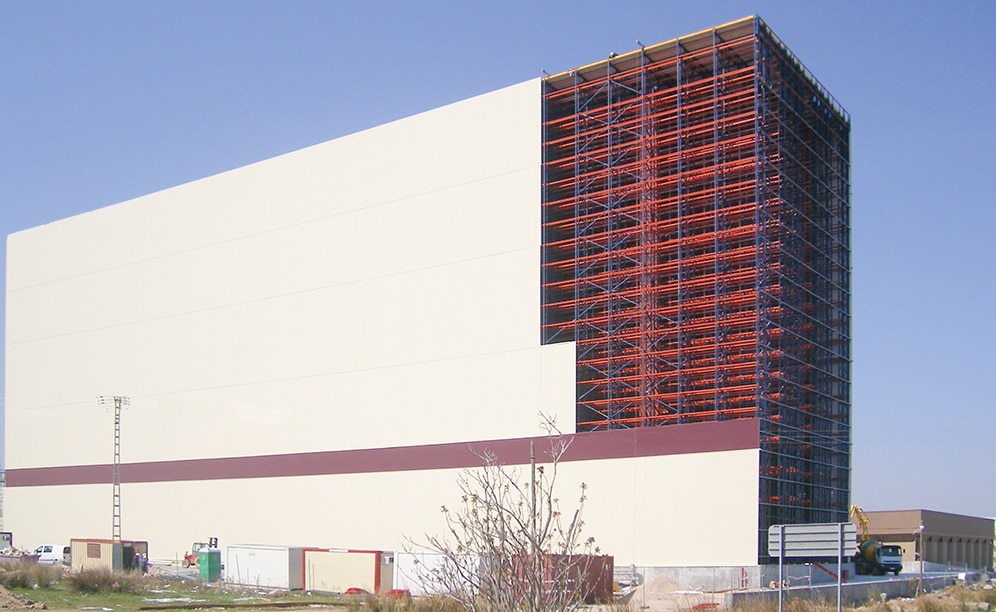
Delaviuda achieves a capacity for 22,000 pallets in 2,209 m2 in a new 42 m high automated warehouse
Delaviuda operates the tallest automated warehouse in Spain
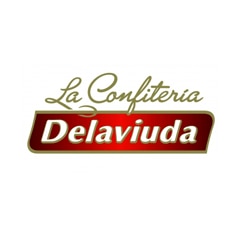
Towering at 42 metres high, this logistics centre built by Mecalux in the municipality of Sonseca (Toledo) has allowed Delaviuda to achieve a storage capacity of more than 22,000 pallets in 2,290 m2. The totally automated warehouse is set up to double its capacity when Delaviuda grows and requires more workspace. The provision included the Mecalux Easy WMS warehouse management system for the purpose of managing all operations in the logistics centre.
Who is Delaviuda?
Delaviuda is one of the most renowned Spanish companies in the manufacture of almond nougat and other snacks, offering up to 150 different products in more than 70 countries. Their workforce consists of more than 700 workers.
Delaviuda is made up of three companies, boasting almost 100 years of experience: Delaviuda Alimentación SA, Almendralia Ibérica, SLU and Artenay Bars SAS. Each one of them has specialised in a particular activity, such as the preparation of marzipan or nougats, the cultivation and harvesting of almond trees and the production of snack bars, respectively.
Food for thought
Throughout the last decade, Delaviuda has experienced enormous growth that has brought it to improve its facilities’ storage capacity and the agility of order preparation.
In order to solve this necessity, Delaviuda considered the construction of a warehouse to centralise all the company’s logistics operations, which was also capable of storing more than 20,000 pallets. In addition, and due to the fact that the vast majority of dispatches are not whole pallets, the installation needed an area set up for order preparation.
Delaviuda entrusted Mecalux to carry out this important project, which automated storage processes from end to end, taking into account possible company growth in a relatively short period of time.
An automated warehouse solution
To fully benefit from a fairly small surface area, the company chose to construct a 42 m high automated warehouse, next to a building with common zone assigned to inputs, outputs and picking.
In order to speed up and improve the flow of goods, a complete conveyor circuit was installed managed thanks to the Easy WMS by Mecalux.
Moreover, the facility is set up to double storage capacity in the future in a very simple way and without interrupting business at Delaviuda.
