
E-commerce fashion retailer Gibon digitises its warehouse in Slovenia
Online shop Gibon installs Mecalux's Easy WMS in its warehouse to speed up the preparation of up to 6,000 orders a day
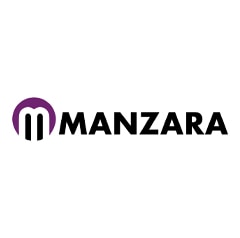
E-commerce fashion retailer Gibon, known for its online shops Manzara and Elegrina, has digitised its warehouse in Slovenia with Easy WMS from Mecalux. This software accurately monitors the company's 1,500 SKUs in real time and has optimised storage and order fulfillment tasks.
Gibon: outfits for every day of the week
Based in Ljubljana, Slovenia, Gibon is an e-commerce fashion retailer with a presence in 20 European countries. In its online shop — Manzara or Elegrina, depending on the country — customers can access its extensive product catalogue of around 10,000 SKUs. These include lingerie, shirts, swimwear, handbags, shoes, shirts, trousers and jackets.
- Founded in: 2015
- No. of employees: 35
- International presence: Belgium, Czechia, Croatia, Slovakia, Spain, Hungary, Italy, Lithuania, Poland, Portugal and Romania, among other countries.
CHALLENGES
|
SOLUTION
|
BENEFITS
|
---|
“We’ve implemented Easy WMS warehouse management software in our facility to optimise operations,” says Gregor Rančnik, CEO of online shop Gibon, an e-commerce fashion retailer with a complex supply chain and demanding operations. In its 1,500 m² warehouse in Ljubljana (Slovenia), the company manages 10,000 different SKUs and prepares some 3,000 orders per day — a figure that can rise to 6,000 during its busy season — which are distributed to customers throughout Europe.
In recent years, the online shop has taken off. “Between 2020 and 2021, we grew by 80%, and in 2022, we hope to increase our turnover by 50%. To make this happen, we’ve expanded our product offering and launched a powerful advertising campaign,” says Rančnik.
The business’s future prospects are promising: it has set itself the target of shipping up to 10,000 daily orders. To drive its growth, Gibon knows that it needs to have effective logistics operations to ensure the distribution of its goods in the shortest time possible.
Manual logistics processes
In the past, all goods management and organisation of Gibon’s warehouse operations were done manually. In the company’s Pantheon ERP system, operators would enter the items received and the orders dispatched.
Gibon was aware that this way of working could be improved, especially order preparation. Picking is a key process in this warehouse, as it consumes 85% of working hours. Every morning, the company would print the delivery notes with the orders placed by customers and distribute them to the warehouse staff. The employees would then travel around the warehouse, preparing orders one by one.
“The operators had a lot of trouble finding the products. Our warehouse is divided into three floors, and it was possible for items in a single order to be located on different levels. As a result, the workers travelled long distances to complete a single order,” says Rančnik.
The intense work pace and the number of orders and SKUs in the facility made it clear that manual management was ineffective. “It entailed a high risk of errors, and operations were slow and inefficient,” says Rančnik.
Gibon came to the conclusion that it had to improve its logistics processes and sought the cooperation of technology company Špica. “We wanted to install a software program that would help us optimise operations in our warehouse. The team of experts from Špica supply chain technology solutions proposed a system capable of meeting our logistics needs,” says Rančnik.
Digital logistics
After analysing Gibon’s operations, Špica selected Mecalux’s Easy WMS warehouse management system. This advanced program would control this e-commerce retailer’s logistics processes and boost the productivity of operations in its facility.
Thanks to digitised management, delivery notes are no longer printed out in the Gibon warehouse. Using RF scanners, operators follow instructions from Easy WMS in real time: the software tells them exactly where to find each item and what quantity to remove. This has reduced operator movements and sped up shipments of goods to customers.
