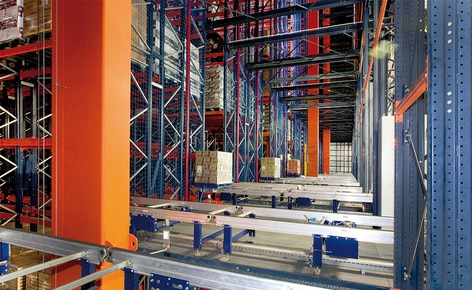
The food company Grupo Siro has increased its capacity and productivity with a 35.5 m high automated clad-rack warehouse
Grupo Siro continues to grow with a large, automated clad-rack warehouse
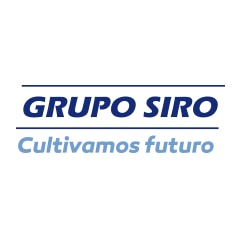
Mecalux has built a fully automated, super-sized clad-rack warehouse for Grupo Siro, one of the largest companies in the food sector in Spain. This innovative logistics centre is part of the Group's commitment to effectual need solving solutions and to new technologies as a source of efficacy and sustainable growth.
About Grupo Siro
Grupo Siro is one of the most prominent manufacturers of biscuits, pasta, bread, pastries and cereals in Spain.
It was established in 1991 with the acquisition of Galletas Siro by Danone. Since then it has always focused on innovation and the use of technology in all its business processes to offer the best quality products at the best price.
Currently, it manufactures over 300 different products and has 13 production centres, a logistics warehouse, a R&D&i centre, a sub-product test centre, two office complexes and the headquarters of the Grupo Siro Foundation.
Needs of the customer
The company has experienced tremendous growth in recent years, especially because of the enormous demand by its primary customer: the Mercadona supermarket chain.
At some point, this growth and the consequent increase in production raised warehouse space needs, usually located within the factories themselves. The company chose initially to rent out external warehouse space to keep pace with production, but that hindered the coordination of its supply chain and increased operating costs.
Resolved to base operations on efficient solutions for their needs and to drive growth, Grupo Siro commissioned Mecalux in the construction of a new logistics centre at its headquarters in Venta de Baños (Palencia) with two very clear premises: improve the storage capacity of its plants and promote high company productivity.
The proposed solution
The technical department of Mecalux, in collaboration with the Siro Group logistics team, analysed the needs, constraints and means in detail, and finally found the ideal solution: building a 36 m high clad-rack warehouse served by stacker cranes and conveyors, all managed by the Mecalux Easy WMS warehouse management system.
The logistics centre is strategically located within a 3 km radius of four of its main factories and less than 100 km away from the other three, which facilitates and speeds up the transport of loads between them all.
The flow of movements is very intense and continuous, so two reception docks are fitted on one side of the warehouse, separated from the nine dispatch docks. This set up avoids interference between the two operations, with ample space allowing a more dynamic movement of the transport manoeuvres and the lorries on standby.
The building annexed to the warehouse consists of two different floors to optimally organise the various operations carried out:
- The lower level is primarily set aside for the receipt and dispatch of the goods, with a wide preloads area on the floor.
- On the top floor, the pallets from the docks at the lower level enter into the warehouse. There is also an area dedicated to picking tasks.
The warehouse
The installation is of a considerable size: 102 m long, 57 m wide and 35.5 m high, the maximum allowed by local regulations. It is distributed into eight aisles with double-deep racking on both sides. Each aisle has 14 load levels of varying heights adapted to the pallet sizes of Grupo Siro: five levels to 1,400 mm high Euro-pallets, eight to 2,000 mm and one to 2,500 mm. Unit loads have an average weight of 800 kg and a maximum of 1,000 kg.
Each aisle is equipped with a twin-mast stacker crane with telescopic forks and an onboard maintenance cabin in the cradle. This machine is responsible for storing each pallet in its proper location depending on its size and turnover.
Warehouse automation is completed with two conveyor circuits: one on the ground floor where the pallets for dispatches are deposited, and another on the top floor, at 6.7 m high, which connects all inputs in addition to the outputs to the picking area.
