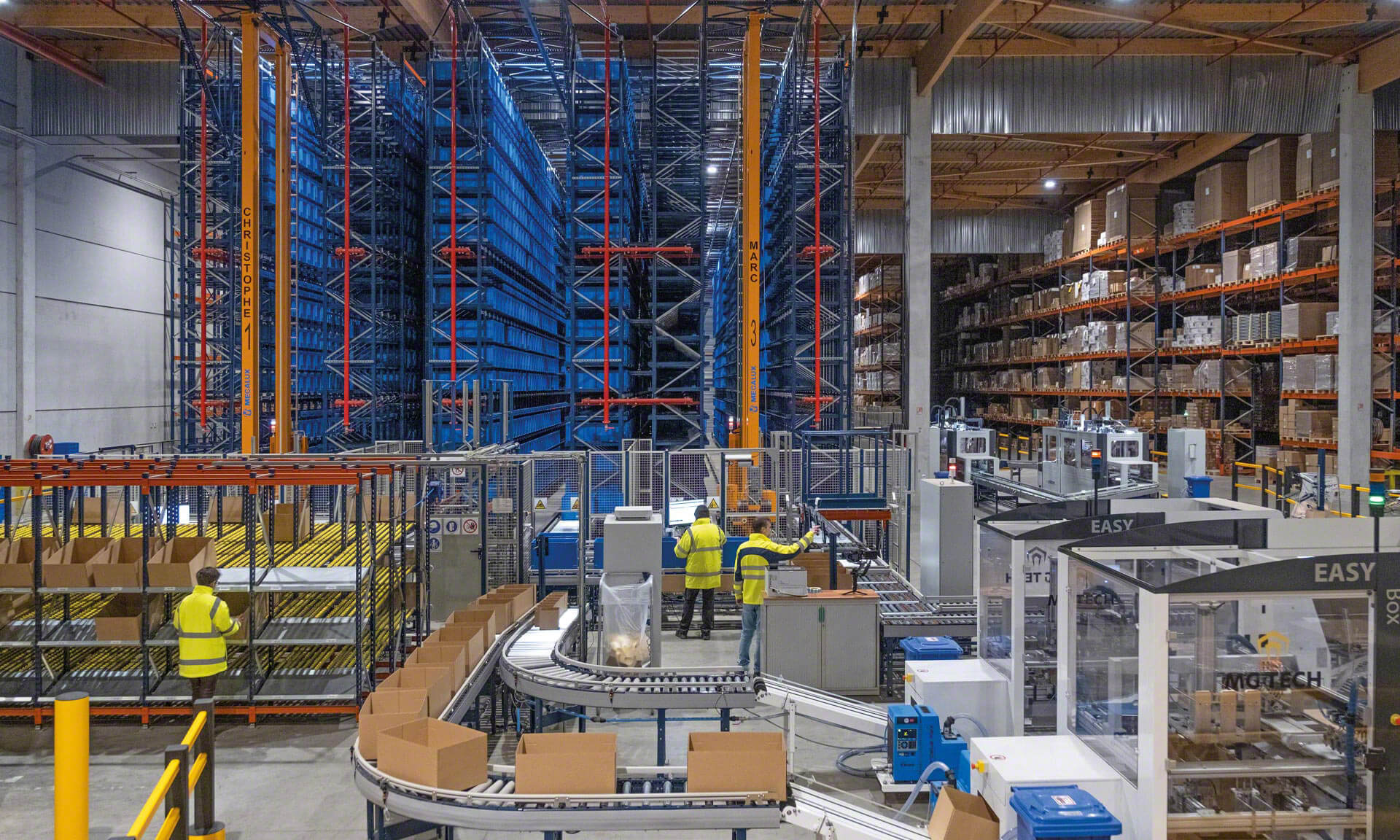
Jung Logistique streamlines order fulfilment with a single AS/RS
The 3PL provider centralises the fulfilment of 2,000 order lines in a miniload AS/RS with Easy WMS.
French 3PL operator Jung Logistique has installed a miniload system (AS/RS for boxes) in its warehouse in Dambach-la-Ville (France). The company has accelerated the storage of small items to fulfil and ship 2,000 order lines daily for clients worldwide.
