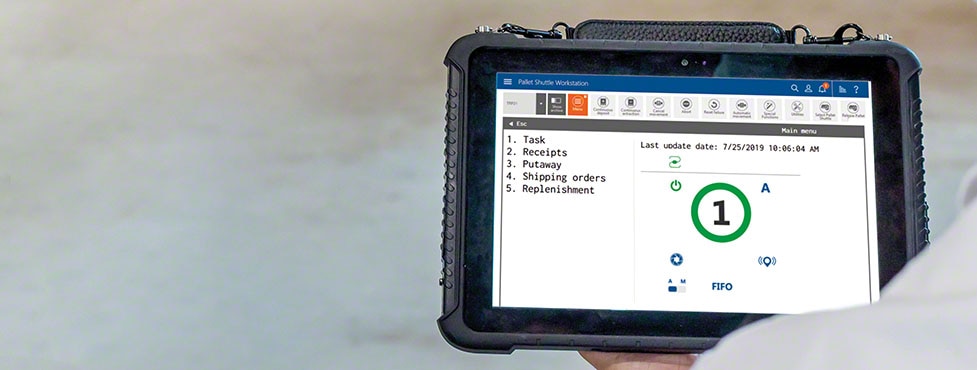
Viñas Familia Gil: controlled logistics for fine wine
Viñas Familia Gil stores nearly 12 million bottles of wine sold in over 40 countries
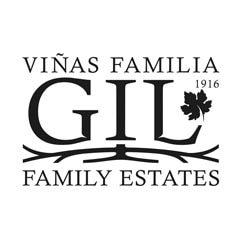
Wine company Viñas Familia Gil has bolstered the growth it has achieved in recent years with the construction of a new warehouse at its headquarters in Jumilla (Murcia, south-eastern Spain). In a surface area of 5,800 m¬, the firm stores 7,692 pallets, in other words, approximately 12 million bottles of wine that are sold in Spain and over 40 other countries. To optimise the storage area, Mecalux has installed the Pallet Shuttle system, pallet racks and its warehouse management software, Easy WMS.
Local varieties
The Italian poet Dante said, , “Wine sows poetry in hearts”; since it was founded in 1916, Viñas Familia Gil has been committed to making wine that awakens and appeals to all the senses.
Over the years, the company has been modernised and well-established. To make its wine, it uses traditional knowledge of the trade passed down from parents to children, in addition to the latest technological advances that ensure rigorous wine temperature control and excellent hygiene conditions. The result could not be better: exceptional wine internationally renowned for its quality.
Since 2002, the business group has strengthened its expansion strategy and increased its product portfolio, incorporating wines of extremely diverse characteristics and designations of origin. It currently has a total of 12 wineries in 11 designations of origin, and its own vineyards, spanning over 1,800 hectares all over Spain.
Revamped logistics
By broadening its portfolio of SKUs, Viñas Familia Gil has also strengthened its presence in the market. Apart from in Spain, its wines are also consumed in around 40 countries, particularly in Europe as well as in the US, Canada and China.
To cope with this expansion, the company has just opened a new 5,800 m2 installation in the city of Jumilla, where it accommodates production for all its wineries throughout Spain. This facility acts as a central warehouse, organising all the finished products from different origins and dispatching them to customers at just the right time from the same logistics centre.
According to Diego Lozano, Operations Manager at Viñas Familia Gil, the company was certain about one thing: “The new installation had to not only provide us with more capacity compared to the current warehouse, but also be equipped with a system that would maximise operations and guarantee efficient goods dispatch. We wanted the WMS to tell us what and how many items we had, as well as their location in our facility. All these needs were perfectly covered by Mecalux’s Easy WMS.”
Every day, the flow of pallets from other wineries and dispatched to customers accounts for around 250 units. Taking into account this amount of work, Mecalux has fitted out the installation with the following logistics solutions:
- Pallet Shuttle system. This is ideal for storing multiple pallets of the same SKU. A motorised shuttle automatically inserts and removes the goods from their locations.
- Pallet racks. A temporary storage area has been set up.
