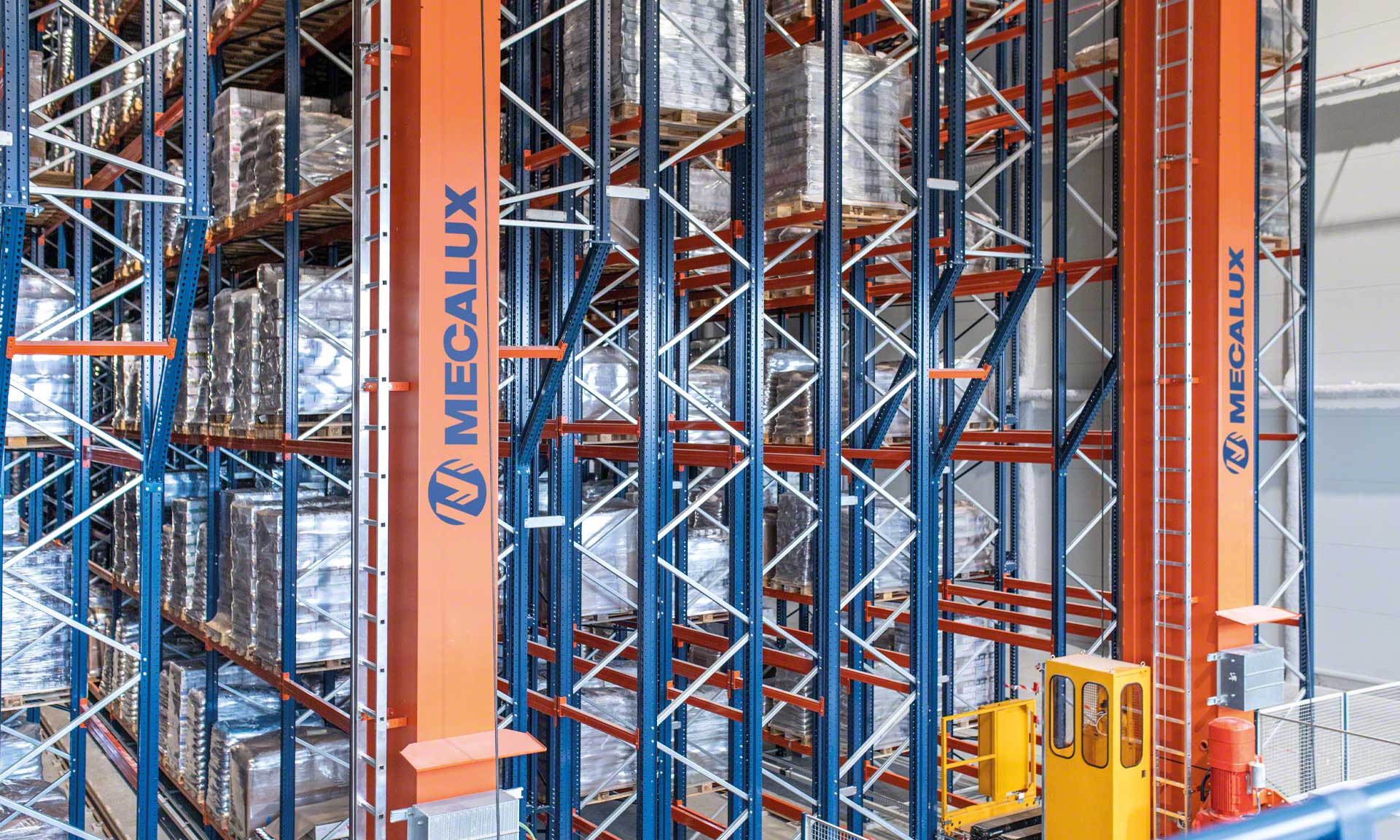
French canned foods producer Sabarot leaps into automation
French canned goods producer Sabarot Wassner has centralised its logistics operations with an AS/RS for pallets.
