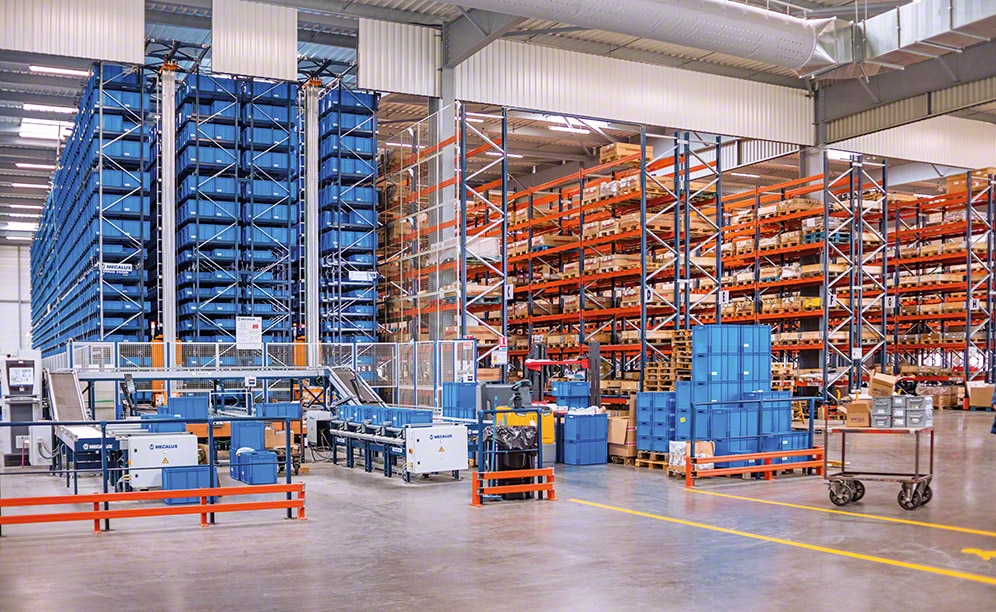
Peak picking productivity at Grégoire-Besson
The new Grégoire-Besson warehouse consists of an automated warehouse for boxes, pallet racking and cantilever racking
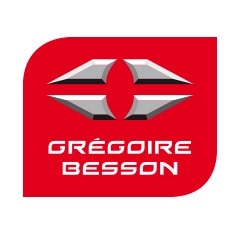
The new Grégoire-Besson distribution centre, a French farm technology equipment company, consists of an automated warehouse for boxes, pallet racking and cantilever racking by Mecalux. The combination of these three storage systems lets merchandise be organised according to their characteristics and demand, streamlining order picking tremendously.
About Grégoire-Besson
For almost 200 years, Grégoire-Besson has led French production of agricultural equipment designed to optimise the natural resources the land produces.
The company enjoys a substantial business presence internationally and owns production centres in France, Germany and Italy. Its machines are outstanding because they are innovative, efficient, heavy-duty and adaptable to the layout of any sort of farmland.
Needs of the company
Grégoire-Besson has constructed a new 4,500 m2 warehouse in the town of Saint Germain sur Moine (France) that will give the company the upper hand in the growth it has experienced over the last few years.
Here goods are stored, and orders are prepared with components and spare parts. The company needed more storage capacity, as well as better product sorting by size and turnover, to achieve top throughput and augment how many dispatches go out daily.
The company consulted Mecalux to discover the best way to solve all the requirements it had laid out for itself. The plethora of different sizes, weights and classifications demanded a very detailed analysis of each one of these.
The solution
Mecalux has fitted out the distribution centre with three different storage systems:
Products are slotted into the most convenient storage solution taking into account their size and level of demand.
Gabin Guegan - Spare Parts Manager at Grégoire-Besson
"With this solution from Mecalux, we have acquired more productivity and efficiency in our order preparation, while at the same time improving the management and safety of our goods".
Cantilever racking
The longest and largest unit loads are housed on cantilever racks.
These are 5 m tall and consist of columns and arms to rest the loads on. Cantilever components are readily configurable and can be readjusted to suit different heights and types of merchandise, as well as varying warehouse logistics requirements down the road.
The lower level includes mesh enclosed shelves, which strengthen the structure by making them rigid. Packets and different sized pallets are deposited there.
Pallet racking
These racks store either palletised goods or containers. These 7.5 m high racks are noted for their versatility to adapt to a wide variety of SKUs of distinct sizes, turnovers and volumes, and have a capacity to store more than 4,400 pallets.
Having direct access is crucial at Grégoire-Besson, since this provides high flexibility when managing goods and preparing orders.
Operators crisscross the warehouse locating the SKUs for each order, as instructed by the Easy WMS warehouse management software by Mecalux through a radiofrequency device. On lower levels, picking is carried out directly from the pallets and reserve products are deposited on upper levels –keeping merchandise available at all times.
In a part of these aisles, the upper levels of the racks include slide-out platforms to deposit containers on. Upon arriving at the location, the worker slides the platform out and can easily access the items within the container.
Miniload warehouse
Smaller products are inserted into the automated warehouses for boxes. Two different box models share the space: on one side, 600 x 400 x 240 mm boxes and, on the other, those of 600 x 400 x 420 mm.
The warehouse is composed of two aisles with double-deep racking on both sides that measure 47 m long, 9 m high and have 17 shelves.
A miniload stacker crane runs through each aisle, inserting and extracting the goods in their locations automatically. These machines that run at a travel speed of 180 m/min and 100 m/min when raised, include an extraction system with telescopic forks that access the second position of each rack location.
