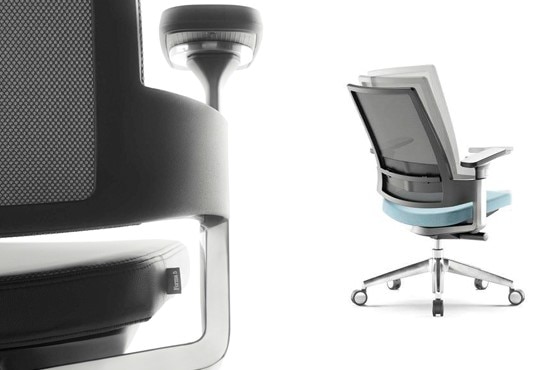
Forma 5: just-in-time furniture production
The organisation of space and operations enables Formula 5 to distribute 425 workstations per day
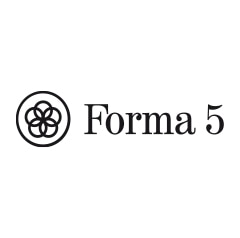
At the installations of office furniture company Forma 5 near Seville (Spain), over 425 complete workstations are manufactured and distributed every day. Each of them contains a table, a chair and a storage unit. To cope with this demanding pace of work, the firm has reorganised and streamlined all its processes. It has also implemented Easy WMS, the warehouse management system by Mecalux, to execute extremely precise control of all its SKUs, including raw materials, semi-finished goods and finished products. This WMS has been connected to the 35 warehouses of Forma 5’s raw material suppliers in order to know the status of inventory in real time.
Workspace solutions
With more than 35 years of experience, Forma 5 is a cutting-edge business in the office furniture sector. Since its inception, it has been committed to innovation with the aim of improving its products on three fronts: quality, comfort and style. This pledge was decisive in the company’s expansion into the international market.
Forma 5’s headquarters are in Seville (Spain), although it has various showrooms in Madrid, Barcelona, London, Paris and Dubai where customers can see, touch and try out all the new products. According to Alfonso Capitán, ICT Director at Forma 5, “our furniture is distributed in 60 countries, amongst them, Spain, France, Portugal, the UK, Australia and Ireland, in addition to the Middle East and Central America.”
Forma 5’s installations in Spain
Located in the city of Dos Hermanas, near Seville, Forma 5’s plant occupies a total surface area of 50,000 m2, the equivalent of 10 football fields. There, it stores materials used to manufacture furniture; at the same space, the parts that make up each piece of furniture (e.g., chair backs) are put together. The final assembly of the furniture is carried out at customers’ facilities.
Optimal organisation of space and operations is essential for Forma 5 to distribute every day the 425 complete workstations purchased by customers. This company’s way of operating is similar to that of — differences aside — the production centre of an automotive company in that the work schedule is extremely demanding. Providers supply Forma 5 at just the right time to prevent interruptions in furniture production.
This working method, known as just-in-time, requires Forma 5 to keep inventory to a minimum and to be fully coordinated with its suppliers so that they deliver the goods on time to finish the manufacturing process.
Alfonso Capitán explains, “To improve our supply chain, it was vital to equip ourselves with a warehouse management system (WMS) that, in addition to monitoring all the products, would enable us to optimise flows. After evaluating various software solutions, we opted for Easy WMS by Mecalux because it was the WMS that could best meet our needs.”.
The WMS also needed to be able to connect to Forma 5’s ERP. The company uses its own software that communicates with Easy WMS continuously and bidirectionally. This exchange of information between the two systems is fundamental for controlling all the goods and verifying that each order contains the items needed to assemble the furniture.
Easy WMS is centred on three key concepts to leverage all of Forma 5’s operations:
1. Control of all inventory
Forma 5’s suppliers (35 in total) are based nearby. Easy WMS is connected to these logistics centres and knows the exact location of the raw materials and semi-finished goods.