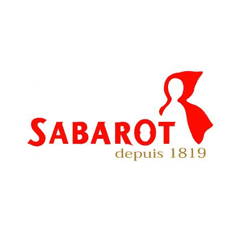
Sabarot, a French company dedicated to the production and distribution of cereals, has centralised its logistics operations with an AS/RS for pallets. Supervised by Easy WMS warehouse management software, the AS/RS is ready to be expanded if Sabarot's future needs require this.
200 years of experience
With over 200 years of experience, family-run business Sabarot offers a wide variety of legumes, cereals and seeds, including Puy lentils and spelt from Velay. It also specialises in mushrooms and escargots. Sabarot selects the best varieties by promoting its associated producers through channels that guarantee the origin and quality of each harvest.
- Founded in: 1819
- International presence: 70+ countries
- Production capacity: 30,000 tonnes/year
CHALLENGES
|
SOLUTIONS
|
BENEFITS
|
---|
French company Sabarot, a producer and distributor of cereals and legumes — i.e., its popular Puy lentils and spelt from Velay — has seen steady annual growth of about 15% over the past 15 years. On a logistics level, this business growth led the company to centralise all its logistics operations, particularly, the storage of the entire production volume.
Sabarot CEO Antoine Wassner says: “Like all companies, we were affected by the coronavirus pandemic. Global economic activity was halted for a time, despite the fact that the food sector has always been essential. The pandemic made us see that both our production and logistics chains had to be more competitive to respond quickly to customer demand.”
Determined to put an end to the cost overruns involved in outsourcing its warehousing needs, Sabarot has centralised all logistics operations in its historic centre in Chaspuzac (France). There, it produces, stores and distributes its goods to customers in over 70 countries. Its main markets are France and the UK, although it also exports its products to countries such as Malaysia, the United Arab Emirates and Singapore.
“We turned to Mecalux once again because we needed to automate to improve our operations. We’d worked with Mecalux before, so we had no doubts when it came to our choice. In fact, we’ve been working together for over 20 years, installing different storage systems. We began by putting in pallet racking and then Movirack mobile racking.”
The most recent project carried out by Sabarot and Mecalux constitutes the construction of an automated storage and retrieval system (AS/RS) managed by the Easy WMS warehouse management system and designed to accommodate finished goods from the production lines. “We’re thrilled with the assembly and start-up of our new logistics automation project because Mecalux implemented it extremely quickly,” says Wassner.
State-of-the-art warehouse
The new AS/RS, with capacity for 6,376 pallets on 21.5-metre-tall racks, stands out for the length of its two aisles: 92 m. A stacker crane operates in each aisle. Following instructions from Easy WMS, these machines are charged with storing, removing and transporting pallets autonomously. Another particular characteristic of this AS/RS is that, at the request of Sabarot, it is prepared to operate at a frozen temperature (-5 °C) as well as at ambient temperature.
The racks installed are double-deep, i.e., they can store two-pallets deep on each level, thus doubling capacity. To access the second pallet, the stacker cranes are equipped with telescopic forks to be able to handle two pallets at a time. Easy WMS is configured so that both positions store pallets of the same SKU, avoiding unnecessary movements. Likewise, the racking locations have been personalised to accommodate pallets of two different sizes and with loads of three possible heights.
In front of the racking, automatic pallet conveyors have been set up to connect the AS/RS with the loading docks and the receiving stations where the goods arrive from production by means of AGVs.
“Not only have we automated the storage process with the stacker cranes, but we’ve also integrated automation in the dispatch of pallets to the loading docks,” says Wassner. In the docking area, Mecalux set up four live preload channels, each with capacity for 17 pallets. The total capacity of these channels (68 pallets) is equivalent to that of two freight lorries.
Sub-zero storage
The Sabarot centre also has a freezer warehouse operating at -20 °C and equipped with Movirack mobile racking. The racks are installed on mobile bases that move sideways autonomously. To open the required aisle and remove or deposit the goods in their locations, the operator merely has to give the command by means of the radio control device. “The mobile racks have enabled us to significantly optimise our storage space compared to adjustable pallet racking. The Movirack system is ideal for cold storage, where energy savings and, hence, costs savings, are a key issue,” says Wassner.
Movirack mobile racking is the only compact storage system that offers direct access to all the pallets stored. With capacity for 1,816 pallets, the Movirack racking leverages all the available surface area to optimise the storage of finished products prior to their shipment to customers.