At the top of the warehouse, they have exploited gaps between the trusses to place the air conditioning ducts that regulate the temperature of the entire installation and properly distribute the air.
Outside the building, at the back, there are four fire safety system pumps and a water tank with sufficient capacity for the warehouse's dimensions. Inside there are sprinklers and fire detectors to prevent any outbreak of fire.
The ground floor
Ground floor distribution:
- Automatic unloading dock
- Standard unloading dock
- Loading docks (9 in total)
- Pallet checkpoint zone and pallet lift
- Pallet outputs from the warehouse
- Preloads on the floor
- Virtual circuit of LGV forklifts
- Accumulation of empty pallets
- Reception and conditioning of incoming pallets
Incoming goods
The entry of goods from different production centres nearby is carried out from the two receiving docks, one of them with automatic lorry unloading and the other manually using forklifts or pallet trucks.
The unloading area has an accumulation capacity of two fully loaded lorries, i.e., a total of 66 pallets that head to the inspection area where the status is validated.
All pallets pass obligatorily through the checkpoint area, where it is verified that they are in good condition and their weight and measurements correspond to the quality requirements in the warehouse. If the pallet is in good shape, the management system gives the order to continue to the pallet lift, which will forward it to the top floor, and then it will enter the automated warehouse.
When the pallet fails inspection, it can be sent to three different areas, depending on the detected anomaly:
- The reconditioning area.
- The compaction area, where shifts or overhangs are corrected that exceed the specified limits.
- The pallet doubler: when the unit loads have an inadequately sized base, they are placed on top of another in good condition by the pallet doubler. These pallets go back to the inspection area and are checked again before entering the upper floor.
The defective pallet that cannot be fixed up will be transported to the inputs area and ejected from the circuit.
The pallets that have been reconditioned go through the checkpoint again to verify that they now meet the warehouse requirements.
It is necessary to ensure that the goods inserted into the automated warehouse are suitable and check that the load does not overflow more than expected.
Warehouse outputs/Dispatches
Laser guided forklifts (LGV) handle pallets leaving the warehouse, picking them up at the exit points of each storage aisle and transporting them to the waiting area allocated in any of the nine loading docks, following a previously programmed virtual circuit.
The forklift defines its path by emitting a laser signal that bounces off deflectors placed at points close to the route. The management system is able to know its exact position and gives the order to go to charging stations when the battery level reaches a set limit. Being a fully automatic connection, human intervention in this process is not necessary.
Only lorry loading is done by operators, who assisted by pallet trucks introduce the goods on the lorry assigned by the warehouse management software according to the order number, the route to take, the customer, etc. The operator confirms each operation and the fulfilment of orders using a RF terminal.
The top floor
Organisation of the top floor:
- Pallet lift
- Internal warehouse circuit
- Input or output conveyors of each aisle
- Transfer car of the picking zone
- Picking stations
- Stretch wrapping and reconditioning zone
- Main input conveyor to the warehouse
Warehouse entrance
The goods from the receiving docks, once they have passed the inspection area, enter the first floor by means of a lift. Then the main conveyor circuit distributes SKUs by input conveyors to different storage aisles. It is a one-way circuit where the pallets leaving the aisles are also moved and head to the picking areas.
Picking area
There are also two picking stations installed side-by-side in which each operator can prepare two orders at once. The area is set up to be expanded in the future if Grupo Siro requires this.
The picking stations are placed above conveyors. On both sides of the operator, there are hydraulic lift tables that adjust to an ergonomic position for handling goods. Thus, the preparation of orders is streamlined.
Each picking station has an accumulation conveyor circuit. In addition, there are pallet stackers and dispensers enabled that supply the area, as well as wait stations for pallets that have left the warehouse and do not have a free space in the circuit of the assigned station.
Once the order is completed, the pallet is incorporated into the conveyor circuit that, after passing through the stretch wrapper, will transfer it back to the warehouse until the management system calls for its dispatch.