Transport, storage and flow management solutions
Jung Logistique is a French company that offers comprehensive and personalised logistics services, from project analysis to monitoring and continuous improvement of processes. Focused on automation and technology, the business leverages advanced tools to manage information flows and provide full supply chain visibility. Founded in 1955, Jung Logistique operates 17 logistics facilities, 250 vehicles and 400,000 m² of storage space.
CHALLENGES
|
SOLUTIONS
|
BENEFITS
|
---|
French third-party logistics (3PL) provider Jung Logistique has carried out an ambitious automation project in its warehouse in Dambach-la-Ville (Alsace region). The aim was to meet the growing demand of one of its biggest clients, a renowned electric material manufacturer.
“Automation is key to our logistics activity. It enables us to optimise processes while staying connected with our customers and preserving our identity as a multi-client, multi-flow service provider,” says Nicolas Hirtz, General Manager of Logistics at Jung Logistique.
When it started doing business, the 3PL provider managed its logistics operations manually. Although the work organisation model did not achieve maximum efficiency, it was sufficient at the time to meet client demands. “Before automating our operations, goods were stored and managed using pallet racking and picking shelves. Our main need was to streamline and optimise the order fulfilment process,” says Hirtz.
Jung Logistique has installed a miniload system comprising three stacker cranes for boxes. This automated storage and retrieval system (AS/RS) manages 5,000 SKUs and supports the shipment of 2,000 order lines daily on average to clients around the globe. The fully automated integrated logistics solution consolidates all operations performed by the 3PL for its clients — putaway, order picking, packaging, packing and shipping — into a single space. The Easy WMS warehouse management system monitors and supervises all processes. Hirtz says: “Thanks to the miniload AS/RS and its packaging line, we now have a versatile, efficient solution. It adapts to the various types of products we handle, enabling us to respond quickly and accurately to our clients’ changing demands.”
As for how Jung Logistique came to select its storage system provider, Hirtz says: “We chose the AS/RS from Mecalux because they supplied our previous racking, so we’d already established a strong relationship. I’d highlight Mecalux’s speed, communication and continuous support. The team demonstrated great commitment and professionalism in our first logistics automation project.”
Automated putaway of 20,000 boxes
“Goods arrive at the AS/RS palletised, either directly from the production line or external suppliers,” says Xavier Charlier, Automation Manager. The logistics process begins with depalletisation. Operators remove items from their original packaging and place them in plastic bins on the conveyors, which move them to the stacker cranes.
The AS/RS racking stands 10 m tall by 43 m long. It ensures a high throughput thanks to the continuous movement of the three stacker cranes, which can transport up to 137 bins per hour, each weighing less than 50 kg. Similarly, the miniload system and conveyors facilitate picking according to the goods-to-person principle. This strategy optimises operations by automatically delivering products to pick stations as directed by Easy WMS. The system strictly monitors all processes through its permanent, two-way connection with Jung Logistique’s logistics software.
In addition to its agile movements, another characteristic of the AS/RS that impressed Jung Logistique was its ability to maximise space utilisation. The new miniload system stores 20,000 bins in just 545 m².
Hirtz says: “Automation offers considerable advantages. On the one hand, it improves ergonomics for pickers. These operators no longer have to travel, reducing the physical strain and time involved in picking. On the other hand, it expedites turnaround time by having the goods ready for processing more quickly.”
Personalised picking and packing
“Every day, we send 500 orders with an average of four lines to clients worldwide,” says Hirtz. To ensure error-free picking, Mecalux equipped the two stations with a put-to-light (PTL) system. “This technology enhances the quality of order fulfilment, guaranteeing greater accuracy and end-customer satisfaction,” says Hirtz.
With the PTL system, operators follow instructions from Easy WMS and easily identify the locations for depositing goods and the quantity. In the first area, SKUs are placed on carton live storage. In the second, orders are filled directly at four conveyor packing stations.
