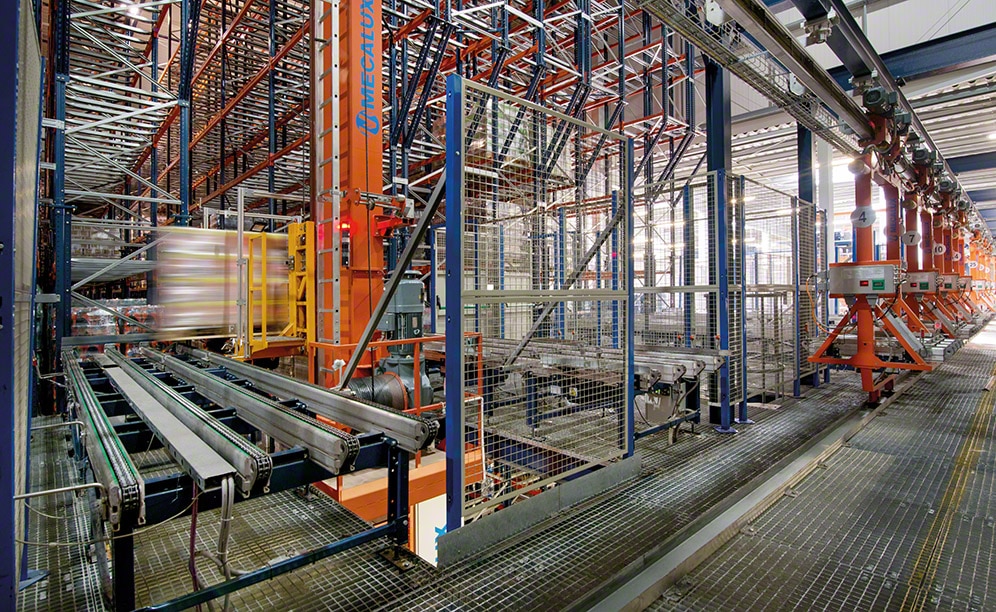
A large warehouse to hold the juices of Sokpol in Poland
Sokpol's juice warehouse in Poland is linked to manufacturing centre through an electrified monorail system (EMS)
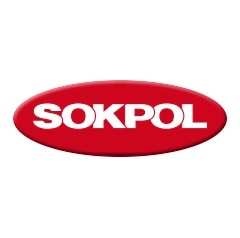
Sokpol is one of the best-known producers of juices, nectars and mineral waters in Poland. Its production centre in Myszków is set up with the latest cutting-edge technology to strengthen its productivity. Constant project improvement has always enlarged and adapted to Sokpol’s business goals and emerging market demands. Currently, the centre contains two warehouses, one of them is equipped with the semi-automatic Pallet Shuttle system and is set aside for high-demand finished products. The other has a capacity for more than 28,400 Euro pallets and is fully automated.
About Sokpol
The juices, soft drinks and fruit concentrates of Sokpol are some of the most popular in Poland. The company was founded in 1992. Since then, it is constantly developing and selling new products.
In the last few years, the business has boosted its presence internationally, and its products are distributed in most of Europe and the US.
The needs of Sokpol
Sokpol owns and operates a production centre in the town of Myszków, in Southern Poland, where it makes the majority of its products. Its location streamlines quick goods distribution throughout Europe.
Initially, the centre had a warehouse next to processing, allocated to storing finished products. However, the space was too small to deal with the increase in production.
Over the last few years, the company broadened its product catalogue and increased sales due to its international business expansion. Bound and determined to face down this and future challenges, it came to Mecalux for help.
The solution
Bearing Sokpol’s requirements in mind, Mecalux designed and built an automated warehouse with a capacity for more than 28,400 Euro pallets (800 x 1,200 mm) or 56,800 half-pallets (400 x 600 mm). This very modern solution is functional and guarantees high productivity, and also exceeds current business requirements.
The Sokpol centre is located on a huge plot of land, and the new warehouse is a ways away from the production plant. Covering this distance could imply higher handling costs when transporting goods, something that specifically needed cutting.
To do so, Mecalux constructed a covered overpass –5 m off the ground– that joins the production exit point to the new warehouse, crossing the first warehouse along one side. Inside the tunnel, an electrified monorail system sends goods full speed ahead.
Warehouse 1
Sokpol erected the first warehouse built next to its factory, equipped with the semi-automatic Pallet Shuttle system.
