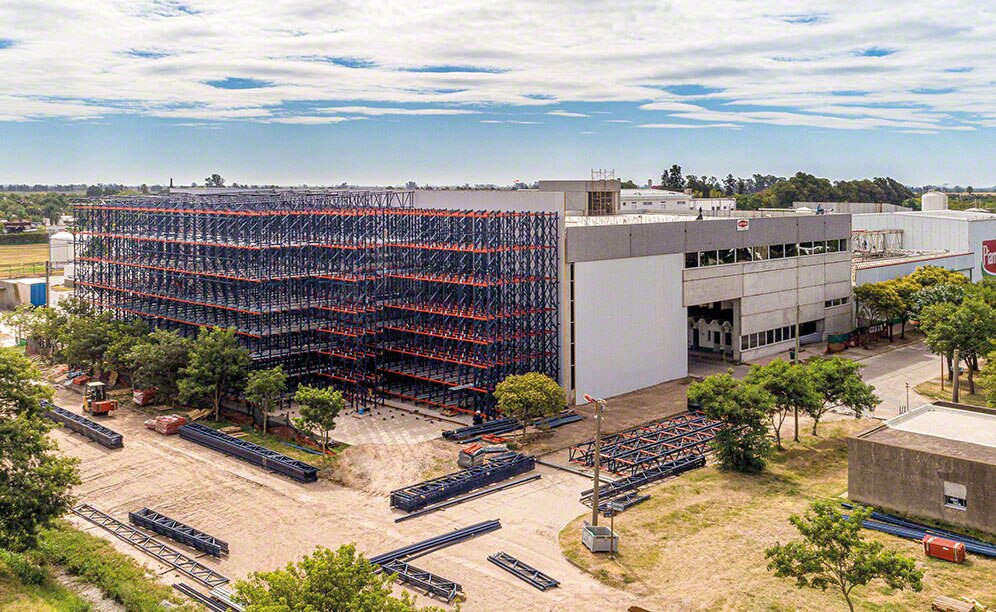
La Piamontesa: automation drives progress
La Piamontesa has built an automated clad-rack warehouse in Argentina for refrigerated foods
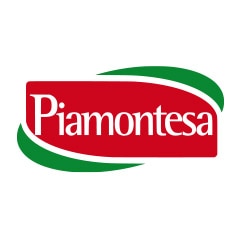
Food company La Piamontesa has come to the conclusion that, when it comes to boosting its business, automation is the way to go. For that reason, at its production plant in Brinkmann (Argentina), Mecalux has built a new, automated clad-rack cold store, where all the firm’s finished products are deposited. Managed by Easy WMS, the warehouse is composed of the Pallet Shuttle system with stacker crane. This solution provides constant goods flows and, most notably, optimises space to achieve a storage capacity of 2,415 pallets in merely 700 m². As food products with expiry dates are managed at this installation, goods control and traceability are key. Thus, the WMS supervises all movements and monitors batches across the supply chain.
An emblematic project
Founded in 1953, La Piamontesa has become one of the largest food companies in Argentina. It mostly produces sausages and meat products that are marketed throughout the country, thanks to a strategic and efficient distribution network.
At the company’s 39,000 m² plant in Brinkmann, Argentina, 500 employees prepare a total of 24,000 tonnes of finished product annually: 14,000 tonnes of pork and 10,000 tonnes of beef. In recent years, La Piamontesa has increased production because of rising demand.
As a result, “we didn’t have enough space to store all the meat, which forced us to rent more warehouses in other cities around Argentina,” explains engineer Diego Ghersi, Head of Engineering and Projects at La Piamontesa.
The company decided to resolve this issue by building a new installation right next to the production lines. “We had limited space, so we wanted to make better use of it to accommodate a larger number of items,” indicates Ghersi. Therefore, it was imperative to equip the firm with a high-density system that would enable optimisation of the storage surface area and, at the same time, help to lower energy consumption by reducing the volume to be cooled. The warehouse operates at a controlled temperature of between 2 and 4 ºC.
