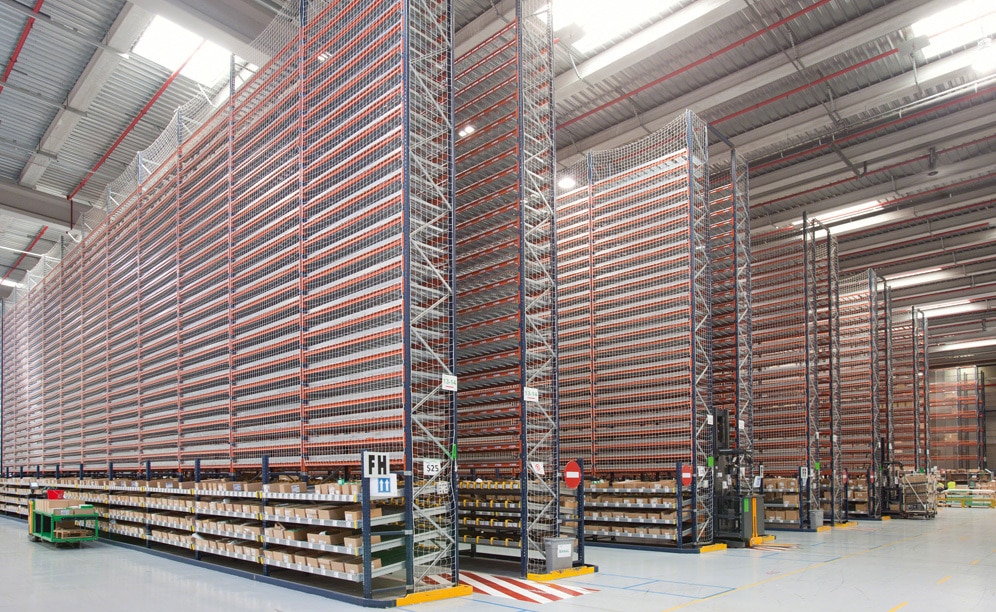
How to achieve the ideal balance between speedy picking and storage capacity
Schneider Electric increases logistical efficiency by combining systems for pallets and boxes
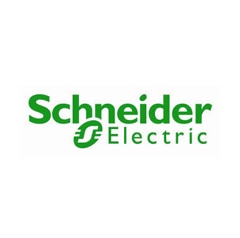
Mecalux has equipped the new logistics centre of Schneider Electric in Sant Boi de Llobregat (Barcelona) based on the objectives of the company: to achieve great agility in order preparation, as well as adapt storage systems to its wide variety of products and depending on the market segment to which they are intended.
A world leader in the electric sector
Founded in 1836, Schneider Electric has become a global benchmark in technologies and power management solutions, offering technological resources that allow safe, reliable, efficient and sustainable electricity processing. With a long history in Spain, the company has always relied on the collaboration of Mecalux to find the best storage systems for its products.
Needs of Schneider Electric
Schneider Electric required an expansion of its warehouse in order to locate the great variety of products that it offers, from small components to industrial sized add-ons. The consumption of its goods is irregular and follows the Pareto principle, or 80/20 rule, i.e. 20% of SKUs generate 80% of sales. In addition, 80% of all items are small in size and mainly picking operations are carried out in the warehouse. This means that a significant percentage of orders typically have little volume and are only occasionally supplied in full pallets.
The experience of the technical and logistical teams at Schneider Electric with the different solutions applied in its other warehouses inclined the company to install conventional storage systems for pallets and boxes, combined with advanced computer equipment and systems for their optimal management.
Solution proposed by Mecalux
With all these factors to be taken into account, Mecalux implemented different storage systems in a 22,000 m2 space adapted to suit the needs of Schneider Electric.
The warehouse is divided into two different sectors, each with their own loading and unloading docks. This is for safety reasons, but also for facilitating the separation of products according to their size and their pre-assigned market segment. In the vast majority of cases, the boxes that contain the products, in particular small sized ones, are stored directly on racks and not on pallets.