Forma 5 sends the materials to be processed to the suppliers. Subsequently, it receives the semi-finished goods (an average of 160 pallets per day). This system has eliminated the need to designate additional space to storage; as they are so close, suppliers can send the required items at the appropriate times.
When the products arrive at the Forma 5 plant, Easy WMS is notified and organises their receipt. Operators identify them one by one with the help of radiofrequency terminals. Easy WMS immediately assigns each item a location, taking into account its size, demand level and type of furniture for which it will be used.
Forma 5 works with nearly 20,000 of raw materials, 73,000 SKUs of semi-finished goods and 178,000 SKUs of finished products. Therefore, automated goods management and traceability enable control of all the items and eliminate any possible errors resulting from manual handling.
2. Assembly stations supplied at all times
When Forma 5’s ERP receives an order, it automatically calculates and generates a bill of materials with the components required for each order. It then sends that list to Easy WMS, which takes charge of the situation. The function of the WMS is to supply the 63 furniture assembly stations with all the necessary materials for operators assigned there to work without interruption.
Throughout the day, these workers receive lists of orders containing the furniture that needs to be assembled. These lists tell them which materials are indispensable for each piece of furniture.
Easy WMS specifies which materials the picking operators need to get from the storage areas. To avoid confusion, the system’s indications are extremely precise: they show the employees the exact location to go to, the number of items to pick and the assembly stations to which they have to be moved.
This type of work organisation allows the company to optimise assembly times and save money, which helps greatly, especially during peak seasons.
3. Proper distribution of goods
Once the work at the assembly stations has finished, the products are sent to the consolidation and dispatch area. Before sending them to customers, they must pass a mandatory inspection to ensure that they were assembled in accordance with quality standards. Easy WMS sends the orders to the operators so that all the items, without exception, go through this process.
In the consolidation area, the goods are grouped by client requirements and specifications. Easy WMS is charged with verifying that all the orders are correct and that no mistakes have been made. Once checked, they can be loaded onto the lorry and delivered to customers. Approximately 14 lorries exit the Forma 5 installations every day.
Alfonso Capitán - ICT Director at Forma 5
“We chose Mecalux because it came highly recommended, and we wanted an experienced software product supplier. Easy WMS has provided our business with considerable advantages, especially the capacity to adapt to our processes. Amongst its benefits, we would highlight the reliability of stock, the ability to locate products quickly and the improvement of processes with more efficient flows.”
Just-in-time logistics for furniture production
Forma 5’s plant stands out for its fastpaced work environment, which guarantees the dispatch of 425 complete workstations per day.
With the installation of Easy WMS, the company has transformed and perfected its supply chain with a single objective: to provide better service.. . All its logistics operations are just-in-time; that is, the production plant is connected to the suppliers in order to receive the needed semi-finished goods at the right time.
Forma 5 can now carry out a more exhaustive control of its wide variety of SKUs (of raw materials, semi-finished goods and finished products) and be more productive. The WMS guides the picking operators at all time, telling them where to locate each item and to which assembly station to bring it. The job of these operators is to supply the workstations with the necessary products to prevent interruptions in furniture production.
The
Advantages for Forma 5
- Just-in-time logistics: Easy WMS ensures uninterrupted and agile furniture production. To do so, it precisely controls all of Forma 5’s stock, guaranteeing that the assembly stations are supplied with all the necessary goods.
- Optimisation of stock and space: the real-time synchronisation of Easy WMS with the 35 raw material suppliers means that the goods essential for manufacturing furniture are always available.
- Traceability and elimination of errors: the WMS organises and manages the workflows. As a result, mistakes are no longer made, and each piece of furniture produced is fully traceable.
Warehouse of Forma 5 | |
---|---|
Surface area of the centre: | 50,000 m² |
SKUs of raw materials: | 20,000 |
SKUs of semi-finished goods: | 73,000 |
SKUs of finished products: | 178,000 |
Workstations distributed per day: | 425 |
Furniture assembly stations: | 63 |
Ask an expert