Easy WMS: warehouse management
“Easy WMS from Mecalux is one of the cornerstones of our logistics operations. We could say it’s like the conductor of an orchestra. It’s responsible for integrating any new product into the flow of goods,” says Wassner.
Sabarot needs to control all its items in real time to minimise mistakes and ensure complete traceability of its 7,800 SKUs. To connect the AS/RS with the other processes in the production plant, Easy WMS is integrated with the software that manages the AGVs and also with Sabarot’s ERP system.
“The permanent connection between the AS/RS and the production lines — both physically via the AGVs and digitally with Easy WMS — allows us to ensure full traceability of all our products. All processes are strictly parametrised to ensure maximum logistics efficiency,” says Wassner.
To introduce raw materials into the AS/RS, the AGV deposits pallets on the conveyors, where they have to pass through a checkpoint to verify that their size and weight correspond to the requirements established for their entry in the AS/RS. This process also serves for Easy WMS to identify which items have arrived so that it can apply rules and algorithms to assign them locations in line with their characteristics.
“In terms of pallet outflows, Easy WMS has helped us to dispatch our products more quickly. The software optimises the preparation of all documentation so that customers receive the correct products in the quantities ordered,” says Wassner.
Future-ready warehouse
The new AS/RS not only matches Sabarot’s current logistics needs, but is also prepared to support business growth. During the design phase and throughout assembly, Mecalux and Sabarot took into account a two-phase future expansion that could triple both the current throughput and storage capacity, accommodating up to 20,000 pallets. The safety and effectiveness enabled by technology are fundamental for Sabarot’s day-to-day activities. With this new AS/RS and the modernisation of the entire Chaspuzac plant, the company can continue to provide its customers around the world with healthy, natural and quality products.
Automation and, in particular, the Easy WMS software, have helped us to improve our storage organisation. As a food business, it’s vital for all our products to be strategically located. With Easy WMS connected to all the automated elements in our centre, we’ve saved time and are more efficient in our goal to satisfy our end customers.
Gallery
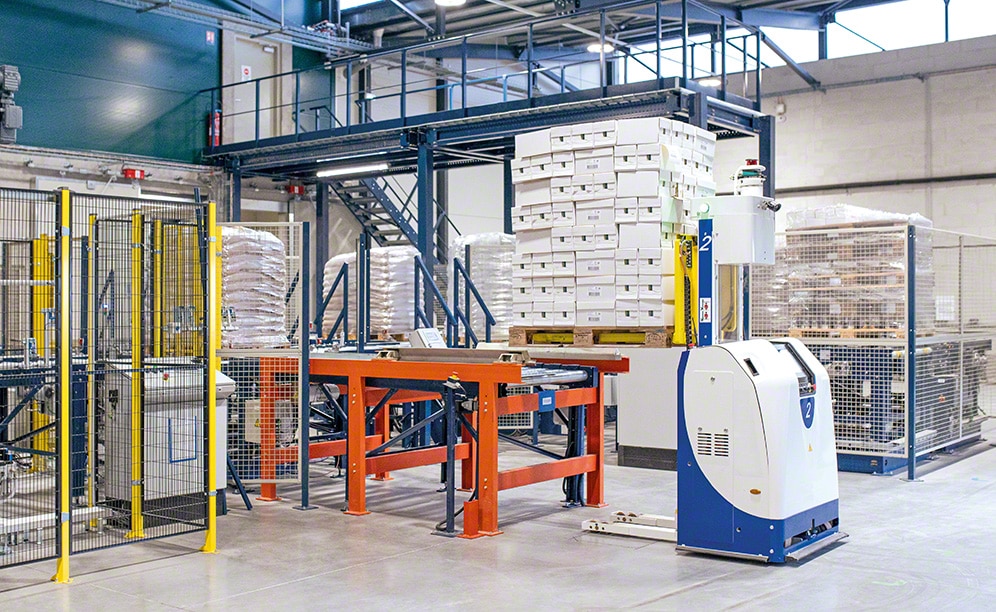
Automation has boosted the logistics operations of cereal producer Sabarot
Ask an expert