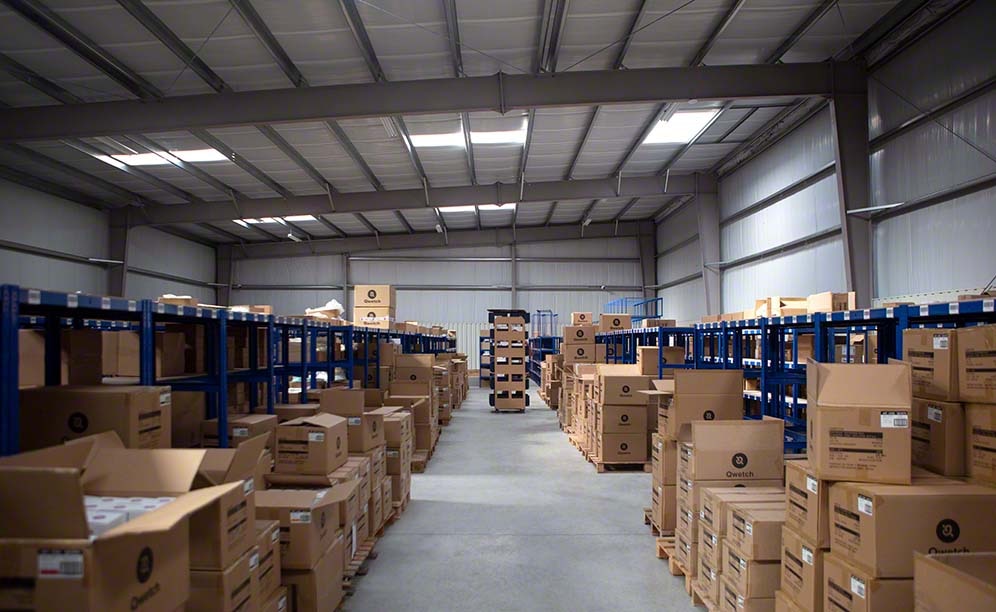
La Ruche Logistique manages products for e-commerce companies in its warehouse
The La Ruche Logistique warehouse is dedicated to order preparation for e-commerce companies
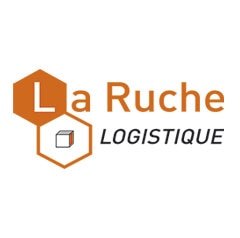
The logistics operator La Ruche Logistique has renovated its warehouse in Créancey (France) to meet the new demands of its customers (mostly e-commerce companies). With the installation of Easy WMS, Mecalux’s warehouse management system, the company has gone from preparing 150 daily orders to 500 consisting of more than 3,000 lines that are distributed and delivered in a matter of hours. With this WMS, the logistics operator has an efficient operation with which to face the rapid growth of e-commerce.
Logistics operator undergoing expansion
Active since 2014, La Ruche Logistique is a French logistics operator offering a customised service to all types of companies, mainly small and medium-sized enterprises.
The majority of its customers are companies in the e-commerce sector. “We live in the era of online sales, with businesses marketing very disparate products — from electronic cigarettes to books and clothing — through their websites. Our customers are growing at full speed, and it is therefore essential that we adapt to their rate of expansion,” explains La Ruche Logistique Manager Thomas Largeron.
These firms require the preparation of a large volume of orders consisting of a few order lines each, and their rapid distribution (within a few hours).
In the town of Créancey, La Ruche Logistique has a 3,000 m² warehouse where it stores its customers’ products and prepares their orders. From a logistical point of view, being between Paris and Lyon, it is in an ideal location for the goods to be delivered as quickly as possible.
Nevertheless, the company wanted to become more competitive and, to do so, it had to make better use of its warehouse. According to Thomas Largeron, “the business was growing unstoppably, and we had more and more customers. The figures speak for themselves: in a short time we went from managing 6,000 SKUs to 12,000.”
To deal with this situation, the company knew it had to optimise warehouse processes, “we needed to speed up order preparation and better manage stock,” admits the manager. There was no doubt about it: it was essential to implement a warehouse management system (WMS).
After comparing different options, the logistics operator opted for Easy WMS, the WMS developed by Mecalux. “We were convinced by the fact that it’s a customisable system,” says Thomas Largeron. “Mecalux’s technical team studied our requirements and operations in detail, so the WMS is configured to respond specifically to our processes.”
Now that it is operational, the company has not only raised productivity, but also the pace of work. The day-to-day running of this centre consists of receiving and storing 200 parcels, preparing 500 orders made up of a total of 3,000 lines, and dispatching 150 parcels.
Quick picking
The company realised that in order to boost its warehouse‘s main operation (order preparation) it had to take care of all the details, starting with the storage of the goods. Good organisation means speedier picking, because operators do not have to spend their time locating the SKUs they need.
“Previously we worked with an Excel table,” says the manager. It was a table where operators wrote down which products had been received, the customer they had come from, their SKU, turnover, etc.
With the installation of Easy WMS, the company has taken a step forward in goods management. “The software distributes the pallets based on different parameters, such as demand level,” says Largeron. Thus the system knows the exact location of each item.
The organisation of the operation and the workers must also be taken into account when perfecting picking. That’s why Easy WMS acts as a warehouse manager, telling operators what to do with each product at all times.
In this warehouse, orders are prepared in waves, that is, several orders are packed at the same time to optimise operator routes through the warehouse.
