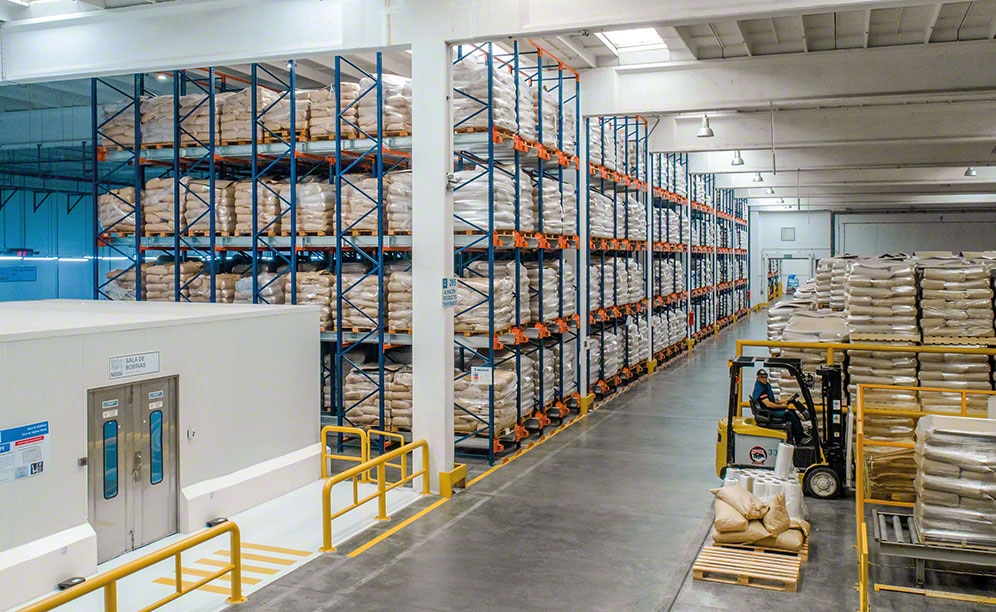
Nestlé is starting up a warehouse for the powdered milk line in Argentina
The Nestlé warehouse in Argentina is equipped with racks featuring the Mecalux Pallet Shuttle system
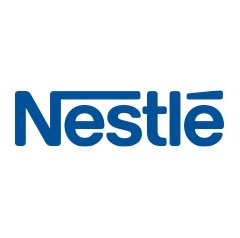
Nestlé has expanded its manufacturing plant in Villa Nueva (Argentina), dedicated to the production of powdered milk, chocolate milk and ready-to-drink beverages for children. In order to accommodate the increase in production, Nestle has opened a warehouse that Mecalux has equipped with racking featuring the semi-automatic Pallet Shuttle system. This solution takes advantage of the entire surface area and provides a storage capacity for 2,668 pallets, as well as agility in the entry and exit of 500 pallets per day.
Ninety years in Argentina
Nestlé is the world’s largest food and beverage multinational. Present in 197 countries, its goal is to inspire people to lead healthier lives. It has multiple brands that offer an enormous variety of products, including baby food, bottled water, breakfast cereals, coffees and teas, confectionery, dairy products and pet food.
Nestlé arrived in Argentina in 1930 and, since then, has been working to improve the quality of life of its clients. “We have been investing in this country for 89 years, something we consider a very special milestone,” says Claudio Marmo, Supply Chain Development Manager at Nestlé Argentina.
In addition to its headquarters in Buenos Aires, Nestlé has six plants located in Mendoza, Buenos Aires, Córdoba and Santa Fe, where it employs more than 2,000 people.
Expansion of the dairy market
In the city of Villa Nueva (province of Cordoba), “in one of the regions with the largest number of dairy companies in the country,” highlights Claudio Marmo, Nestlé has a production centre specialising in the production of powdered milk, chocolate milk and ready-to-drink beverages for children. These items are marketed in Argentina as well as in other Latin American countries.
This year, the production centre has been expanded with the incorporation of a new production line that allows 10 million litres of sterilised milk per year to be produced following the UHT (ultra-high temperature) method for brands such as Nesquik, Nido and NAN.
The only disadvantage of adding this production line is that it meant the loss of space dedicated to the storage of finished products. “We needed to recover storage capacity without having to build another building, and we didn’t want to resort to external warehouses either,” explains Claudio Marmo.
New Nestlé project
To resolve this situation, the company has just set up a warehouse right next to the new production line. The operators collect the products that come out of production and deposit them directly on the racks right in front of them. According to the director of Supply Chain Development, “we have optimised product movements. In short, the internal logistics of the production centre.”
For this warehouse, Nestlé was looking for a solution that would help it maximise space and also adapt to the specific features of its products, “with variable dimensions and seasonal sales,” says Claudio Marmo. That is why it came to Mecalux for advice.
The two multinationals have collaborated on multiple projects in Argentina, as well as in different countries where they are present (for example, Mecalux equipped a Nestlé warehouse in Chile dedicated to its pet food line and another in Spain for its coffee brand in capsules).
“We contacted Mecalux because of the good experience we have with them and because we know the quality of their products and the commercial reliability for which they are renowned as suppliers. For this new project, it was very clear to us that the warehouse should have the most automatic operation possible,” points out Claudio Marmo.