The new warehouse has brought the company a series of advantages, which include key improvements like the reduction of logistics costs, better service in terms of delivery dates and quantities, agility in order preparation, fewer preparation errors, stock minimisation and savings on electricity. The warehouse is composed of:
- Main automated warehouse
- Conveyor circuit
- Picking warehouse
- Raw material warehouse
- Packaging warehouse
- Reception, dispatch and preloads
Automated warehouse: features
It consists of three storage aisles with double-deep pallet racks placed on both sides. A stacker crane circulates in each aisle, which performs the pallet movements from the front of the warehouse to the assigned location.
The pallet racks are 21 load levels high, four set up for 1.9 m high pallets and the rest for 1.35 m high pallets. Every level houses three pallets deep, each a maximum of 2,100 kg.
Being such a high building, the cross-sectional horizontal forces, mainly those of the wind, are absorbed by a reduced number of uprights. This fact made a specialised manufacture imperative so uprights are capable of standing up against not only the wind, but the weight of pallets, of the racks themselves, of the snow and the forces that stacker cranes transmit.
The stacker cranes, which are double-mast in composition, must also support dynamic loads handled in extreme situations, as indicated in the corresponding standards.
Cooling tubes were placed in the upper part of the racks, without taking up space and allowing correct air circulation throughout the building. Their purpose is to maintain a certain temperature and prevent goods from deteriorating.
The fire safety system tubes and sprinklers were installed between the racks. Their placement coincides with the beams to avoid loss of storage space and to enable correct spraying of the pallets in case of a fire.
The two main warehouse conveyors, located at the opposite end to the docking and picking area, are within a low annexed building that connects with the central warehouse.
Inbound goods
A part of the goods that enter from outside the warehouse is assigned to the raw material warehouse. Reception takes place via a conveyor circuit that includes a checkpoint, and a lift that bridges the unevenness between the two areas.
Pallets going to the main warehouse enter by means of a circuit that runs along the side and the rear part of the central building, ending up at the front of the main warehouse. The extra-long circuit offers the possibility of having a large number of accumulating pallets, allowing operations to continue if an incidence in the system took place. Its length was necessary due to the distribution of the zones and the operations they perform.
The entry and start points of both conveyor circuits coincide in the same zone. Additional elements have been arranged that assure the optimal operation of the installation, within the circuit assigned to warehouse entries. For example, a stretch wrapping machine, a labeller, an entry control, the automatic checkpoint and the rejects station.
Outbound goods
Outputs that come from the main warehouse can go directly to dispatches (docks) or to the picking warehouse. The entire output circuit that crosses the rear part of the central building is ‘U’ shaped.
Three single exits from the picking warehouse have been set up and two with pallet accumulation assigned to dispatches. These final conveyors are adapted to handle pallets both on the narrow side and the wider side.
Docking zone
The area, located in front of the picking warehouse and the wrapping area for prepared orders, has seven completely equipped docks in order to avoid abrupt temperature changes and airflow between the outside and the central warehouse.
Orders accumulate in preloads and are placed on the floor, piled up on top of each other to fully load the transport vehicle. Operators, using electric pallet trucks, are responsible for loading the trucks.
Picking functions
Picking of medium and high turnover products is done on lower pallet rack levels, whereas low turnover products are on the second level. Reserve palletised goods have been placed on upper levels.
The operator who carries out picking uses an electric pallet truck with a lift (stackers) that allows him to raise the pallet to an ergonomic height. This handling equipment also offers the possibility of moving pallets from upper levels and stacking shorter, already palletised prepared orders.
Prepared orders in the picking warehouse must go through the stretch wrapping machine before being transferred to preloads.
Raw material warehouse
This consists of cold storage where products are basically stored in bulk, the majority in ‘big bags’, which are also placed on pallets. A pallet racking storage system is used with direct access to any pallet. This system is ideal to maintain proper product turnover with the assistance of the Easy WMS warehouse management system by Mecalux.
The goods arrive to this warehouse via an automatic conveyor circuit consisting of conveyors with rollers and chains. Next to this warehouse there is an area assigned to packaging and labelling, separated by a wall because it does not need to be cooled.
Easy WMS
The warehouse management system by Mecalux controls all the operations pertinent to the different warehouses that compose this logistics centre. Key functions include:
- Reception of goods.
- Labelling.
- Location in the different warehouses according to the product and the previously programmed parameters.
- Management of the warehouse layouts and real-time stock control.
- Control of outputs, assigned to either production, picking and dispatches, maintaining the parametrised criteria.
- Management of all the processes related to picking.
- Preparation of customer delivery routes.
