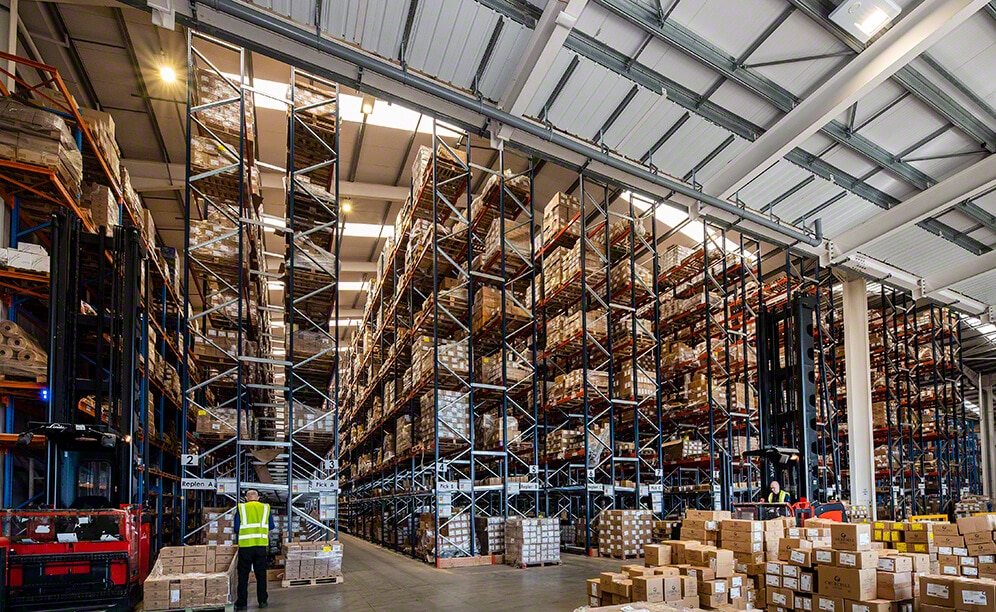
Churchill China warehouse in UK with ceramic tableware
Churchill China has increased storage capacity and streamlined order picking
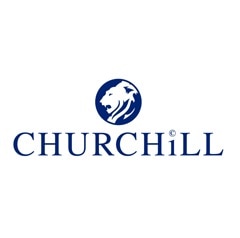
The versatility of Mecalux pallet racking is ideal for increasing storage capacity and, at the same time, streamlining order picking. The British company Churchill China has benefitted from this solution in its warehouse and, thanks to which, has increased productivity by 10% and space allocated to picking by 40%.
About Churchill China
Churchill China is a British ceramic tableware manufacturer with its headquarters in Stoke-on-Trent (UK). Its origins trace back to 1795, when it opened its first factory. However, it was not until 1984 that the company was renamed Churchill China. Currently, it combines its vast knowledge and expertise with state-of-the-art technology so that its products meet the highest standards in design, functionality and quality. The Churchill brand has achieved global recognition as a reputable supplier of high performance ceramics to the hospitality industry.
Finished product warehouse
The company has a 18,500 m2 warehouse facility next to its Stoke-on-Trent production centre. It is allocated to finished product that arrives from manufacturing, waiting to be distributed to its customers. Recently, it has worked alongside Mecalux to reorganise its space.
According to Jamie Clare, warehouse operations manager of Churchill China, “with this project, we plan to get better storage capacity and, at the same time, improve product organisation and distribution.” The company needed a system that would help efficiently manage the extensive SKUs and which would give them the means to prep a very high number of orders. Taking all of these features into account, Mecalux has installed pallet racks that fill almost the entire surface of the warehouse and provide storage capacity for in excess of 5,000 pallets. What is more, order picking takes place on the lower storage levels. To do so, live channels were enabled for both boxes and pallets.
“Due to the solution provided by Mecalux, there has been a significant increase in efficiency and productivity, which has reduced the cost per carton despatched,” explained Jamie Clare.
The warehouse has been sectored in order to organise all the products and ease the operators’ work. Certain products are grouped in each zone and assigned a specific number of operators to pick orders. All of these measures have contributed to improving picking and the installation’s productivity.
Maximum operational productivity
Pallets are deposited in the 11 m high racks, which flow from production and arrive on a daily basis to the warehouse. The proper distribution of this volume of products is vital to achieve the maximum productivity of all operations and to ensure good customer care for the clients.