In view of this request, Mecalux proposed equipping the warehouse with high-density racks with the semi-automatic Pallet Shuttle system for two reasons: for one thing, the racks take advantage of the available warehouse space and provide as much storage capacity as possible and, for another, this solution greatly streamlines storage tasks.
The racks measure 8 m in height, with four levels, and accommodate 2,668 pallets. The goods are managed according to the FIFO (first in, first out) principle, i.e. the pallets are inserted through the loading aisle and removed at the opposite aisle (closer to the loading docks), thus offering perfect product turnover.
Each day, the warehouse receives an average of 200 pallets (150 of powdered milk and 50 of ready-to-drink beverages) from production. Subsequently, between 250 and 300 pallets are distributed to customers in Argentina and Latin America.
The Pallet Shuttle is an ideal solution to cope with this workload. It is a system capable of minimising operator manoeuvres and speeding up pallet entry and exit. The operators do not go into the lanes to handle the goods, rather the shuttle executes the movements automatically.
The operation of the Pallet Shuttle is very simple and, in the words of Claudio Marmo, “the operators became familiar with the system after a very short period of time.” The operators, with the help of reach trucks, place the electric shuttle in the corresponding channel. They then place the pallets in the first position on the racks and the shuttle moves them to the next free slot within the channel. The reverse operation is performed to remove the goods.
Claudio Marmo - Supply Chain Development Manager Nestlé Argentina
“We have worked with Mecalux on numerous occasions, so we know the quality of their products and the reliability for which they are renowned as suppliers. The new warehouse was designed to meet our needs: to expand storage capacity without having to build another building.”
Flexible logistics
Nestlé’s new warehouse is designed to store all the products produced in the Villa Nueva production centre. The installation of the Pallet Shuttle system has led to a breakthrough in the company’s logistics by meeting three of the goals set with this project: capacity, flexibility and agility.
The racks take advantage of the entire storage space to accommodate the largest number of products. In addition, they adapt to the different types of articles managed by the company (powdered milk sacks, the most heterogeneous article combinations, etc.) and, thanks to the motorised shuttle, the flow of movements is constant. The opening of this warehouse has been a turning point for Nestlé.
Not only has it incorporated another production line into its business, but it has also modernised its logistical processes in order to better serve the needs of its customers in Argentina and Latin America.
Advantages for Nestlé
- Warehouse next to production: the racks are right in front of the production lines, so the operators pick up the pallets and bring them directly into their slots very quickly.
- Continuous flow of goods: the Pallet Shuttle system facilitates the entry of 200 pallets and the exit of another 250-300 daily.
- Space optimisation: in total, the racks with Pallet Shuttle offer storage capacity for 2,668 pallets loaded with powdered milk, chocolate milk and ready-to-drink beverages for children.
Nestlé warehouse | |
---|---|
Storage capacity: | 2,668 pallets |
Pallet sizes: | 1,000 x 1,200 mm |
Max. pallet weight: | 1,000 kg |
Rack height: | 8 m |
Gallery
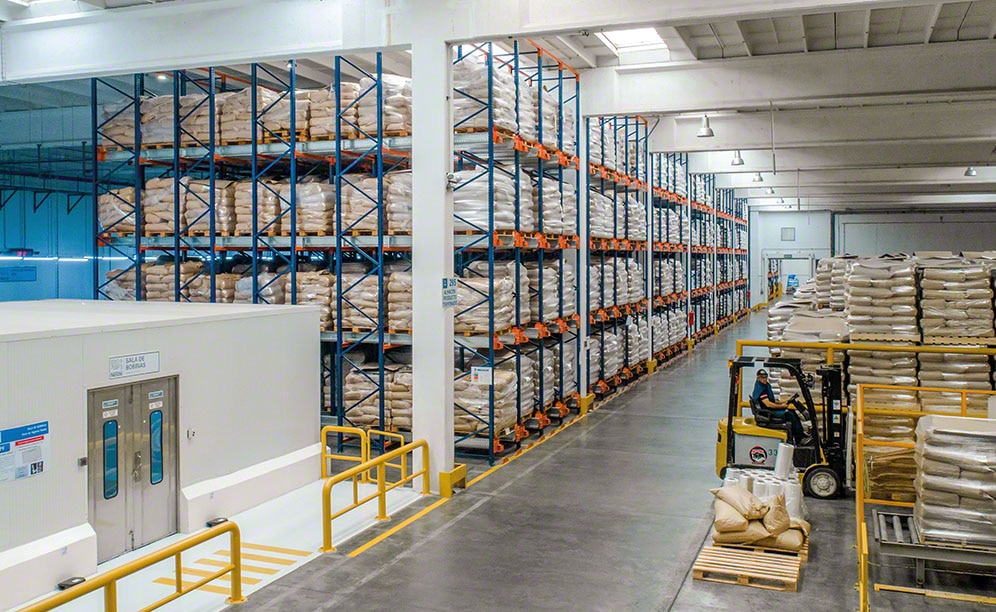
Nestlé warehouse in Argentina with semi-automated Pallet Shuttle system
Ask an expert