The solutions adopted to meet the requirements of the company favour speedy order prep versus storage capacity:
- Picking from live pallet racking levels for boxes using high and low-level order pickers.
- Picking from mesh shelves using high-level order pickers.
- Picking from live racking levels of pallets, combining trilateral and low-level order pickers.
- Picking from conventional pallet racks, with the use of trilateral and low-level order pickers.
- Picking from pallets and shelves using reach trucks and low-level order pickers.
- Storage of bulky items in conventional pallet racks using reach trucks.
- Storage of large sized profiles on cantilever racks with the help of reach trucks.
- Packaging and consolidation in a wide-span mezzanine.
Consumer goods
Schneider Electric needed an optimal solution for small sized products with the highest consumption (type A and B). That is why they installed racking with live channels on lower levels; where picking tasks are directly perform. Upper levels are allocated for the deposit of reserve boxes.
They have prepared working aisles with sufficient breadth to allow different operators to work at the same time with great agility, while avoiding interferences. They prepare orders and group them into waves with the help of RF terminals, which facilitate the labelling and classification of products.
These racks are supplied from narrow aisles where high-level order pickers circulate, which are used to replenish reserve boxes and house them at higher levels. This solution provides the following benefits:
- There are always products available. In the channels, several boxes in depth of a same SKU accumulate and move forward as items in front are removed.
- Allows a great diversity of SKUs, since each channel can store a different item.
- There is no interference between picking and replenishing work, since the tasks are carried out in different aisles.
- Enables maximum use at heights.
- Higher performance of operators thanks to ergonomic workstations, which facilitates product handling.
Lower demand products
Boxes with lower demand, small sized SKUs are placed on very high racks. Aisles are narrow and order pickers are used at heights as well as shuttles with multi-order locations, thereby achieving good accessibility and high capacity.
These machines also serve to replenish products, but in a different time slot. In order to facilitate this process, there is a parking space for shuttles with replenish products prepared for pick up.
This storage system is complementary for small sized, A and B type products mentioned above, since in both cases the same type of products is prepared but with a different turnover.
To finish the process, orders prepared in both areas are consolidated on a mezzanine located in an area next to the docks that uses roller and belt conveyors.
Palletised SKUs
Larger items are deposited on pallets as transport and storage units, with dimensions that may vary depending on the volume of products. Pallets are 1,200 x 800 mm and 600 x 800 mm in size. In this area, a different mixture of pallet racks has been installed.
Medium-dimensioned and higher consumption products are stored in single access racks, with levels formed by perforated shelves housing different sized pallets. In this zone, trilateral lift machines are used to perform replenishment tasks, so aisles are narrower. These aisles do not interfere with the wider aisles where picking with low-level order pickers is done.
Picking tasks take place on the lower rack levels. An operator places the pallets with reserve products in the top shelf using a trilateral machine. Subsequently, it replaces product at lower levels, lowering the corresponding pallet from its location.
Bulky items
The other products on pallets are stored in conventional pallet racks supplied by reach trucks. The location criterion of the different pallets is based on the SKU size. In these racks, 1,200 x 800 mm or greater capacity pallets can be deposited, having one, two or three pallets per space according to its size. Order preparation is carried out in the same aisles where the forklift circulates.
Large and long products are placed on cantilever racks and handled by the same type of forklift.
The mezzanine floor as a consolidation area
The solution chosen for the preparation and consolidation area of small sized orders is a wide-span mezzanine with hot-rolled structural profiles. This system has brought Schneider certain advantages:
- Ample and diaphanous spaces obtained below, being that the structure requires fewer columns.
- Using fire-resistant intumescent paint to protect the structure, which is not possible with cold-rolled profiles.
- Simplified dismantling and transformation of the system.
