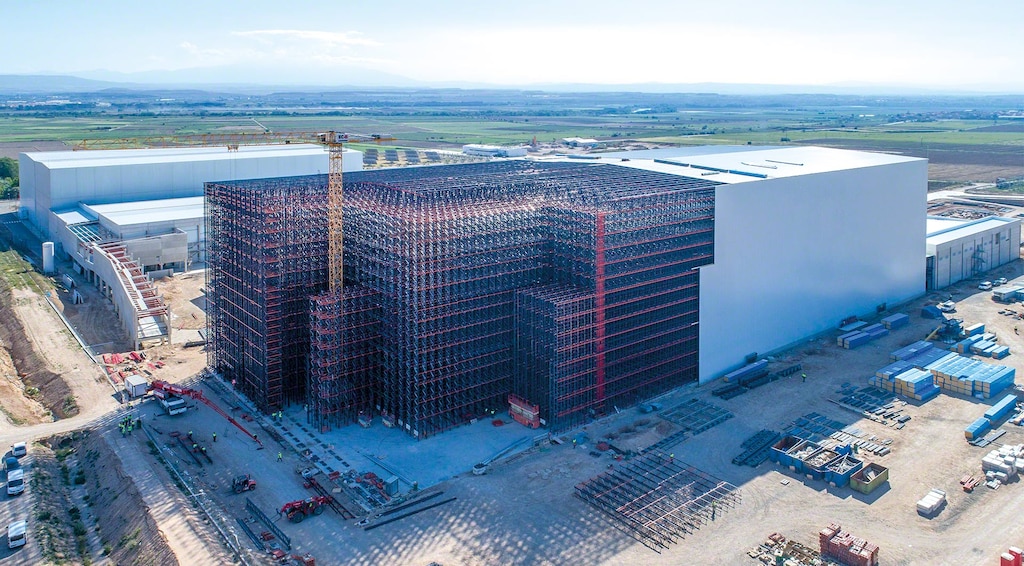
Rack Supported Warehouse (Clad Rack)
Comprehensive storage system in which the racking forms the structure of the warehouse. Space optimisation, cost savings and faster implementation.
The product
Clad rack: great height and maximum storage capacity
Clad rack warehouses are buildings whose main structural component is the racking. The racks bear the weight of the goods stored in addition to the side and roof cladding and external agents, such as wind force. Therefore, rack supported buildings require minimal civil works, which streamlines assembly and reduces costs compared to traditional construction systems.
Rack supported warehouses make the most of all available space and can reach heights of up to 45 m. They also stand out for their great versatility: they can be designed to incorporate several types of storage solutions, from conventional and drive-in/drive through racking to fully automated storage and retrieval systems (AS/RS). Mecalux accompanies its clients throughout the project, from the preliminary calculations and design phase to the warehouse’s commissioning.
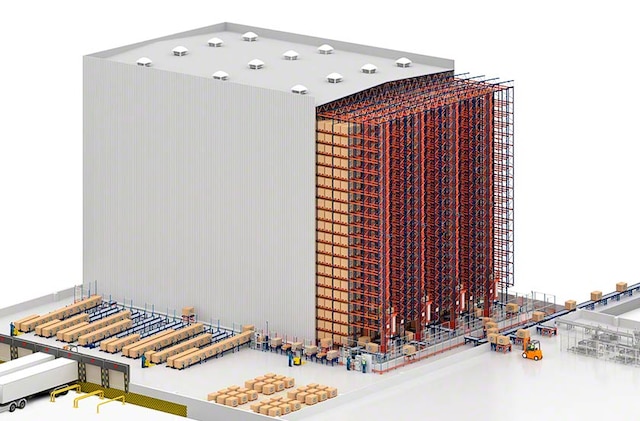
Advantages of clad rack warehouses
- Fast, simple construction: project implementation times for rack supported buildings are shorter compared to traditional warehouses. Moreover, they require minimal construction.
- Cost savings: the investment is also lower than that required for traditionally built facilities.
- High-bay storage: clad rack warehouses can be up to 45 m tall. Their height is only limited by local regulations and the reach of the handling equipment used.
- Optimal utilisation of surface area: the warehouse and racking are designed simultaneously. They occupy only the necessary space, without any intermediate columns.
- Maximum versatility: rack clad buildings can be configured with the storage system that best meets each need. These range from conventional and drive-in/drive-through racking solutions operated with forklifts through to fully automated storage and retrieval systems (AS/RS).
