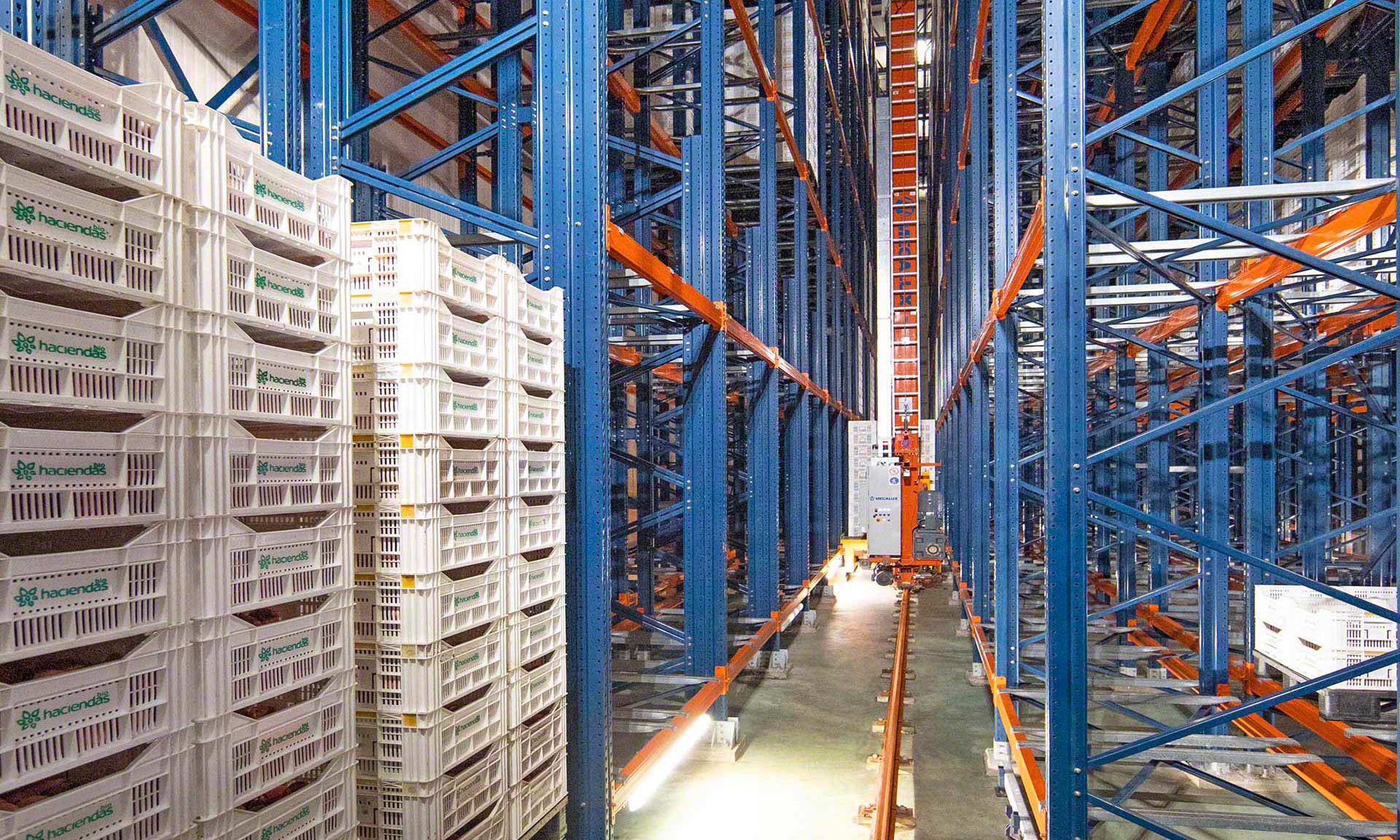
Hacienda La Albuera: automated buffer at different temperatures
Easy WMS provides traceability of the fruit, managing its location according to temperature and humidity
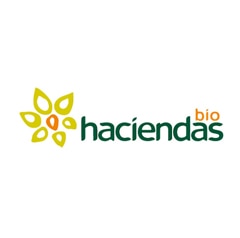
Agricultural company Hacienda La Albuera has built an automated clad-rack cold-storage warehouse in Extremadura, Spain, to manage its annual production of 32,700 tonnes of freshly harvested fruit and vegetables. The facility, with a capacity for 5,800 containers, serves as a storage buffer and is automatically connected with the calibration and packaging area. Easy WMS provides total traceability of the fruit, guaranteeing that the correct temperature and humidity conditions are maintained. In the time since this automated warehouse was commissioned, the company has grown by 85%.