The frontal part of the warehouse is where a roller conveyor circuit is installed that takes goods to the two picking stations. These comprise an order prep table capable of holding waves of four orders at once.
Order preparation fulfils the 'goods-to-person' principle, i.e., the stacker crane provides the operators with the goods automatically. Next, the operators extract the products specified to them by the WMS and place these items into the corresponding box on the order prep table.
Once the four-order wave is completed, the conveyor circuit shifts the boxes to the consolidation area –located at one side of the warehouse. Here there are two tables with computer terminals, scales, box sealers, labellers and strapping machines. Items are set in the cardboard boxes and packaging, labelling and issuing of the documentation needed to dispatch these boxes are carried out.
There is a replenishment post alongside the picking stations. It has the equipment needed to carry this task out, such as a scale, a scanner and a computer screen with auxiliary devices.
Dispatch zone
In front of the racks, a spacious reception and expedition area has been arranged, which includes a preloads area on the floor.
This space is allocated to the sorting, consolidation and closing of orders. The pallets are grouped according to if they correspond to the same order or delivery route. Orders are prepared before the lorry is loaded to cut wait times for goods leaving the warehouse.
An intelligent software
Mecalux has implemented the Easy WMS warehouse management software in the Grégoire-Besson installation. It runs through a SQL Server database in a virtualised environment, thus optimising the performance of hardware resources (data storage devices, processors, etc.).
Easy WMS by Mecalux controls all installation workflows, both in the automated miniload warehouse and the pallet racks. It is involved in all processes and operations being carried out, from the arrival of the goods, to when they are located into the racks, up to when they are loaded onto distribution vehicles.
The WMS receives input orders from the ERP. Once the goods are received, they are moved to the corresponding rack depending on the product type (boxed or palletised) and on the previously configured WMS rules and strategies for product locations.
Boxes are placed on the floor, waiting to be inserted into the miniload warehouse. Meanwhile, pallets are assigned a location in the pallet racks. Unlabelled goods are sent directly to the cantilever racks.
Easy WMS receives output commands from the ERP for dispatching the goods. Next, the WMS can create picking instructions for the automated warehouse for boxes or ones for shipping out entire pallets from the pallet racks.
Prepared goods, ready to be dispatched, are deposited in the consolidation areas or sent directly to the docks to be loaded onto the transportation vehicles.
In one part of the consolidation area, an express orders station was enabled and, in another, ten stations for the remaining orders. Here they deposit pallets coming from the pallet racks that hold part of the order. Then, they complete this order with products from the miniload warehouse.
For the system, the orders are closed automatically when the requested goods have been loaded onto the lorry. While it loads, the WMS checks that the different pallets of the same order are assigned to the same carrier.
Control module
Easy WMS by Mecalux is in continuous communication with the Galileo control module by Mecalux, which commands the stacker cranes and conveyors to move, which in turn send boxes to picking stations or to the consolidation area.
Advantages for Grégoire-Besson
- Efficient picking: the layout of the goods in the warehouse guarantees fast, accurate order preparation.
- High storage capacity: the warehouse is equipped with three storage systems that adapt to the wide product range of Grégoire-Besson.
- Intelligently managed: the Galileo control module gives movement orders to the various electromechanical equipment of the miniload warehouse.
Automated miniload warehouse | |
---|---|
Storage capacity: | 10,064 boxes |
Max. weight per box: | 50 kg |
No. of stacker cranes: | 2 |
Warehouse height: | 9 m |
Warehouse length: | 47 m |
Storage levels: | 17 |
Gallery
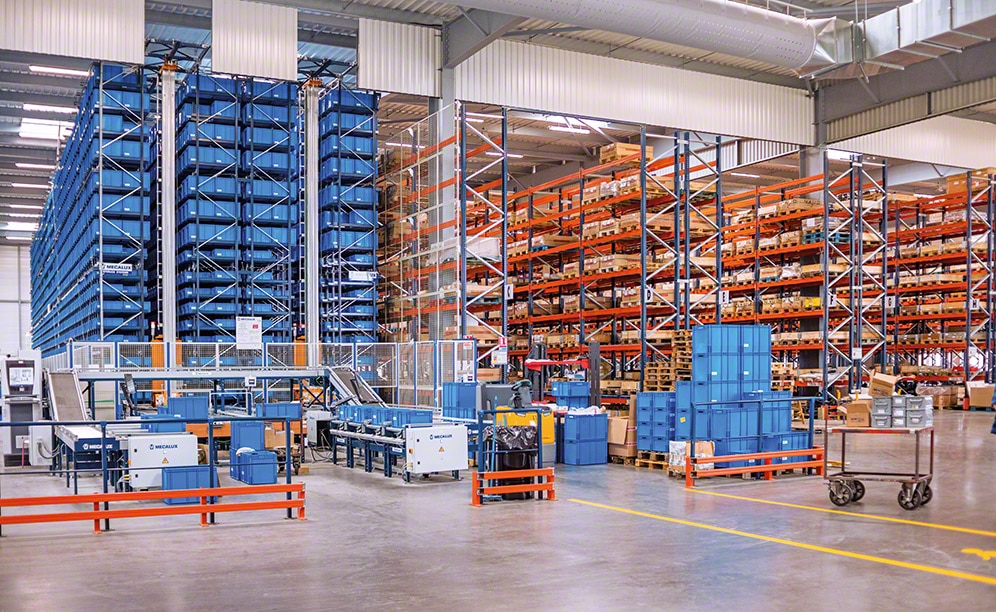
Ask an expert