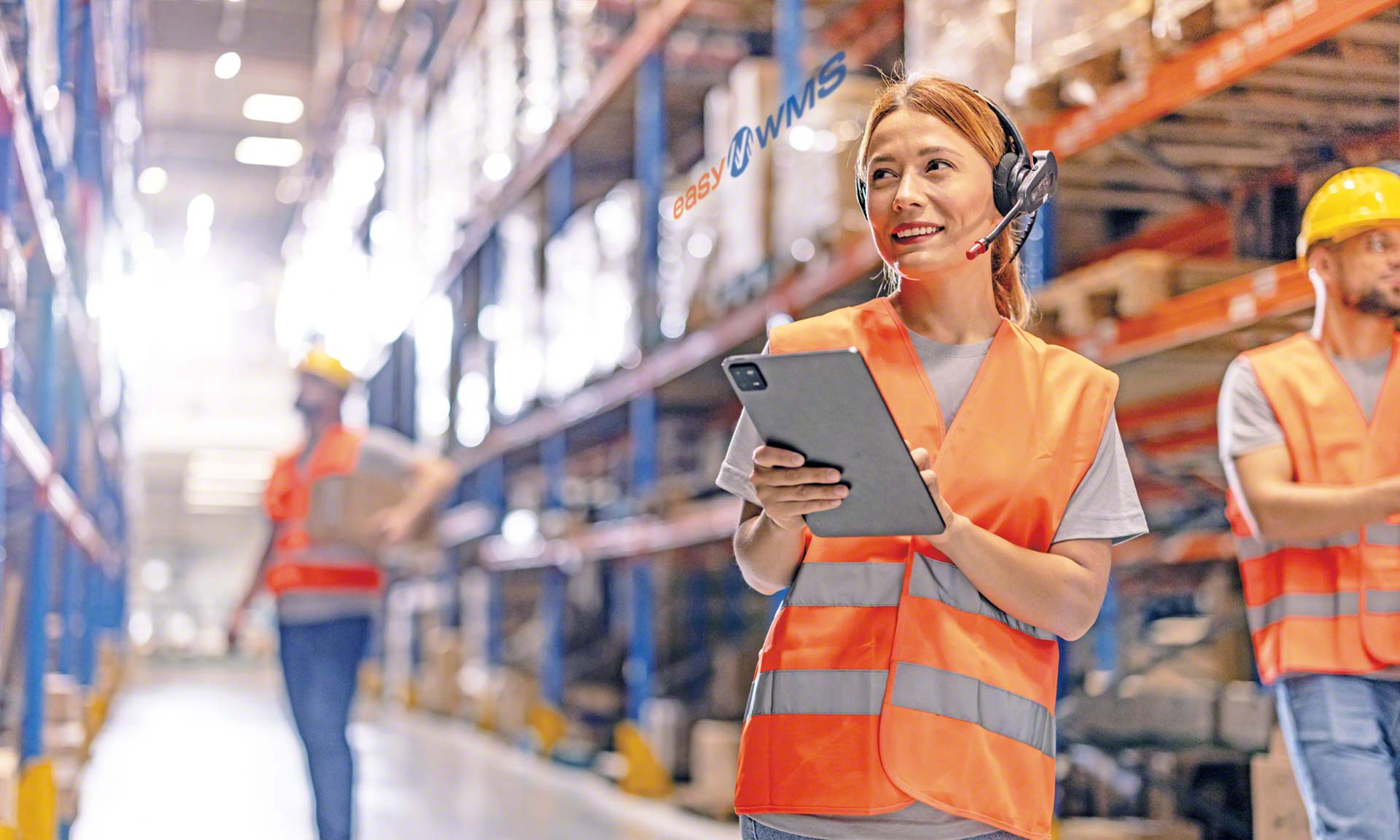
Gusto distributes 2,000 fresh-food SKUs with Easy WMS
The food distributor supplies gourmet Italian, French, Mexican and Asian products to a thousand restaurants.
Gusto imports Italian, Mexican and Asian products and supplies high-quality French food to restaurants throughout France. After experiencing rapid growth, the company has digitalised its logistics operations to continue delivering top service to its clients.
Top-quality food distribution
Gusto supplies gourmet products from France, Italy and other countries to restaurants nationwide. Its founder, Laurent Knibbe, managed the supply and service of the Parisian restaurant Casa Cosa for years. In 2015, driven by a desire to bring fine cuisine to more people, he started his own company. Gusto has been part of the GRAL network of independent distributors since 2019. In the wake of its rapid rise (recognised by media outlets such as Les Échos and the Financial Times) and partnerships with brands like Aoste, Saint Jean and Harry’s, Gusto has digitalised its logistics operations to continue providing its clients with top-tier service.
CHALLENGES
|
SOLUTION
|
BENEFITS
|
---|
Ingredient freshness and quality can mean the difference between a good dish and a true delicacy. Laurent Knibbe, founder and former manager of the Parisian restaurant Casa Cosa, understood this principle well. In 2015, he made his foray into food distribution with Gusto. The business supplies Italian, French and other international products to a thousand restaurants across the country from Wissous, just south of Paris.
Gusto’s journey began by importing only Italian artisanal products such as prosciutto, Parmesan cheese, burrata and buffalo mozzarella. But the company quickly took off. Knibbe and Francesca, Gusto’s first employee, were soon joined by dozens more. Now part of the GRAL network of independent distributors, the organisation has 50 workers and a fleet of 15 vehicles that accepts orders 24/7. To adapt successfully to this fast-paced expansion while maintaining quality service for clients, Gusto implemented Mecalux’s Easy WMS warehouse management system.