The decking of the mezzanine floor is treated wood, finished in white melamine on the bottom and a textured, scratch-resistant, dark grey melamine on the top. It is a non-slip finish, and withstands the passage of carts and pallet trucks, holding up against long-term mechanical wear and tear.
The forklifts handle the pallets from the ground floor. On one side of the mezzanine floor’s top level, there are two doors or an up-and-over gate for the safety of operators.
Consolidation and dispatch areas
In this warehouse, they prepare orders by areas depending on the type of SKUs. Therefore, it was necessary to set up all the required packing and labelling equipment in each specific zone for consolidation. There are three distinct areas:
- Bulky profiles and items are consolidated in the spaces close to the loading docks.
- Medium-sized products are placed in a large area on the ground floor.
- For small sized SKUs – because they involve the bulk of the most important orders – there is a reserve space close to the mezzanine and the two levels that compose it.
Given its importance, this last consolidation area was organised around the following elements:
- Provisional parking spaces for carts with already prepared orders.
- Belt conveyors to move boxes between the two levels of the mezzanine floor.
- Automatic classifiers for orders in a consolidation phase.
- Conveyors and classifiers for completed orders.
- Consolidation worktables.
- Strapping machines and auxiliary equipment for packaging goods.
- Computer equipment for monitoring, identification and printing labels and packing lists.
At the top of the mezzanine floor, orders are prepared in shipping crates. Thus, the lower part is devoted to pallet preparation according to a route classification criterion. Subsequently, orders are moved to preload areas, which coincide with the assigned docks.
Advantages for Schneider Electric
- Maximising storage: the new Schneider Electric 22,000 m2 warehouse is equipped with different storage systems that are ideally suited to its wide variety of products, with very different dimensions.
- Flexible order prep system: the most suitable system to prepare orders was installed, depending on the size of the products and the market segment to which they are directed.
- High productivity: the combination of picking functions at lower rack levels and the reserve goods at the top provide great efficiency, increasing speed in the preparation of orders.
Gallery
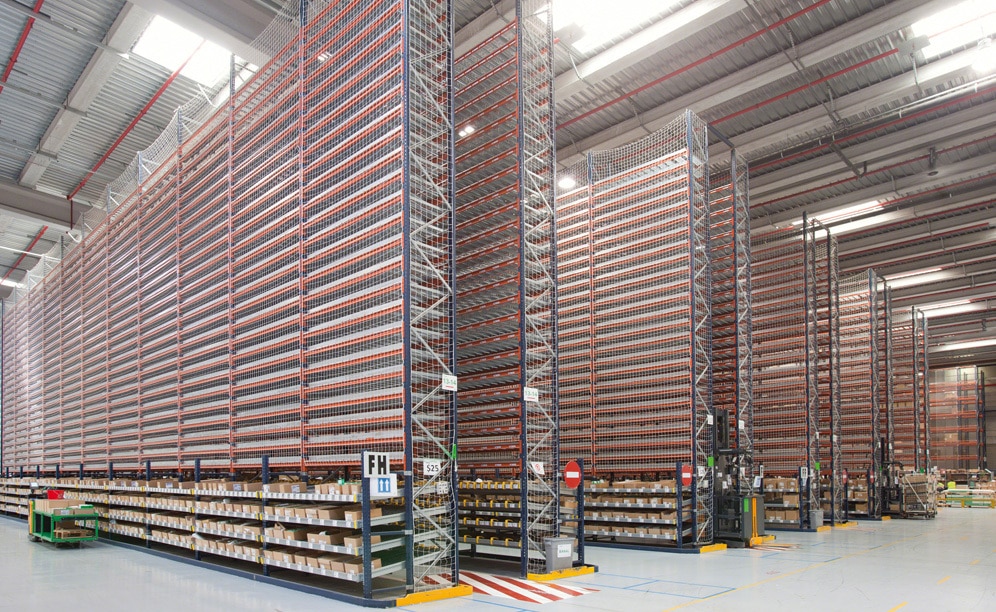
Ask an expert