It acts as a buffer (short-stay warehouse) and is where it houses mainly finished consumer products, waiting to be shipped out.
This system is very suitable for this type of product, for consumer products and with a high number of pallets per SKU. Every bit of available space is fully used to top out storage capacity. Moreover, it runs simple, fast operations that require little to no action by operators, leading to a constant inflow and outflow of items.
The goods are managed as per the FIFO principle (first in, first out). In other words, the first pallet in is the first to leave. It features two working aisles: a loading aisle and another for unloading, which avoids interferences between the operations.
The warehouse has a preload staging area in front of the docks. Pallets are grouped together on the floor to speed up the subsequent loading of lorries.
Additionally, there are two floors. Each of these is used for different operations:
Bottom floor
The production centre and the warehouse fill this space. The workers reap the benefits of direct, unbarred access when transporting goods from one place to another.
Operators run forklifts to retrieve pallets and deposit them in the racking channels assigned by the warehouse management system. Next, the motorised shuttle shifts the load to the first open location automatically.
A conveyor circuit has also been installed, right at the production exit point, where pallets are inserted and flow directly to Warehouse 2. The conveyors channel the pallets towards two pallet lifts that move the loads to the upper floor, where the electrified monorail system runs.
A third lift, next to the docks, shifts products to the upper floor. This entry point is set aside for products flowing from other production centres that must be housed in the Warehouse 2.
Pallets go through a checkpoint before arriving at the pallet lift. There it is verified that all are in good condition and their weight and measurements correspond to the quality requirements in the automated warehouse.
Both the conveyor and the lift are enclosed with protective mesh, optical light sensors and safe access doors, which stop unauthorised personnel from entering their operating radius.
Upper floor
The electrified monorail system flows along one side of the warehouse and ends at the covered overpass. Warehouse 2 is located on the other side of the overpass.
By setting up the electrified monorails at such heights, the warehouse’s floor space is used well and this avoids interferences with other operations in-progress.
Covered overpass and electrified monorail system
The overpass tunnel is the best way to connect the three buildings together. In addition, it joins warehouses 1 and 2, which have a street that separates them.
An electrified monorail circuit is placed inside the tunnel. It is a very high-speed, smooth transport system that goes up to 100 m/min and guarantees a continuous flow of merchandise.
This circuit is composed of rails suspended from the ceiling, which the autonomous trollies move along while carrying the pallets. It is possible to increase the number of trolleys as per the changing needs and growth of the company.
In-warehouse operations mostly work with Euro pallets and half-pallets. Both the EMS trolleys and the conveyors are fitted out with four chain strands to move them.
The main benefits of electrified monorail systems are their high efficiency, versatility and minimal errors.
The circuit runs along the front of Warehouse 2, inserting and taking pallets off the incoming and outgoing conveyors of each aisle. At the end of the route, a maintenance area is enabled where trolleys are sent for needed repairs and those on standby are grouped.
This circuit has been meticulously designed, keeping in mind workflows and pallet numbers that must move back and forth between the two warehouses. That is why two shortcuts were created to avoid trolleys from having to run along the entire circuit.
Warehouse 2
The 15.5 m high automated warehouse contains nine aisles with double-deep racking on both sides.
SKUs are deposited in the corresponding locations based on A, B, C turnover criterion. Consumer products are placed in the front of the warehouse and those in less demand, at the rear. This layout optimises the movements of the handling equipment and boosts the number of cycles.
A stacker crane circulates in each aisle, operating at a speed of 160 m/min and 38 m/min when raised.
The stacker cranes collect the pallets from the inbound conveyors and deposit them in the locations assigned by the Easy WMS warehouse management software of Mecalux. Subsequently, they perform the same motion, but in the reverse order, for outbound goods.
The frontal warehouse area is two-floored. Electrified monorails circulate in the upper one and carry out the inputs and outputs of goods from the warehouse. Meanwhile, the bottom floor is used to place the power and control cabinets, as well as the access doors to the maintenance areas.
The electrical cabinets send and receive signals, and also carry electricity to the warehouse’s machines, like the stacker cranes, conveyors, electrified monorails and pallet lifts.
A shorter building is constructed onto one side of the warehouse, and distributed in two floors with different operations:
Upper floor
Picking stations are set up in the space of this open-plan area.
The electrified monorail system supplies this warehouse zone with the pallets it needs to prepare orders. The input conveyors include a hydraulic table that facilitates pallet truck operations.