Each day it distributes more than 100 pallets throughout the world. The racks offer direct access to the products, which helps the workers slot and retrieve loads from their locations easily. “This feature significantly reduces congestion, allowing for continuous inputs and outputs of the goods to be done,” pointed out Jamie Clare.
Besides being ready to carry out storage tasks quickly, in reality, the warehouse is designed to maximise order picking performance. A part of the lower storage levels contains live channels. Two pallets are inserted there, one behind the other, and the operators collect the SKUs that each order contains directly from the first pallet. Here is where consumer products are picked because, with this system, reserve products are available right behind. So, goods are always available, preventing service stoppages and stockouts.
There are also storage levels fitted out with carton live storage where it houses up to 32,670 boxes (max.). These comprise slightly inclined frames with roller tracks, meaning boxes slide via gravity. Boxes are inserted into the load aisle and extracted through the opposite side, i.e. the work aisle where the operators go about picking orders.
“With these picking solutions enabled, we have increased our warehouse’s productivity by 10% and the space allocated to picking by 40%,” specified Jamie Clare. The warehouse’s sectoring has also contributed to improved order picking, since each area has an assigned number of racks and operators. The warehouse’s sectoring and proper product distribution have helped to improve Churchill China’s productivity.
Jamie Clare - Warehouse Operations Manager of Churchill China
“We went through a tender process with five different storage system suppliers, in which Mecalux scored highest. We opted for Mecalux because its products are specifically designed for speed and facilitate order picking, the main operation we run in this warehouse.”
Advantages for Churchill China
- Prepping daily orders: the layout of the warehouse and merchandise were planned out so workers could put together a large volume of orders per day.
- Efficient work: the racks provide direct access to the pallets, which facilitates the inflows and outflows of the goods, as well as error- and interference-free order picking.
- Surface area purposing: the racks take up almost the entire 18,500 m2 surface area the warehouse inhabits.
Warehouse of Churchill China | |
---|---|
Storage capacity: | +5,000 pallets |
Pallet size: | 1,000 x 1,200 mm |
Max. pallet weight: | 2,000 kg |
No. stored boxes: | 32,670 |
Box size: | 300 x 300 mm |
Max. box weight: | 10 kg |
Racking height: | 11 m |
Gallery
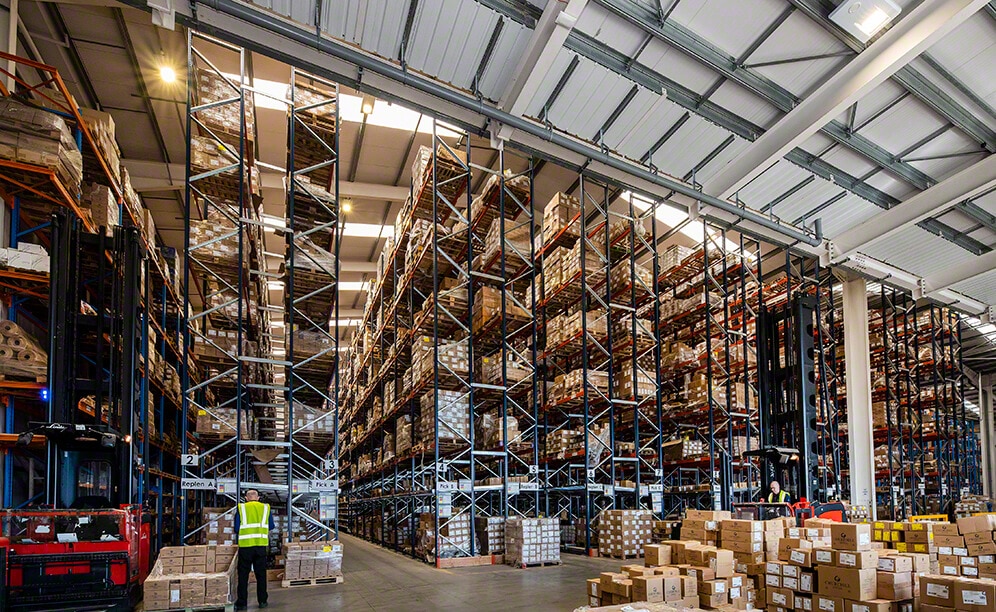
Churchill China has increased productivity by 10%.
Ask an expert