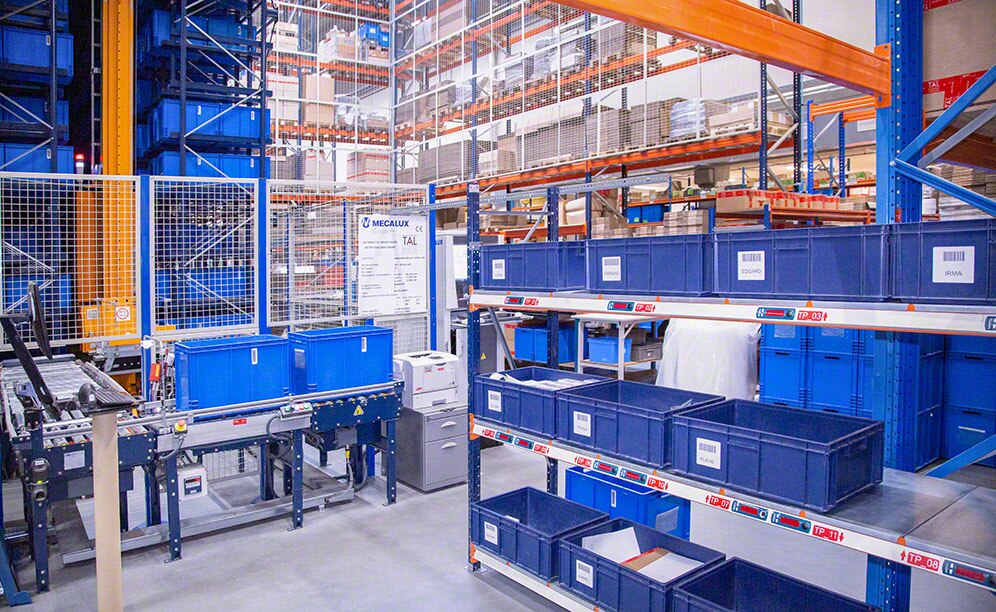
TAL: an automated warehouse shining through and through
Automation optimises space, ensures safe goods storage and minimises errors
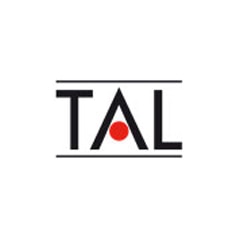
TAL, a Belgian manufacturer of high-quality lighting systems and accessories, has equipped its new distribution centre in Pittem, Belgium, with an automated warehouse for boxes. Its aim is to optimise space, ensure safe goods storage and minimise errors, ensuring the productivity required by omnichannel retail. Managed by Easy WMS, the facility holds approximately 1,400 SKUs in 6,300 boxes. Mecalux has also installed pallet and cantilever racks to store larger products.
Design, quality and innovation
TAL (Technical Architectural Lighting) is a renowned Belgian designer and manufacturer of high-end lighting systems. It works with LED, low-energy-consumption, halogen and fluorescent lamps, among others.
Founded in 1992 under the name Digilight, the firm began implementing its expansion plan in the early 2000s. Through hard work and dedication, it has become a benchmark company in the sector. Nearly half of its current turnover comes from the international market. TAL’s lighting systems are present in over 70 countries.
Sustained growth
If there is one word that defines TAL’s business philosophy, it is quality. For TAL, quality is non-negotiable; it is imbued in each and every one of its departments and operations, including logistics.
To improve the quality of its logistics processes and bolster its steady growth, the company has changed the location of its head office twice, always remaining in northern Belgium. Recently, it has opened a two-storey 8,000 m2 building in a business area in Pittem. The ground floor is home to all of TAL’s operations: production, assembly, storage and distribution. The upper floor houses offices and a 600 m2 showroom for its products.
TAL’s former warehouse had become overloaded, precluding the firm from moving forward with its growth plan. “Operations were 100% manual,” affirms Francis Deneckere, Operations Manager at TAL. Determined to change this dynamic, the business sought to automate its new warehouse with a solution designed for its finished products and components used in assembly. Deneckere states, “Our main logistics need was to optimise goods dispatch in terms of both flexibility and efficiency.”
Likewise, it was essential that the solution optimise storage space, in addition to increasing productivity, reducing errors and ensuring safe goods storage with high added value. The new installation also had to address the company’s omnichannel retail strategy and be efficient enough to supply distributors, online end-customers, lighting specialist shops, and so on.
High throughput in a small space
With all those requirements in mind, Mecalux decided to set up an automated warehouse for boxes on one end of the building, just beside the assembly area. Managed by the Easy WMS warehouse management system, the installation was designed to store small finished products as well as components needed for assembly.
With 10-metre-high racks, the warehouse occupies only 178 m2 of surface area. It can store up to 6,300 boxes weighing 40 kg each on 15 levels. This solution has a single 52.4-metre-long aisle, although there is still room for a second aisle if TAL requires it. A miniload stacker crane moves with full autonomy through the aisle, inserting and removing boxes into/from their corresponding locations as per instructions from Mecalux’s Easy WMS.
“The automated miniload warehouse has brought us huge benefits, among which I would stress error reduction and a notable increase in throughput. Now, we can carry out all our tasks more quickly,” enthuses Francis Deneckere, TAL’s Operations Manager.
The WMS organises the products and decides on a location for each of them. It does this based on rules and algorithms that take into account their particular traits and demand level. The distribution of the goods is intended to get the most out of the stacker crane, which is prepared to insert and extract 80 boxes/hour in combined cycles.
According to TAL’s Operations Manager, “A warehouse management system such as Easy WMS provides a whole host of advantages. Of all of them, I would mention the capacity to optimise storage location management.”