Biodynamic farming
Hacienda La Albuera, founded in 2015 in the town of Guareña (Extremadura, Spain), is a business dedicated to the cultivation and marketing of agricultural products. It is noted for its constant search for new crops to meet the most demanding needs of the market. The company does all of this while always ensuring food safety through organic and sustainable production based on respect for the environment and biodiversity.
The company forms part of HaciendasBio, a leading firm in the European organic fruits and vegetables market, which boasts more than 1,000 hectares of farmland among its 30 farms strategically located in nine Spanish provinces. With over 1,500 employees, 98% of the fruit and vegetables it sells is self-produced.
Recently, and as a result of its growth over the past few years, the company opened a new centre spanning 400 hectares. It houses the fruit and vegetable production zone and the calibration and packaging area, in addition to offices, a space open to visitors and a shop with organic products. This facility has become the company’s new corporate and industrial headquarters, replacing the one it had in Guareña.
Hacienda La Albuera’s production centre is equipped with latest-generation technology, which is indispensable for managing its annual production of 32,700 t of fruit and vegetables (specifically, 20,000 t of fruit and 12,700 t of vegetables). Technology not only boosts throughput, but also enables the practice of a sustainable, eco- and environmentally-friendly activity. In fact, the packaging area is equipped with a system that recovers residual energy from processes.
Automated buffer
Hacienda La Albuera has a space for the temporary management at a controlled temperature of freshly picked fruits and vegetables that must go through the calibration process (consisting of selecting and sorting the products according to their diameter, length and shape) and are then packaged. “We calibrate all the fruit we harvest on our farms: approximately 20 batches a day. Additionally, each one of these batches contains eight types of fruit,” explains Paco Casallo, Chairman of Hacienda La Albuera.
In the past, the firm organised all of these goods manually. However, with the increased production, and in line with its modernisation and sustainability strategy, it considered investing in automation. “The reason is obvious: all the fruit needs to be properly identified, traceable and available to be sent to the calibration zone at the right time, which is only possible with the help of automation,” affirms Paco Casallo.
With this idea in mind, the company turned to Mecalux because, as Hacienda La Albuera’s Chairman points out, “we were familiar with the quality of its racks and their behaviour in cold storage warehouses and high humidity conditions.”
Mecalux proposed building a 20-metre-tall automated clad-rack warehouse consisting of two aisles with double-deep racking on both sides. A twin-mast stacker crane operates in each aisle, automatically storing and retrieving over 300 pallets by following orders from the Easy WMS warehouse management system.
“Our assessment of the Mecalux team’s offer was very positive. We especially liked the fact that the warehouse management system could be easily integrated with our Keops ERP system,” notes Paco Casallo.
The racks measure 46 m long and have six storage levels. They are designed to store goods up to 2.3 m tall and manage two types of unit loads: pallets and containers, both 1,000 x 1,200 mm. Each location can store one pallet or up to four containers one on top of the other, providing a total capacity of 5,800 containers.
The cold storage facility has been designed taking into account future expansion to increase the storage capacity, in line with the company’s growth prospects.
Automated cold storage warehouse
The automated buffer operates at a constant temperature of 0-2 °C with a relative humidity of 92-97 °C so as to maintain the flavour, colour, texture, aroma and nutritious properties of the fruit and vegetables.
Well aware of the importance of temperature and humidity for the final product, Mecalux has set up a cooling tunnel comprising the last two rows of racks in the automated facility. Containers that enter the warehouse with a temperature above 2 °C are temporarily stored there. “This enables us to guarantee the most appropriate cooling time for each type of fruit, which has helped us to improve their preservation,” adds Paco Casallo.
To maintain the temperature inside the cold storage facility, automatic access doors have been installed between the entrance to the warehouse and the cooling tunnel.
Putaway management
Easy WMS is charged with organising locations in the warehouse and cooling area, as well as properly supervising inflows and outflows. To do so, it is connected to Hacienda La Albuera’s ERP system, Keops, as well as the ventilation system managed by Johnson Controls. “The integration between Easy WMS and the other software has been a success, with all systems sharing data and optimising processes accordingly,” highlights the company Chairman.
When storing a pallet in the cooling area, Easy WMS notifies Johnson Controls of the cell in which the fans should be activated to cool that zone. Once the preset temperature has been reached, Easy WMS orders that pallet to be removed, and the fans stop immediately.
In the rest of the warehouse, the putaway strategy is based on product turnover and estimated storage time. Easy WMS takes into account the fact that the warehouse is zoned based on the temperature of each location. This means that the locations closest to the four evaporators installed above the racks have the lowest temperature.