- Easy WMS warehouse management system. This supervises all operations taking place in the installation and coordinates product inflows and outflows.
- WMS and Pallet Shuttle integration. A specific Easy WMS software module manages all Pallet Shuttle system operations.
Pallet Shuttle system
The warehouse consists of four racking units measuring 12 m high and 11.4 m deep. With a total of 400 locations, 4,800 pallets with a maximum unit weight of 1,425 kg can be stored. Each channel can hold between 10 and 12 pallets deep of the same SKU. Pallets with wine bottles will remain there for a particular time depending on customers’ needs.
The Pallet Shuttle is a high-density system that leverages the available storage area and increases capacity.
Goods management is carried out according to the FIFO (first in, first out) criterion; that is, the pallets with wines that have been bottled before are the first to be stored and dispatched. To prevent interference between operations, the pallets are inserted on one side of the racking unit (the one closest to the side of the installation). They are removed on the opposite side, coinciding with the central warehouse area, where the picking and stretch wrapping tasks are performed.
WMS and Pallet Shuttle integration
The installation is equipped with specific software for managing the Pallet Shuttle that is integrated with the warehouse management system. With this module, the WMS can control all warehouse processes, including the movements of the motorised shuttles.
Operators use a WiFi-connected tablet to give orders to the shuttles. With their extremely intuitive interface, workers can carry out a multitude of functions. For example, they can select the amount of pallets to be inserted or retrieved, take inventory and order pallets to be accumulated in a single channel. While loading and unloading pallets, operators can simultaneously consult the orders they need to execute next.
Comprehensive production control software
There is no doubt that the Viñas Familia Gil installation is highly complex. In a single space, it houses all production from the group’s various wineries in different wine-producing areas across Spain (up to 700 SKUs). Accurate control of each bottle and box of wine and of all movements taking place in the warehouse is indispensable for providing excellent service.
One of the company’s priorities is traceability, that is, rigorously monitoring the goods, knowing the exact amount of time each bottle has been stored and tracking the products’ path.
To monitor its installation and ensure full traceability of its goods, the company knew it needed to implement a warehouse management system (WMS). “After weighing different options, we decided to go with Mecalux’s proposal and its Easy WMS software; although it was not the most economical in terms of the initial investment, we were sure it would be in the short and medium term. Right away, we saw that it was the solution that best fit our organisation’s needs. Among other operations, it can optimise movement and guarantee traceability and speed in executing tasks. Plus, it enables us to perform receipt processes for all the goods from the different work centres efficiently, knowing ahead of time all the information on the products we are expecting.”
Easy WMS has been integrated with the Navision ERP at Viñas Familia Gil. In this way, the ERP can transfer data and information to the WMS to request orders that need to be dispatched in a timely fashion. The result is enhanced productivity and full assurance that operations in the installation are geared towards meeting customer needs.
Easy WMS intervenes in all warehouse processes:
Goods receipts
The ERP informs Easy WMS in advance of the products that are about to arrive at the installation from the company’s other wineries (this is known as Advanced Shipping Notification or ASN). In doing so, the WMS has all the data on the goods and can begin to organise their distribution in the installation.
Once the pallets are received, the operators identify them with the help of radiofrequency terminals to verify whether the products match those previously indicated. As the terminals help the employees to work extremely quickly, their throughput is much higher and more efficient.
Sample storage and preparation
Easy WMS incorporates rules and algorithms to decide the best location for each pallet. This WMS recognises the date of production of each product and, thus, ensures that wines that were made before are stored first.
“One of the Easy WMS features that we are most satisfied with is the possibility of excluding specific pallets from the workflow. Although there are different reasons for this, the most common is that the wines need to remain in the bottle for a certain time before being sold. Therefore, the WMS blocks their availability and excludes them from the order inventory until they reach the stipulated time, which is established beforehand by the technical department of each winery,” explains Lozano.
On the other hand, the WMS also controls and maximises the work done in the installation. Easy WMS sends clear orders to operators, including, for example, tasks to replenish products used in picking. In this case, the commands are transmitted in line with warehouse priorities to make sure that one job in progress does not slow down the rest of the operations.
