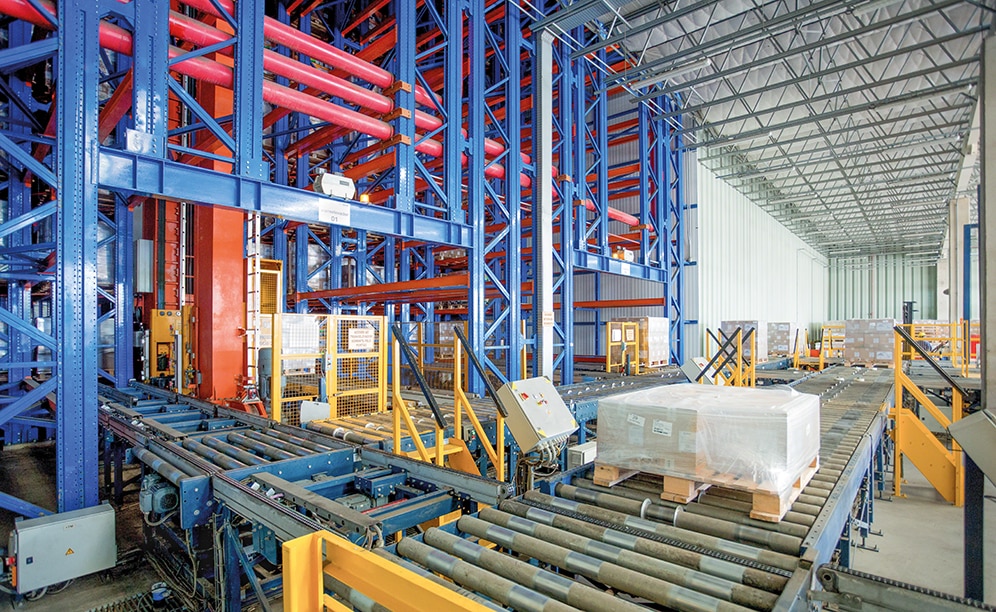
The international chemical powerhouse consolidates its presence in Brazil with an automated clad-rack
BASF chooses automation to reinforce its leadership in South America
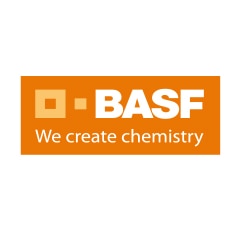
The BASF automated clad-rack warehouse in Guaratinguetá-SP (Brazil), in operation since 2011, has a storage capacity of more than 8,160 pallets. It is made up of two double-deep aisles served by twin-mast stack cranes and a conveyor circuit, in addition to the picking area at the front of the warehouse. All operations are controlled and directed via the Mecalux Easy WMS warehouse management system.
Needs of BASF in Brazil
BASF is a company with a long history in the manufacture and distribution of industrial chemical products and with a solid presence worldwide. It has always been committed to innovation, sustainability and the quest for the best solutions designed to satisfy current and future needs of society.
In order to adapt to the market demands in the last few years, the company required a warehouse with sufficient capacity to deal these needs.
Mecalux took the reins from the beginning of the project, which fortified BASF’s position in South America.
The BASF automated warehouse
Mecalux designed and constructed a 1,400 m2 automated clad-rack warehouse that measures 30 m high and 101 m long. It consists of two aisles with double-deep racking on both sides, which have a capacity for more than 8,160 pallets without losing direct access to the merchandise.
Each aisle is served by a twin-mast stacker crane that picks up pallets from incoming conveyors and deposits them in the location that has been assigned by the Mecalux Easy WMS warehouse management system. Later, they perform the same movement but in reverse for outgoing goods.
Since it is a large-scale clad-rack installation enabled to store chemical products, safety has been of the utmost importance. Emergency exits have been set up at strategic points. In the event of an incident, the automatic equipment stops, facilitating the evacuation of the operators.
Incoming and outgoing goods
The operations in the warehouse stand out because of their simplicity: the receipt and dispatch of goods is carried out automatically at the front of the warehouse via a conveyor circuit with rollers and chains that controls the pallets at all times. This system allows goods to be moved independently, without the need for human intervention, and prevents logistical errors. Both processes are separated to avoid interference.
Before entering the automated warehouse, goods must pass through the checkpoint to validate that they fulfil the requirements established for their location in the warehouse. Pallets that do not pass inspection are deposited on the rejects conveyor, placed in parallel, for their reconditioning.
The picking area
At the front of the conveyor system two picking stations were also placed. The operators prepare orders with agility thanks to vacuum lifters that raise and move the heaviest goods.
Just behind the work stations, there are two lines of bidirectional conveyors. These are assigned to provide the empty pallets needed for operations and the dispatch of completed orders.
Warehouse management software
The Easy WMS by Mecalux is a powerful warehouse management system whose purpose is to coordinate and manage all internal operations. The functions it performs include reception, the allocation of locations and storage of pallets based on turnover, extraction, order preparation and final dispatch.
Being a completely automated warehouse, the Galileo control module was installed that takes charge of giving movement commands to the different devices that the installation is composed of, as well as controlling the safety measures.
Easy WMS by Mecalux is in permanent and bidirectional communication with the ERP of BASF, transferring data and information to itself to operate and manage the warehouse effectively and to obtain maximum profitability from the logistics processes.
Advantages for BASF
- Large capacity: BASF’s new clad-rack warehouse has a capacity to locate more than 8,160 pallets of different sizes and characteristics in 1,400 m2.
- Maximum agility: operations are very simple, lithe and completely automated, minimising human intervention.
- Optimal management: the warehouse is controlled by the Mecalux warehouse management system the Easy WMS in order to optimise all the movements and operational processes that take place.
BASF automated clad-rack warehouse | |
---|---|
Storage capacity:: | 8,160 pallets |
No. of stacker cranes:: | 2 |
Type of stacker crane:: | twin-mast |
Type of fork:: | double depth |
Warehouse height:: | 30 m |
Warehouse type:: | clad-rack |
Gallery
Ask an expert