“After weighing different options, we decided on an automated solution,” notes Ghersi. Among the multiple advantages offered by automation, optimisation of the surface area used, also stands out, since automatic handling equipment requires less surface to manoeuvre.
In addition, automation provides constant and controlled goods movements across the various logistics processes. “With everything we have learned from this installation, we are convinced that the future of our company lies in automation,” says the Head of Engineering and Projects.
Connection with production
The new warehouse fulfils the important function of storing finished products at refrigerated temperature as they leave production and then distributing them to La Piamontesa’s more than 2,000 customers throughout Argentina. The installation is divided into two floors on which clearly differentiated operations are carried out: Upper floor: used solely for inflows (between 80 and 150 pallets are received per day, depending on the time of year). Lower floor: between 100 and 300 orders are prepared and shipped daily.
The warehouse is clad-rack constructed, i.e., the racks withstand their own weight as well as that of the goods and of the wall and roof cladding. On an area of 700 m², the building was designed to incorporate the racking as part of its structure. Thus, it occupies only the space strictly necessary.
The warehouse is comprised of a single 43-metre-long aisle with a racking unit on each side, each of which holds a maximum of nine pallets deep. Overall, the storage capacity amounts to 2,415 pallets with 77 different SKUs.
La Piamontesa handles 1,000 x 1,200 mm pallets with a maximum total weight of 1,100 kg. The height of the loaded pallets can be 1,870, 1,570 or 1,210 mm. Accordingly, the racking slots were adapted to these three different heights.
In the aisle, a stacker crane automatically moves the goods from the warehouse entry point to the corresponding storage channel. Once there, a motorised shuttle enters the racks to place the pallets in the deepest available location in the channel.
Mecalux proposed installing the automatic version of the Pallet Shuttle system with stacker crane because it combines all the advantages of high-density storage and automation. This solution is the result of merging the storage capacity of high-density systems with the reduction in the time spent on each operation, typical of automated systems.
The automatic Pallet Shuttle is expressly designed for high-volume SKUs and mass-consumption goods, as in the case of La Piamontesa. With this installation, the company has been able to not only store all its products, but also ensure their immediate entry and exit at the right time.
Order prep and dispatch
The lower floor of the warehouse is specifically intended for order preparation (between 100 and 300 orders per day). According to engineer Diego Ghersi, “each order is made up of a very diverse number of lines. Some customers request a single full pallet (e.g., supermarkets), while others want a combination of multiple SKUs.”
Proper organisation of the floor dedicated to picking and the incorporation of automatic equipment are crucial for achieving the required cycles and optimising order prep.
A transfer car collects the pallets leaving the installation and deposits them in one of the 15 positions where operators carry out picking tasks. This system prevents interruptions, as the necessary goods are always available.
Operators extract the products they need from each pallet according to orders from Easy WMS, the warehouse management system by Mecalux. By means of RF terminals, the WMS tells the operators which SKUs and quantities to pick for each order. There are three positions for full pallets that leave the installation without having to be split.
Just in front of the picking area, an extensive preload zone has been set up. As the items stored are food products with expiry dates, for La Piamontesa, it is essential to sequence and organise orders optimally by batch and transport route. In this area, orders are sorted; they then wait to be loaded onto the lorry at the right time.
Cross-docking of products that do not require refrigeration (mainly the sausages line) also takes place in the preload zone. Operators complete orders with these products, which are temporarily placed in this area.
Goods control
To streamline La Piamontesa’s supply chain, the company has implemented Easy WMS by Mecalux. This warehouse management system is charged with overseeing all goods movements and operations: inflows, storage tasks, order prep and dispatches.
Easy WMS has been integrated with La Piamontesa’s ERP in order to transfer data and information to manage the warehouse efficiently. In this way, the company can carry out extremely accurate monitoring of all the merchandise.
As most of the items have high turnover rates, goods inflows and outflows are constant. Easy WMS sorts pallets the moment they arrive at the warehouse and assigns them a location, taking into account their height and demand level.
