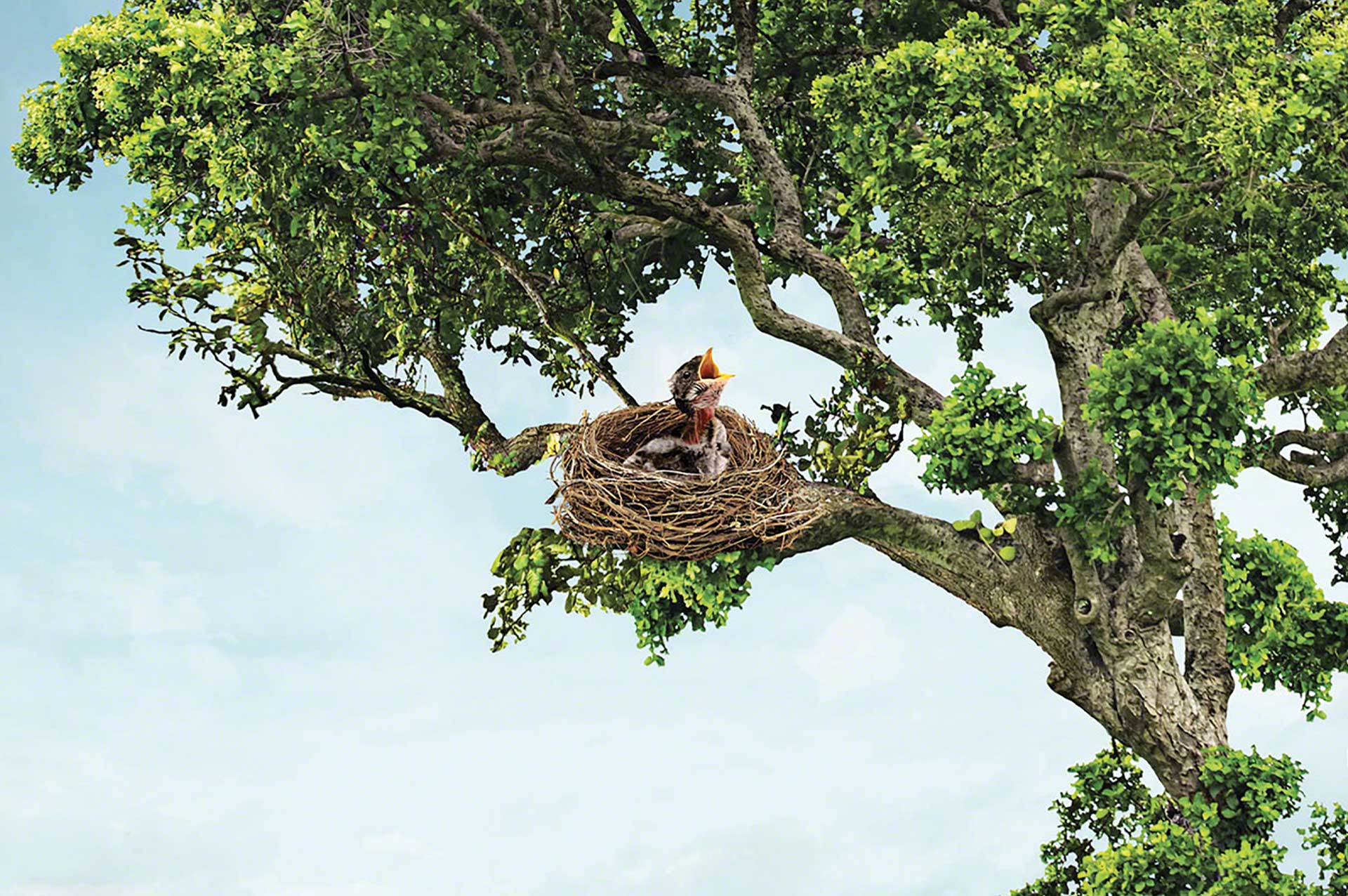
Konya Şeker installs an automated warehouse in a seismic region
Konya Şeker, Turkey’s largest sugar manufacturer, connects its production plant in an earthquake-prone region with a 38 m tall automated warehouse.
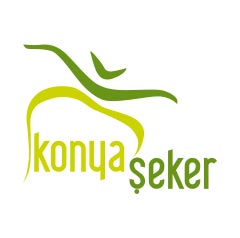
Konya Şeker, Turkey’s largest sugar producer, has modernised logistics operations in its Çumra centre with a 38 m tall seismic-resistant automated warehouse. Connected to the production lines, the automated facility streamlines the daily distribution of 2,000 pallets containing chocolates and biscuits.