Easy WMS is also configured to control Hacienda La Albuera’s products that do not need to be stored and, thus, are sent directly to the calibration zone. Lastly, the WMS orchestrates the storage of empty pallets, boxes and auxiliary material used in the calibration and packaging process.
Connection with the calibration and packaging area
The automated warehouse is responsible for supplying the calibration and packaging zones with the required fruit and vegetables and then storing them once again.
In carrying out this process, Easy WMS plays a fundamental part: it ensures just-in-time supplies to the production lines. Moreover, for this to be possible, the WMS and ERP system must be connected.
When the ERP system notifies the WMS that it needs a specific product, it is not sent all at once, but is supplied gradually. Since the calibration and packaging zone does not have enough storage space, the containers are sent as they are needed.
The same occurs when sending empty boxes to the production area. The ERP requests the boxes necessary for performing the calibration process, and Easy WMS supplies them on demand.
Fully automated operations
With this automated buffer, Hacienda La Albuera has a solution that allows it to efficiently manage all its fruit with no operator intervention, from its harvest from the fields to its dispatch to customers.
Thanks to automation, the company has markedly cut the time taken to complete each operation and sped up goods entries and exits, moving more than 300 pallets a day. The business can now respond better to changes in demand.
Furthermore, automation has not only boosted operational throughput, but has also been essential for maintaining the cold chain required for preserving the fruit and vegetables optimally. “Since this automated warehouse was put into service, we’ve grown by 85%. In addition, by having the fruit supplied to the calibration and packaging area automatically, we can concentrate on other operations that add more value to our business,” enthuses Paco Casallo.
We’re very pleased with the automated clad-rack warehouse. It provides us with highly accurate stock control, improved responsiveness and the agility to be able to supply the calibration and packaging area in under three minutes. Consequently, we’ve enhanced the quality of our service and cut costs by not having to stop production due to a lack of supplies.
Advantages for Hacienda La Albuera
- Automated buffer: the company manages its fruit in a completed automated way, from its arrival from fields through to its shipment to customers.
- Just-in-time supply: the automated warehouse supplies the goods required in the calibration and packaging area piecemeal and on demand.
- Controlled temperature: Easy WMS is tasked with placing the containers in the right area based on turnover, stipulated temperature and the time they must remain in the automated facility.
Automated warehouses for pallets | |
---|---|
Storage capacity: | 1,664 pallets |
Max. No. of containers: | 5,800 |
Pallet size: | 1,000 x 1,200 mm |
Max. weight per pallet: | 1,000 kg |
Racking height: | 17.4 m |
Racking length: | 46 m |
Gallery
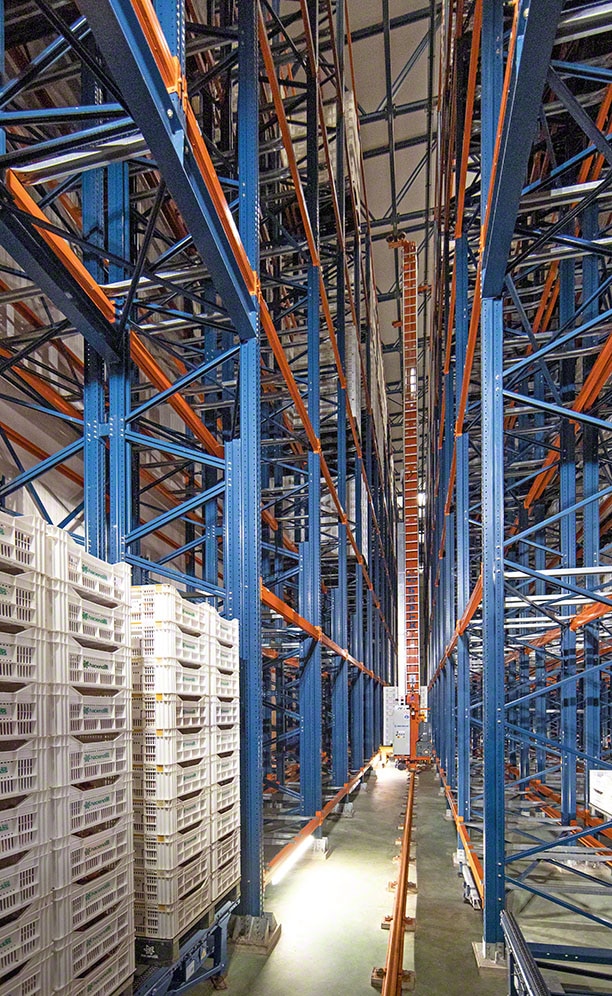
Hacienda La Albuera's automated fruit and vegetable warehouse in Guareña, Spain
Ask an expert