“Easy WMS has improved the way we work, particularly because it assigns specific tasks to each operator and can control their execution. One of the difficulties we encountered when the number of orders began to rise was hiring new employees; that is, they needed time to learn how to perform tasks in the warehouse. With the Mecalux software that Špica recommended to us, new operators can work in the facility from day one, so they’re much more productive than before. The throughput of the rest of the staff has also increased dramatically — by nearly 30% — thanks to a more accurate distribution of the goods and traceability of operations. And we expect productivity to go up even more in the future, after the operators have mastered the system and know how to better leverage it,” says Rančnik.
With Easy WMS, Gibon has optimised its warehouse operations, from goods receipt to order fulfilment and dispatch.
Goods receipt
“Every month, we receive two sea containers in addition to 100 kg of items a day sent from China by suppliers,” says Rančnik.
The receiving process is crucial in any logistics facility, as it affects all other operations. In the Gibon warehouse, efficient organisation of the goods received makes for much more streamlined order preparation.
Digitisation has expedited the goods receipt process. Operators no longer have to note the products that arrive at the loading docks one by one. Now, they simply scan the barcodes with their RF scanners to automatically enter them in the Easy WMS database.
E-commerce has led to a spike in returns, so Gibon also required efficient management of reverse logistics. Nearly 20% of items received every day are customer returns. For these cases, upon reading the barcodes, Easy WMS tells the operators what to do with the merchandise. In line with Gibon’s returns policy, if the items are in good condition, they can be stored again.
Storage and inventory control
Easy WMS applies rules and parametrisable algorithms to assign each item a location taking into account its characteristics and turnover. “Products are stored by category. For example, best sellers are usually located in accessible positions to make it easy to slot and remove them,” says Rančnik.
Once all the products are identified, Easy WMS designs a route that optimises the paths that the operators will follow to replenish the shelves.
Another improvement seen in the Gibon warehouse is in inventory control. With seasonal changes, this e-commerce retailer found it very difficult to rigorously monitor its products. With Easy WMS, on the other hand, inventory is perpetual: the number of goods the company has is updated in real time, enabling strict stock control.
Order picking
“With Easy WMS, we can cope with the increased number of orders we’ve seen in recent years. Operators learn to use the management software in record time. The system is so intuitive that, following its instructions, our workers are much faster and don’t make mistakes,” says Rančnik.
Nowadays, the Gibon warehouse neither prints delivery notes nor distributes them to operators. Instead, Easy WMS organises and distributes the work completely automatically and more efficiently. Operators merely have to consult their RF scanners to know which orders to prepare and where to find the items requested.
Since they began using Easy WMS, operators have gone from preparing orders one at a time to completing up to 32 at once on a single warehouse run.
Moreover, through the efficient organisation of the goods and stock control in real time, operators no longer have to change floors as often as they used to. They can carry out picking on one floor and complete the 32 orders in as little time as possible. This new working method has enabled Gibon to prepare up to 6,000 orders a day during peak periods.
Order consolidation and distribution
The consolidation area is made up of eight workstations, where operators bring their 32 finished orders. The workers at these stations verify that the orders contain the correct items.
They then package the goods, label them and sort the orders by delivery agency. Easy WMS has made it much easier to create and print the necessary documentation for carriers with the aim of eliminating errors. The documents include the shipping information and the package contents, which are essential for carriers to be able to do their work more efficiently.
Lastly, the software manages the grouping and classification of packed and labelled orders by delivery agency. Organisation of this process is vital for Gibon, which works with a multitude of distribution agencies to dispatch goods to the thousands of customers that purchase its products in 20 European countries.
Optimised warehouse
E-commerce fashion retailer Gibon has made the jump to digital logistics, substantially improving its processes and controlling the traceability of its 10,000 SKUs. With the Mecalux software, the entire warehouse is in order, and operators are more agile and productive, preparing up to 6,000 orders a day.
Easy WMS is a scalable, flexible software program that can be adapted to Gibon’s changing needs. This WMS allows the company to leverage all its warehouse resources to efficiently prepare and distribute a growing number of orders.
Easy WMS has completely overhauled our way of working. The software assigns and distributes tasks to operators much more efficiently. We’re really happy because it’s a very intuitive, user-friendly system. Our operators have improved their throughput and have learned how to use it in no time.
Ask an expert