Konya Şeker: Turkey’s largest sugar manufacturer
Konya Şeker is a Turkish business specialising in the production and sale of sugar and other derivatives. The company also makes a wide variety of sweets prepared with its sugar, including chocolates, biscuits and halvas (Middle Eastern sweets made with sesame paste). Since 2008, Konya Şeker has been a part of the Anadolu Birlik Holding (ABH) group, which brings together industries in diverse sectors such as food, agriculture, energy and chemicals. Founded in 1954, Konya Şeker has 45 facilities, 900,000 farmers and more than 10,000 employees.
CHALLENGES
|
SOLUTIONS
|
BENEFITS
|
---|
Over the past few decades, Konya Şeker has completely overhauled its logistics and production operations with the latest technologies in the market, firmly embracing robotic process automation. By upgrading its supply chain, the company increased its production volumes, becoming Turkey’s largest sugar manufacturer. Moreover, this modernisation prepared the organisation to carry out an ambitious expansion project. Currently, Konya Şeker’s 45 production facilities produce approximately 22% of the sugar consumed in Turkey. The business is also a leader in the frozen potato market.
In the town of Çumra, on the outskirts of the city of Konya, the company boasts the largest sugar factory in Turkey. This facility spans 260 hectares and is equipped with 27 production lines. “In recent years, we’ve doubled our annual sugar production, reaching 435,500 tonnes. All machinery and equipment were sourced from top-tier European suppliers specialising in state-of-the-art technology. Moreover, this is the only sugar factory in the world that can obtain its raw materials within a 20-kilometre radius,” says Kerim Başaran, AS/RS Warehouse Manager at Konya Şeker.
The Çumra plant is home to the manufacturing centre for the organisation's brand of chocolates and biscuits. “Our Torku chocolate production facility stands out as one of the most modern centres in terms of technology. It serves the domestic market and enables us to export our products to 74 countries, including Switzerland, the motherland of chocolate,” says Başaran.
A few years ago, Konya Şeker expanded and diversified Torku’s product portfolio, introducing chocolates, dairy, meat, pastries, oil and vinegar, among other items. Consequently, the company had to prioritise its logistics operations to cope with the increase in production. Initially, it managed its raw materials and finished products in a traditional warehouse. However, the need to reduce goods-in/goods-out lead times led the business to invest in intralogistics technology.
In line with its modernisation strategy, Konya Şeker set up an automated clad-rack warehouse. Managed by Mecalux’s Easy WMS software, the facility distributes 2,000 pallets a day. The warehouse, capable of storing 48,000 pallets containing biscuits and chocolates, is integrated with the production centre. This connection facilitates the autonomous exchange of raw materials and finished goods ready for distribution.
In addition to boosting throughput, technology has helped to maximise the quality of the sweets by ensuring strict adherence to safety and hygiene protocols. “Our top priority at the facility is consumer health. Therefore, we focus our efforts on producing natural, additive-free chocolate while preserving its properties. To do this, it’s essential to ensure compliance with the relevant legislation,” says Başaran.
An automated warehouse in a seismic region
Most of Turkey sits on the Anatolian tectonic plate, wedged between the Eurasian, Arabian and African plates. The friction between these plates makes this country one of the most seismically active regions on the planet.
Konya Şeker’s warehouse is a clad-rack structure, meaning the racking supports its own weight as well as that of the roof, vertical enclosures and goods. Mecalux designed it taking into consideration several factors affecting the structure, including wind force. In this specific case, it also accounted for seismic activity in the area and the local regulations currently in effect.
Building a 38-metre-tall warehouse on a site with such a high degree of earthquake activity as Konya posed a challenge for Mecalux’s structural engineering department. It demanded tremendous precision during the assembly process. The racking was reinforced and sturdier central frames were employed to absorb the dynamic forces caused by potential seismic movements.
Maximum storage productivity for Konya Şeker
“Automation has reduced our goods storage and retrieval times,” says Başaran. Konya Şeker’s automated warehouse consists of seven aisles, each 138 m long, with double-deep racking. To deposit and retrieve materials, the Mecalux stacker cranes for pallets installed in each aisle are equipped with telescopic forks. This allows them to access the second storage position on all levels. These machines, which follow the commands of Easy WMS, operate at a travel speed of 220 m/min and a lifting speed of 64 m/min.
Two of Konya Şeker’s warehouse aisles are allocated to raw materials and packaging items, while the remaining five aisles house finished goods. Three of these run at a controlled temperature of 15 °C to preserve the consistency, flavour and aroma of the chocolates. The other two aisles operate at ambient temperature.
SKUs are assigned to locations based on their dimensions and the ABC analysis, managed by Easy WMS. High-turnover products are placed on the ends of the aisles, closest to the incoming and outgoing conveyors. Meanwhile, low-turnover items are slotted further away, at the opposite end of the aisles. This strategy optimises stacker crane movements.
Automatic connection with production
One of the greatest advantages of automating Konya Şeker’s warehouse is its integration with the manufacturing centre. This plant is divided into two distinct areas: one dedicated to chocolates and another to biscuits.