Easy WMS also brings great value to picking, keeping everything under control, from inventory to operator tasks. Through its connection with TAL’s SAP ERP, the WMS knows which orders have to be dispatched and which items are needed to prepare them.
The front of the automated warehouse is fitted out with a conveyor circuit that brings the boxes to the pick stations, following the product-to-person principle. Operators pick products from the boxes designated by the WMS and deposit them on the shelves just behind them, which are enabled to prepare up to 12 orders simultaneously.
Easy WMS guides the operators in order prep with the help of put-to-light devices. These are found on the front of each of the slots on the shelves and serve to show the number of SKUs to be put in each box. Once the operator has placed the item(s) in the box, he/she pushes the confirmation button to notify the WMS that the action has been completed and to receive more boxes.
Most SKUs stored in the miniload installation pertain to components used in the assembly area, located next to the automated warehouse. There, operators put together all the parts to form the lighting systems that will be subsequently dispatched.
Put-to-light advantages
- Productivity. It decreases the number of operator movements and eliminates the product-reading process.
- Error reduction. Goods verification is immediate, with correct-order rates of 99.5%.
- Real-time updates. Inventory data is updated in real time, as stock movements are transmitted to the WMS and recorded in the database.
- Optimal usability. Of the various picking support systems, it is the technology that requires the least training for operators.
Bulky product storage
In addition to the automated facility, Mecalux installed manual storage systems for housing goods of larger sizes.
On the one hand, it set up racks measuring 10.5 m tall that can accommodate more than 1,000 pallets with a maximum unit weight of 650 kg. The versatility and sturdiness of these racks makes it possible to adapt and use the storage levels according to the company’s needs. For example, on many of the lower levels of the racks, picking is done directly from the pallets, with reserve pallets placed on the upper levels. Finished products and materials used for dispatch (e.g., cardboard boxes) are also stored on these racks.
On the other hand, products that are even bulkier, especially in terms of length, are deposited on 7-metre-high cantilever racks. This storage system is made up of columns and a number of cantilevered arms upon which the loads rest. TAL stores goods measuring up to 6.1 m long, such as pendant and ceiling lamps.
Illuminating the world
The growth achieved by TAL in recent years is a combination of work, passion and ambition to improve every day to provide more competitive and attractive lighting systems.
Throughout this journey, logistics — together with the production and assembly processes — has played a fundamental role. Therefore, the company continues to modernise its operations with a view to building a more competitive supply chain. Its new automated installation enables it to boost its throughput, minimise errors and ensure safe storage of its products in an optimised space.
Moreover, the implementation of Easy WMS provides TAL with traceability and more efficient inventory management, cutting logistics costs and speeding up warehouse operations.
We’re extremely satisfied with the operation of the automated warehouse for boxes from Mecalux. In addition to improving efficiency by speeding up operations and decreasing errors, we have complete stock control. Thanks to Easy WMS, we can consult our inventory from a computer at any time.
Advantages for TAL
- Increased productivity: the stacker crane removes and inserts 80 boxes/hour from/into the racks in combined cycles, continuously working 24/7.
- Space optimisation: in just 178 m2, TAL stores 6,300 boxes on 10-metre-high racks along a 52.4-metre-long aisle.
- Inventory management: Easy WMS ensures full control of the 1,400 SKUs stored, in addition to speeding up picking and minimising errors.
Automated warehouse for boxes | |
---|---|
Storage capacity: | 6,300 boxes |
Box size: | 400 x 600 mm |
Max. box weight: | 40 kg |
Racking height: | 10 m |
Racking length: | 52.4 m |
Gallery
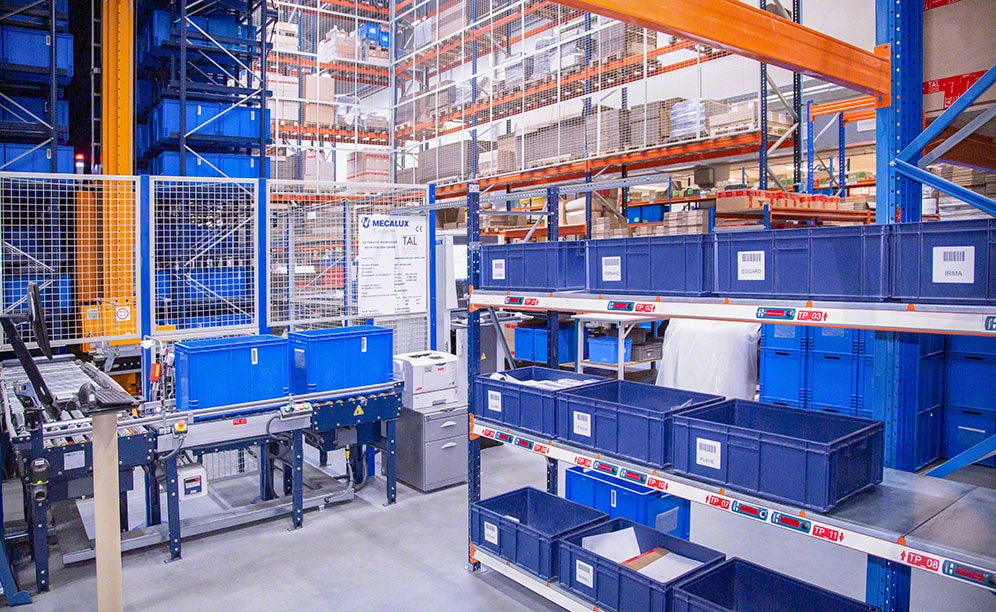
The new automated installation addresses TAL's omnichannel retail strategy
Ask an expert