The software
The warehouse is managed by the Mecalux Easy WMS software and is in constant communication with the ERP of Grupo Siro, to control, coordinate and report on all logistics processes and operations that are taking place in the warehouse.
The software is designed to be practical and operational, in addition to performing these functions:
- Absolute control over warehouse management.
- Management of incoming and outgoing goods from the loading and unloading docks.
- Strategic placement of unit loads in the warehouse according to the management of aisles and its locations.
- Real-time registration and stock adjustment.
- The design of the order of outgoing goods and their subsequent loading onto the lorry through a RF terminal.
- Optimisation of tasks according to the picking route.
- Direct communication with the logistics provider of Grupo Siro.
- Coordination of all master data (items, owners, suppliers, customers, etc.).
Advantages for Grupo Siro
- Operational cost savings: the elimination of external storage and the centralisation of operations in the same logistics centre results in an increase in productivity and a rapid return on investment.
- Maximum capacity: the high-rise warehouse and the use of stacker cranes have multiplied the storage capacity of Grupo Siro, adapting to the growth of production.
- Fully automated management: Grupo Siro has integrated and coordinated its operations of reception, storage, picking and dispatch of goods into one space. These tasks are under the management and control of the Easy WMS, optimising the performance of its entire logistics chain.
- Increased safety: automated warehouses offer maximum protection for operators and goods, thereby contributing to the company's goal of promoting efficient processes to ensure the safety of personnel at all times.
Automated clad-rack warehouse for Grupo Siro, Spain | |
---|---|
Total capacity: | 40,320 pallets |
Pallet sizes: | 800 x 1,200 x 1,400/2,000/2,500 mm |
Max. pallet weight: | 1,000 kg |
No. of racks: | 16 double-depth |
No. of aisles: | 8 |
No. of stacker cranes: | 8 |
No. of load levels: | 14 |
Warehouse length: | 101 m |
Warehouse width: | 57 m |
Warehouse height: | 33.,5 m |
Gallery
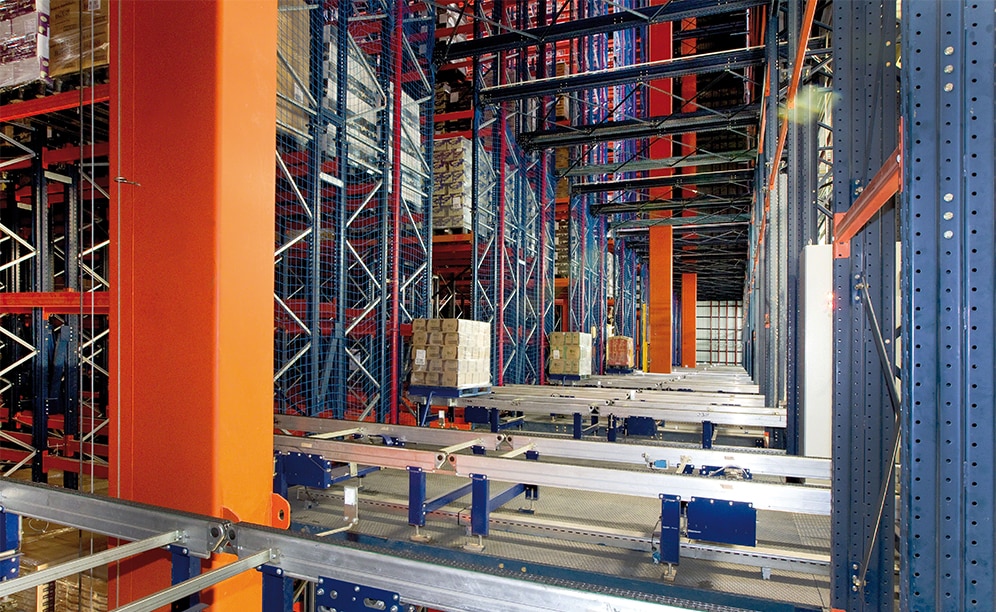
Mecalux has built a fully automated, super-sized clad-rack warehouse for Grupo Siro
Ask an expert