The WMS controls all the goods, providing real-time information on stock status, which is indispensable when working with batches and perishable products. “Easy WMS has given us total traceability. We are able to know exactly what processes each item has undergone,” highlights engineer Diego Ghersi. Thus, with these data, decisions that help improve processes can be made much more easily.
Greater capacity and control
La Piamontesa has enhanced the storage capacity of its centre in Brinkmann to accommodate the rise in production recorded in recent years. If there is one thing that characterises its new warehouse, it is the optimisation of the entire surface area, which has helped reduce logistics and energy costs.
Among the numerous advantages of automation, the increased availability of products stands out. In addition, the Pallet Shuttle system serviced by a stacker crane ensures the continuous flow of goods.
The automated management of goods by Easy WMS has helped the company bring to fruition its new projects and supply an ever-growing number of customers. La Piamontesa’s future plans include expanding into the Asian market, which will be possible with a flexible, modern and efficient supply chain.
Ingeniero Diego Ghersi - Head of Engineering and Projects at La Piamontesa
“Traceability is one of the greatest advantages that technology — particularly, Easy WMS by Mecalux — has given us. We now know the specifics regarding the products we receive, such as where they are located and what processes they have gone through. This control is vital to our business, as we manage perishable products with expiry dates.”
Advantages for La Piamontesa
- A highly technological warehouse: automation streamlines and facilitates the management of 2,415 pallets without any possibility of error.
- Traceability for perishable products: Easy WMS knows the status of the goods in real time and, thus, can monitor them throughout the various processes they must undergo.
- Cost savings optimisation: of the surface area ensures a high-density system that reduces logistics costs and, at the same time, lowers the energy consumption needed to maintain the warehouse at a controlled temperature.
Automated clad-rack cold store of La Piamontesa | |
---|---|
Storage capacity: | 2,415 pallets |
Pallet sizes: | 1,000 x 1,200 x 1,870 / 1,570 / 1,210 mm |
Max. pallet weight: | 1,100 kg |
Warehouse height: | 14 m |
Warehouse length: | 43 m |
Gallery
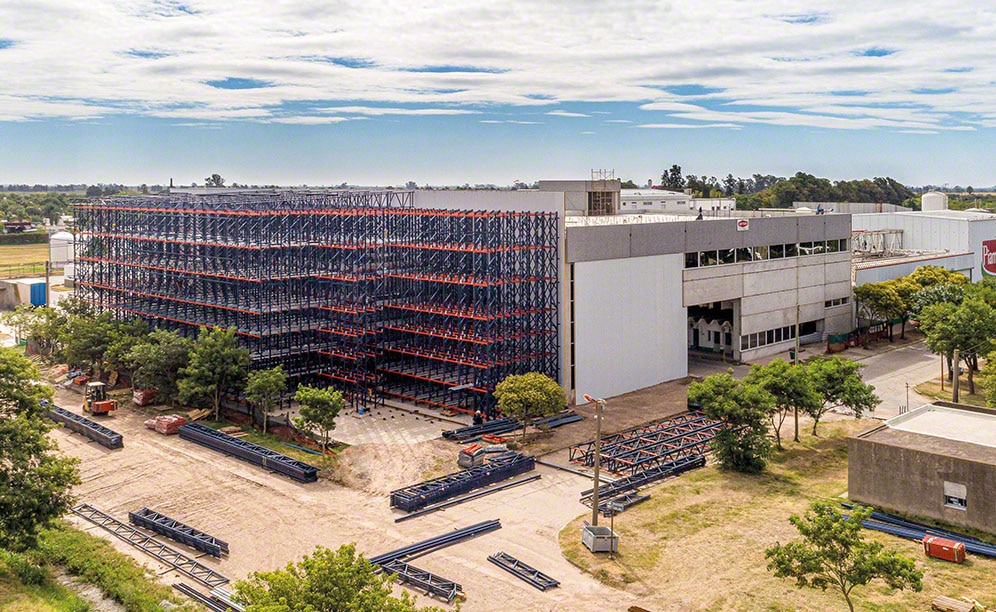
Warehouse in Argentina with La Piamontesa's refrigerated foods
Ask an expert