Operators use radiofrequency terminals to communicate with the WMS in real time and to receive orders and confirm that they have been fulfilled. “They love this system because its interface is very intuitive,” says the manager. They also use carts that have between four and ten slots, each of which is usually earmarked for an order. When orders are smaller and include small products, such as cologne jars, 30 orders can be prepared simultaneously (three per space).
“We’re more productive and almost error-free,” enthuses Thomas Largeron. “We used to print the Excel table so that the operators knew which orders to prepare, which was very time-consuming. At most, we were able to ship 150 orders a day, which is a far cry from the 500 we are currently closing,” he adds.
One of La Ruche Logistique’s objectives with this new project was to eliminate errors and, as a result, raise customer satisfaction. Thomas Largeron explains: “Before implementing Easy WMS, there were errors in two or three orders per day on average. Now, they are really exceptional (one every two weeks at the most).”
Efficient delivery service
With the rise of e-commerce, users are demanding that order deliveries adapt to their lifestyles, without waiting the slightest bit to receive them. With a situation like this, a logistics operator must offer very short delivery times: a matter of hours or the next day. To achieve this, it is essential for the workflow to be well organised and for fulfilment to be agile.
With this premise, La Ruche Logistique has implemented Multi-Carrier Shipping, an Easy WMS module that manages the packaging and labelling processes. In addition, the WMS can communicate with the shipping agency that distributes the orders. This program allows:
- Control of the number of packages so that the transport agency knows in advance how many boxes make up each order.
- Printing the necessary documentation, either the labels for the carrier, or the delivery note.
- Confirmation of the tracking number. This is a code with which end customers can track the shipment.
“Thanks to Multi-Carrier Shipping, Easy WMS communicates directly with our carrier to inform them of the orders to be distributed,” says Thomas Largeron. Smooth, two-way communication between the transport agency and the WMS avoids errors and shipment delays.
Thomas Largeron - Manager of La Ruche Logistique
“Mecalux has kept its promises. With Easy WMS and Multi-Carrier Shipping we are more productive, faster in the preparation and distribution of orders, we have optimised the storage space and, above all, we no longer make mistakes.”
The moment for growth
La Ruche Logistique has transformed its business with the installation of Easy WMS. One of its priorities was to optimise goods management, something it has achieved with the Mecalux WMS. According to Thomas Largeron, ““we offer complete traceability to our e-commerce customers.”
The company has achieved unlimited possibilities for expansion because, in the words of the manager of La Ruche Logistique, ““our turnover has increased in the last two years and should maintain that trend in the next three or four years.”
Advantages for La Ruche Logistique
- Total traceability: Easy WMS carries out a very strict control of the 12,000 SKUs stored from the moment they arrive at the distribution centre.
- More fluid dispatch: with Multi-Carrier Shipping, the order packaging and labelling processes are perfectly coordinated with transport agencies. This system communicates with carriers to inform them which purchase orders to distribute.
- More productive picking: Mecalux’s WMS tells operators how to prepare orders. Easy WMS supervision has helped them go from preparing 150 orders a day to 500.
La Ruche Logistique warehouse | |
---|---|
Warehouse dimensions: | 3,000 m² |
Number of SKUs: | 12,000 |
No. of packages received/day: | 200 |
No. of packages dispatched/day: | 150 |
No. orders prepared/day: | 500 |
Number of lines that make up the orders: | 3,000 |
Gallery
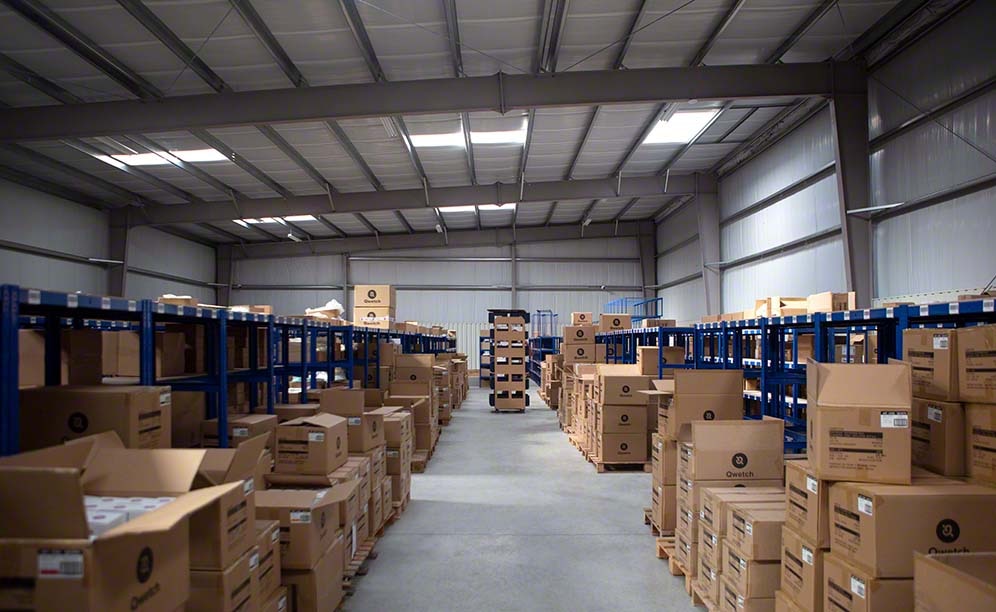
La Ruche Logistique warehouse in Pouilly-en-Auxois (France) with Easy WMS
Ask an expert