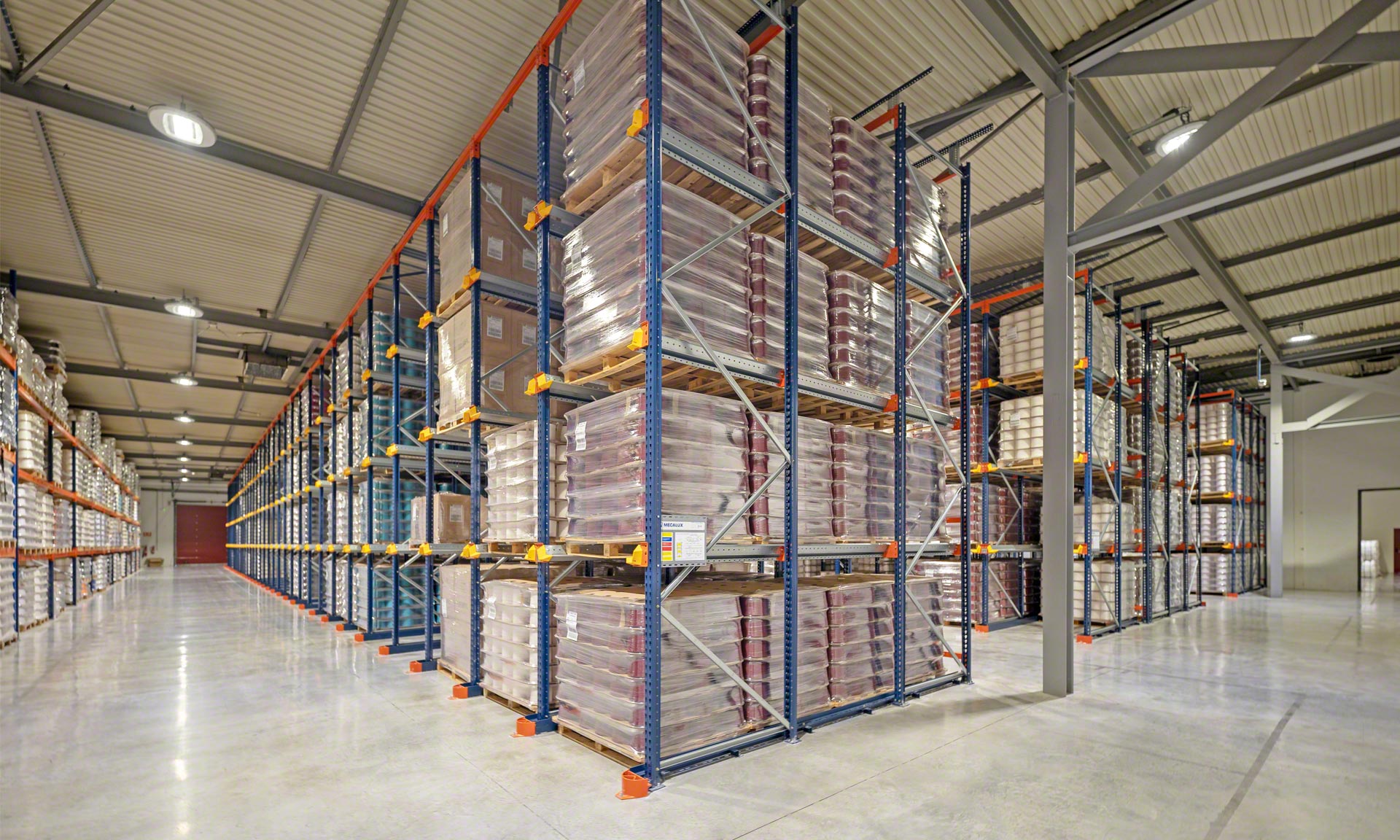
Selvafil modernises and leverages all its warehouse space
The racks have optimised the available space, enabling Selvafil to manage its products more efficiently.
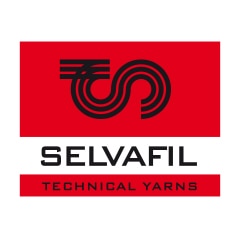
Technical yarn manufacturer Selvafil has opened a new warehouse in Maçanet de la Selva, Spain, to increase its storage capacity and provide its customers with optimal service. Mecalux has supplied the company with six compact pallet rack units that can accommodate a total of 2,784 pallets.
Weaving the future
Founded in 1973, Selvafil produces technical yarns used mainly by weavers and garment makers all over the world. With four production plants in Maçanet de la Selva, Spain, the business is approved to spin most of the technical fibres available on the market.
When fitting out its centres, Selvafil has always relied on technology: this guarantees the utmost quality of its products, minimises pollution risks and raises productivity. In fact, Selvafil boasts the most modern and automated staple fibre spinning plant in all of Europe.
Selvafil debuts a warehouse
The business is noted for updating its installations regularly with a view to adapting its processes to new market demands. From the outset, its sights have been clearly set on the international stage. Today, 80% of its production is sold abroad (above all, in Europe, but also in China, India, Australia, South Africa and the US).
Recently, the company has started up a new warehouse very close to its installations in Maçanet de la Selva. Initially, this building belonged to another firm, and, when it closed, Selvafil purchased it. “With this installation, we were looking to boost our storage capacity,” says Ivan Bohigas, Director of Operations at Selvafil.
When it came to equipping this facility, Selvafil knew just who it would count on: Mecalux. The two companies had worked together in the past on other projects, installing storage solutions in the central warehouse in Maçanet de la Selva (pallet racks, drive-in racking and picking shelves).
