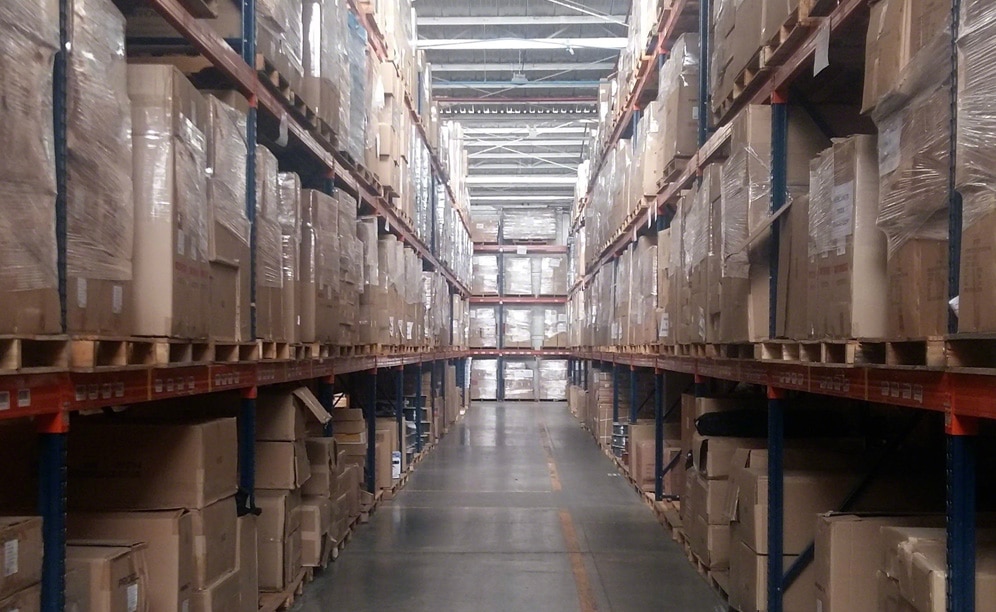
The warehouse of a musical instruments shop with Easy WMS of Mecalux
The warehouse of Gonher, an online musical instruments shop, is run through intelligent management
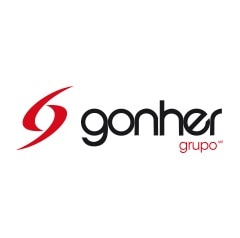
Gonher, a musical instruments and sound equipment company, has fully transformed its business since the implementation of the Easy WMS warehouse management system of Mecalux in its distribution centre in Mexico City. Recently, the company reorganised its warehouse, achieving the productivity it needed to supply its customers spread around the entire country.
Music culture develops in Mexico
Gonher first opened in Mexico in 1956, starting out as a business which sold records and music equipment. These days, it has a significant presence in the wholesale market and is making inroads in online shopping. It is a business leader in the import and sale of musical instruments and sound equipment for hobbyists and professional musicians in this country. From its beginnings, Gonher has been known for its ability to develop, design and install sound systems in theatres, hotels, buildings, clubs, restaurants, etc.
Likewise, it runs music schools where acoustic and electric guitar, bass, drums, piano and saxophone are taught, among other instruments.
Needs of Gonher
The company has a 6,000 m2 distribution centre in Mexico City. There it houses a wide variety of SKUs (around 14,900) that include all kinds of music-related products and those for live events (instruments, cords, cymbals, LED screens, microphones, speakers, etc.).
In the past, goods came from different countries (mainly, China, Germany, Italy, Argentina, Spain, the United States and Japan), and were deposited in the distribution centre as they reached the facility.
Operators had a lot of work in locating the products they needed and, consequently, picking orders was very slow. Time and again, the warehouse’s team had to work overtime to try to catch up on the workload (receptions, storage, order picking and dispatches). “Well, we had operations under control, but wanted higher productivity,” explained Esther Aguilar, operations manager of Gonher.
Plus, by not keeping the inventory under strict control, some product could end up being stored for too long, with all the costs this would involve.
In 2015, the business started to expand and Gonher experienced a jump in sales. Space in the warehouse was being misallocated and squandered, meaning the company was having a tough time managing all its products. It end up being impossible to squeeze in any more new inbound items.