Onboarding new hires
“We multiplied our products in no time. At first, we knew the codes and locations by heart. However, bringing in new people soon became difficult because we no longer had 1,200 SKUs, but 2,000,” says Knibbe, who believes his experience as a restaurateur helps him better meet his clients’ needs.
By digitalising its warehouse with Easy WMS, Gusto can fulfil orders for any destination within a day, positioning the business as a competitive distributor. Once the ERP system supplies the warehouse management software with data on available SKUs, the WMS generates the optimal pick path and provides instructions to operators. Anyone can process orders using this software. It has reduced the number of errors compared to when the company only used the EBP ERP solution. The two systems interface seamlessly through an application integration connector. “The implementation project was based on logistics flows and IT processes. This required excellent collaboration between Mecalux, Limpid IT — the EBP integrator — and our teams,” says Knibbe.
Efficiency and traceability
“One mistake could cost us dearly and even mean losing a client. But with Easy WMS, we’ve significantly reduced order fulfilment errors,” says Knibbe. He stresses that when it comes to fresh produce, picking the wrong pallets can lead to waste. With this software, Gusto has optimised employee training time and improved stock turnover with the FEFO (first expired, first out) method. These strategies have helped avoid inventory shrinkage and make better use of food.
Algorithm for recording variable weight
Another feature that allows Gusto customers to enjoy fresh products is Easy WMS’s batch management capability. For example, a Parma ham that initially arrived at the warehouse as a single unit can be registered according to its variable weight, providing the option to sell portions by weight. This thorough control is made possible through product scanning in coordination with the Mecalux software.
With Easy WMS, Gusto effectively manages the batch numbers of the products entering and leaving its 4,500 m² warehouse. It has also gained a comprehensive view of its stock, which includes both imported foods and top-quality French products. “Through Mecalux, we know how many batches we have and their locations at any given time. This makes us more rigorous and gives us complete confidence in traceability,” says Knibbe.
Now, Gusto clients can place their orders via an app. Once validated, Easy WMS receives the information and indicates whether the goods are ready for order processing or need to be replenished. Prior to shipment, operators read products with RF scanners to verify quantities, batch numbers and expiry dates. Easy WMS ensures the traceability of goods stored at three different temperatures: ambient, cold and sub-zero. Moreover, it enables Gusto to perform processes even faster through wave picking. With this method, operators fill several orders simultaneously, reducing distances travelled throughout the warehouse.
After years of bringing the finest Italian and global delicacies to restaurant kitchens across France, Knibbe and the rest of the Gusto team remain focused on delivering high-quality service. Their goal is to consolidate their rapid growth while optimising management with Easy WMS.
One mistake could cost us dearly and even mean losing a client. But with Easy WMS, we’ve significantly reduced order fulfilment errors.
Gallery
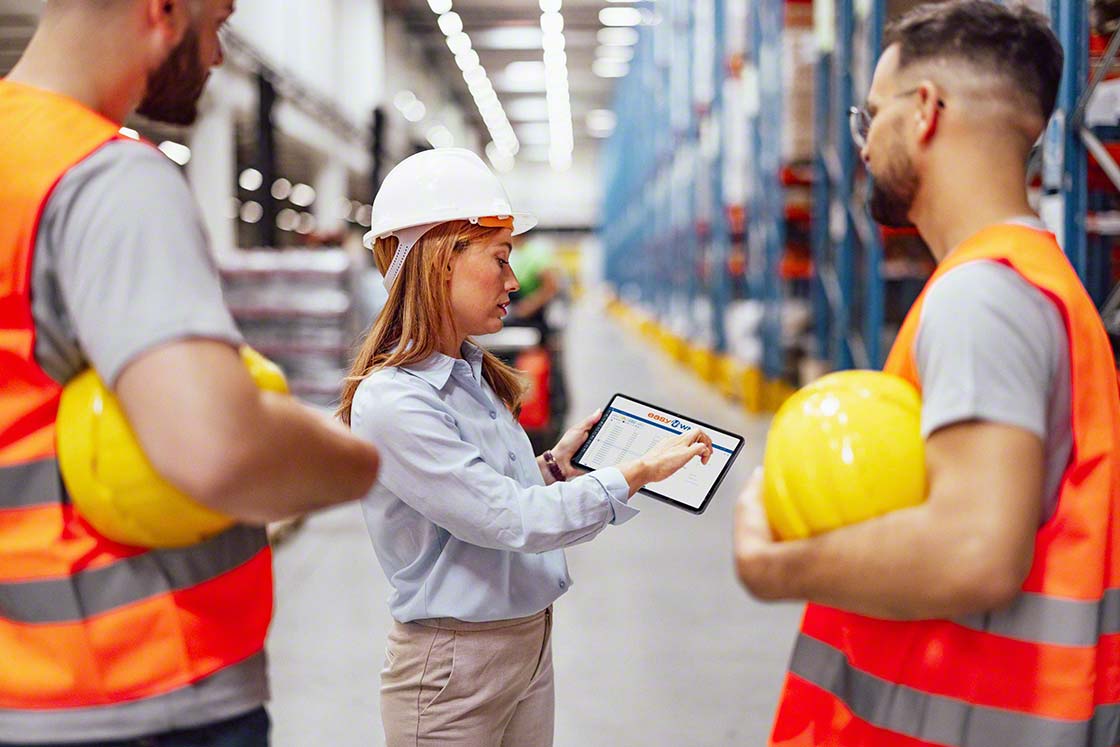
With Easy WMS, Gusto now has a comprehensive view of its warehouse inventory
Ask an expert