- Generating reports.
All actions conducted by operators are managed through the individual computer terminals that form part of the system via RF remote connection. Backed by Mecalux’s Galileo control software, Easy WMS manages all the automatic movements performed by the different handling equipment on-premise using pre-programmed rules and routes. This includes elements such as stacker cranes, conveyors, lifts, stretch wrapping machines, checkpoints, etc.
Easy WMS is permanently connected to the customer’s ERP, interchanging precise information on all processes that take place in the logistics centre.
Fire safety system
The Delaviuda warehouse fulfils local fire protection regulations, thanks to a sophisticated and efficient fire detection and extinction system equipped with smoke detectors and other control devices.
The automatic fire sprinklers are strategically placed inside the racks. Thus, they are protected from possible blows and will correctly spray the pallets when needed.
A high-rise clad-rack warehouse
The key feature of a clad-rack warehouse is that there are no pillars or columns that hold up the building. The structure of the building consists of the racks themselves and the outer cladding that is attached to them.
To calculate the structure of a clad-rack warehouse its weight, the weight of the stored goods, the wind forces ― both the pressure and suction based on the area where it is constructed ―, the weight of snow according to established standards, impacts from stacker cranes and, lastly, the seismic activity corresponding to the territory in which it is located are taken into account.
Advantages for Delaviuda
- High storage capacity: the Delaviuda warehouse houses more than 22,100 pallets in a surface area of 2,290 m².
- Reduced costs: the automation of the warehouse as well as the inbound and outbound goods have allowed Delaviuda to boost efficiency and reduce logistics and personnel costs.
- Increased productivity: the specific design of the warehouse and the automation of the main processes make it possible to prepare orders in the shortest possible time.
- Control of the warehouse: thanks to the Easy WMS warehouse management system, Delaviuda controls everything from the reception, storage and dispatch of SKUs to picking operations.
Almacén autoportante automático de Delaviuda, Toledo | |
---|---|
Capacidad de almacenaje: | 22.152 palets |
Dimensiones del palet: | 800 x 1.200 mm |
Peso máximo por palet: | 700 kg |
Altura del almacén: | 42 m |
Longitud del almacén: | 101 m |
Anchura del almacén: | 22,7 m |
Número de pasillos de almacenaje: | 3 |
Número de transelevadores: | 3 |
Tipo de transelevadores: | monocolumna |
Niveles de carga: | 21 |
Sistema de extracción: | doble profundidad |
Gallery
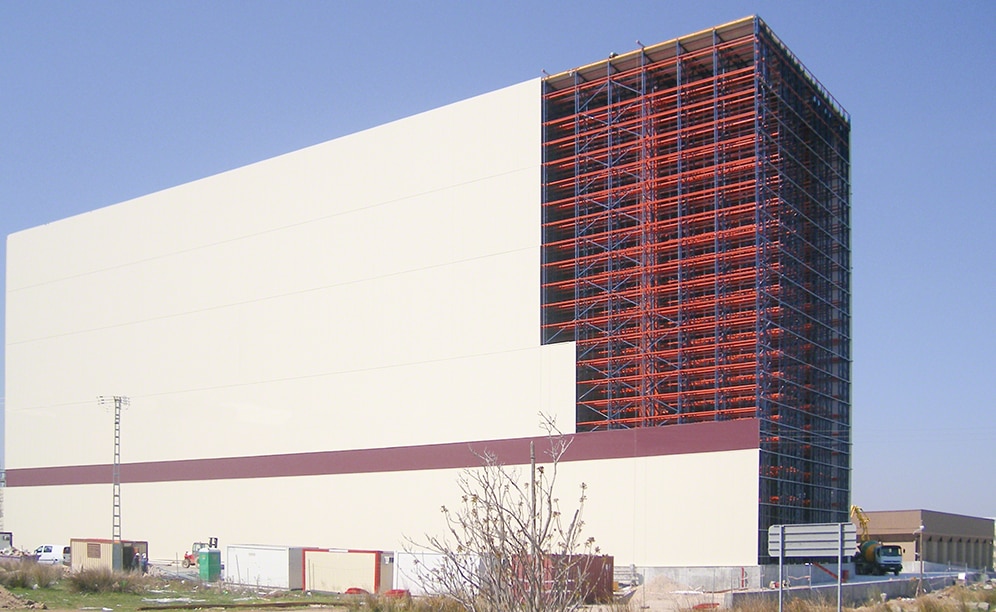
Ask an expert