Faced with this situation, Gonher got in touch with Mecalux aiming to find an effective solution for its warehouse that would permit it to “process orders more efficiently,” added Esther Aguilar
A more productive warehouse
The Mecalux technical team analysed Gonher’s needs at length. Its proposal included, on the one hand, the redesign of the warehouse and, on the other, the rollout of a management system (WMS) able to optimise all processes.
The warehouse comprised an ample zone equipped with single-depth pallet racks. It turned out that the distribution centre’s ceiling had different heights. So, the racks had to be adapted to this distinctive structural feature.
There is also a zone for shelving for picking. Costlier and smaller-sized products are deposited here (such as metronomes, tuners or high-definition microphones). These items make up 80% of the sales at Gonher, so the access these racks provide also facilitates product handling.
Lastly, it allocated an area for floor level product storage. It deals with bulky items, mainly used to set up stages, which are stored in containers.
Each day it receives goods in containers. These are housed in their slots and, from mid-morning into the evening, all the orders are prepared and distributed.
Products are sent to twelve points-of-sale that Gonher has spread through the Mexican republic’s states, to other specialty music shops and to customers who have made purchases online. On the other hand, the deployment of the Easy WMS, the warehouse management software of Mecalux, means operators are much more efficient. Now, the company only runs a single work shift (enough to deal with all its daily tasks).
Before getting the warehouse up and running, the company moved a portion of its goods to another distribution centre, which it rented to physically put the warehouse in order as per the WMS’s requirements. During this time, the Mecalux technical team was able to do an in-depth study of the new distribution and warehouse map, the products catalogue and each one of the processes that generate input and output movements. All this was done to fully personalise the Easy WMS and so it would adapt to Gonher’s specifications. “Thus, the new system’s implementation and start-up went smoothly, without affecting or stopping the business’s operations,” points out Esther Aguilar.
Moving to the rhythm of Easy WMS
The deployment of a WMS in a warehouse is a crucial decision for any company because it has a direct impact on the business’s productivity. So, before making any sort of choice, the responsibles at Gonher wanted to be completely sure of their decision.
As Esther Aguilar put, “we saw a working model of Easy WMS before we installed it. We had the opportunity to visit another warehouse with fairly similar operations and were convinced because we discovered the WMS was highly-suited to our logistics needs.”
The WMS is like an orchestra conductor, since it is in charge of all elements and operations that are carried out in the warehouse. Operators work in unison to achieve the maximum productivity and, ultimately, supply all the national customers as quickly as possible. They have radiofrequency devices to communicate with the system in real-time. Through these devices, operators receive instructions and confirm they have fulfilled them.
The system is very flexible and prevents operators from stopping to consider or question each action or task so that they can focus on the job at hand. As a result, productivity is much, much higher and, almost error-free.
Esther Aguilar - Operations Director at Gonher
“We are very pleased with Easy WMS because it has provided us with many advantages, most importantly picking agility and optimal product organisation, so that everything is always slotted and identified.”
Receipt of goods
Daily, workers unload between 25 and 30 containers and operators ID each product separately.
Next, the Easy WMS assigns each a location, taking into account the different variables like rotation, size and cost. For example, consumer products are set in lower racking levels (more accessible to operators), while low rotation ones are set on upper storage levels.
Proper organisation of the in-warehouse products has had a direct effect on all business activities being run there, including all the operators’ work and stock management. According to Esther Aguilar, “one of the advantages of installing Easy is that we can know our inventory levels in real-time.”
Storage of goods
Once all the products are received, operators are tasked with moving them to the location Easy WMS has assigned them. This spot might be in the pallet racks, in the containers stacked on the floor or on the hand-pick shelving modules.
The WMS instructs the operators continuously to prevent any type of error. Firstly, it shows them which coordinates they should go to and, secondly, in which exact location they must insert the pallets into. This has led to better space purposing of the warehouse.
Plus, the moment a product has been removed from its location and, as such, has run out, the Easy WMS is designed to generate a resupply command automatically.
Easy WMS launches the replenishment order when the location is empty. Meanwhile, in the case of the picking shelves, in particular, Gonher can preestablish the moment it wants these shelves resupplied. So, for example, higher demand products are replenished more frequently, before they run out, to prevent service stoppages.