“The automatic conveyors are essential in our warehouse. They seamlessly connect the picking, packing and shipping phases. This system facilitates a continuous workflow, optimises time and reduces manual handling, resulting in more efficient and accurate order fulfilment,” says Hirtz.
The boxes head from the pick stations to the packing, labelling and cutting zones. There, the packaging is checked to verify that it meets the requirements of shipping agencies such as UPS, FedEx and Chronopost. All these areas — particularly the cutting space — have been personalised. For example, the machines cut and seal cartons at the appropriate height, avoiding empty spaces inside them. Tailoring all the automated systems to the specific characteristics of each box and its movement was a challenge, as each carton reacts differently depending on its weight, size and contents.
Finally, Jung Logistique’s order consolidation and shipping area is equipped with five automatic conveyor lines where boxes are placed on pallets for loading onto vehicles. Each line corresponds to a different transport agency.
Warehouse with 2,000 daily order lines
The result of this sophisticated network of automated systems installed by Mecalux speaks for itself: Every day, the facility accurately ships 500 boxes and 300 pallets, ensuring efficiency and speed in Jung Logistique’s logistics operations.
“Our goal is to further automate our operational processes to optimise flows, increase efficiency and meet our clients’ growing demands even more effectively,” says Hirtz.
We now have a system capable of adapting to the various types of products we handle, enabling us to respond quickly and accurately to our clients’ demands.
Gallery
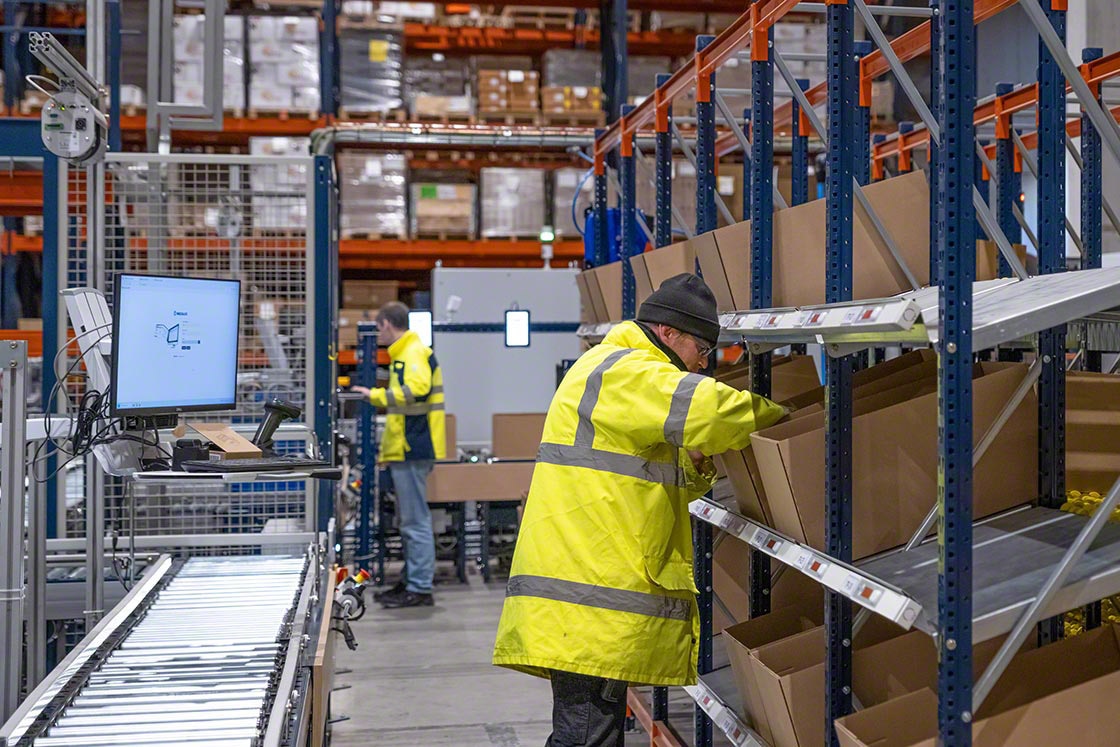
Jung Logistique stores small items automatically
Ask an expert