Bottom floor
The area is allocated to outgoing dispatches and to preloads. Two lifts lower pallets to the bottom floor, where twin transfer cars organise this area depositing the goods in the corresponding live channel.
The transfer cars link two points in a straight line and can run bi-directionally. They slide over rails and are enabled with four strands of conveyor chains to move the pallets.
Forty live preload channels are placed on a slight incline, streamlining the gravity flows of pallets from the highest point to the lowest point, which faces the docks. Once there, the rollers are set apart so that the forklift’s blades can extract the pallets.
Easy WMS by Mecalux
Given the scale of this centre, a highly efficient IT system is crucial. In this respect, the warehouse management software developed by Mecalux organises and is involved in all tasks in-progress, including: the entry of goods from the processing plant and outside sources, the allocation of locations, stock control, extractions, transfers to dispatch etc.
When storing goods in their locations, Easy WMS has rules and algorithms that take into account the products’ characteristics, consumption criteria and their turnover.
The WMS shows which products must leave the warehouse. These move automatically to the preloads area, and stay on-hold until the lorry backs into the dock to be loaded.
So that this centre runs smoothly, Easy WMS is in permanent communication with the Sokpol ERP and, also, with the Galileo control module.
Galileo is the Mecalux control software and is tasked with giving orders to the machinery (conveyors, stacker cranes, electrified monorail systems) in both warehouses, as well as recording any possible incidents. It provides information in real-time for each piece of handling equipment and is able to simulate the electromechanical operations of the entire automated installation via a control system, called SCADA.
Advantages for Sokpol
- Efficient transport system: the electrified monorail circuit connects the two warehouses to processing, ensuring Sokpol gets the pallet flows it needs.
- A safe installation: the electromechanical equipment is protected against incidents, as well as unauthorised access by personnel.
- Optimal operations: goods are distributed in the warehouse according to their characteristics and rotation, thus increasing the productivity of the two warehouses.
Sokpol automated warehouse in Poland | |
---|---|
Installed equipment: | Electrified monorail system |
Installed equipment: | Pallet lifts |
Installed equipment: | Stacker cranes |
Installed equipment: | Transfer car |
Installed equipment: | Conveyors |
Installed equipment: | Live preload channels |
Gallery
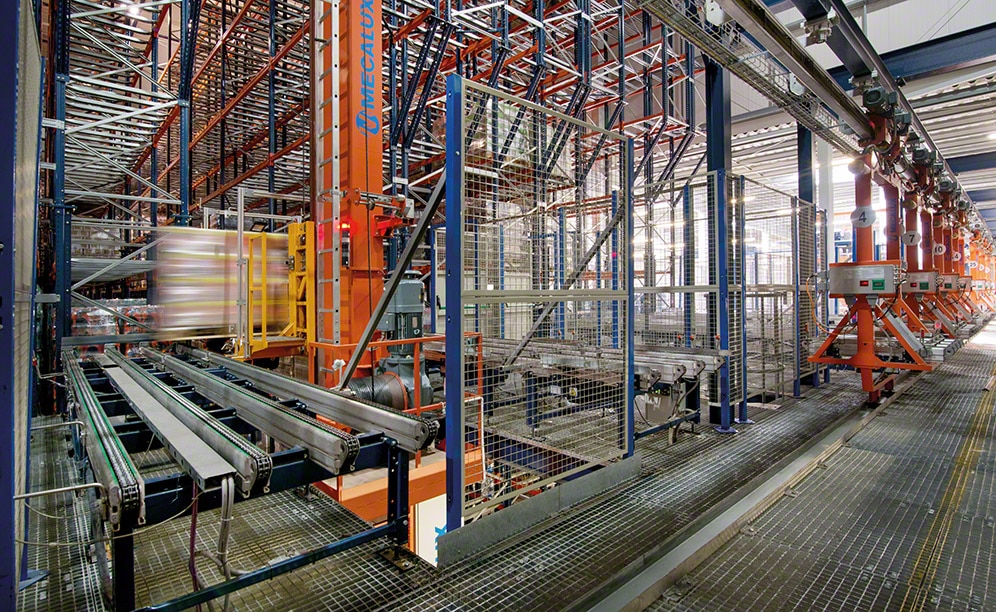
The automated warehouse of Sokpol with storage capacity for 28,400 pallets
Ask an expert