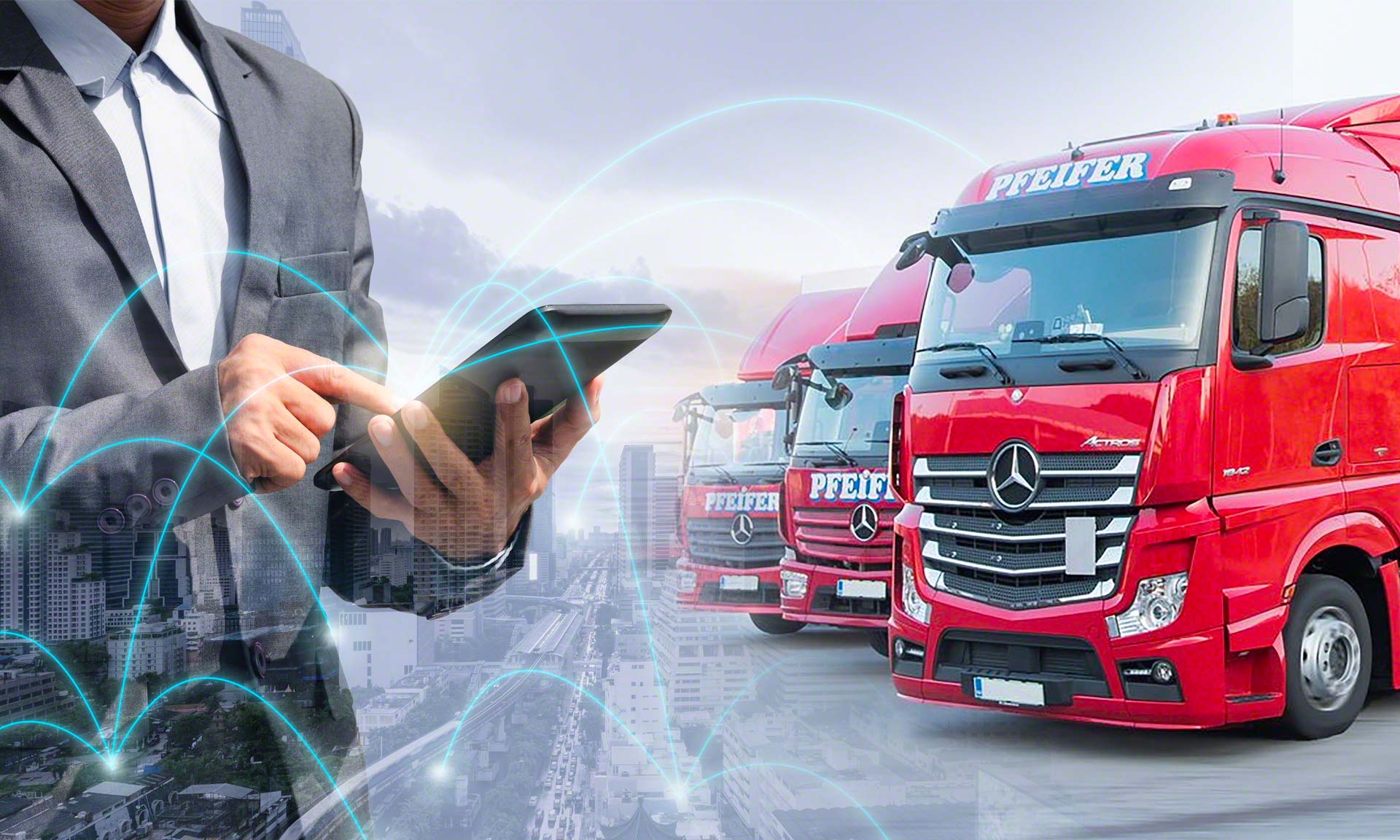
Pfeifer: technology for a 3PL in expansion mode
Easy WMS has the ability to adapt to changes in Pfeifer's warehouse
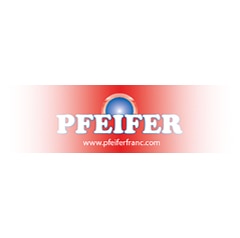
Logistics provider Pfeifer has its foot on the gas. The company, dedicated to 3PL (third-party logistics), grew by 40% in 2020 and is currently developing at an unprecedented rate. To bolster its future prospects, Pfeifer has digitised its facility in Nazarje, Slovenia, with the Easy WMS warehouse management system from Mecalux. This software provides total control of the 3,700 SKUs belonging to the company’s different customers and sends precise instructions to operators on how to perform each task.
Pfeifer was founded in Slovenia at the beginning of the 1970s. With over 100 employees and 10,000 m² of storage area, the firm provides logistics and transport services to all kinds of companies.