Picking orders
Picking is one of the central operations of this warehouse because, as per Esther Aguilar, “each day operators put together about 90 orders comprised of 40 lines each, on average.”
Operators move through the aisles collecting the products listed for each order directly off the shelves. Personnel follow the order grouping system, which consists of putting together several orders during the same warehouse run.
Every day, between 20 and 30 pallets leave the warehouse with products that must be delivered to its customers. According to the company’s operations director, “Generally speaking, distribution is done inside Mexico City, although some products are also sent by lorry to other towns in the country.”
Gonher has streamlined order picking in two different ways. In the first place, thanks to the racks. The storage system stands out for being accessible, which spurs on the handling of goods.
In the second place, Easy WMS directs the operators by showing them which products they must pick off the shelves. As Esther Aguilar points out, “the WMS has helped reduce order shipping times. An order that comes in before 12 noon can be processed in less than 24 hours.”
Communicating with the ERP
In order to achieve global warehouse management, Easy WMS must be in permanent, bidirectional contact with Gonher’s ERP. To make this possible, an interface was created that facilitates the flow of messages sent from the ERP to Easy WMS and, also, from the Easy WMS to the ERP. Each message establishes an action to carry out and contains all the necessary information to do so.
For example, after purchasing from a provider, reception starts the moment in which the ERP notifies the Easy WMS of these products’ arrival (it shows quantities, features, units, etc.). When the goods have arrived at the distribution centre, the operators are tasked with checking if what was received corresponds to the listed information. Once this work is done, the WMS issues a file with the actual quantities that were input into the warehouse and sends this file to the ERP.
Since there are two-way interfaces (like in receptions, because communication is produced between the ERP and the WMS), there are also one-way interfaces (like in stock keeping, that involve the WMS sending the ERP stock level information).
Advantages for Gonher
- Goods control: the system organises storage locations based on strategies and rules, it labels products upon their receipt and has the capacity to give instructions to operators on where to store them.
- Systematically run: Easy WMS directs all operators at all times, whether it is instructing them where to slot or collect the goods, what orders they must prepare, etc.
- Picking speeds: with the installation of Easy WMS, order preparation and distribution is much, much faster, cutting deliveries times to only 24 hours post-purchase.
Gallery
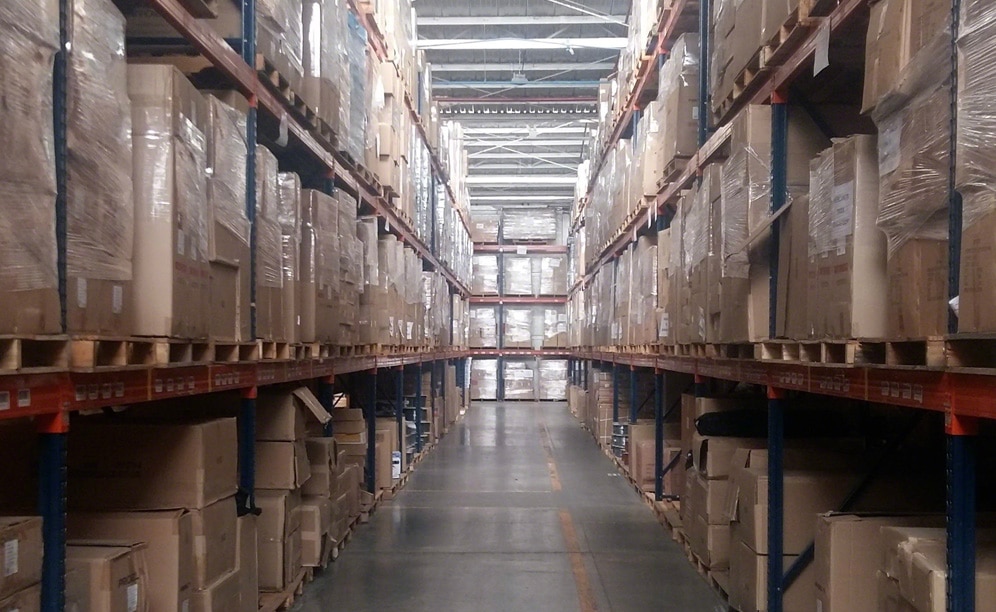
Intelligent management in the warehouse of an online musical instruments shop
Ask an expert