Dispatches
Easy WMS also organises goods dispatch, a vital process that must be carried out effectively to avoid delays and guarantee on-time deliveries to customers.
The system tells the operators which pallets need to be extracted from their locations and brought to the dispatch area. There, goods are grouped according to whether they correspond to the same order or with a view to streamlining their subsequent loading onto the lorry.
Fluid logistics, sip by sip
To produce quality wine, various factors have to come together. Amongst them are the origin and ripeness of the grapes and the proper storage, preservation, ageing, and distribution of the wine. A company like Viñas Familia Gil, with an increasingly larger international presence, is especially rigorous in carrying out strict process control up to the time the wines reach its customers.
For this reason, the company has transformed its installation in Jumilla and, hence, its entire logistics system, to bring together all its wine brands under one roof. Not only has it obtained greater storage capacity, but it can also monitor its goods more accurately.
According to Viñas Familia Gil’s Operations Manager, “The main advantage we have found with the start-up of this installation and the implementation of Mecalux’s Easy WMS warehouse management system is the considerable reduction in storage costs for each of our SKUs. At the same time, we can assure our customers that the wines they receive comply strictly with the conditions stipulated by the technical department for temperature, preservation and moment of consumption. Another added benefit of Easy WMS is how easy it is to know the location of all our stock in real time. In short, the WMS we have chosen lets us control everything.”
Diego Lozano - Operations Manager at Viñas Familia Gil
“Our day-to-day activities have confirmed to us that the commissioning of this installation and implementation of Easy WMS have allowed us to make a giant leap forward and given us a competitive advantage; they have simplified operations and internal management and provided our customers with an efficient supply chain. The knowledge, passion and respect we have for the field and the land is present in each of our processes — this helps us to give us the edge. We want to convey this spirit to our customers, and, to do so, it is important to offer them wine with the highest assurance of quality and preservation. They are the ones who, through their loyalty, put us where we are as a company. With the construction of this warehouse, we have come full circle with what started in the field, with the land.”
Advantages for Viñas Familia Gil
- Efficient management of all operations: Mecalux’s Easy WMS optimises the processes carried out in Viñas Familia Gil’s warehouse. It is also integrated with the Pallet Shuttle system to ensure its proper operation.
- Streamlined, high-density system: of all the high-density storage systems, the Pallet Shuttle is the most agile, facilitating the entry and exit of 200 pallets a day to and from the four racking units.
- Precision and flexibility: supervision of all operations by Easy WMS is essential for operators to perform storage and order prep tasks without making mistakes.
Pallet Shuttle system | |
---|---|
Storage capacity: | 4,800 pallets |
Pallet size: | 800 x 1,200 mm |
Max. pallet weight: | 1,425 kg |
Racking height: | 12 m |
Gallery
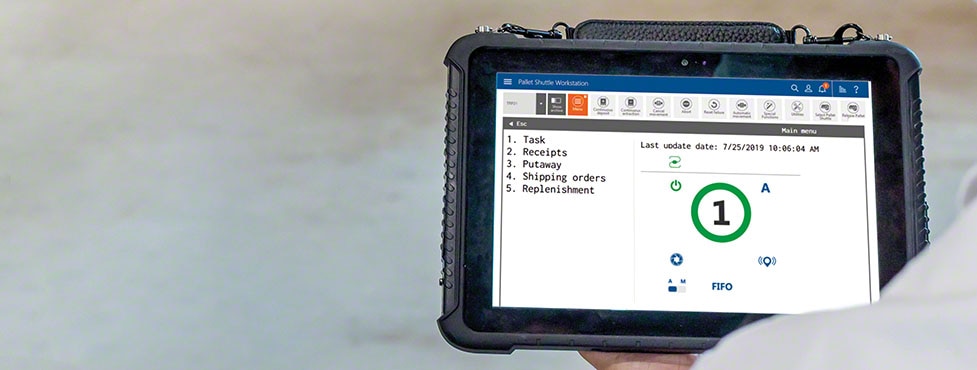
Easy WMS optimises operations at Viñas Familia Gil's warehouse
Ask an expert