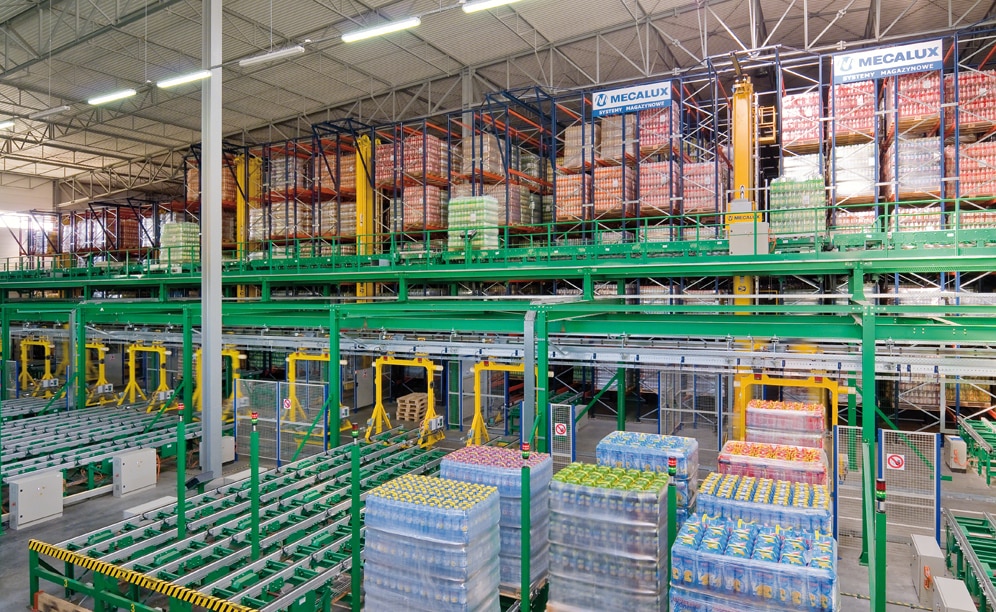
A high profit-automated warehouse for one of the leading manufacturers of beverages in Poland
Integrating processes, capacity and agility for Zbyszko Company
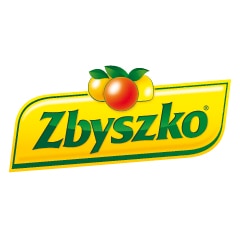
Aiming to keep pace with its growing business, the company Zbyszko wanted to expand the capacity and agility of their warehouse in addition to integrating their production and storage processes. In order to meet this demand, Mecalux built them an automated warehouse connected to the production plant via a 100 m long overpass equipped with conveyors. All this is coordinated and controlled by the warehouse management system Mecalux Easy WMS software
Zbyszko Company and their needs
Zbyszko Company, a company specialized in the production of carbonated drinks, soft drinks and flavoured waters, was created by Zbigniew Bojanowicz in 1993 in the Polish city of Białobrzegi. In just 10 years, the Zbyszko Company has experienced spectacular growth that has made it one of the most successful Polish manufacturers within the natural beverages market.
In the face of its incessant headway, Zbyszko Company has relied on Mecalux to provide it with a new storage centre to centralise all the company’s logistical activities and which is equipped with the newest, most innovative technologies in order to deal with high production rates and save on logistics costs. Present and future growth demand it.
Speeding up internal transport was also a crucial prerequisite of the project, creating a direct connection between the warehouse and the production area. This was done via maximum automation of the storage processes in order to increase Zbyszko Company’s market competitiveness.
Proposed solution: connecting the production area and the warehouse
Mecalux has set up an automated warehouse that connects the production area via a 100 m long overpass through which already palletised goods circulate on a circuit of roller conveyors.
The checkpoint, located at the beginning of the circuit and within the same production area, verifies that the dimensions and the quality of each pallet are appropriate. The conveyors have two lines – one in each direction – working independently despite being placed in parallel.
Inside the warehouse two levels of conveyors are arranged. The upper level is allocated to the input of goods, while the lower level has been reserved for outputs. There is also the possibility that outside goods, destined for the warehouse or the production area, can enter at this level. Not to mix operations, they have set up a conveyor just above the docks for inputs into the warehouse, with a lift placed at the end that raises the pallets to the upper level.
On the ground floor, so that throughput is as high as possible, a circuit of electrified monorails capable of transporting SKUs at more than 100 m/min – and which links the warehouse with the preload area – was installed. This system is ideal for connecting distant points of the installation at a steady pace.