The Slovenian region of Nazarje is home to one of the company’s largest warehouses (2,300 m²), where it stores its customers’ products.
One of the problems Pfeifer was facing in its day-to-day activities was how to manage the increasing volume of goods while maintaining speedy deliveries. The facility accommodates 6,500 pallets with 3,700 SKUs of varying characteristics, turnovers and storage requirements.
New warehouse management system
“When our customers’ production rate went up, we realised we were struggling to cope with the rise in demand. The management software we’d been using to organise operations in our facility had become obsolete,” says Franci Pfeifer, Head of Logistics.
The company decided to start looking for a more modern warehouse management system that would reorganise and optimise its operations in its facility. “We turned to Špica because it’s a technology company with an excellent reputation in Slovenia. They’re extremely receptive and flexible professionals with expertise in modern supply chain solutions.”
Špica analysed Pfeifer’s needs and came to the conclusion that the 3PL provider required management software agile enough to adapt quickly to market needs. Špica had one solution in mind: Easy WMS, the warehouse management system from Mecalux.
"What we liked most about this solution is its adaptability to the changes in our warehouse, such as the increased demand. We were also pleased that it was intuitive and user-friendly. The new warehouse operators needed minimal training to work with this tool,” affirms Pfeifer.
Efficient organisation of operations
Easy WMS manages all processes in Pfeifer’s facility. “The software from Mecalux gives us strict and effective control of all warehouse operations. We use Easy WMS to oversee and optimise processes such as goods receipt, inventory and dispatch,” says the Head of Logistics.
Easy WMS monitors the goods rigorously, from their arrival through to their shipment. “The software has provided us with total visibility of our stock in real time,” adds Pfeifer. Easy WMS controls the traceability of the goods: it knows exactly where each pallet is located and which processes it has undergone before being dispatched. Armed with all these data in the warehouse management system, Pfeifer can inform its customers of the status of their products.
These RF scanners receive detailed instructions from Easy WMS such as which aisle and location the operator should go to in order to store or remove a pallet. This way, they can complete their tasks faster and without making mistakes.
How does Easy WMS supervise all the operations in the Pfeifer warehouse?
- Goods receipts: Every day, the facility receives 400 pallets from customers. The operators identify each item (by reading the barcode with their RF scanners), and Easy WMS assigns the products a location.
- Storage: Easy WMS uses algorithms and parametrisable rules to assign the pallets a slot, taking into account the customer to which it belongs, its characteristics and its demand level. Next, the operators move the pallets to the corresponding location.
- Order preparation: Most of the pallets are dispatched without having to be broken down; only 15% of the stock is shipped in smaller quantities. For these cases, Easy WMS tells the operators where to locate the items and how many to extract from each pallet. These products are then labelled before being loaded onto the delivery lorry.
- Dispatch:The pallets to be shipped - around 400 a day for customers in Slovenia and throughout Europe - are sent to the staging area, where they are grouped by order, customer and transport route. Finally, Easy WMS generates a delivery note for the carrier specifying the pallets included in the delivery.
Software for thriving logistics
Pfeifer is growing at a fast pace. More and more companies in Slovenia and throughout Europe are requesting the services of this 3PL provider because of its professionalism, speed and security when managing its customers’ goods.
Pfeifer has digitised its warehouse in Nazarje with a single goal in mind: to bolster its future growth perspectives. “Despite the difficulties brought on by the coronavirus pandemic, in 2020, our business increased by 40%. In 2021, we hope to grow by 50% compared to last year,” says the company’s Head of Logistics.
Pfeifer has a promising future, with several exciting projects planned, including the expansion of its corporate headquarters and the opening of additional warehouses in Slovenia. One thing Pfeifer knows for certain is that technology will play a part in all its projects. With Easy WMS software, the company now has an efficient supply chain capable of meeting the needs of its customers with no margin for error.
Špica suggested Easy WMS as a future-forward solution for our company. The characteristic that most impressed us in terms of this software is its flexibility and adaptability to our business. We’d also highlight its user-friendly interface. With the help of Easy WMS, we have complete visibility of stock in real time.
Advantages for Pfeifer
- Full traceability: Easy WMS monitors the 3,700 SKUs stored from the moment they arrive at the facility until they are dispatched to be delivered to customers.
- Flexible solution: Easy WMS software is capable of adapting to the particular characteristics and requirements of the business. Pfeifer has installed it in its warehouse in Nazarje with a view to further digitising its future centres.
- Intuitive software: the WMS stands out for exceptionally intuitive, user-friendly interface. The system sends instructions to the operators on how to perform each task quickly and without error.
Ask an expert