- Low-temperature storage: these rack supported structures can also function as cold storage and freezer warehouses.
- Strength and safety: rack supported warehouses are extremely robust structures designed to withstand the effects of external forces such as wind, snow loads and seismic movements.
- Demountable: the structure is primarily formed racking with components that are assembled or bolted together. Therefore, it can be easily dismantled, allowing for the recovery of a high percentage of components.
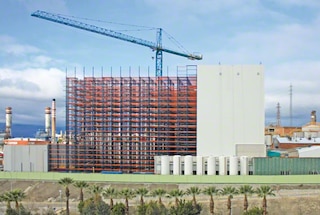
With the clad rack warehouse installed by Mecalux, we can store up to 15,000 pallets, which would be impossible in a traditional warehouse
Types of clad rack warehouses
Rack supported buildings adapt to multiple operational needs and requirements
The structure of a clad rack warehouse can be designed from a wide array of storage solutions. These can range from conventional and drive-in/drive-through racking to fully automated storage and retrieval systems (AS/RS) that use robotic equipment to handle loads.
Design and operation of clad rack warehouses
Extremely robust buildings with quick assembly
Rack supported buildings are projects that require a thorough structural analysis. However, the construction work involved is minimal, and they are built within a short time frame. The process consists of various phases, encompassing the warehouse design, manufacture and assembly.
Testimonials
Case studies
See more case studiesComponents of a rack supported warehouse
The primary feature of a clad rack warehouse is that the racking that comprises it supports several elements: the stored loads, the thrust of the handling equipment, the other structural components (roof and side cladding) and external agents (wind forces, snow loads, seismic movements, etc.).
The basic structure of a clad rack warehouse is formed by three main elements: the racking, concrete floor slab and cladding (both roof and façade panels).
A rack supported building can be configured from a wide range of pallet storage solutions, from conventional and high-density racking to fully automated systems.
Safety is a priority in the design, choice of materials and assembly of Mecalux rack supported warehouses. They comply with regulations in force and meet various fire protection requirements.
FAQs
The definition of a clad rack warehouse is simple: it is a type of building in which the racking constitutes the main structural component of the construction system. For this reason, in a clad rack warehouse, the racking supports its own weight, that of the stored goods and that of the roof and façade cladding; the stresses of the handling equipment; and the action of external agents, such as wind force and roof overloads due to snow.
A pallet rack supported building is the perfect solution for achieving a short construction time frame and significant cost savings compared to traditional systems. It is also an ideal alternative for maximising the use of available floor space, regardless of building height. Likewise, this construction system is recommended for cold storage and freezer warehouses.
Mecalux has extensive experience in designing, manufacturing, and assembling rack clad buildings for a wide variety of sectors. These range from the automotive, pharmaceutical and petrochemical industries to food, metallurgy and ceramics.
The civil work involved in building a clad rack warehouse is minimal. It is limited to the construction of the concrete slab upon which the structure will stand and, if necessary, a perimeter sealing wall.
Clad rack warehouses have multiple benefits, although two stand out: faster construction and lower initial investment compared to traditionally built facilities. As the racking itself constitutes the building’s main structural component, the required civil work is minimal. This approach results in considerable cost savings as well as speedier assembly and commissioning.
However, due precisely to the nature of the storage system’s structure, modifications applicable to it are limited. Nevertheless, clad rack warehouses are easily disassembled, making it possible to recover a large share of their components.
Rack supported buildings can be designed using a wide variety of storage systems. For example, selective pallet racking and drive-in/drive-through racking systems can be installed for load handling using forklifts. Meanwhile, automated storage and retrieval systems (AS/RS) — e.g., stacker cranes and the Automated Pallet Shuttle — completely automate product loading and unloading from the racking.
Mecalux’s clad rack warehouses are compatible with any type of cladding available in the market. It just needs to be defined in the design and preliminary calculation phase.
The height of a rack supported building is only conditioned by the regulations in force and the reach of the handling equipment employed. In an automated clad rack warehouse, for instance, it is possible to install racking measuring up to 45 m high.
Indeed. The construction system of a rack supported building can also be used in designing and assembling cold storage and freezer warehouses. In fact, it is the perfect solution for building these kinds of facilities, as the building occupies only the space necessary to house the racking. This maximises energy efficiency, resulting in significant cost savings.
Ask an expert