To maintain a continuous flow of movements, a 6-metre-high raised tunnel connects the outputs from the chocolate and biscuit production lines directly to the warehouse. Inside the tunnel, an automatic conveyor line runs along the side of the logistics complex, extending the front of the rack-supported building. Thanks to the conveyor’s accumulation capacity, the pallets can remain on stand-by temporarily, awaiting entry in an orderly manner and without needing to be placed on the floor. Subsequently, lifts located at the beginning and end of the tunnel transport the goods between different levels.
Automated picking floor at Konya Şeker
Konya Şeker is charged with supplying its products to supermarkets and shops across Turkey every day. With this objective in mind, a two-storey building is located at one end of the warehouse. Order picking is performed on the upper floor, while the lower floor is dedicated to shipping.
The picking floor has four blocks of live channels for high-consumption goods. An automatic transfer car supplies each channel, which can store up to three pallets of a single SKU. Thus, reserve merchandise is always available. On the lower part of the channels, operators access the pallets directly. They retrieve the boxes that make up each order, travelling through the aisles assisted by order pickers. Operators locate SKUs as instructed by Mecalux’s warehouse management system via their RF scanners.
In front of the storage aisles, the conveyors transport the necessary SKUs to three pick stations for low-demand items. Operators can prepare up to 12 orders simultaneously.
Once the orders are closed, the pallets proceed to the stretch wrapper. They are then stored until Easy WMS assigns them a route and dispatches them to the shipping area.
The lower floor of the building adjacent to the warehouse handles outbound operations. A transfer car classifies and sequences the goods into 26 live preload channels. Pallets are grouped in each channel — taking into account whether they belong to the same order or route — and later loaded onto lorries.
The Mecalux software plays a pivotal role in all Konya Şeker logistics processes: “With Easy WMS, we maintain tighter control over the 48,000 pallets in our automated warehouse. It helps make all our operations faster as well as error-free,” says Başaran.
To enhance goods management, the software interfaces with Konya Şeker’s ERP system. The ERP notifies Easy WMS in advance of the items that will arrive at the automated warehouse from production. This enables the WMS to assign the products locations more quickly.
Konya Şeker: high-performance logistics processes for a leading company
“Torku has earned consumer recognition with its 100% natural, safe and high-quality products. We make them by overseeing the entire process from seed to table, guaranteeing their purity and supporting the work of Anatolian farmers,” says Başaran.
The 38-metre-tall automated warehouse has marked a turning point in Konya Şeker’s supply chain, specifically for Torku chocolates and biscuits. Logistics automation and digitalisation are fundamental tools for the company to achieve its targets. Thanks to these technologies, the business tracks its products comprehensively. Furthermore, it has improved the efficiency of its operational processes with a clear goal: to ensure the distribution of 2,000 pallets daily to 74 countries.
With Easy WMS, we maintain tighter control over the 48,000 pallets in our automated warehouse. It helps make all our operations faster as well as error-free.
Gallery
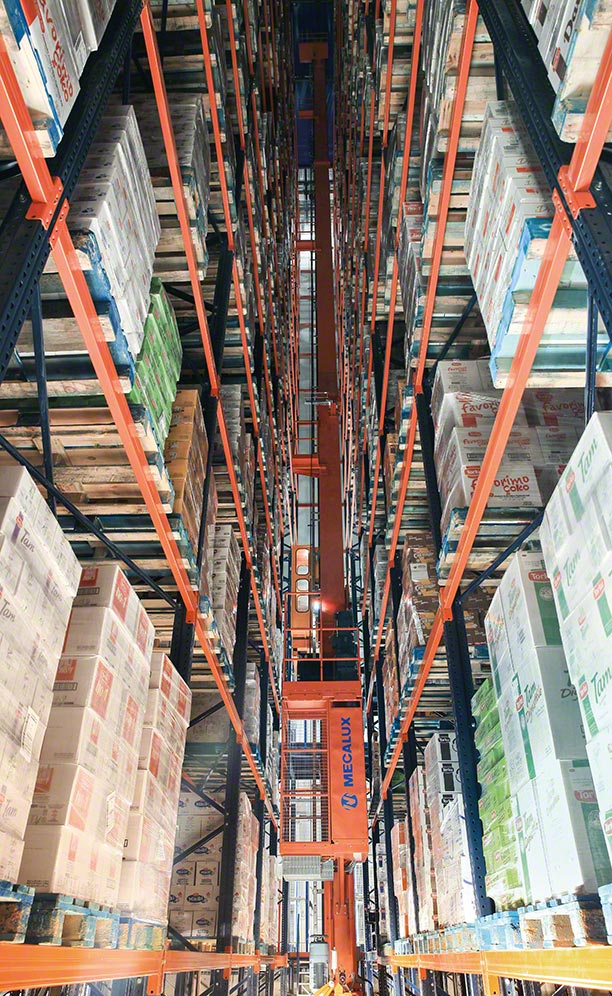
The stacker crane moves pallets inside Konya Şeker’s storage aisles
Ask an expert