuous supply of its production lines and efficiently distribute its finished products.
“We’re realistic, and we understand that the current public health situation is complicated; but we’re really excited and optimistic at the same time. We know that we’ll overcome the difficulties of the pandemic, thanks to our strength and our desire to invest in improvements, as seen with this new, fully optimised supply chain,” acknowledges Jordi Llort.
Aided by Easy WMS, the firm can monitor all its products in real time and, simultaneously, boost the work of its operators and the productivity of its facility.
We’ve boosted our logistics processes. With the Pallet Shuttle system, we’ve made the most of our warehouse. We can accommodate a large number of products in a small space and in a very orderly way. Meanwhile, the Easy WMS warehouse management system from Mecalux allows us to control the goods with full traceability. This was fundamental for our business, as we have to meet stringent safety controls.
Advantages for Costa Concentrados Levantinos
- Surface area optimisation: the company leverages all the warehouse space, thanks to pallet racking and racks with the Pallet Shuttle system that house 3,414 pallets in total without having to resort to external facilities.
- Increased traceability: Easy WMS monitors the goods throughout the various phases they go through, from the receipt of the raw materials through to the dispatch of the finished products.
- FIFO management: the products are inserted on one end of the racks and then removed from the other side, in line with the FIFO (first in, first out) method.
Pallet racks | |
---|---|
Storage capacity: | 1,830 pallets |
Pallet sizes: | 800 x 1,200 mm |
Max. pallet weight: | 850 kg |
Racking height: | 6.5 m |
Racking length: | 14 m and 17 m |
Gallery
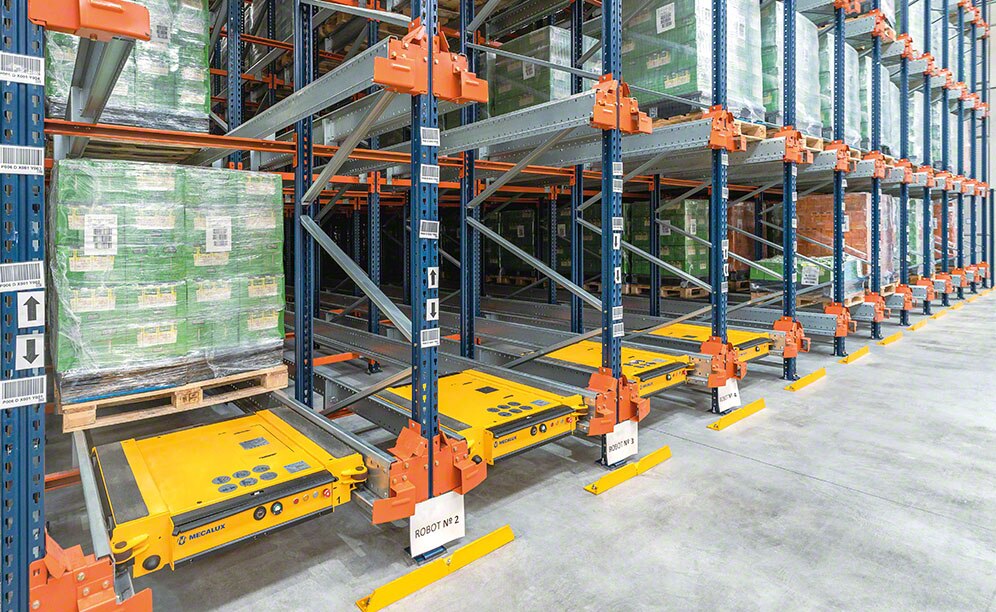
Costa warehouse with vegetable drinks and horchata
Ask an expert