For this new facility, Mecalux once again suggested installing drive-in pallet racking. “These are the ones that best meet our needs: they’ve really leveraged the space we had, and they’ve provided us with the capacity we needed to supply our customers,” adds Bohigas.
Racking characteristics
The warehouse comprises six high-density drive-in racking units with a total storage capacity of 2,784 pallets. These racks are used to hold Selvafil’s finished products, “mainly yarn cones on pallets, ready to be distributed to its customers when required,” explains Ivan Bohigas.
The racks are made up of lanes with four levels, each measuring 5.5 m tall. Each level is composed of support rails on each side, which hold the pallets in place. They are made from galvanised sheet steel and have a triangular shape to easily centre the pallets.
With this storage system, only one aisle is needed for loading and unloading goods. Aided by counterbalanced forklifts, operators enter the lanes with the merchandise raised above the level where it will be deposited.
We’re pleased with the new warehouse because it gives our company a truly contemporary look. Plus, Mecalux’s racks have notably increased our storage capacity. They’re resistant, high-quality structures that have improved safety when storing products.
Advantages for Selvafil
- Increased storage capacity: Selvafil has achieved one of its main goals by opening this installation, raising its storage capacity. These accumulative racks can accommodate up to 2,784 pallets, thereby providing better service to its customers.
- Space optimisation: the racks maximise the available storage space and only require one aisle for pallet loading and unloading.
- Proper goods distribution: the warehouse is well-organised, taking into account product turnover to facilitate storage tasks.
Warehouse of Selvafil | |
---|---|
Storage capacity: | 2,784 pallets |
Pallet size: | 900 x 1,200 mm |
Max. pallet weight: | 350 kg |
Racking height: | 5.5 m |
Gallery
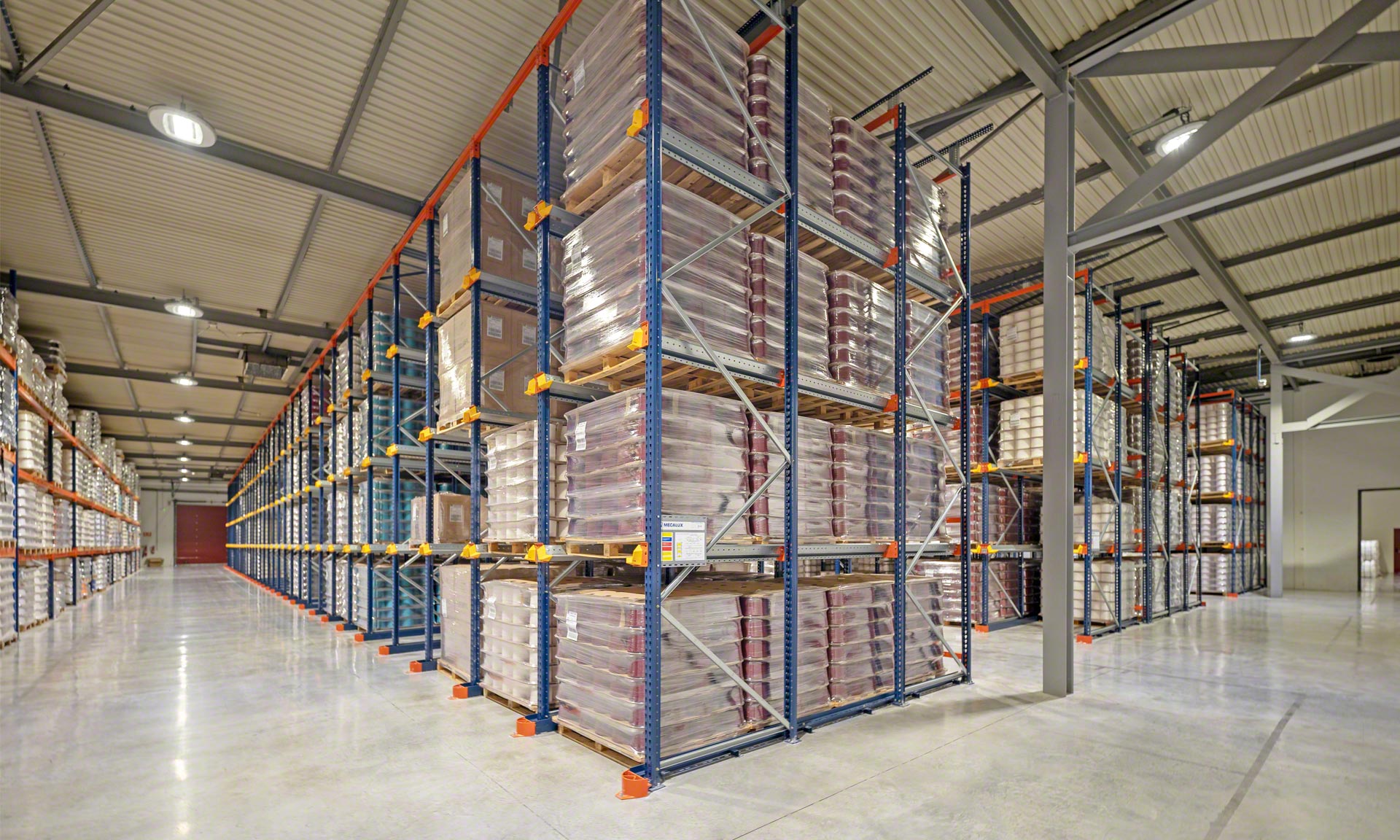
Selvafil's installation with drive-in racks in Girona, Spain
Ask an expert