Inside the warehouse
The warehouse occupies a 7,000 m2 surface area and is built in a facility only 11 m high. The installation of stacker cranes makes it possible to warehouse up to 18,000 pallets despite this limited height.
Having few SKUs, they chose to place double-depth racks, a very common method in automated logistics centres that require a large storage capacity. The racks are served by eleven, fully automated stacker cranes, which move quickly along their respective aisles handling pallets weighing up to 1,000 kg each.
Dispatches
The stacker cranes are responsible for automatically extracting stored goods from the production area and bringing them to the corresponding output conveyor. Once on the conveyor, the electrified monorails directed each pallet to their assigned preload area.
There are numerous options for creating an electrified monorail circuit. In Zbyszko Company’s case it was decided that a simple loop circuit, operated by 21 individually controlled shuttles, was the most cost-effective, seamless solution.
The software that controls the machines is connected with the WMS (Warehouse Management Software) throughout the warehouse, and to the customer's ERP.
There are the following areas:
- Warehouse
- Inputs into the upper level
- Electrified monorails
- Preloads area
- Input conveyors from the docks
Warehouse Management System: Mecalux EASY WMS
Zbyszko Company uses the warehouse management system Mecalux Easy WMS to check each and every one of the movements that takes place in the logistics centre, and thus efficiently manage their storage space.
Easy WMS communicates with the customer’s ERP SAP in order to be able to carry out the dispatch, reception, distribution, transfer processes, and other tasks related to the logistics centre.
This powerful system ensures the proper operation of the machines that are used in the automation of the warehouses, which simplifies transportation, eliminates human errors and reduces staffing costs.
Advantages for Zbyszko Company
- Maximum space utilisation: the warehouse, only 11 m high, has an 18,000 pallet storage capacity in a 7,000 m2 surface area.
- Cost savings: the overpass that connects the warehouse to the production area allows Zbyszko to save in logistical costs.
- Increased productivity: order preparation is fast and efficient thanks to the speed of the stacker cranes, the conveyor circuits and the electrified monorails installed, which can issue up to 200 pallets/hour.
Automated warehouse in Poland | |
---|---|
Storage capacity:: | 18,000 pallets |
Maximum weight per pallet:: | 1,000 kg |
Height of the warehouse:: | 11 m |
Warehouse surface area:: | 7,000 m2 |
No. of stacker cranes:: | 11 |
Fork type:: | double-depth |
No. of shuttles on the electrified monorails:: | 21 |
Length of the overpass:: | 100 m |
Gallery
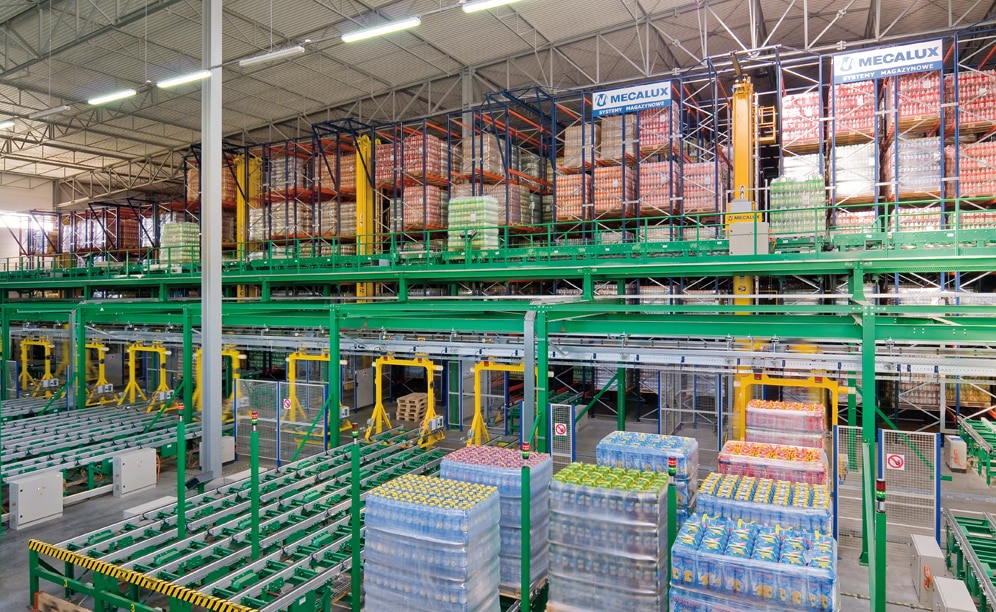
Ask an expert